- お役立ち記事
- How to achieve results with manufacturing talent development programs
How to achieve results with manufacturing talent development programs
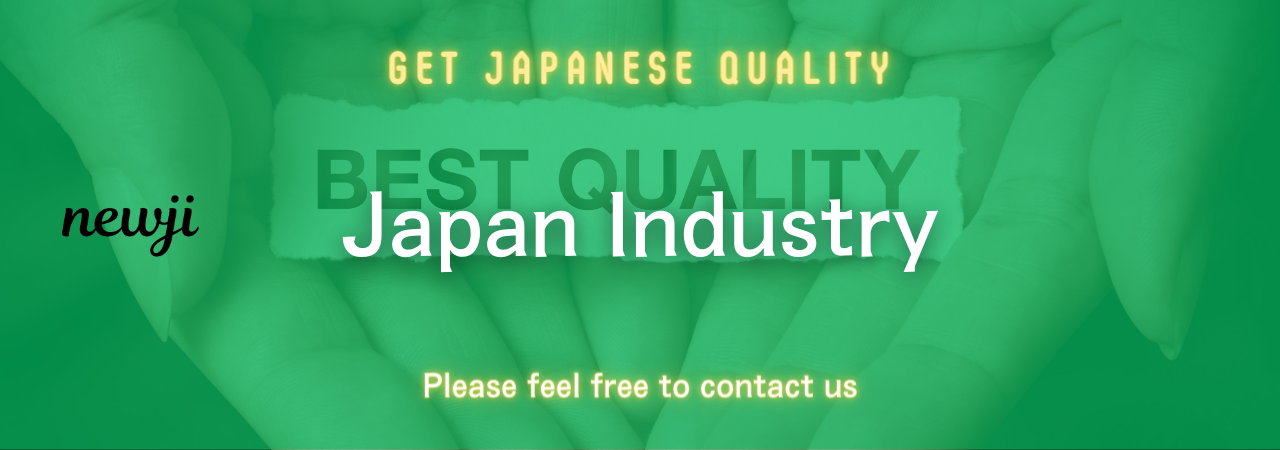
目次
Understanding the Importance of Talent Development in Manufacturing
In the constantly evolving world of manufacturing, the significance of talent development programs cannot be overstated.
Manufacturing is no longer just about machinery and assembly lines.
It now requires a skilled workforce that can adapt to technological advancements and new methodologies.
To remain competitive, companies must invest in the growth and development of their human resources.
Talent development programs are designed to enhance the skills and competencies of employees.
These programs contribute to the overall success of the organization by improving productivity, innovation, and employee satisfaction.
By cultivating a culture of continuous improvement and learning, manufacturing companies can create a strong foundation for long-term success.
Identifying Key Skills for Manufacturing Success
Before implementing a talent development program, it’s essential to identify the key skills and competencies required for success in the manufacturing sector.
These skills often include technical abilities, problem-solving, teamwork, and leadership.
Each manufacturing company may have unique needs depending on its products and processes.
Thus, conducting a thorough analysis of current workforce capabilities and future requirements is crucial.
Technical skills are the backbone of manufacturing.
Employees must be trained to handle complex machinery, understand production processes, and maintain safety standards.
Problem-solving abilities allow employees to address issues efficiently, ensuring minimal disruption in the production line.
Teamwork and communication are equally important, as manufacturing often involves collaboration across different departments.
Encouraging strong leadership skills within the workforce ensures that there are capable individuals ready to take charge and guide others.
Developing an Effective Talent Development Program
An effective talent development program in manufacturing begins with establishing clear objectives.
What does the company hope to achieve with this program?
Are there specific skills that need to be improved, or is the goal to prepare employees for future leadership roles?
Once these objectives are set, the program should be designed in a way that aligns with the company’s strategic goals.
This might include a combination of on-the-job training, workshops, and e-learning modules.
On-the-job training allows employees to gain practical experience under the guidance of seasoned professionals.
Workshops and seminars offer opportunities for learning new techniques and strategies that can be implemented within the company.
E-learning modules provide flexibility, enabling employees to learn at their own pace and revisit material as needed.
Monitoring and evaluation are essential components of any talent development program.
Regular assessments help identify areas for improvement and measure the success of the program.
Engaging and Retaining Manufacturing Talent
A successful talent development program does more than just enhance skills; it also plays a vital role in employee engagement and retention.
When employees feel valued and see opportunities for growth, they are more likely to stay with the company long-term.
This not only reduces turnover costs but also contributes to a more experienced and knowledgeable workforce.
To engage employees, it’s important to involve them in the development process.
Seek their feedback on the types of training they find most beneficial and incorporate their suggestions into the program.
Creating a personalized learning path for each employee can also enhance engagement.
Recognition and rewards for achievements in development can motivate employees to continue their learning journey.
These can range from simple acknowledgments to career advancement opportunities.
Leveraging Technology in Talent Development
Technology plays a crucial role in modern talent development programs.
With advancements in digital tools and platforms, manufacturing companies can offer more interactive and personalized learning experiences.
Virtual reality (VR) and augmented reality (AR) are increasingly being used for simulation training, providing a safe and immersive environment for employees to practice skills without disrupting actual production.
Learning management systems (LMS) offer an efficient way to track progress and manage training materials.
They allow for customizable content, making it easier to tailor the learning experience to the needs of the business and its employees.
Overcoming Challenges in Manufacturing Talent Development
While the benefits of talent development programs are clear, implementing them in the manufacturing sector does come with challenges.
One common issue is resistance to change, particularly among employees who are accustomed to existing methods.
Addressing this requires clear communication about the benefits of the program and ensuring that there is support at all levels of the organization.
Limited resources can also be a challenge, especially for smaller manufacturing companies.
In such cases, partnerships with educational institutions or industry groups can help provide access to necessary training resources.
Keeping up with rapid technological changes is another hurdle.
Continuous learning must be emphasized as part of the company culture to ensure that employees are always equipped with the latest skills and knowledge.
Conclusion
Investing in manufacturing talent development programs is not just beneficial; it is essential for the growth and competitiveness of a company.
By identifying the skills needed for success, developing effective training programs, and leveraging technology, manufacturing companies can nurture a workforce that is skilled, adaptable, and ready for future challenges.
Engaging employees in their personal development and addressing challenges head-on will further ensure that these programs achieve desired outcomes, leading to both individual and organizational success.
The commitment to developing talent is a powerful strategy that sets companies apart in a highly competitive manufacturing landscape.
資料ダウンロード
QCD調達購買管理クラウド「newji」は、調達購買部門で必要なQCD管理全てを備えた、現場特化型兼クラウド型の今世紀最高の購買管理システムとなります。
ユーザー登録
調達購買業務の効率化だけでなく、システムを導入することで、コスト削減や製品・資材のステータス可視化のほか、属人化していた購買情報の共有化による内部不正防止や統制にも役立ちます。
NEWJI DX
製造業に特化したデジタルトランスフォーメーション(DX)の実現を目指す請負開発型のコンサルティングサービスです。AI、iPaaS、および先端の技術を駆使して、製造プロセスの効率化、業務効率化、チームワーク強化、コスト削減、品質向上を実現します。このサービスは、製造業の課題を深く理解し、それに対する最適なデジタルソリューションを提供することで、企業が持続的な成長とイノベーションを達成できるようサポートします。
オンライン講座
製造業、主に購買・調達部門にお勤めの方々に向けた情報を配信しております。
新任の方やベテランの方、管理職を対象とした幅広いコンテンツをご用意しております。
お問い合わせ
コストダウンが利益に直結する術だと理解していても、なかなか前に進めることができない状況。そんな時は、newjiのコストダウン自動化機能で大きく利益貢献しよう!
(Β版非公開)