- お役立ち記事
- Industrial application of foam mechanism and effective defoaming technology
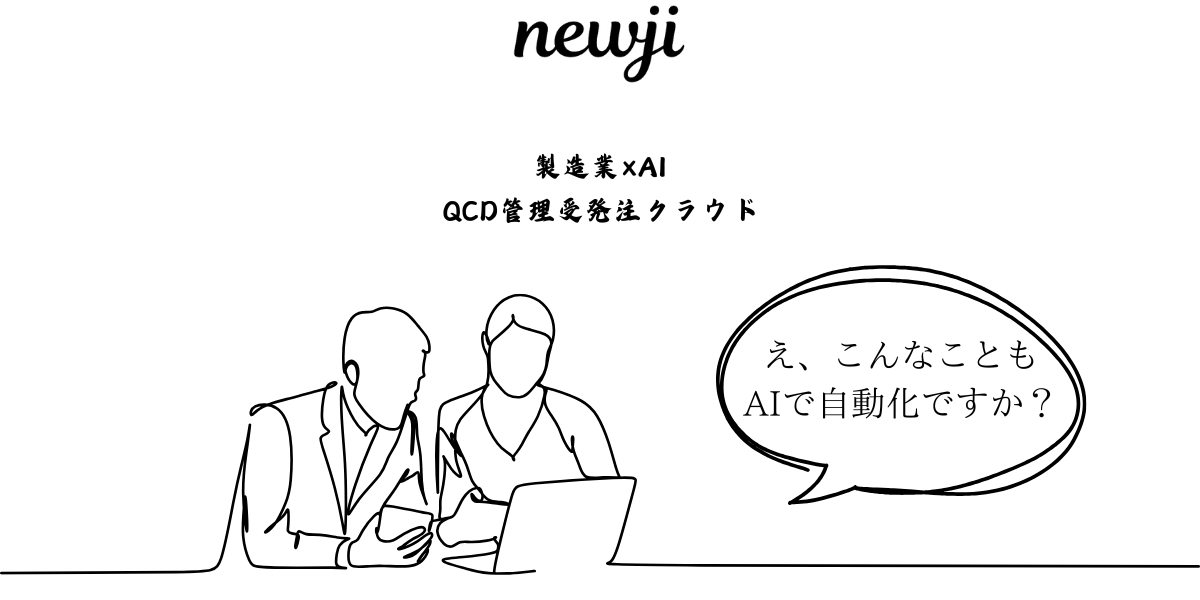
Industrial application of foam mechanism and effective defoaming technology
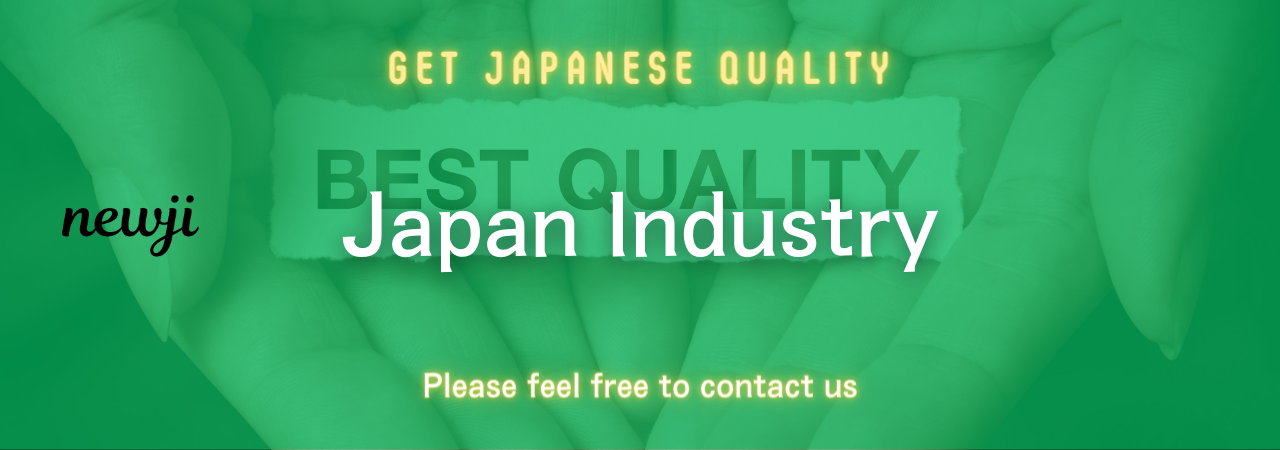
目次
Understanding Foam Mechanisms in Industrial Applications
Foam formation is a common phenomenon in various industrial processes.
Foam, essentially, is a mass of bubbles formed when gas is dispersed in a liquid.
Though it might seem trivial, controlling foam is crucial as it affects the efficiency, quality, and safety of industrial operations.
Industries such as food processing, oil and gas, and wastewater treatment frequently encounter foam.
For instance, in the food processing industry, improper foam control can lead to product defects and losses.
Meanwhile, in wastewater treatment, excessive foam can interfere with water purification processes.
Understanding the mechanisms that lead to foam formation is fundamental for industries to manage and mitigate foaming issues.
Several factors contribute to the generation of foam, including surfactants, which stabilize the surface of the bubbles, and the mechanical agitation that introduces air into the mixture.
Surfactants, or surface-active agents, are compounds that lower the surface tension between two substances.
In industrial situations, they can either be naturally present in the raw materials or added during processing.
The presence of surfactants facilitates the formation of a film around gas bubbles, thus stabilizing the foam and prolonging its life-span.
Mechanical processes such as mixing, pumping, or aeration introduce air into liquids.
When surfactants are present, they quickly surround the introduced air, trapping it and forming stable bubbles.
The size and persistence of these bubbles depend on the nature and concentration of the surfactants, as well as the physical conditions of the process.
Challenges of Foam in Industrial Processes
While foam might be desirable in certain processes or products, such as in beverages or cosmetics, excessive foam is often problematic.
Undesirable foam can lead to overflow, contamination, and interference in the function of equipment, potentially causing operation shutdowns and resulting in financial losses.
In chemical manufacturing, foam can disrupt the accurate measurement and control of reactions, leading to inefficiencies or safety hazards.
Similarly, in the petroleum industry, foam can obstruct the separation of oil and gas, thus complicating downstream processing.
Wastewater treatment plants face severe operational issues due to foam.
Excess foam can cover the surface of the treatment ponds or tanks, making it difficult to monitor and control the processes beneath.
This can lead to decreased treatment efficiency and higher operational costs.
Foam also poses environmental concerns.
In cases where foam spills over from containment areas, it can carry pollutants into the environment, impacting ecosystems and potentially violating environmental regulations.
Effective Defoaming Technologies
To tackle foam issues, industries employ various defoaming technologies and strategies.
Defoamers or antifoams are chemical agents specifically formulated to reduce or eliminate unwanted foam.
They work by rapidly spreading over the foam’s surface, collapsing the bubbles and preventing new ones from forming.
Defoamers are classified based on their composition and application.
Oil-based defoamers contain oils that help disperse the foam faster, making them suitable for use in many industrial processes.
Water-based defoamers are often used where compatibility with specific ingredients is necessary.
Silicone-based defoamers provide excellent stability and efficiency, especially in high-temperature applications.
In addition to chemical defoaming agents, physical methods are also employed.
For example, mechanical foam breakers use rotating blades to physically disrupt foam, making them ideal for use in large tanks or vessels.
Ultrasonic defoaming involves the use of high-frequency sound waves to break up foam, providing a chemical-free option for sensitive processes.
Controlling process parameters can also significantly reduce foam formation.
Careful monitoring and adjustment of temperature, agitation speed, and the concentration of surfactants can minimize foam-related issues without the need for defoamers.
Choosing the Right Defoaming Strategy
Selecting the most appropriate defoaming strategy depends on several factors, including the type of process, the nature of the foam, and the specific requirements of the industry.
Understanding the composition of the foam is critical.
Analyzing the types and concentrations of surfactants present can help in choosing a compatible defoamer that effectively targets the issue without adversely affecting the process.
Considering the environmental impact and compliance with regulations is also essential.
Many industries are moving towards more sustainable and environmentally friendly defoaming solutions.
Economic factors, such as the cost of defoaming agents and their impact on overall production costs, also play a significant role in decision-making.
An effective defoaming strategy should strike a balance between cost efficiency and operational effectiveness.
The Future of Foam Control in Industry
Ongoing research and technological advancements continue to improve foam control strategies in industries.
Innovations in the development of new defoaming agents and techniques provide more reliable, efficient, and environmentally friendly solutions.
Industries increasingly emphasize reducing the formation of foam at its source rather than solely relying on defoaming agents.
This is achieved through improved formulations, optimized process parameters, and real-time monitoring systems.
Collaboration between different sectors can lead to the sharing of best practices and cross-industry insights, fostering innovation in foam control solutions.
Ultimately, effective foam management will continue to play a crucial role in optimizing industrial processes, ensuring product quality, and protecting both the environment and industrial investments.
資料ダウンロード
QCD調達購買管理クラウド「newji」は、調達購買部門で必要なQCD管理全てを備えた、現場特化型兼クラウド型の今世紀最高の購買管理システムとなります。
ユーザー登録
調達購買業務の効率化だけでなく、システムを導入することで、コスト削減や製品・資材のステータス可視化のほか、属人化していた購買情報の共有化による内部不正防止や統制にも役立ちます。
NEWJI DX
製造業に特化したデジタルトランスフォーメーション(DX)の実現を目指す請負開発型のコンサルティングサービスです。AI、iPaaS、および先端の技術を駆使して、製造プロセスの効率化、業務効率化、チームワーク強化、コスト削減、品質向上を実現します。このサービスは、製造業の課題を深く理解し、それに対する最適なデジタルソリューションを提供することで、企業が持続的な成長とイノベーションを達成できるようサポートします。
オンライン講座
製造業、主に購買・調達部門にお勤めの方々に向けた情報を配信しております。
新任の方やベテランの方、管理職を対象とした幅広いコンテンツをご用意しております。
お問い合わせ
コストダウンが利益に直結する術だと理解していても、なかなか前に進めることができない状況。そんな時は、newjiのコストダウン自動化機能で大きく利益貢献しよう!
(Β版非公開)