- お役立ち記事
- Key points for success in production equipment renewal projects at manufacturing sites
Key points for success in production equipment renewal projects at manufacturing sites
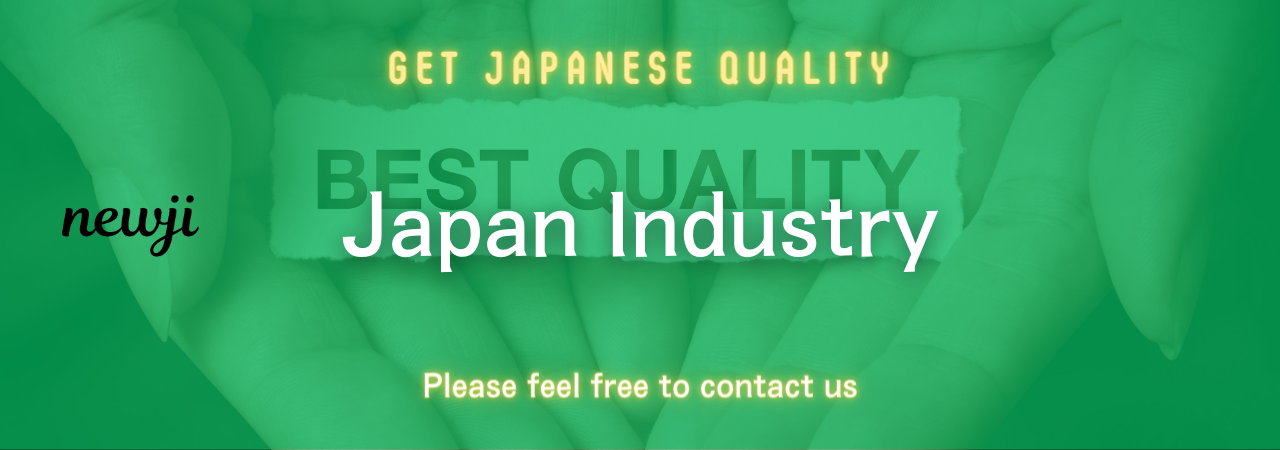
目次
Understanding the Importance of Production Equipment Renewal
Renewing production equipment is a significant undertaking at any manufacturing site.
It’s essential to grasp why these projects are crucial.
Outdated machinery can hinder production efficiency, lead to frequent breakdowns, and increase maintenance costs.
Moreover, it can affect product quality, safety, and overall operational effectiveness.
When equipment is modernized, manufacturers experience improved efficiencies and reduced downtime.
New technologies often come with enhanced features that allow for better precision and control, leading to higher-quality outputs.
Furthermore, newer equipment is typically more energy-efficient, aligning with sustainability goals and reducing utility expenses.
Setting Clear Goals for Equipment Renewal Projects
Before diving into an equipment renewal project, it’s vital to establish clear goals.
What are the desired outcomes?
Are you looking to increase capacity, reduce operation costs, enhance product quality, or all of the above?
By setting definitive objectives, you create a roadmap for the entire process.
These goals will guide decisions regarding equipment selection, budget allocation, and timeline management.
Clarity here will help in communicating the project scope to all stakeholders involved, ensuring everyone is aligned with the project’s purpose.
Conducting a Thorough Needs Assessment
A critical step in any equipment renewal project is conducting a needs assessment.
This involves evaluating the current equipment to determine inefficiencies, limitations, and areas needing improvement.
Engage with plant operators and technical staff who interact with the machinery daily, as their insights are invaluable.
Additionally, assess the technological trends within the industry.
Understanding what innovations are available can inform your decision on which new equipment to invest in.
While assessing needs, consider conducting a cost-benefit analysis to weigh the long-term benefits against the immediate expense.
Careful Selection of Equipment and Vendors
Choosing the right equipment and vendors is pivotal to the success of the renewal project.
Start by identifying equipment that aligns with your goals and assessment outcomes.
Ensure it meets the requirements for production volume, quality standards, and technological advancement.
Vendor selection is equally important.
Look for suppliers with a proven track record, solid after-sales support, and an understanding of your industry needs.
Involve stakeholders, such as procurement teams and finance departments, to ensure transparency and alignment throughout the purchasing process.
Negotiations with vendors can often lead to better deals, so be open and prepared to discuss terms.
Planning for Integration and Installation
Successful integration and installation of new equipment require meticulous planning.
Create a detailed plan that outlines each phase of the installation process, from logistics to on-site setup.
This plan should also include staff training as it ensures operators are familiar with the new systems.
Consider scheduling installation during times that minimally disrupt production, perhaps during planned maintenance shutdowns or slow production periods.
Establish a timeline with critical milestones to track progress and identify potential bottlenecks.
Flexibility in the plan is important to accommodate unforeseen challenges.
Training and Support for Staff
Introducing new equipment means changes in operation, which necessitates comprehensive training for the staff.
Training programs should be structured to equip staff with the necessary skills to operate and maintain the new equipment efficiently.
Engage with vendors to provide initial training, but also consider developing in-house training capabilities for ongoing education and troubleshooting.
Ongoing support is crucial to ensure any operational challenges are promptly addressed, minimizing disruptions.
Employee adaptation not only improves productivity but also boosts morale as staff feel competent and comfortable in their roles.
Monitoring and Evaluation Post-Installation
Once new equipment is installed, monitoring and evaluation become critical to measure the project’s success.
Establish performance metrics based on the goals set before the project began.
Regularly review these metrics to assess improvements in efficiency, production quality, and cost savings.
Feedback loops should be created for operators and maintenance personnel to report any issues or recommendations for further enhancements.
Schedule periodic evaluations to make necessary adjustments, ensuring the equipment continues to meet evolving production demands.
Continuous Improvement and Maintenance
The renewal project is not complete when the new equipment is up and running.
Continuous improvement should be a core part of the strategy.
Embrace a culture of ongoing learning and adaptation, ensuring that the equipment continues to perform optimally.
Regular maintenance schedules should be established to prevent downtime and extend the equipment’s lifespan.
Stay informed about updates or upgrades offered by the vendor, as these can enhance performance and offer competitive advantages.
In conclusion, the success of production equipment renewal projects hinges on thorough planning, effective communication, and ongoing evaluation.
When these elements are prioritized, manufacturing sites can experience significant improvements in efficiency, quality, and cost management, ultimately leading to greater competitiveness in the market.
資料ダウンロード
QCD調達購買管理クラウド「newji」は、調達購買部門で必要なQCD管理全てを備えた、現場特化型兼クラウド型の今世紀最高の購買管理システムとなります。
ユーザー登録
調達購買業務の効率化だけでなく、システムを導入することで、コスト削減や製品・資材のステータス可視化のほか、属人化していた購買情報の共有化による内部不正防止や統制にも役立ちます。
NEWJI DX
製造業に特化したデジタルトランスフォーメーション(DX)の実現を目指す請負開発型のコンサルティングサービスです。AI、iPaaS、および先端の技術を駆使して、製造プロセスの効率化、業務効率化、チームワーク強化、コスト削減、品質向上を実現します。このサービスは、製造業の課題を深く理解し、それに対する最適なデジタルソリューションを提供することで、企業が持続的な成長とイノベーションを達成できるようサポートします。
オンライン講座
製造業、主に購買・調達部門にお勤めの方々に向けた情報を配信しております。
新任の方やベテランの方、管理職を対象とした幅広いコンテンツをご用意しております。
お問い合わせ
コストダウンが利益に直結する術だと理解していても、なかなか前に進めることができない状況。そんな時は、newjiのコストダウン自動化機能で大きく利益貢献しよう!
(Β版非公開)