- お役立ち記事
- Analysis and strategies for successful factory improvement
月間77,185名の
製造業ご担当者様が閲覧しています*
*2025年2月28日現在のGoogle Analyticsのデータより
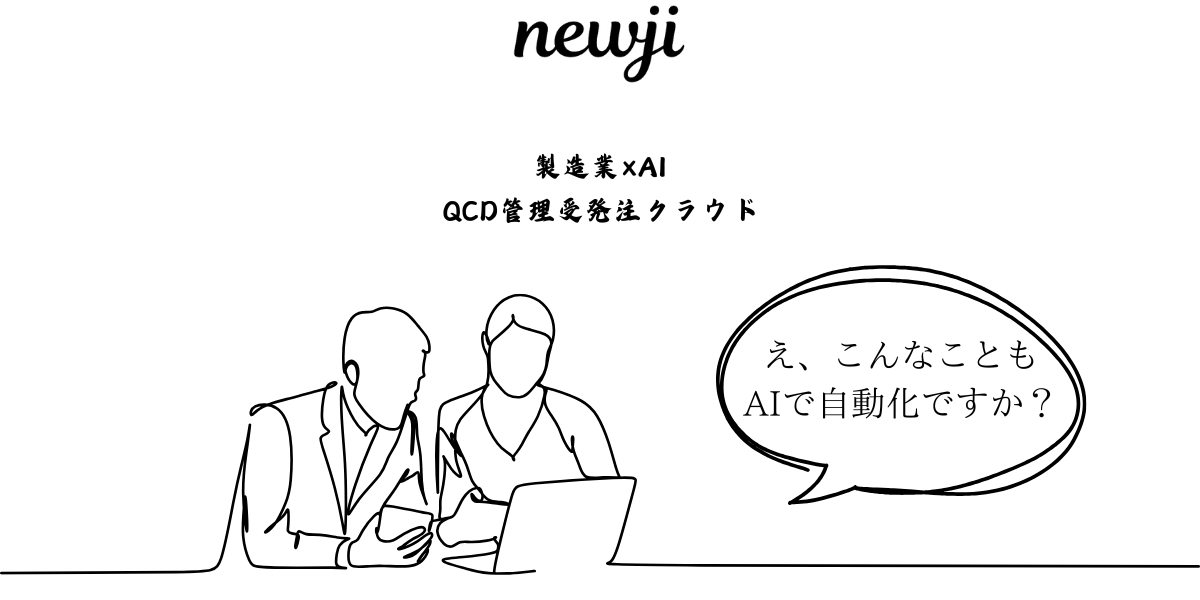
Analysis and strategies for successful factory improvement
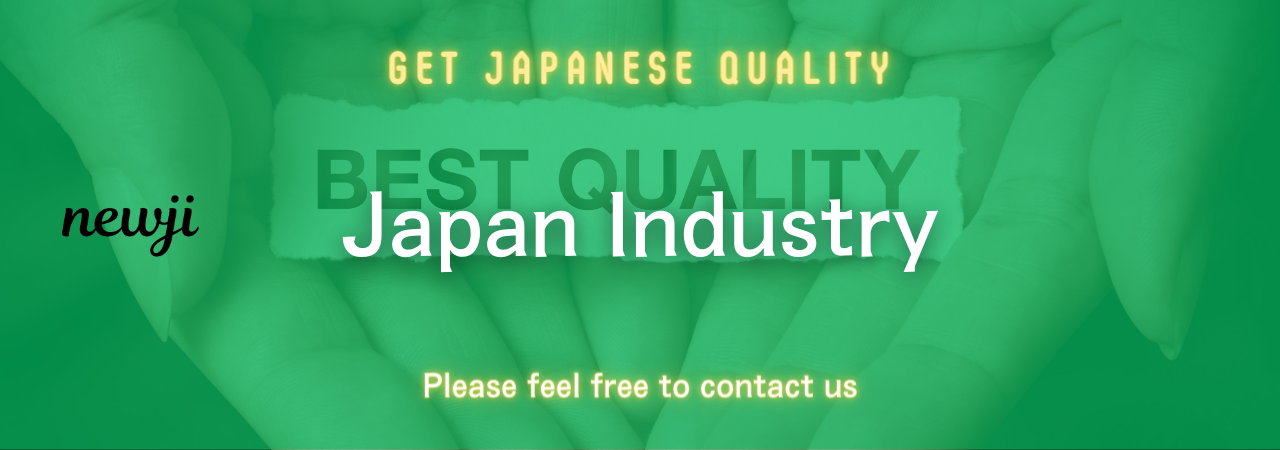
目次
Understanding the Importance of Factory Improvement
In today’s fast-paced industrial world, staying ahead requires continuous efforts in improving factory operations.
Companies that succeed in regular enhancements enjoy increased efficiency, reduced costs, and a competitive edge.
When you consider factory improvements, think of it as creating a finely tuned machine that can adapt to new challenges with ease.
Factories produce goods at an alarming rate, making them a backbone of modern economies.
However, this level of activity often leads to bottlenecks, inefficiencies, and other operational hitches.
Successful factory improvement means identifying these issues and implementing strategies to resolve them.
It’s about embracing change and innovation to achieve long-term success.
Key Areas for Improvement
Not every part of your factory requires the same level of attention.
By focusing on the following critical areas, you can initiate substantial improvements:
1. Streamlining Production Processes
Streamlining the production process is essential to factory improvement.
This involves examining current operations and identifying bottlenecks or unnecessary steps.
Creating a lean production process not only reduces waste but also maximizes productivity.
Mapping out your production flow can significantly aid in recognizing inefficiencies.
Using tools like flowcharts or value stream mapping can provide a clear picture of how your processes interact.
Armed with this information, you can implement changes that enhance the overall speed and efficiency of your operations.
2. Enhancing Quality Control
Quality control is a crucial component of factory improvement.
High standards of quality not only satisfy customers but also reduce costs associated with returns or defective products.
To enhance quality control, regularly review quality assurance processes and make adjustments based on feedback and data analysis.
Incorporating technology, such as automated testing and monitoring systems, can significantly improve quality levels.
This approach allows for real-time adjustments and minimizes human error, ensuring that only the best products reach the market.
3. Investing in Employee Training
An often-overlooked aspect of factory improvement is employee training.
Well-trained employees are both more efficient and more motivated, directly impacting the factory’s performance.
Regular training sessions can empower your workforce to operate machinery effectively and safely, reducing downtime and accidents.
Invest in comprehensive training programs that cover both technical skills and soft skills.
Encouraging continuous learning and development fosters a culture of improvement that resonates throughout your entire operation.
4. Implementing Advanced Technologies
Technological advancements are reshaping the way factories operate.
Embracing cutting-edge technology can lead to significant improvements in efficiency and productivity.
From automation and robotics to data analytics and IoT integration, these technologies can transform traditional factories into smart operations.
Begin by assessing the latest technologies relevant to your industry and evaluating their potential impact.
Incorporating these advancements gradually, while ensuring the workforce adapts to them, can yield substantial benefits.
Strategies for Successful Factory Improvement
Improving a factory requires a strategic approach that aligns with the overall goals of the company.
Consider the following strategies to ensure a successful factory improvement initiative:
1. Conduct Regular Audits
Regular audits are vital to understanding the strengths and weaknesses of your factory operations.
Conduct comprehensive audits that evaluate aspects such as processes, equipment, safety, and workforce efficiency.
The insights gained from these audits provide valuable data for crafting targeted improvement plans.
Through consistent auditing, you set a benchmark for continuous improvement.
It allows your factory to adapt quickly to necessary changes and remain competitive.
2. Foster a Culture of Continuous Improvement
Cultivating a culture of continuous improvement is central to sustainable factory enhancements.
Encourage your employees to be proactive in identifying issues and proposing solutions.
By establishing an environment where every member feels they play a critical role in improvement, you’ll benefit from collective innovation.
Introduce programs like Kaizen, which advocate for small, regular changes rather than massive overhauls.
Such methodologies not only sustain morale but also contribute to steady growth and development.
3. Set Clear Goals and KPIs
Clearly defined goals and Key Performance Indicators (KPIs) are essential for tracking progress and success.
Set realistic and measurable improvement targets that align with your company’s objectives.
Monitor these KPIs closely and adjust your strategies as needed to ensure you’re on track.
Remember that what gets measured, gets managed.
Having concrete goals keeps your factory improvement efforts focused and accountable.
4. Collaborate with Experts
Sometimes, seeking external expertise can accelerate your factory improvement initiatives.
Experts bring fresh perspectives and specialized knowledge that might be lacking internally.
Engage with consultants, industry specialists, or technology vendors to explore new solutions and innovations.
While collaboration incurs costs, the investment often results in greater efficiency and productivity, justifying the expense.
These partnerships can also introduce you to best practices and cutting-edge industry standards.
Overcoming Challenges in Factory Improvement
Improving a factory is not without its challenges.
Resistance to change, tight budgets, and unforeseen disruptions can slow down progress.
However, with a clear strategy and a resilient mindset, these obstacles can be overcome.
Prioritize communication and transparency throughout the improvement process.
Keeping all stakeholders informed and involved helps in gaining their support and easing transitions.
Be prepared to manage risk by having contingency plans for potential disruptions.
Flexibility and adaptability are critical components of successful factory improvements.
Factory improvement is not a one-time initiative but a continuous journey.
Efforts should be aligned with technological advancements and market demands to maintain a competitive position.
By adopting a purposeful approach, factories can achieve operational excellence and contribute to sustainable growth.
資料ダウンロード
QCD管理受発注クラウド「newji」は、受発注部門で必要なQCD管理全てを備えた、現場特化型兼クラウド型の今世紀最高の受発注管理システムとなります。
ユーザー登録
受発注業務の効率化だけでなく、システムを導入することで、コスト削減や製品・資材のステータス可視化のほか、属人化していた受発注情報の共有化による内部不正防止や統制にも役立ちます。
NEWJI DX
製造業に特化したデジタルトランスフォーメーション(DX)の実現を目指す請負開発型のコンサルティングサービスです。AI、iPaaS、および先端の技術を駆使して、製造プロセスの効率化、業務効率化、チームワーク強化、コスト削減、品質向上を実現します。このサービスは、製造業の課題を深く理解し、それに対する最適なデジタルソリューションを提供することで、企業が持続的な成長とイノベーションを達成できるようサポートします。
製造業ニュース解説
製造業、主に購買・調達部門にお勤めの方々に向けた情報を配信しております。
新任の方やベテランの方、管理職を対象とした幅広いコンテンツをご用意しております。
お問い合わせ
コストダウンが利益に直結する術だと理解していても、なかなか前に進めることができない状況。そんな時は、newjiのコストダウン自動化機能で大きく利益貢献しよう!
(β版非公開)