- お役立ち記事
- Metal Fractography and Applications in Failure Mechanism and Cause Analysis
Metal Fractography and Applications in Failure Mechanism and Cause Analysis
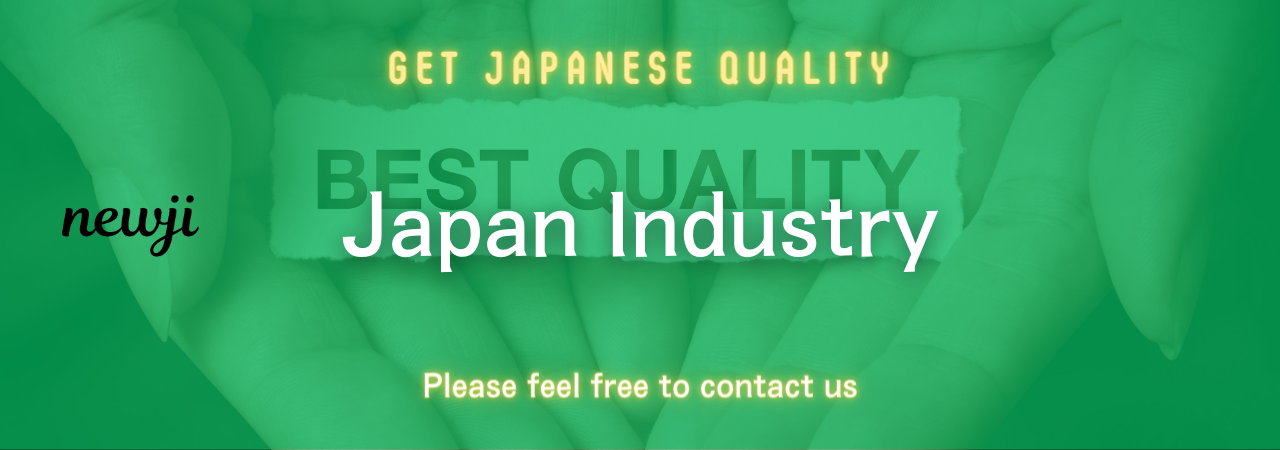
目次
Understanding Metal Fractography
Fractography is a fascinating branch of materials science focused on the study of fracture surfaces of materials.
Metal fractography, in particular, involves examining the broken surfaces of metallic materials to understand the causes of failure.
This discipline combines principles from both engineering and science, providing valuable insights into the underlying mechanisms that lead to material breakdown.
The analysis typically begins by visually inspecting the fracture surfaces using different magnification levels.
The detailed examination can be conducted using optical microscopes or more sophisticated electron microscopes.
These tools allow engineers and researchers to identify various features on the fracture surface that can indicate how and why a material failed.
The Importance of Metal Fractography in Industry
In industries where metal plays a crucial role, such as automotive, aerospace, and construction, understanding why and how metals fail is essential.
Failures can lead to costly repairs, downtime, and even catastrophic accidents.
Metal fractography provides the necessary insights to prevent recurrence by analyzing the physical characteristics of fractures.
Moreover, metal fractography aids in improving material design and manufacturing processes.
By recognizing the signs of stress and fatigue in metals, engineers can enhance the durability and reliability of components.
This leads to the production of safer and longer-lasting products.
Common Fracture Types in Metals
Different types of fractures can occur in metals, each providing clues about the failure mechanism.
The most commonly analyzed fractures include ductile, brittle, fatigue, and stress-corrosion fractures.
Ductile Fractures
Ductile fractures are characterized by significant plastic deformation before failure.
These fractures tend to have a rough, fibrous appearance, often with large dimpled areas on the fracture surface.
The presence of ductile fractures suggests that the material was able to absorb a considerable amount of energy before breaking.
Brittle Fractures
Brittle fractures, in contrast, occur with little to no preceding plastic deformation.
These fractures appear smooth and flat with a shiny, crystalline appearance.
Brittle fractures usually indicate a sudden failure, often due to low temperatures, high strain rates, or the presence of stress concentrators like sharp notches or cracks.
Fatigue Fractures
Fatigue fractures develop over time due to repeated loading and unloading cycles.
They can be identified by their beach-mark or striation patterns, indicative of the progressive nature of the crack growth.
Fatigue fractures are prevalent in components subjected to cyclic stresses like engine parts and aircraft wings.
Stress-Corrosion Cracking
Stress-corrosion cracking occurs when a material cracks due to the combined effects of tensile stress and corrosive environments.
These fractures are typically intergranular, following the grain boundaries of a metal.
Industrially significant, they pose a substantial threat, particularly to metals exposed to harsh chemical environments.
Applications of Metal Fractography in Failure Analysis
Metal fractography is extensively applied in failure analysis to ascertain the root cause of failures in metallic components.
This approach involves thorough examination and documentation of the fracture surface to trace the failure history.
Root Cause Identification
One of the primary applications is determining the root cause of a failure.
Through fractography, investigators can deduce whether the material failed due to design flaws, manufacturing defects, inappropriate material selection, or unexpected service conditions.
By pinpointing the cause, organizations can adopt corrective measures to avoid such failures in the future.
Quality Control and Assurance
In manufacturing, metal fractography serves as a powerful tool for quality control and assurance.
It helps in verifying whether production methods and materials meet required standards.
Fracture analysis can identify issues like welding defects or improper heat treatments, which might reduce a component’s strength and durability.
Product Development and Improvement
Metal fractography significantly contributes to product development and improvement.
By understanding the conditions under which materials fail, engineers can innovate designs that distribute stress more evenly.
They can also select alloys or introduce coatings that enhance resistance to specific types of wear.
Tools and Techniques in Metal Fractography
A range of sophisticated tools and techniques are employed to analyze fracture surfaces precisely.
The choice of technique often depends on the nature of the fracture and the information required.
Optical Microscopy
Optical microscopes provide the initial approach to fractography, offering a broad overview of the fracture surface.
While they offer lower magnification compared to electron microscopes, optical microscopes are crucial for locating areas of interest.
Scanning Electron Microscopy (SEM)
SEM is a pivotal tool in metal fractography, offering high-resolution images of fracture surfaces.
The high depth of field in SEM images allows for a three-dimensional view, crucial for understanding complex fracture features.
Energy Dispersive X-ray Spectroscopy (EDS)
EDS, often coupled with SEM, identifies the elemental composition of the fracture surface.
This technique is particularly useful for detecting foreign materials, contamination, or unexpected inclusions that may have contributed to failure.
The Future of Metal Fractography
As technology advances, the field of metal fractography continues to evolve.
The development of more sophisticated imaging and analytical tools will provide even deeper insights into fracture mechanisms.
Moreover, integrating artificial intelligence and machine learning could enhance the accuracy and speed of fractographic analysis.
Future trends may include the use of 3D fractography to fully visualize fracture surfaces in three dimensions, improving our understanding of complex fracture patterns.
These advancements will undoubtedly bolster industries in making safer, more reliable, and more efficient products.
In conclusion, metal fractography is a vital discipline in the analysis of failure mechanisms.
Its applications are crucial in diverse industries, helping to enhance safety, efficiency, and reliability.
As the field continues to evolve, it promises to offer even greater insights into the complex world of metal fractures.
資料ダウンロード
QCD調達購買管理クラウド「newji」は、調達購買部門で必要なQCD管理全てを備えた、現場特化型兼クラウド型の今世紀最高の購買管理システムとなります。
ユーザー登録
調達購買業務の効率化だけでなく、システムを導入することで、コスト削減や製品・資材のステータス可視化のほか、属人化していた購買情報の共有化による内部不正防止や統制にも役立ちます。
NEWJI DX
製造業に特化したデジタルトランスフォーメーション(DX)の実現を目指す請負開発型のコンサルティングサービスです。AI、iPaaS、および先端の技術を駆使して、製造プロセスの効率化、業務効率化、チームワーク強化、コスト削減、品質向上を実現します。このサービスは、製造業の課題を深く理解し、それに対する最適なデジタルソリューションを提供することで、企業が持続的な成長とイノベーションを達成できるようサポートします。
オンライン講座
製造業、主に購買・調達部門にお勤めの方々に向けた情報を配信しております。
新任の方やベテランの方、管理職を対象とした幅広いコンテンツをご用意しております。
お問い合わせ
コストダウンが利益に直結する術だと理解していても、なかなか前に進めることができない状況。そんな時は、newjiのコストダウン自動化機能で大きく利益貢献しよう!
(Β版非公開)