- お役立ち記事
- Fundamentals of thermal design in electronic equipment, selection of optimal heat dissipation devices, application to heat dissipation design, and practical know-how
Fundamentals of thermal design in electronic equipment, selection of optimal heat dissipation devices, application to heat dissipation design, and practical know-how
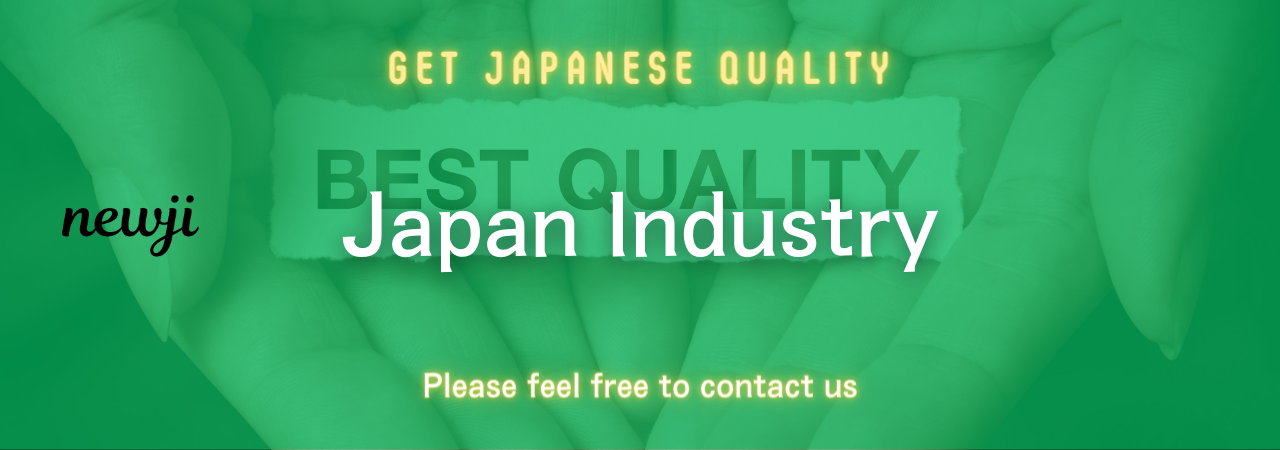
目次
Understanding Thermal Design in Electronic Equipment
Thermal design is an essential aspect of creating efficient electronic devices.
It ensures that electronic components operate within their intended temperature range, preventing overheating that could lead to damage or reduced performance.
A thorough understanding of thermal design involves grasping how heat is generated, transferred, and eventually dissipated in electronic systems.
Heat Generation in Electronic Devices
Electronic components such as chips, resistors, and transistors generate heat during operation.
Heat generation is primarily due to electrical resistance and inefficiencies in energy conversion.
Managing this heat is critical to maintaining device reliability and longevity.
Heat Transfer Mechanisms
There are three main ways heat can be transferred within and from electronic equipment: conduction, convection, and radiation.
**Conduction** occurs when heat moves through solid materials.
In electronics, conduction often happens through the circuit board and adjacent components.
**Convection** involves heat moving away from components via a fluid medium, typically air.
Fans and airflow systems are common convection methods in electronic devices.
**Radiation** is the process of heat dissipating into the surrounding environment in the form of electromagnetic waves.
While less significant than conduction and convection in most electronics, it still plays a role in overall thermal management.
Selecting Optimal Heat Dissipation Devices
To manage heat effectively, designers must select appropriate heat dissipation devices for their systems.
Different Types of Heat Sinks
Heat sinks are a popular choice for passive cooling solutions in electronics.
They work by increasing the surface area in contact with the air, allowing for greater heat dissipation through convection and radiation.
**Natural Convection Heat Sinks** rely on the natural rise of heated air.
They are usually simple in design and suitable for low to moderate heat generation environments.
**Forced Convection Heat Sinks** integrate fans to enhance air movement over their surfaces, improving cooling efficiency.
These are ideal for systems with higher power outputs.
Fans and Blowers
Fans and blowers are active cooling devices that force air over hot components, facilitating convection.
They are used in systems where passive solutions, like heat sinks alone, are insufficient.
Heat Pipes and Vapor Chambers
Heat pipes and vapor chambers offer efficient ways to transfer heat within electronic devices.
They utilize the phase change of a working fluid to move heat away from hot spots quickly.
**Heat Pipes** provide a simple, cost-effective method for heat transfer with minimal temperature difference.
**Vapor Chambers** are more sophisticated, offering uniform temperature distribution over larger areas.
Thermal Interface Materials (TIMs)
TIMs are crucial for enhancing thermal contact between surfaces, such as between a chip and a heat sink.
They fill microscopic gaps to improve heat transfer efficiency.
Applying Heat Dissipation Techniques to Design
Implementing effective heat dissipation techniques during the design phase can significantly enhance the reliability of electronic equipment.
Design Considerations
Designing for thermal efficiency requires a holistic approach, considering all aspects of the device’s operation and environment.
Layout optimization is crucial, ensuring heat-generating components are positioned to maximize heat dissipation.
This includes placing them near airflow paths or areas that can accommodate larger heat sinks.
**Material Selection** can influence thermal performance.
Materials with high thermal conductivity, such as aluminum and copper, are preferred for heat sinks and thermal spreading layers.
Simulation and Testing
Thermal simulation tools allow designers to model heat flow and identify potential thermal issues before physical prototypes are built.
By using simulations, potential hotspots can be identified and mitigated early in the design process.
After simulation, **Prototyping and Testing** should be performed to validate thermal design under real-world conditions.
Thermal imaging and sensor data can offer insights into temperature distribution and verify the effectiveness of cooling solutions.
Practical Know-How for Effective Thermal Management
Successfully managing thermal performance involves both theoretical knowledge and practical know-how.
Here are some essential tips from experienced engineers.
Stay Informed on New Technologies
As technology evolves, new materials and methods for thermal management are developed.
Staying updated on these advances ensures that designers can implement cutting-edge solutions.
Consider Environmental Conditions
Designing for the environment where the device will operate is necessary.
Extreme temperatures, humidity, and altitude can all impact thermal management strategies.
Customized cooling solutions might be required for devices intended for unique settings.
Energy Efficiency and Power Management
Incorporate energy-efficient components and power management techniques to minimize heat generation.
Lower power consumption not only reduces thermal difficulties but also enhances the overall energy efficiency of the device.
Collaborate with Multidisciplinary Teams
Thermal design benefits from input across disciplines such as electrical, mechanical, and materials engineering.
Collaborative efforts ensure a balanced approach that considers all aspects of the system’s performance and constraints.
In conclusion, understanding and applying the fundamentals of thermal design is imperative in developing reliable electronic equipment.
By selecting the right heat dissipation devices and effectively applying design techniques, engineers can ensure the optimal performance and longevity of their devices.
Continuously learning and adapting to new technologies and methodologies will further enhance the ability to manage thermal challenges efficiently.
資料ダウンロード
QCD調達購買管理クラウド「newji」は、調達購買部門で必要なQCD管理全てを備えた、現場特化型兼クラウド型の今世紀最高の購買管理システムとなります。
ユーザー登録
調達購買業務の効率化だけでなく、システムを導入することで、コスト削減や製品・資材のステータス可視化のほか、属人化していた購買情報の共有化による内部不正防止や統制にも役立ちます。
NEWJI DX
製造業に特化したデジタルトランスフォーメーション(DX)の実現を目指す請負開発型のコンサルティングサービスです。AI、iPaaS、および先端の技術を駆使して、製造プロセスの効率化、業務効率化、チームワーク強化、コスト削減、品質向上を実現します。このサービスは、製造業の課題を深く理解し、それに対する最適なデジタルソリューションを提供することで、企業が持続的な成長とイノベーションを達成できるようサポートします。
オンライン講座
製造業、主に購買・調達部門にお勤めの方々に向けた情報を配信しております。
新任の方やベテランの方、管理職を対象とした幅広いコンテンツをご用意しております。
お問い合わせ
コストダウンが利益に直結する術だと理解していても、なかなか前に進めることができない状況。そんな時は、newjiのコストダウン自動化機能で大きく利益貢献しよう!
(Β版非公開)