- お役立ち記事
- Basics of Machine Tool Maintenance: How to Maximize Production Efficiency
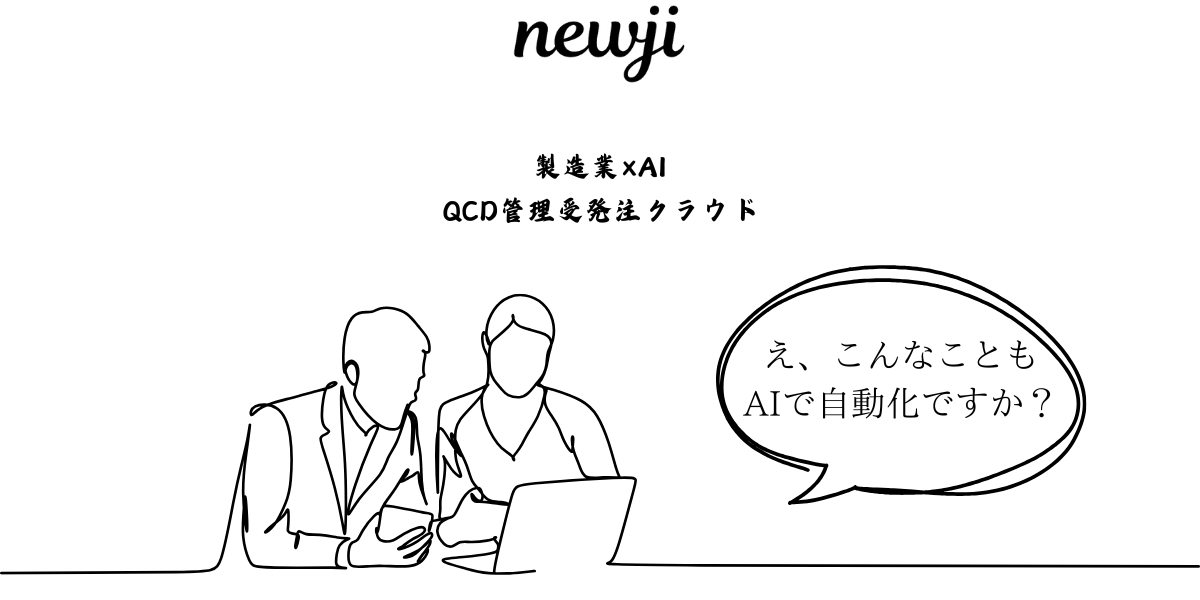
Basics of Machine Tool Maintenance: How to Maximize Production Efficiency
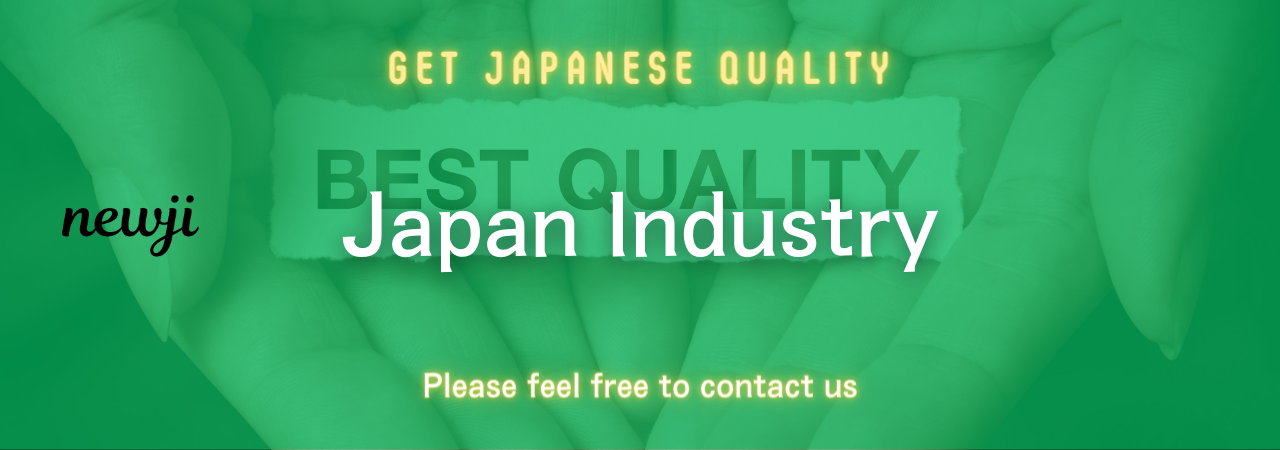
目次
Understanding the Importance of Machine Tool Maintenance
Machine tools are essential components in the manufacturing industry, playing a vital role in shaping, cutting, and forming materials to create precise parts and products.
Their performance can significantly impact productivity, quality, and overall production efficiency.
Therefore, understanding the importance of machine tool maintenance is critical for any manufacturing operation.
Proper maintenance ensures that machine tools operate at their optimum level, reducing the likelihood of downtime caused by mechanical failures.
Unplanned downtime can lead to delayed production schedules and increased operational costs, affecting a company’s bottom line.
Effective maintenance strategies can mitigate these risks, allowing for smoother operations and maximizing production efficiency.
Moreover, regular maintenance is crucial for ensuring the longevity of machine tools.
Equipment that is well-maintained is less likely to suffer from wear and tear, ultimately extending its lifespan and providing a better return on investment.
In addition, well-maintained machines are more likely to produce high-quality products with precise specifications, which is essential for maintaining customer satisfaction and building a strong reputation in the marketplace.
Key Components of Machine Tool Maintenance
Maintenance activities can be broken down into various components, each playing an integral role in ensuring the proper functioning of machine tools.
Understanding these components can help businesses design effective maintenance programs tailored to their specific needs.
1. Routine Inspections
Routine inspections involve the regular checking of machine tools to identify potential issues before they escalate into significant problems.
During inspections, technicians examine components like machine beds, spindles, and coolant systems to ensure they are functioning correctly.
Any signs of wear, misalignment, or leaks should be addressed immediately to prevent more severe damage.
2. Cleaning and Lubrication
Cleaning and lubrication are essential tasks in machine tool maintenance.
Over time, dust, debris, and metal shavings can accumulate in machine parts, leading to increased friction and wear.
Regular cleaning ensures that these contaminants are removed, allowing the machine to operate smoothly.
Additionally, proper lubrication reduces friction between moving parts, minimizing wear and maintaining consistent performance.
3. Calibration
Machine tools require periodic calibration to maintain their accuracy and precision.
Calibrating involves adjusting the machine settings to ensure they produce parts with the desired specifications.
This process is particularly important for industries that require high precision, such as aerospace and medical device manufacturing.
Regular calibration can help identify discrepancies in machine performance, allowing for timely adjustments and avoiding costly production errors.
4. Replacement of Wear Parts
Some parts of machine tools, such as bearings, seals, and belts, are subject to wear over time and will require replacement.
Regularly replacing these wear parts before they fail can prevent more significant damage to the machine and minimize production downtime.
Establishing a schedule for the replacement of wear parts can help ensure that machines continue to operate efficiently.
Developing a Proactive Maintenance Strategy
A proactive maintenance strategy focuses on preventing issues before they occur, rather than reacting to problems after they have happened.
By prioritizing preventive measures, businesses can improve machine tool reliability and extend equipment lifespan.
1. Scheduled Maintenance
Scheduled maintenance involves performing maintenance activities at regular intervals based on manufacturers’ recommendations or previous experience.
This approach can help businesses anticipate potential issues and address them in a planned manner, minimizing surprise disruptions to production.
2. Predictive Maintenance
Predictive maintenance leverages data and technology to predict when machine tools are likely to fail.
By monitoring the condition of key components using sensors and analyzing this data, businesses can identify patterns and trends that indicate imminent failures.
This enables maintenance teams to perform necessary actions before breakdowns occur, optimizing machine uptime and reducing repair costs.
Training and Skill Development for Maintenance Personnel
An essential aspect of maximizing production efficiency through maintenance is ensuring that maintenance personnel are adequately trained and skilled.
Technicians should be knowledgeable about the different types of machine tools and their specific maintenance requirements.
Providing ongoing training and professional development opportunities can help maintenance teams stay up-to-date with evolving technologies and best practices in machine tool maintenance.
This enables them to perform maintenance tasks more efficiently and effectively, ultimately enhancing production efficiency.
Leveraging Technology for Maintenance Optimization
With technological advancements, businesses have access to a range of tools and software that can enhance machine tool maintenance efforts.
From predictive analytics to maintenance management software, these technologies allow businesses to streamline maintenance processes, monitor equipment health, and optimize resources.
Implementing a computerized maintenance management system (CMMS) can provide valuable insights into maintenance activities, scheduling, and resource allocation.
This helps ensure that maintenance tasks are completed on time and that spare parts and resources are available when needed.
Additionally, the integration of IoT (Internet of Things) devices can provide real-time monitoring of machine conditions, allowing for instant alerts and more informed decision-making.
Conclusion
In conclusion, effective machine tool maintenance is a critical factor in maximizing production efficiency.
By understanding the key components of maintenance, developing a proactive strategy, investing in training, and leveraging technology, businesses can ensure that their machine tools operate optimally, minimize downtime, and maintain high-quality production standards.
Prioritizing maintenance not only protects the significant investment in machinery but also builds a foundation for sustainable growth and competitiveness in the manufacturing industry.
資料ダウンロード
QCD調達購買管理クラウド「newji」は、調達購買部門で必要なQCD管理全てを備えた、現場特化型兼クラウド型の今世紀最高の購買管理システムとなります。
ユーザー登録
調達購買業務の効率化だけでなく、システムを導入することで、コスト削減や製品・資材のステータス可視化のほか、属人化していた購買情報の共有化による内部不正防止や統制にも役立ちます。
NEWJI DX
製造業に特化したデジタルトランスフォーメーション(DX)の実現を目指す請負開発型のコンサルティングサービスです。AI、iPaaS、および先端の技術を駆使して、製造プロセスの効率化、業務効率化、チームワーク強化、コスト削減、品質向上を実現します。このサービスは、製造業の課題を深く理解し、それに対する最適なデジタルソリューションを提供することで、企業が持続的な成長とイノベーションを達成できるようサポートします。
オンライン講座
製造業、主に購買・調達部門にお勤めの方々に向けた情報を配信しております。
新任の方やベテランの方、管理職を対象とした幅広いコンテンツをご用意しております。
お問い合わせ
コストダウンが利益に直結する術だと理解していても、なかなか前に進めることができない状況。そんな時は、newjiのコストダウン自動化機能で大きく利益貢献しよう!
(Β版非公開)