- お役立ち記事
- How to strengthen production process management by introducing smart factories
How to strengthen production process management by introducing smart factories
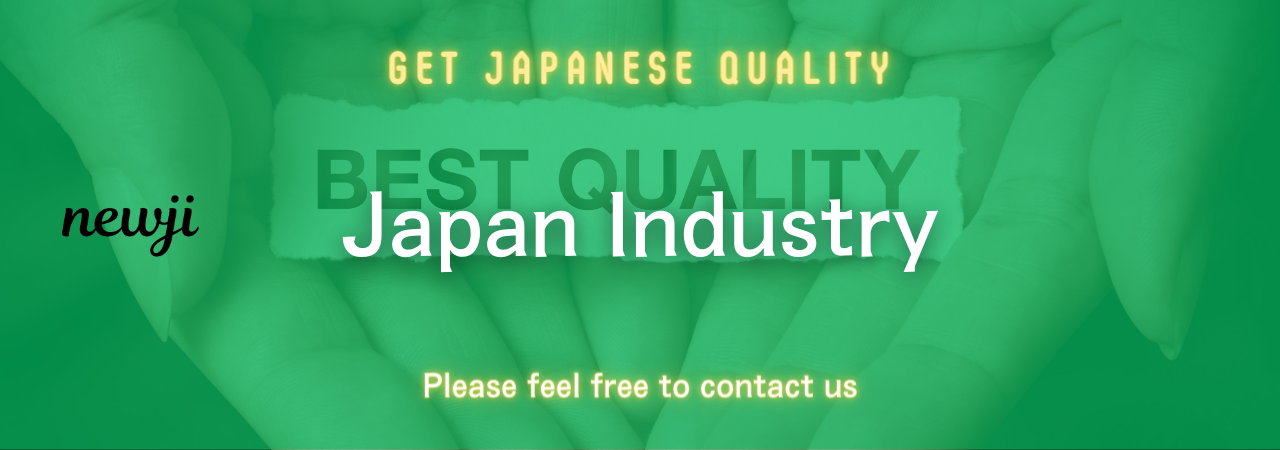
目次
Understanding Smart Factories
The concept of smart factories has significantly transformed the landscape of industrial production, offering opportunities for increasing efficiency and enhancing production process management.
A smart factory is an advanced manufacturing setup where physical production processes are integrated with digital technology, IoT, machine learning, and robotics.
This results in a highly collaborative and flexible manufacturing system that uses a continuous flow of data to optimize resources and achieve production goals.
These factories are often referred to as the future of manufacturing, and rightly so, as they incorporate cutting-edge technologies to streamline processes and improve product quality.
The Role of Smart Factory in Production Management
Every manufacturing unit wants to deliver the best quality products in the most efficient manner possible.
A smart factory enhances production management by providing tools and technologies that enable precise control and monitoring of every stage of the production process.
These technologies include sensors and IoT devices that collect real-time data, allowing managers to make informed decisions that can enhance productivity and reduce waste.
By offering instantaneous communication and transparency among different production stages, smart factories help in identifying bottlenecks or inefficiencies in the system quickly.
Key Features of Smart Factories
Smart factories come with a variety of features that aid production process management.
One of the most crucial features is automation and robotics, which help in executing repetitive tasks accurately and consistently, reducing the likelihood of human error.
Another essential feature is the use of sensors and data analytics, which provide comprehensive insights into production processes.
This data can be used to forecast demand, manage supply chains more effectively, and adjust schedules to optimize resource usage.
Moreover, smart factories rely heavily on cloud computing.
This feature ensures that all shared data is securely stored and accessible to authorized personnel anywhere in the facility, ensuring seamless production management.
Steps to Implement Smart Factories
Transitioning to a smart factory may seem overwhelming, but it can be broken down into manageable steps.
Here is a structured approach to help you implement smart production management systems.
Step 1: Assess and Plan
The first step is to conduct a thorough assessment of your current production processes.
Identify the areas that need improvement and determine how smart technologies can address these challenges.
Once the assessment is complete, devise a strategic plan outlining your objectives, budget, and timeline for implementation.
Keep in mind the anticipated challenges, and plan for contingencies to avoid any potential roadblocks.
Step 2: Invest in Suitable Technology
Choose technologies that best fit your operational needs and budget.
Invest in fundamental components like IoT devices, sensors, and automation tools that provide the backbone for smart manufacturing.
Consider scalable solutions since your factory’s needs might evolve over time.
Conduct a cost-benefit analysis to ensure that the returns justify the investment.
Step 3: Training and Development
Training the workforce is vital for the successful implementation of a smart factory.
Employees must be well-acquainted with new technologies and understand how to operate and maintain these systems.
Offer rigorous training sessions and provide ongoing support to help staff adapt to the technological changes.
This not only boosts their confidence but also enhances operational efficiency.
Step 4: Execution and Review
Start implementing the smart systems gradually, focusing on high-priority areas first.
Monitor the performance of these systems closely to ensure they meet business objectives and troubleshooting issues as they arise.
Once the system is fully operational, conduct regular reviews and gather feedback from workers to identify areas for further improvement.
This helps to fine-tune processes and maintain production process excellence.
Benefits of Smart Factories in Production Management
The introduction of smart factories comes with numerous benefits.
Increased Productivity and Efficiency
Smart factories leverage automation and data analysis, resulting in faster production cycles, reduced downtime, and the ability to meet production goals more consistently.
Predictive maintenance based on real-time data minimizes machine breakdowns and extends their lifespan, subsequently decreasing operational costs.
Improved Product Quality
With real-time monitoring and data insights, smart factories significantly reduce defects and ensure optimal product quality.
The data-driven insights also foster continuous improvement initiatives focused on quality enhancement.
Enhanced Flexibility
Smart factories provide a higher degree of flexibility, allowing for the customization of production processes according to dynamic market demands.
This adaptability means manufacturers can swiftly switch production lines, introduce new product designs, and respond to consumer feedback more effectively.
Better Resource Management
By closely monitoring resource consumption, smart factories optimize energy and raw material usage, thereby reducing waste and promoting sustainable practices.
This not only lowers costs but also supports environmental conservation efforts.
Conclusion
The integration of smart factories into production process management marks a significant shift towards the future of manufacturing.
These factories, with their advanced technologies, offer a pathway for businesses to optimize production processes, reduce costs, and enhance product quality.
By embracing smart manufacturing, companies can remain competitive and achieve sustainable growth in an ever-evolving industrial landscape.
To fully leverage the potential of smart factories, businesses must remain committed to continuous innovation, training, and evaluation of their systems and processes.
In doing so, they will not only strengthen their production management but also achieve excellence in their respective industries.
資料ダウンロード
QCD調達購買管理クラウド「newji」は、調達購買部門で必要なQCD管理全てを備えた、現場特化型兼クラウド型の今世紀最高の購買管理システムとなります。
ユーザー登録
調達購買業務の効率化だけでなく、システムを導入することで、コスト削減や製品・資材のステータス可視化のほか、属人化していた購買情報の共有化による内部不正防止や統制にも役立ちます。
NEWJI DX
製造業に特化したデジタルトランスフォーメーション(DX)の実現を目指す請負開発型のコンサルティングサービスです。AI、iPaaS、および先端の技術を駆使して、製造プロセスの効率化、業務効率化、チームワーク強化、コスト削減、品質向上を実現します。このサービスは、製造業の課題を深く理解し、それに対する最適なデジタルソリューションを提供することで、企業が持続的な成長とイノベーションを達成できるようサポートします。
オンライン講座
製造業、主に購買・調達部門にお勤めの方々に向けた情報を配信しております。
新任の方やベテランの方、管理職を対象とした幅広いコンテンツをご用意しております。
お問い合わせ
コストダウンが利益に直結する術だと理解していても、なかなか前に進めることができない状況。そんな時は、newjiのコストダウン自動化機能で大きく利益貢献しよう!
(Β版非公開)