- お役立ち記事
- Example of process management that reduces lead time in the manufacturing industry
Example of process management that reduces lead time in the manufacturing industry
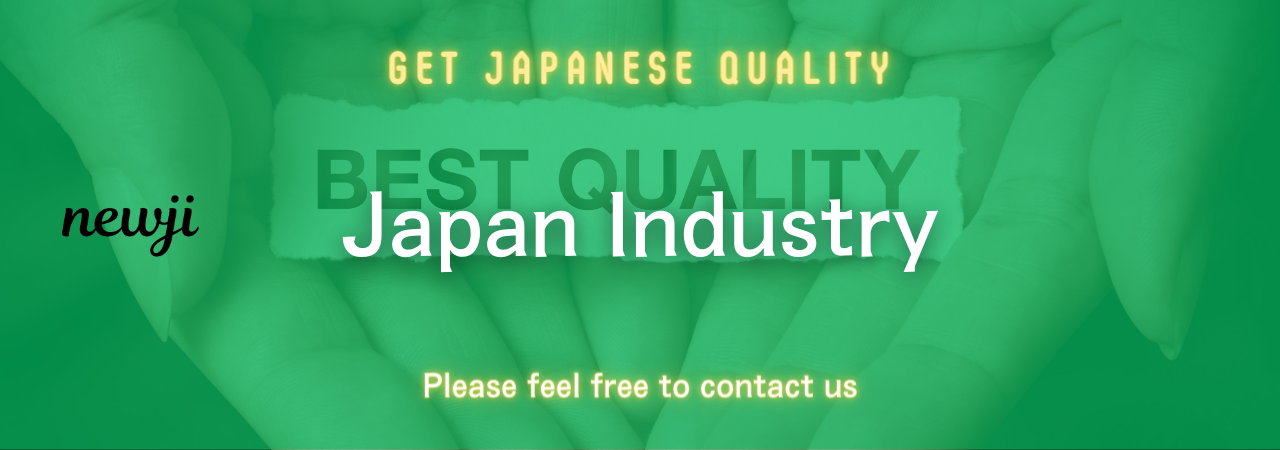
目次
Understanding Process Management
Process management is a systematic approach that helps organizations streamline their operations and improve efficiency.
In the manufacturing industry, effective process management can significantly reduce lead time, which is the duration it takes from the start of production to the final delivery of the product.
By understanding and implementing process management techniques, manufacturers can ensure timely production and meet customer demands promptly.
Lead time is a crucial factor for any manufacturing business.
Reducing it not only improves customer satisfaction but also increases competitiveness in the market.
With shorter lead times, companies can respond more quickly to market changes, reduce inventory costs, and improve cash flow.
So how does process management reduce lead time in the manufacturing industry?
Let’s explore some key aspects and examples that highlight the impact of efficient process management.
Identifying Bottlenecks
One of the primary steps in process management is identifying bottlenecks — stages where production slows down due to inefficiencies.
These can be caused by various factors such as equipment malfunctions, inadequate workforce, or improper scheduling.
By pinpointing these problem areas, manufacturers can take corrective actions to alleviate the blockage and streamline operations.
For example, a factory producing electronic components might find that their assembly line frequently halts due to a lack of components.
By addressing supplier delays or improving inventory management, they can ensure a steady flow of materials, thus reducing downtime and lead time.
Standardizing Operations
Standardization is another essential aspect of process management.
By creating uniform procedures and protocols, manufacturers can minimize variability and improve consistency in production.
Standardized operations ensure that every stage of production is carried out with precision and accuracy, reducing errors and delays.
This approach not only speeds up the manufacturing process but also enhances the overall quality of the products.
Consider a car manufacturing plant where each vehicle must undergo rigorous quality checks.
By developing a standardized checklist for inspections, the plant can ensure that all vehicles meet quality standards while significantly reducing the time spent on each check.
Implementing Lean Manufacturing
Lean manufacturing is a methodology that focuses on minimizing waste within a manufacturing system without sacrificing productivity.
Derived from the Toyota Production System, lean principles aim to enhance efficiency, cut costs, and improve lead times.
Techniques such as Just-In-Time (JIT) production can drastically reduce lead times by aligning production schedules with demand.
This means components are produced only when needed, rather than being stored in large quantities.
Consequently, it reduces inventory costs and ensures that resources are utilized efficiently.
Incorporating lean manufacturing practices can lead to remarkable improvements in lead time.
For instance, a clothing manufacturer might adopt a JIT approach to produce garments as orders arrive, rather than maintaining a large stockpile of finished goods.
This flexibility allows the company to respond swiftly to fashion trends and customer preferences.
Embracing Automation
Automation plays a critical role in reducing lead time by enhancing process efficiency and reducing manual intervention.
By automating repetitive and time-consuming tasks, manufacturers can ensure faster production cycles and improved accuracy.
For instance, an automotive parts manufacturer might utilize robotic welders for assembling components.
This not only accelerates production but also minimizes human errors, ensuring high-quality outputs.
With reduced manual labor, the workforce can focus on more value-added tasks, leading to overall productivity gains.
Effective Communication and Collaboration
Effective communication and collaboration among teams are vital in process management.
By ensuring that all departments are aligned and informed about production schedules, potential disruptions, and resource availability, manufacturers can prevent delays and maintain a smooth workflow.
Utilizing collaborative tools and platforms can facilitate real-time information sharing and enhance coordination among teams.
For example, a confectionery company might use cloud-based software to track production progress and communicate with suppliers about raw material needs.
By doing so, they can preemptively address any shortages and avoid production delays.
Continuous Improvement and Monitoring
In process management, continuous improvement is crucial for achieving sustainable lead time reductions.
Manufacturers should regularly review their processes, gather feedback, and identify areas for improvement.
By implementing a robust monitoring system, companies can track key performance metrics and evaluate the effectiveness of their process management strategies.
Tools such as Six Sigma and Total Quality Management (TQM) provide frameworks for ongoing assessment and improvement.
For example, a furniture manufacturer may adopt a process improvement strategy where they periodically evaluate their production line for efficiency.
By analyzing data on production times, machine performance, and workforce productivity, they can identify trends and make informed decisions that enhance efficiency and reduce lead time.
Conclusion
Process management is an invaluable tool for the manufacturing industry to reduce lead time and boost operational efficiency.
By identifying bottlenecks, standardizing operations, embracing lean manufacturing, utilizing automation, ensuring effective communication, and committing to continuous improvement, manufacturers can significantly cut down lead times.
These strategies not only enhance customer satisfaction but also foster a culture of innovation and adaptability, keeping manufacturers competitive in today’s dynamic market.
By prioritizing process management, companies can thrive and achieve sustainable growth in the manufacturing sector.
資料ダウンロード
QCD調達購買管理クラウド「newji」は、調達購買部門で必要なQCD管理全てを備えた、現場特化型兼クラウド型の今世紀最高の購買管理システムとなります。
ユーザー登録
調達購買業務の効率化だけでなく、システムを導入することで、コスト削減や製品・資材のステータス可視化のほか、属人化していた購買情報の共有化による内部不正防止や統制にも役立ちます。
NEWJI DX
製造業に特化したデジタルトランスフォーメーション(DX)の実現を目指す請負開発型のコンサルティングサービスです。AI、iPaaS、および先端の技術を駆使して、製造プロセスの効率化、業務効率化、チームワーク強化、コスト削減、品質向上を実現します。このサービスは、製造業の課題を深く理解し、それに対する最適なデジタルソリューションを提供することで、企業が持続的な成長とイノベーションを達成できるようサポートします。
オンライン講座
製造業、主に購買・調達部門にお勤めの方々に向けた情報を配信しております。
新任の方やベテランの方、管理職を対象とした幅広いコンテンツをご用意しております。
お問い合わせ
コストダウンが利益に直結する術だと理解していても、なかなか前に進めることができない状況。そんな時は、newjiのコストダウン自動化機能で大きく利益貢献しよう!
(Β版非公開)