- お役立ち記事
- Fundamentals of digital twin technology and its application to prediction and control in industrial processes
月間77,185名の
製造業ご担当者様が閲覧しています*
*2025年2月28日現在のGoogle Analyticsのデータより
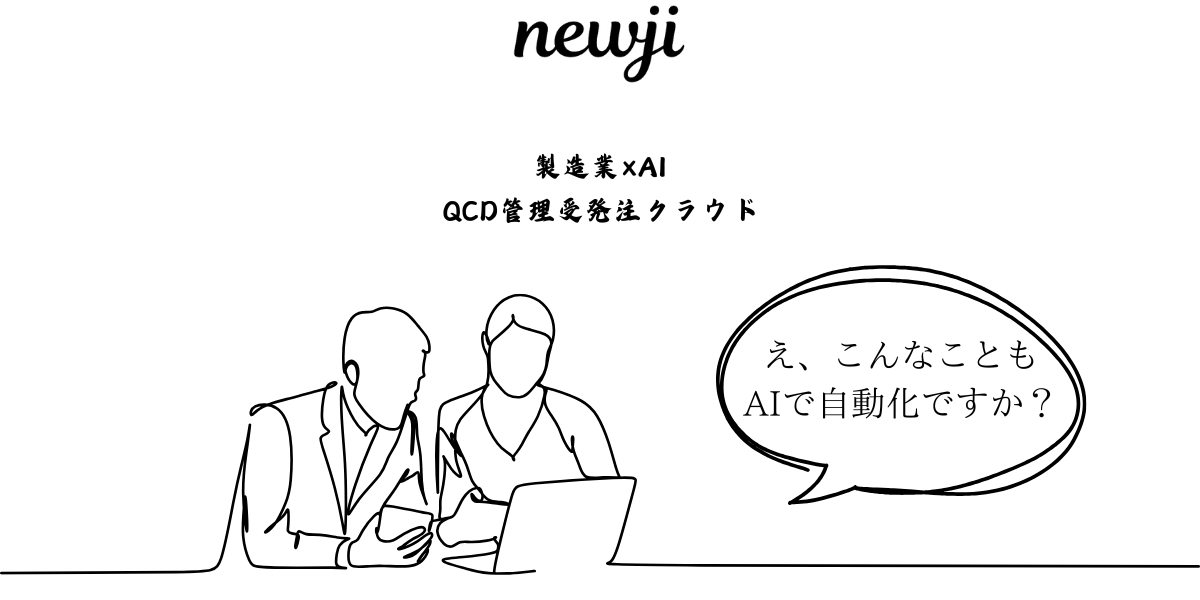
Fundamentals of digital twin technology and its application to prediction and control in industrial processes
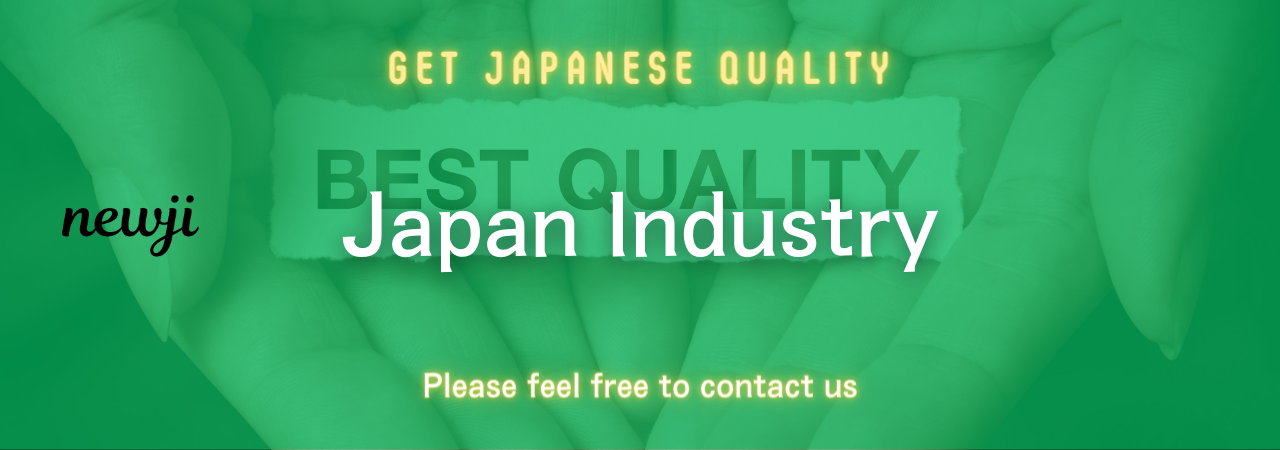
目次
What is Digital Twin Technology?
Digital twin technology represents a paradigm shift in how industries manage, predict, and optimize industrial processes.
It involves creating a virtual model of a physical process, product, or service, allowing engineers and stakeholders to simulate and analyze real-world scenarios in a digital environment.
These digital replicas are interconnected with sensors and data sources to mirror their physical counterparts in real-time.
The concept of digital twin technology is rooted in the idea of bridging the physical and digital worlds.
By leveraging this technology, businesses can gain valuable insights, streamline operations, and foresee potential issues before they occur.
How Digital Twins Work
Digital twins function by continuously collecting data from physical assets through IoT devices and sophisticated sensors.
This data is fed into a digital model to replicate the current state of the asset.
Advanced analytics and machine learning algorithms process this information to provide comprehensive insights into performance, condition, and future behavior.
Moreover, digital twins use feedback loops to ensure that the virtual model remains in sync with the physical counterpart.
This synchronization allows organizations to enhance predictive maintenance strategies, avoiding unnecessary downtime and prolonging equipment lifespan.
Key Components of Digital Twin Technology
1. **Physical Product**: The tangible asset or process that the digital twin represents.
2. **Virtual Model**: The software-based representation equipped with data-driven simulations.
3. **Connection**: Real-time links enabled by sensors and IoT to synchronize the twin and its physical counterpart.
4. **Data**: Continuous streams of information processed to evaluate current performance and predict future outcomes.
Applications in Industrial Processes
Digital twin technology offers numerous applications across a broad range of industrial processes.
One of the most significant benefits lies in its predictive capabilities, which can radically transform the management and optimization of operations.
Enhancing Predictive Maintenance
Preventing equipment failure is crucial in maintaining efficient industrial operations.
By using digital twins, organizations can identify wear and tear in machinery before breakdowns occur.
The continuous monitoring of equipment health facilitates timely interventions, reducing operational costs and minimizing unexpected downtime.
Optimization of Manufacturing Processes
In manufacturing, digital twins can simulate production processes to identify inefficiencies and suggest optimizations.
By analyzing data from every stage of the production line, manufacturers can streamline workflows, reduce waste, and elevate product quality.
This results in improved margins and a more sustainable operation.
Design and Testing of New Products
Developing new products often requires extensive testing and modifications.
Digital twins enable engineers to conduct virtual trials, significantly reducing the resources needed for physical prototypes.
Through detailed simulations, companies can accurately predict how a new product will perform under different conditions, ensuring a more successful design process.
Improving Supply Chain Management
Supply chain logistics benefit greatly from the predictive capabilities of digital twins.
By simulating supply chain scenarios, businesses can foresee potential disruptions and optimize inventory levels.
This intelligent approach allows for precise demand forecasting, ensuring that supply chain operations are resilient and responsive.
Benefits of Digital Twin Technology
Adopting digital twin technology provides a wide array of benefits, particularly for industries dealing with complex operations and large volumes of data.
Real-time Monitoring and Analysis
The real-time analysis provided by digital twins helps organizations keep a pulse on their operations.
This visibility allows them to make informed decisions quickly, responding to changes and challenges as they arise.
Enhanced Collaboration
With a digital twin, teams from different departments can collaborate more effectively.
The shared model ensures everyone has access to the same information, reducing misunderstandings and promoting more comprehensive solutions to problems.
Cost Efficiency
Through predictive analytics and optimized processes, companies can achieve significant cost savings.
By preventing failures and enhancing operational efficiency, digital twins help organizations reduce waste and improve their bottom line.
Innovation and Experimentation
Digital twins create a safe environment for innovation, allowing businesses to test new ideas without the risk of costly failures.
This experimentation fosters creativity and can lead to groundbreaking improvements across the industry.
Challenges in Implementing Digital Twin Technology
Despite its promising potential, implementing digital twin technology is not without challenges.
Companies must overcome several hurdles to fully realize its benefits.
Data Integration
For a digital twin to be effective, it requires seamless integration of data from various sources.
Organizations may encounter difficulties in consolidating disparate data systems and ensuring data accuracy.
High Initial Investment
Establishing a comprehensive digital twin system involves significant upfront costs.
The expense of installing advanced sensors, developing sophisticated software models, and hiring skilled personnel can be daunting for some companies.
Security Concerns
With the increased connectivity digital twins require, there is a heightened risk of cyber threats.
Protecting sensitive data and ensuring the security of IoT devices is paramount to prevent unauthorized access and potential breaches.
Skills Gap
The successful deployment of digital twin technology demands a workforce skilled in data analytics, software development, and IoT management.
Bridging this skills gap is essential for companies looking to implement and maintain digital twin systems effectively.
The Future of Digital Twin Technology
As digital twin technology evolves, it promises to redefine industrial processes and pave the way for new innovations.
Advancements in artificial intelligence, machine learning, and data analytics will further enhance the precision and functionality of digital twins.
Industries across the globe are poised to leverage these advancements, creating smarter and more efficient processes.
Embracing digital twin technology will be crucial for companies seeking to maintain a competitive edge in the rapidly changing industrial landscape.
資料ダウンロード
QCD管理受発注クラウド「newji」は、受発注部門で必要なQCD管理全てを備えた、現場特化型兼クラウド型の今世紀最高の受発注管理システムとなります。
ユーザー登録
受発注業務の効率化だけでなく、システムを導入することで、コスト削減や製品・資材のステータス可視化のほか、属人化していた受発注情報の共有化による内部不正防止や統制にも役立ちます。
NEWJI DX
製造業に特化したデジタルトランスフォーメーション(DX)の実現を目指す請負開発型のコンサルティングサービスです。AI、iPaaS、および先端の技術を駆使して、製造プロセスの効率化、業務効率化、チームワーク強化、コスト削減、品質向上を実現します。このサービスは、製造業の課題を深く理解し、それに対する最適なデジタルソリューションを提供することで、企業が持続的な成長とイノベーションを達成できるようサポートします。
製造業ニュース解説
製造業、主に購買・調達部門にお勤めの方々に向けた情報を配信しております。
新任の方やベテランの方、管理職を対象とした幅広いコンテンツをご用意しております。
お問い合わせ
コストダウンが利益に直結する術だと理解していても、なかなか前に進めることができない状況。そんな時は、newjiのコストダウン自動化機能で大きく利益貢献しよう!
(β版非公開)