- お役立ち記事
- Fundamentals of screw fasteners, technology to prevent fatigue damage and loosening, and improvements in fastening reliability and their key points
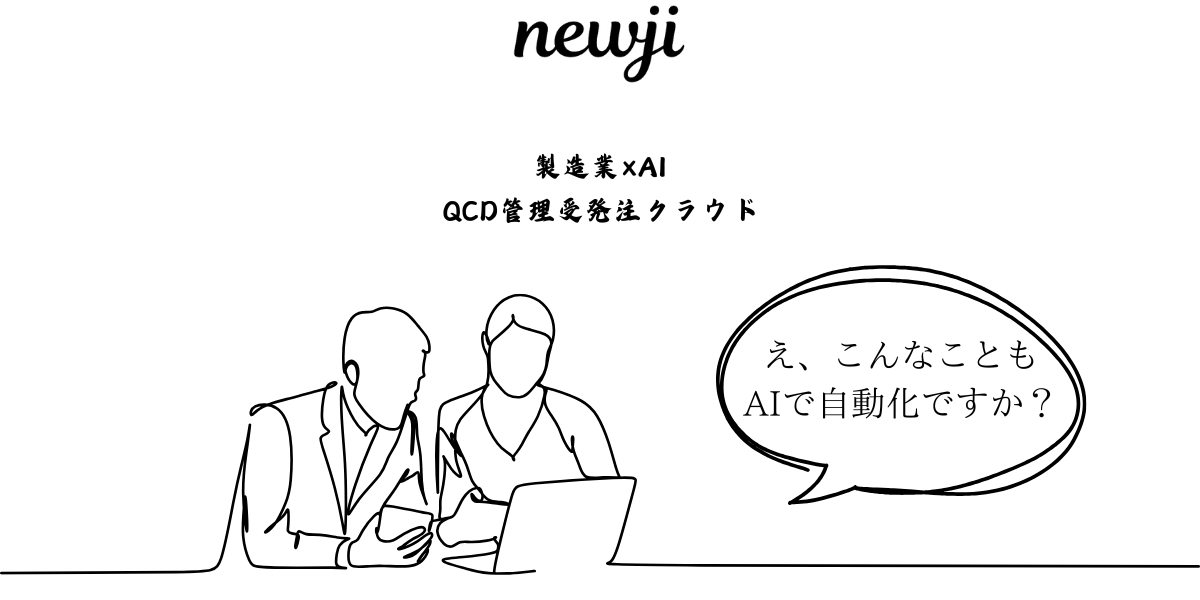
Fundamentals of screw fasteners, technology to prevent fatigue damage and loosening, and improvements in fastening reliability and their key points
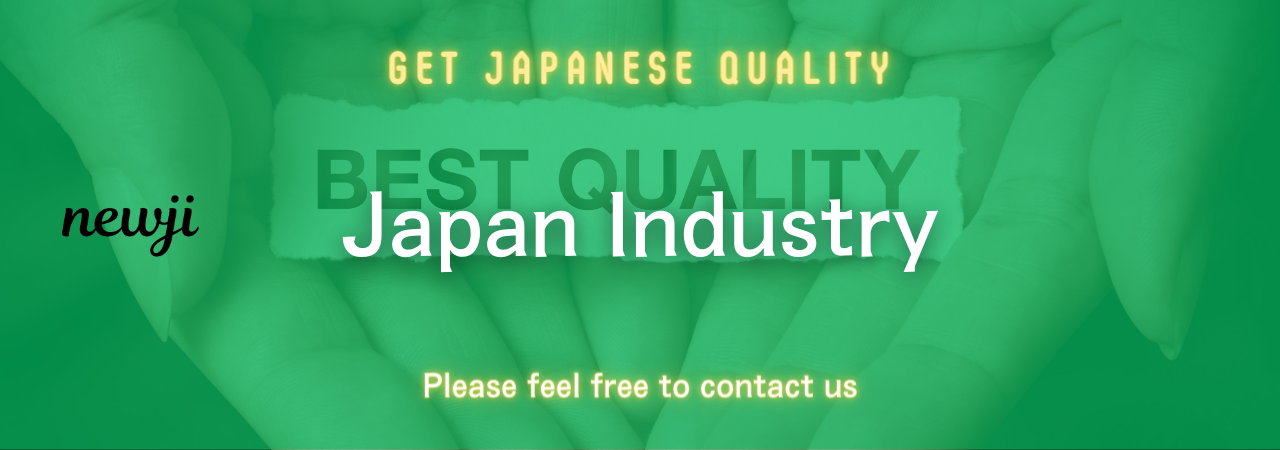
目次
Understanding Screw Fasteners
Screw fasteners play a crucial role in many industries, serving as a primary tool for joining materials securely.
They come in various forms, including bolts, screws, studs, and nuts, each designed for specific applications.
The basic function of a screw fastener is to hold two or more objects together, and its effectiveness depends on its design, the materials used, and the method of installation.
Screws provide a mechanical advantage, enabling the transmission of a force over a distance to create tight, non-permanent joints.
This unique capability makes them indispensable in construction, automotive, aerospace, and electronics industries, among others.
Different types of screw fasteners have unique properties and functions, making it essential to choose the right type for specific applications.
Techniques to Prevent Fatigue Damage
Fatigue damage is a critical concern when it comes to maintaining the structural integrity of screw fasteners.
It occurs when fasteners are subjected to repeated loading and unloading, leading to small cracks that can grow over time.
Preventing fatigue damage requires attention to detail during the design, material selection, and installation processes.
Firstly, selecting the right material is crucial.
Fasteners made from high-strength materials such as alloy steels are more resistant to fatigue failure.
Heat treatment processes like annealing can also improve a fastener’s fatigue performance by relieving internal stresses that can contribute to crack initiation.
Secondly, optimizing the design of the screw fastener can significantly reduce the likelihood of fatigue damage.
Design improvements, such as reducing stress concentrations by using smooth transitions and proper fillet radii, can minimize the risk of crack growth.
Moreover, ensuring that the fastener is not over-tightened during installation can prevent unnecessary stress on the material.
Lastly, regular maintenance checks are essential to detect early signs of fatigue damage.
Visual inspections and non-destructive testing methods like ultrasound can help identify cracks before they propagate and lead to catastrophic failures.
Preventing Loosening of Fasteners
Loosening is another significant issue that affects the performance of screw fasteners.
Fasteners can loosen due to vibrations, changes in temperature, and insufficient initial tightening.
Preventing loosening is essential to maintain the integrity of the joint and ensure safety.
One effective method to prevent loosening is the use of locking mechanisms.
Locking nuts, washers, and adhesive threads can provide additional resistance to rotation, keeping the fastener in place despite vibrations or movement.
Thread-locking adhesives, applied to the threads of the fastener, can also serve as a deterrent against loosening.
Another preventive measure is to apply proper torque during installation.
Using a calibrated torque wrench ensures that the fastener is tightened to the manufacturer’s specified torque level, which helps maintain optimal clamping force.
This prevents both under and over-tightening, reducing the chances of loosening over time.
The design of the joint can also contribute to preventing loosening.
For instance, designing joints that minimize dynamic loading and ensuring even stress distribution across the fastener can reduce the risk of loosening.
Improving Fastening Reliability
Ensuring the reliability of screw fasteners is critical in maintaining the safety and functionality of mechanical systems.
Reliability can be achieved by focusing on several key factors, including design optimization, material selection, and proper installation techniques.
Design optimization involves creating a system where fasteners can perform optimally under expected loads.
This includes considering factors such as joint geometry, load distribution, and the overall configuration of the system.
Simulations and testing can help identify potential weaknesses in the design and offer insights for improvements.
Material selection is equally important.
Choosing materials with the appropriate mechanical properties, corrosion resistance, and thermal stability is essential for ensuring long-term reliability of the fasteners.
In harsh environments, fasteners made from corrosion-resistant alloys or treated with protective coatings can prevent degradation over time.
Proper installation practices are fundamental to achieving fastening reliability.
This includes using the right tools, adhering to torque specifications, and following manufacturer guidelines for installation.
Training employees involved in the fastening process can also improve consistency and accuracy during installation.
Key Points to Remember
To effectively utilize screw fasteners and enhance their performance, it is important to keep several key points in mind:
– **Select the Right Fastener:** Consider the application’s requirements and choose a fastener that meets the necessary mechanical and environmental conditions.
– **Prevent Fatigue Damage:** Use high-strength materials, optimize design features, and perform regular maintenance checks to reduce the risk of fatigue failure.
– **Prevent Loosening:** Employ locking mechanisms, ensure proper torque during installation, and design joints to withstand dynamic loads.
– **Improve Reliability:** Optimize design, select suitable materials, and adhere to proper installation practices to ensure the reliability and longevity of fasteners.
By understanding these fundamental principles and applying them to the design, selection, and installation of screw fasteners, industries can enhance the performance and safety of their mechanical systems.
Stay informed about new technologies and methods in fastening to continually improve the effectiveness of your fastening solutions.
資料ダウンロード
QCD調達購買管理クラウド「newji」は、調達購買部門で必要なQCD管理全てを備えた、現場特化型兼クラウド型の今世紀最高の購買管理システムとなります。
ユーザー登録
調達購買業務の効率化だけでなく、システムを導入することで、コスト削減や製品・資材のステータス可視化のほか、属人化していた購買情報の共有化による内部不正防止や統制にも役立ちます。
NEWJI DX
製造業に特化したデジタルトランスフォーメーション(DX)の実現を目指す請負開発型のコンサルティングサービスです。AI、iPaaS、および先端の技術を駆使して、製造プロセスの効率化、業務効率化、チームワーク強化、コスト削減、品質向上を実現します。このサービスは、製造業の課題を深く理解し、それに対する最適なデジタルソリューションを提供することで、企業が持続的な成長とイノベーションを達成できるようサポートします。
オンライン講座
製造業、主に購買・調達部門にお勤めの方々に向けた情報を配信しております。
新任の方やベテランの方、管理職を対象とした幅広いコンテンツをご用意しております。
お問い合わせ
コストダウンが利益に直結する術だと理解していても、なかなか前に進めることができない状況。そんな時は、newjiのコストダウン自動化機能で大きく利益貢献しよう!
(Β版非公開)