- お役立ち記事
- Supplier performance evaluation method for manufacturing industry useful for purchasing department
Supplier performance evaluation method for manufacturing industry useful for purchasing department
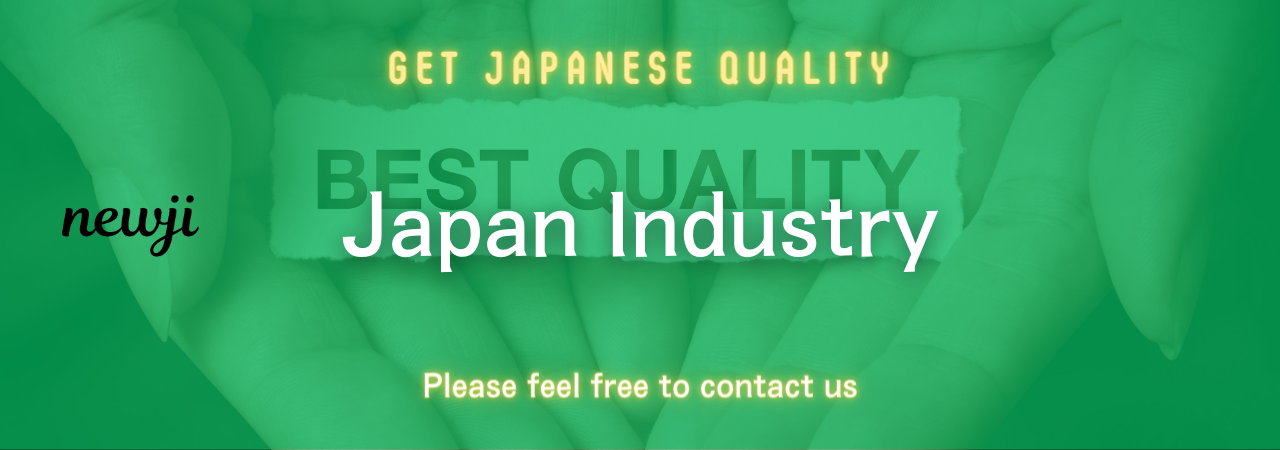
目次
Introduction to Supplier Performance Evaluation
In the dynamic world of manufacturing, the purchasing department plays a crucial role in maintaining the flow of production.
A critical component of this function is the assessment of supplier performance.
A robust supplier performance evaluation method not only ensures the smooth operation of supply chains but also drives improvements in cost efficiency and product quality.
This article explores effective supplier performance evaluation methods that can be used by the purchasing department in the manufacturing industry.
Why Supplier Performance Evaluation Matters
Supplier performance evaluation is essential for several reasons.
First, it enables manufacturers to identify reliable suppliers who contribute positively to their supply chain, ensuring timely delivery of quality materials and components.
Second, it helps in recognizing potential risks within the supplier base, allowing companies to address issues before they escalate into significant disruptions.
Third, evaluating suppliers can lead to better negotiation outcomes, as performance data provide critical leverage in discussions.
In turn, this fosters a collaborative relationship, enhancing overall supply chain resilience.
Key Metrics for Supplier Performance Evaluation
To accurately assess supplier performance, it is vital to establish clear and measurable metrics.
Several key performance indicators (KPIs) can be utilized:
1. Delivery Performance
Assessing delivery performance is fundamental in supplier evaluation.
It includes tracking on-time delivery rates, lead times, and order fulfillment accuracy.
Suppliers who consistently meet delivery schedules contribute to minimizing production downtime and maintaining inventory levels.
2. Quality of Products
Product quality is a crucial metric, as poor quality can affect the manufacturing process and lead to defective end-products.
Measurement tools such as defect rates, number of returns, or compliance with quality standards can help evaluate how well a supplier meets quality requirements.
3. Cost Management
Effective cost management by suppliers can significantly impact a manufacturer’s bottom line.
Evaluating a supplier’s ability to offer competitive pricing, manage production costs, and provide value-add services is a critical aspect of performance review.
4. Responsiveness and Communication
Effective communication and the ability to respond swiftly to inquiries indicate a supplier’s commitment and customer service capability.
Assessing how quickly a supplier addresses issues or changes in order demands offers insight into their operational flexibility.
5. Sustainability and Ethical Practices
Increasingly, manufacturers are focusing on sustainable sourcing as part of their supplier evaluation process.
Suppliers are assessed based on their environmental impact, adherence to ethical labor practices, and corporate social responsibility.
Evaluating these elements ensures alignment with the manufacturer’s values and regulatory compliance.
Methods for Supplier Performance Evaluation
Once performance metrics are established, the next step is to select appropriate evaluation methods.
Here are some popular approaches:
1. Scorecard Method
The scorecard method involves grading suppliers across various performance categories, using a predetermined scale.
Each category is weighted according to its importance to the manufacturing process.
This visual representation aids in identifying strengths and weaknesses, guiding strategic decisions with clear data.
2. Benchmarking
Benchmarking compares the performance of suppliers against industry standards or peer groups.
This approach identifies areas where a supplier is falling behind or excelling, which can drive targeted improvements or innovations.
3. Supplier Audits
Conducting on-site supplier audits helps verify compliance with quality standards and contractual obligations.
Audits can uncover operational inefficiencies or processes that need refining, providing a direct channel for feedback and improvement.
Implementing Supplier Performance Evaluation
Implementing a supplier performance evaluation process requires commitment and collaboration across different departments within an organization.
Here are some steps to successfully integrate a supplier performance evaluation method:
1. Define Objectives
Clear objectives that align with the company’s strategic goals should be set.
This includes identifying specific outcomes, such as improving supplier quality or reducing delivery times.
2. Communicate Expectations
Suppliers should be informed about evaluation criteria and expectations, which enhances transparency and fosters a partnership approach.
Regular communication ensures that both parties are aligned in their objectives.
3. Utilize Technology
Leveraging technology, such as supplier management software, can streamline the evaluation process.
These tools facilitate the collection and analysis of performance data, making it easier to track progress and generate insights.
4. Continuous Improvement
Supplier performance evaluation should be an ongoing process, not a one-time event.
Regular assessment and feedback loops ensure that suppliers are continuously working towards performance improvement.
Conclusion
In the manufacturing industry, the purchasing department plays a key role in ensuring efficient operations by selecting and managing suitable suppliers.
Implementing a systematic supplier performance evaluation method provides valuable insights into supplier capabilities, leading to more informed decision-making.
By employing methods such as scorecards, benchmarking, and audits, manufacturers can optimize their supply chain processes, enhance supplier relationships, and ultimately improve competitive advantage.
Above all, maintaining a proactive, communicative, and data-driven approach will sustain supplier excellence and drive long-term business success.
資料ダウンロード
QCD調達購買管理クラウド「newji」は、調達購買部門で必要なQCD管理全てを備えた、現場特化型兼クラウド型の今世紀最高の購買管理システムとなります。
ユーザー登録
調達購買業務の効率化だけでなく、システムを導入することで、コスト削減や製品・資材のステータス可視化のほか、属人化していた購買情報の共有化による内部不正防止や統制にも役立ちます。
NEWJI DX
製造業に特化したデジタルトランスフォーメーション(DX)の実現を目指す請負開発型のコンサルティングサービスです。AI、iPaaS、および先端の技術を駆使して、製造プロセスの効率化、業務効率化、チームワーク強化、コスト削減、品質向上を実現します。このサービスは、製造業の課題を深く理解し、それに対する最適なデジタルソリューションを提供することで、企業が持続的な成長とイノベーションを達成できるようサポートします。
オンライン講座
製造業、主に購買・調達部門にお勤めの方々に向けた情報を配信しております。
新任の方やベテランの方、管理職を対象とした幅広いコンテンツをご用意しております。
お問い合わせ
コストダウンが利益に直結する術だと理解していても、なかなか前に進めることができない状況。そんな時は、newjiのコストダウン自動化機能で大きく利益貢献しよう!
(Β版非公開)