- お役立ち記事
- Smart factory implementation steps to achieve factory energy saving goals
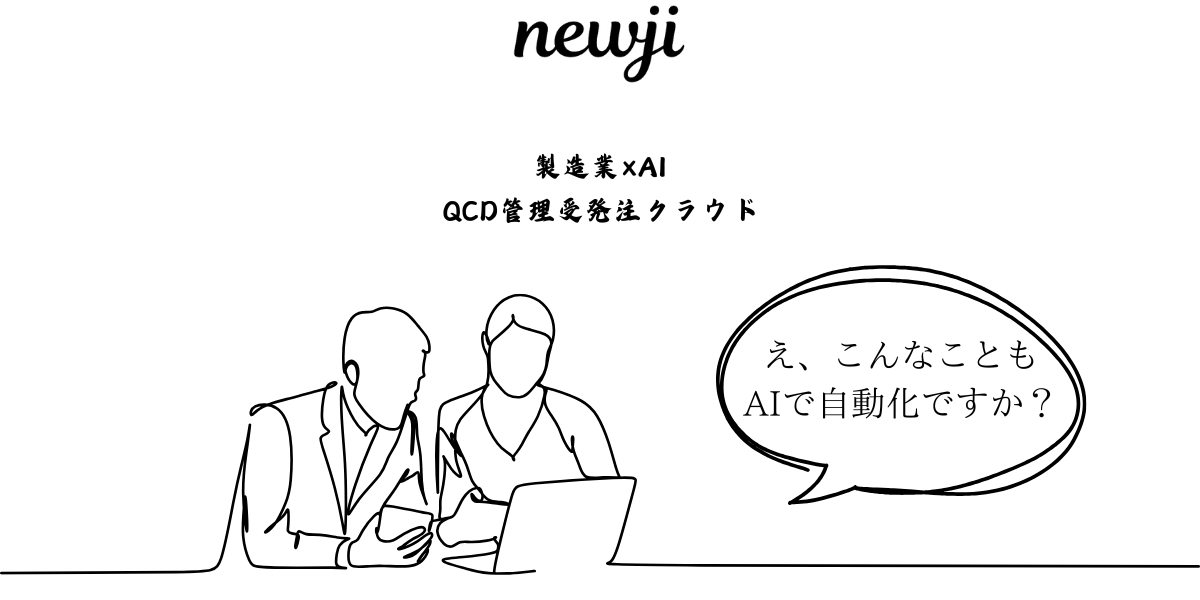
Smart factory implementation steps to achieve factory energy saving goals
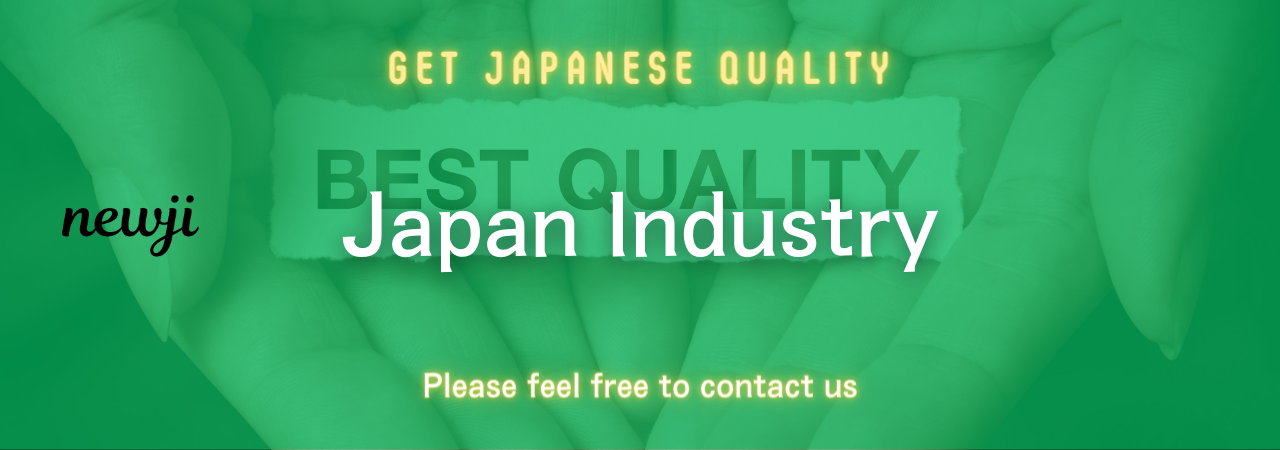
目次
Understanding the Concept of a Smart Factory
A smart factory represents a leap towards the future of manufacturing by integrating modern technologies into the production process.
These technologies include automation, data analytics, machine learning, and IoT (Internet of Things).
The objective of transforming a traditional factory into a smart factory is to enhance operational efficiency, improve product quality, and achieve significant energy savings.
At the heart of a smart factory is the seamless communication between machines, equipment, and human operators.
This interconnectedness allows for a flexible manufacturing setup capable of rapid adjustments and predictive maintenance.
The result is a more responsive and sustainable production environment.
Importance of Energy Efficiency in Manufacturing
Energy efficiency in manufacturing is vital for several reasons.
First, it reduces operational costs, freeing up financial resources for other vital business activities.
Second, it minimizes the carbon footprint of manufacturing operations, thus contributing to global environmental sustainability.
Lastly, adhering to energy efficiency standards can help a business comply with local and international regulations, avoiding potential fines and enhancing its public image as an environmentally responsible company.
A smart factory achieves energy efficiency through real-time monitoring and management of energy consumption.
The application of cutting-edge technologies means energy waste is minimized, and overall resource utilization is optimized.
Steps to Implement a Smart Factory
1. Assessing the Current State
The journey to a smart factory begins with a comprehensive assessment of the existing manufacturing setup.
This involves identifying current technologies, understanding production processes, and analyzing energy consumption patterns.
The insights from this assessment provide a clear baseline against which improvements can be measured.
Engaging with experts or consultants specializing in smart factory implementation can offer external perspectives and recommend proven strategies tailored to your unique business needs.
2. Setting Clear Goals
The second step is to define clear, achievable goals.
These goals should focus on specific outcomes like reducing energy consumption by a certain percentage, minimizing production downtime, or improving product quality.
Setting these objectives ensures that every aspect of the smart factory transformation aligns with broader business and sustainability goals.
Having specific measurements in place also allows for tracking progress and making data-driven adjustments to strategies and technologies over time.
3. Establishing a Robust Communication Network
For a factory to be truly smart, it needs a robust communication network that supports seamless data exchange between machines and systems.
This network should be capable of integrating new technologies and scaling as the factory grows or evolves.
Securing a strong IT infrastructure involves investing in high-speed internet, reliable data storage, and advanced cybersecurity measures to protect sensitive operational data.
4. Utilizing IoT and Automation
The integration of IoT devices and automation is central to a smart factory.
IoT devices collect data from various points in the production process, providing insights into energy usage, machine health, and production efficiency.
Automation, on the other hand, replaces manual processes with intelligent machines that can operate independently of human intervention.
This shift not only improves efficiency but also reduces energy consumption and errors, contributing to overall factory energy-saving goals.
5. Implementing Data Analytics and Machine Learning
Data is the lifeblood of a smart factory.
The ability to analyze this data enables predictive maintenance, optimizing scheduling, and enhancing production processes.
Machine learning algorithms process the data collected by IoT sensors to identify patterns, predict potential system failures, or anticipate maintenance needs, thereby preventing costly downtimes.
The utilization of advanced data analytics facilitates informed decision-making and continuous improvement in energy efficiency.
6. Training and Engaging Employees
Successful implementation of a smart factory requires a workforce that is skilled in using new technologies.
Training programs should be instituted to equip employees with the necessary skills and knowledge.
Engaging employees in the transformation process fosters a culture of innovation and shared responsibility towards achieving energy-saving goals.
Employee feedback should be actively sought, as it can provide unique insights into operational challenges and opportunities.
Overcoming Challenges in Smart Factory Implementation
Though the benefits of a smart factory are clear, businesses may face challenges during the transformation process.
One significant challenge is the initial investment in new technology and infrastructure.
However, this cost is often offset by long-term savings and efficiencies gained.
Another challenge is the integration of new systems with existing ones, which requires careful planning and execution to avoid disruptions in production.
A phased implementation approach can help manage this transition smoothly.
Measuring Success and Continuous Improvement
To ascertain the success of smart factory implementation, companies must establish key performance indicators (KPIs) that track progress toward the defined goals.
These KPIs may include metrics such as energy consumption rates, production efficiency levels, downtime occurrences, and overall cost savings.
Continuous monitoring and improvement are crucial for maintaining the advantages of a smart factory.
Technology is constantly evolving, and staying ahead requires a commitment to regularly upgrading systems and processes.
In conclusion, implementing a smart factory is a strategic move that not only enhances the efficiency of manufacturing operations but also significantly contributes to achieving energy-saving goals.
With careful planning, a focus on technology, and an engaged workforce, the transition to a smarter, more sustainable future is within reach.
資料ダウンロード
QCD調達購買管理クラウド「newji」は、調達購買部門で必要なQCD管理全てを備えた、現場特化型兼クラウド型の今世紀最高の購買管理システムとなります。
ユーザー登録
調達購買業務の効率化だけでなく、システムを導入することで、コスト削減や製品・資材のステータス可視化のほか、属人化していた購買情報の共有化による内部不正防止や統制にも役立ちます。
NEWJI DX
製造業に特化したデジタルトランスフォーメーション(DX)の実現を目指す請負開発型のコンサルティングサービスです。AI、iPaaS、および先端の技術を駆使して、製造プロセスの効率化、業務効率化、チームワーク強化、コスト削減、品質向上を実現します。このサービスは、製造業の課題を深く理解し、それに対する最適なデジタルソリューションを提供することで、企業が持続的な成長とイノベーションを達成できるようサポートします。
オンライン講座
製造業、主に購買・調達部門にお勤めの方々に向けた情報を配信しております。
新任の方やベテランの方、管理職を対象とした幅広いコンテンツをご用意しております。
お問い合わせ
コストダウンが利益に直結する術だと理解していても、なかなか前に進めることができない状況。そんな時は、newjiのコストダウン自動化機能で大きく利益貢献しよう!
(Β版非公開)