- お役立ち記事
- How to use digital twin technology to strengthen safety management
How to use digital twin technology to strengthen safety management
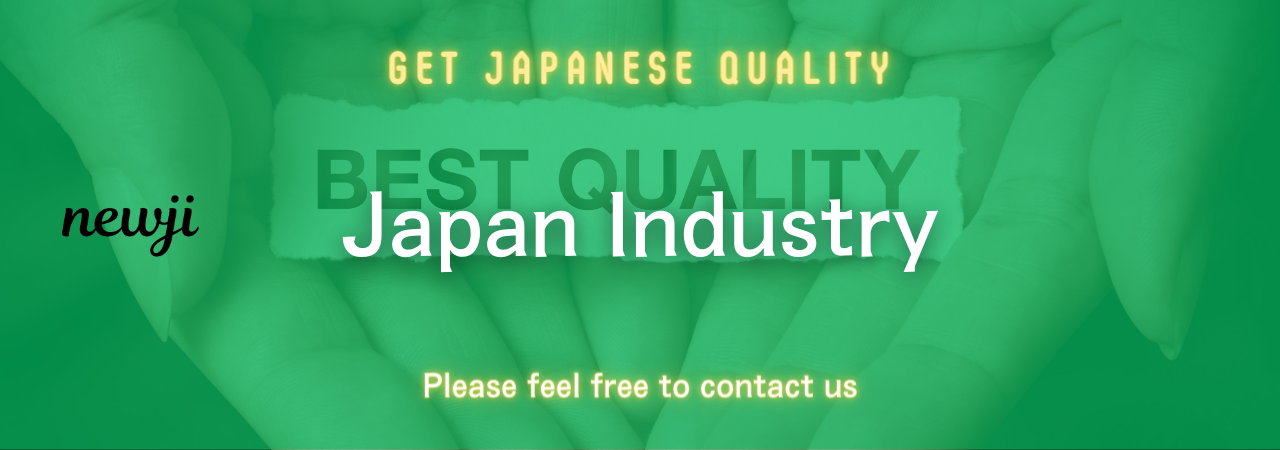
目次
Understanding Digital Twin Technology
Digital twin technology is a revolutionary approach that creates a virtual representation of physical objects or systems.
This technology allows for the simulation, analysis, and monitoring of real-world systems in a virtual environment.
By doing so, organizations can predict issues, optimize performance, and enhance decision-making processes.
Digital twins are essentially digital replicas of real-world objects, ranging from simple devices to complex systems such as aircraft or entire manufacturing plants.
These digital counterparts are continuously updated with real-time data, enabling them to mirror the behavior of their physical counterparts accurately.
This continuous data inflow allows for precise simulations and predictions, making digital twins a valuable tool for various industries.
The Role of Digital Twins in Safety Management
Safety management is a critical aspect of any organization, especially those operating in high-risk environments such as manufacturing, construction, and energy production.
Ensuring the safety of employees, equipment, and the environment is paramount.
Digital twin technology can play a vital role in enhancing safety management by providing detailed insights into equipment and processes.
With digital twin technology, organizations can simulate and predict potential hazards or failures before they occur.
By analyzing the digital twin, safety managers can identify vulnerabilities or inefficiencies within a system and implement corrective measures proactively.
This predictive capability reduces the risk of accidents and improves overall workplace safety.
Real-Time Monitoring and Alerts
One of the most significant advantages of digital twin technology is its ability to provide real-time monitoring of systems and equipment.
By continuously feeding data from sensors and IoT devices into the digital twin, organizations gain a holistic view of their operations.
This real-time monitoring enables safety managers to receive instant alerts about any deviations from normal operating conditions.
These alerts can prompt immediate action, such as shutting down a machine or dispatching a maintenance team, to prevent accidents or equipment failure.
The ability to respond quickly to issues reduces downtime and minimizes potential damage, ensuring a safer working environment.
Enhanced Training and Simulation
Digital twin technology also offers advanced training and simulation capabilities.
By creating a virtual replica of equipment or processes, organizations can conduct realistic training sessions for employees.
This approach allows workers to practice emergency procedures and safety protocols in a risk-free environment.
Simulations help employees understand how to respond to different scenarios, such as equipment malfunctions or hazardous material spills.
This hands-on experience enhances their ability to handle emergencies effectively, reducing the likelihood of accidents caused by human error.
Predictive Maintenance and Risk Assessment
Predictive maintenance is a game-changer for safety management.
Digital twins can monitor the condition of equipment in real-time, allowing organizations to predict when maintenance is necessary.
By analyzing data from the digital twin, maintenance teams can identify patterns and trends that indicate potential issues.
This proactive approach to maintenance prevents unexpected equipment failures, which can lead to accidents or production downtime.
Moreover, digital twins facilitate risk assessment by enabling safety managers to evaluate the impact of potential failures on overall operations.
By simulating different scenarios, safety managers can prioritize and address high-risk areas before incidents occur.
Environmental Impact Simulations
Digital twin technology extends its benefits to environmental safety as well.
Organizations can use digital twins to simulate the environmental impact of their operations.
By modeling potential scenarios such as chemical spills or emissions, companies can assess the consequences and develop strategies to mitigate adverse effects.
These simulations enable organizations to design safer processes and implement measures to minimize environmental risks.
By understanding how different factors interact and affect the environment, companies can make informed decisions that align with sustainability goals.
Continuous Improvement and Feedback Loops
Digital twins facilitate a culture of continuous improvement through their feedback loops.
By analyzing performance data and identifying areas for enhancement, organizations can implement changes that improve safety outcomes.
Continuous feedback from the digital twin helps refine processes, ensuring that safety protocols remain effective and up-to-date.
Incorporating lessons learned from virtual simulations into real-world practices fosters a proactive safety management approach.
Implementing Digital Twin Technology
To leverage digital twin technology for safety management, organizations need to follow a structured implementation process.
The first step is to identify the systems or equipment that could benefit from a digital twin representation.
Prioritize areas with high-risk potential or critical importance to overall operations.
Next, integrate sensors and IoT devices to collect real-time data, which will feed into the digital twin.
Ensure that data is accurate and reliable to create a true representation of the physical counterpart.
Collaboration is key when implementing digital twin technology.
Involve safety managers, engineers, and IT professionals in the process to ensure all aspects of safety management are considered.
This multidisciplinary approach ensures that the digital twin addresses both technical and safety concerns.
Finally, establish protocols for monitoring, analysis, and reporting.
Regularly review the data and insights provided by the digital twin to ensure that safety measures are effective and adjustments are made as necessary.
Conclusion
Digital twin technology offers a powerful tool for strengthening safety management across various industries.
By providing real-time insights, predictive capabilities, and enhanced training opportunities, digital twins enable organizations to proactively manage risks and improve safety outcomes.
Implementing digital twin technology requires careful planning and collaboration but offers significant benefits in terms of workplace safety, operational efficiency, and environmental protection.
As digital twin technology continues to evolve, its role in safety management will expand, offering even greater opportunities for organizations to protect their employees and assets effectively.
資料ダウンロード
QCD調達購買管理クラウド「newji」は、調達購買部門で必要なQCD管理全てを備えた、現場特化型兼クラウド型の今世紀最高の購買管理システムとなります。
ユーザー登録
調達購買業務の効率化だけでなく、システムを導入することで、コスト削減や製品・資材のステータス可視化のほか、属人化していた購買情報の共有化による内部不正防止や統制にも役立ちます。
NEWJI DX
製造業に特化したデジタルトランスフォーメーション(DX)の実現を目指す請負開発型のコンサルティングサービスです。AI、iPaaS、および先端の技術を駆使して、製造プロセスの効率化、業務効率化、チームワーク強化、コスト削減、品質向上を実現します。このサービスは、製造業の課題を深く理解し、それに対する最適なデジタルソリューションを提供することで、企業が持続的な成長とイノベーションを達成できるようサポートします。
オンライン講座
製造業、主に購買・調達部門にお勤めの方々に向けた情報を配信しております。
新任の方やベテランの方、管理職を対象とした幅広いコンテンツをご用意しております。
お問い合わせ
コストダウンが利益に直結する術だと理解していても、なかなか前に進めることができない状況。そんな時は、newjiのコストダウン自動化機能で大きく利益貢献しよう!
(Β版非公開)