- お役立ち記事
- Latest monitoring system for manufacturing industry aiming to improve equipment utilization rate
月間77,185名の
製造業ご担当者様が閲覧しています*
*2025年2月28日現在のGoogle Analyticsのデータより
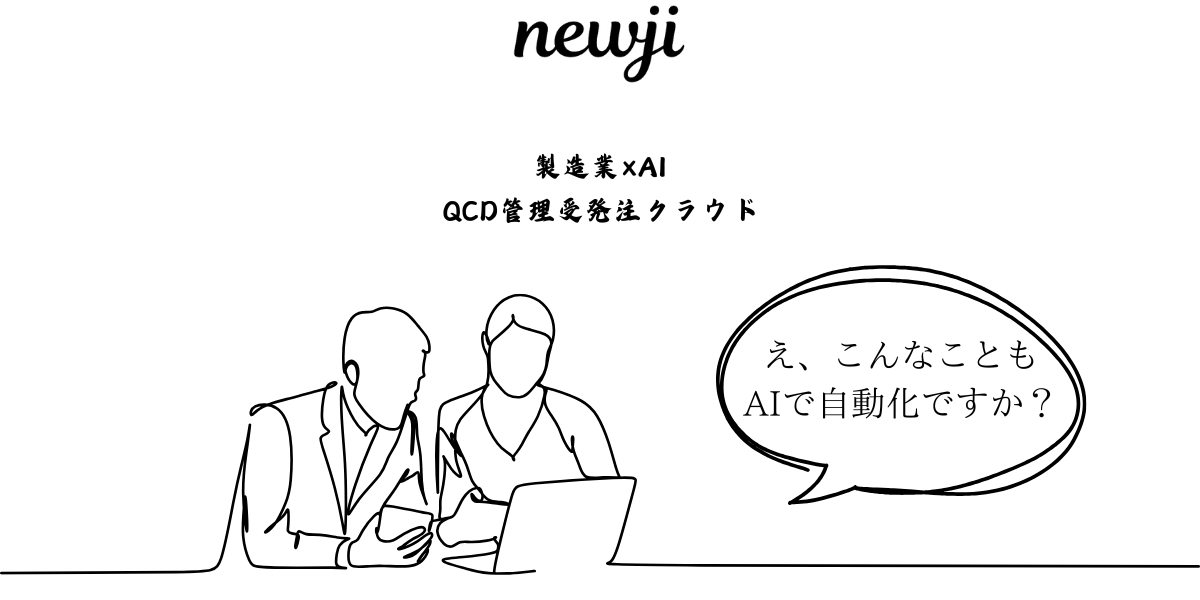
Latest monitoring system for manufacturing industry aiming to improve equipment utilization rate
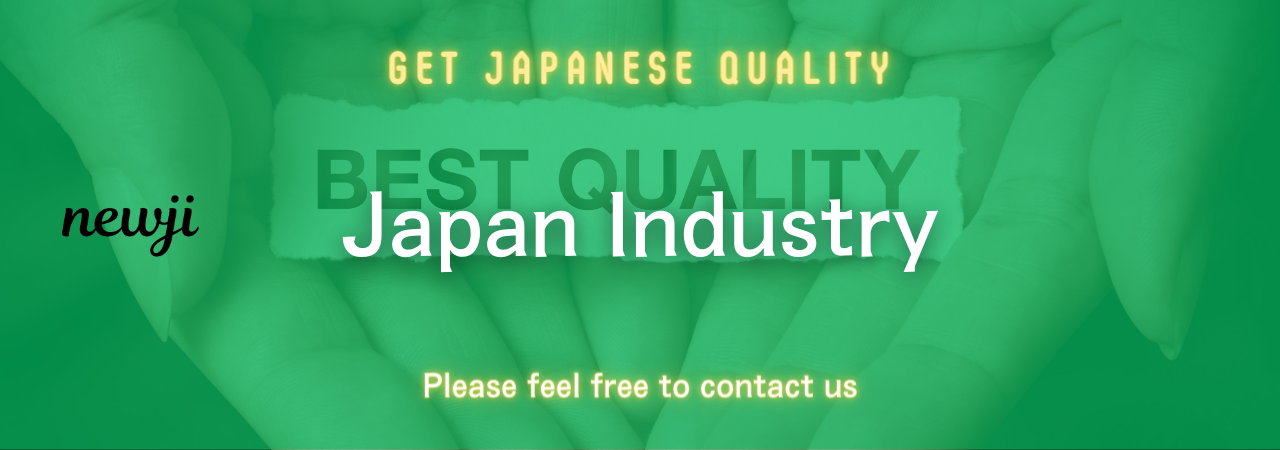
目次
Introduction to Monitoring Systems in Manufacturing
The manufacturing industry is constantly seeking ways to improve efficiency and productivity.
One of the key focuses is enhancing equipment utilization rates.
Advancements in technology have paved the way for sophisticated monitoring systems that aid in achieving this goal.
In today’s rapidly evolving industrial landscape, implementing a modern monitoring system is not just beneficial; it’s essential.
Monitoring systems in manufacturing are designed to ensure that machinery and equipment run at their optimal capacity.
These systems collect and analyze data in real-time, providing insights that help manufacturers reduce downtime, prevent equipment failures, and streamline operations.
This article delves into the latest developments in monitoring systems aimed at improving equipment utilization rates.
Why Equipment Utilization is Important
Equipment utilization refers to the extent to which manufacturing machinery is used compared to its full potential.
High equipment utilization means machines are being used efficiently, whereas low utilization indicates underuse or inefficiencies.
Improving equipment utilization directly impacts a company’s bottom line by reducing costs, increasing output, and optimizing resource allocation.
It also reduces the environmental impact by minimizing energy consumption and waste.
Challenges in Equipment Utilization
Several challenges can impede optimal equipment utilization in manufacturing.
These include:
– Unscheduled Downtime: Unexpected machine failures or maintenance issues can lead to production halts.
– Suboptimal Scheduling: Inefficient scheduling of jobs leads to gaps in production and underutilization of machinery.
– Lack of Real-Time Data: Without real-time data, identifying problems quickly and efficiently becomes challenging.
– Inadequate Maintenance: Reactive rather than preventive maintenance practices result in frequent breakdowns.
The Role of Monitoring Systems
Monitoring systems serve as a critical tool in overcoming these challenges.
They employ advanced sensors and IoT (Internet of Things) technologies to track machine performance continuously.
Here’s how these systems enhance equipment utilization:
Predictive Maintenance
Modern monitoring systems are equipped with predictive analytics capabilities, allowing manufacturers to implement predictive maintenance.
This approach involves using historical data and real-time machine parameters to predict potential failures before they occur.
By scheduling maintenance proactively, companies can prevent unplanned downtime and extend the life of their equipment.
Real-Time Data Analytics
Monitoring systems provide real-time data about machine performance, efficiency, and utilization.
Operators can access dashboards and reports that highlight key performance indicators, alerting them to any deviations.
This instant feedback loop allows for quick, data-driven decisions to rectify issues and optimize processes.
Enhanced Automation and Integration
The latest monitoring systems integrate seamlessly with existing automation technologies in the manufacturing floor.
This integration facilitates smooth communication between different machines and systems, leading to coordinated operations and improved overall equipment efficiency.
Customizable Alerts and Reporting
Manufacturers can customize alerts and reports based on specific operational requirements or thresholds.
These alerts can notify personnel about potential issues via text, email, or through on-screen notifications.
Customizable reporting helps in making informed decisions and tailoring strategies to improve utilization further.
Implementing a Monitoring System
Deciding to implement a monitoring system involves careful consideration and planning.
Here are some essential steps to get started:
Assess Current Systems
Begin by assessing existing equipment and monitoring infrastructure.
Identify machines that are most critical to your operations and determine where improvements can be made.
Recognize the limitations of current systems and set clear objectives for the new monitoring solution.
Select the Appropriate Technology
Choose a monitoring system that aligns with your organizational needs and technical requirements.
Consider factors such as scalability, ease of integration, and compatibility with existing technology.
It’s important to evaluate vendors and select one that offers robust support and advanced technological features.
Train Personnel
Ensure operators and maintenance staff are trained to use the new monitoring system effectively.
Their understanding of how to interpret data and take corrective actions is crucial to maximizing the benefits of the technology.
Training also facilitates a smoother transition and encourages buy-in from employees.
Monitor and Evaluate Performance
After implementation, continuously monitor the performance of the system and its impact on equipment utilization.
Use the data collected to make informed decisions and continuously refine processes.
Periodically evaluate the performance to ensure it meets the desired objectives and adjusts strategies as necessary.
Conclusion
The latest monitoring systems represent a significant advancement in the manufacturing sector’s quest for efficiency and productivity.
By providing predictive maintenance capabilities, real-time analytics, and customizable solutions, these systems greatly enhance equipment utilization rates.
Investing in such technologies is a smart move not only for improving operational efficiency but also for achieving long-term sustainability and competitiveness in the industry.
Embracing these innovations allows manufacturers to stay ahead of the curve, ensuring equipment is running at its maximum potential and contributing positively to the company’s growth and success.
資料ダウンロード
QCD管理受発注クラウド「newji」は、受発注部門で必要なQCD管理全てを備えた、現場特化型兼クラウド型の今世紀最高の受発注管理システムとなります。
ユーザー登録
受発注業務の効率化だけでなく、システムを導入することで、コスト削減や製品・資材のステータス可視化のほか、属人化していた受発注情報の共有化による内部不正防止や統制にも役立ちます。
NEWJI DX
製造業に特化したデジタルトランスフォーメーション(DX)の実現を目指す請負開発型のコンサルティングサービスです。AI、iPaaS、および先端の技術を駆使して、製造プロセスの効率化、業務効率化、チームワーク強化、コスト削減、品質向上を実現します。このサービスは、製造業の課題を深く理解し、それに対する最適なデジタルソリューションを提供することで、企業が持続的な成長とイノベーションを達成できるようサポートします。
製造業ニュース解説
製造業、主に購買・調達部門にお勤めの方々に向けた情報を配信しております。
新任の方やベテランの方、管理職を対象とした幅広いコンテンツをご用意しております。
お問い合わせ
コストダウンが利益に直結する術だと理解していても、なかなか前に進めることができない状況。そんな時は、newjiのコストダウン自動化機能で大きく利益貢献しよう!
(β版非公開)