- お役立ち記事
- Distortion, residual stress, crack generation mechanism and countermeasures by heat treatment simulation
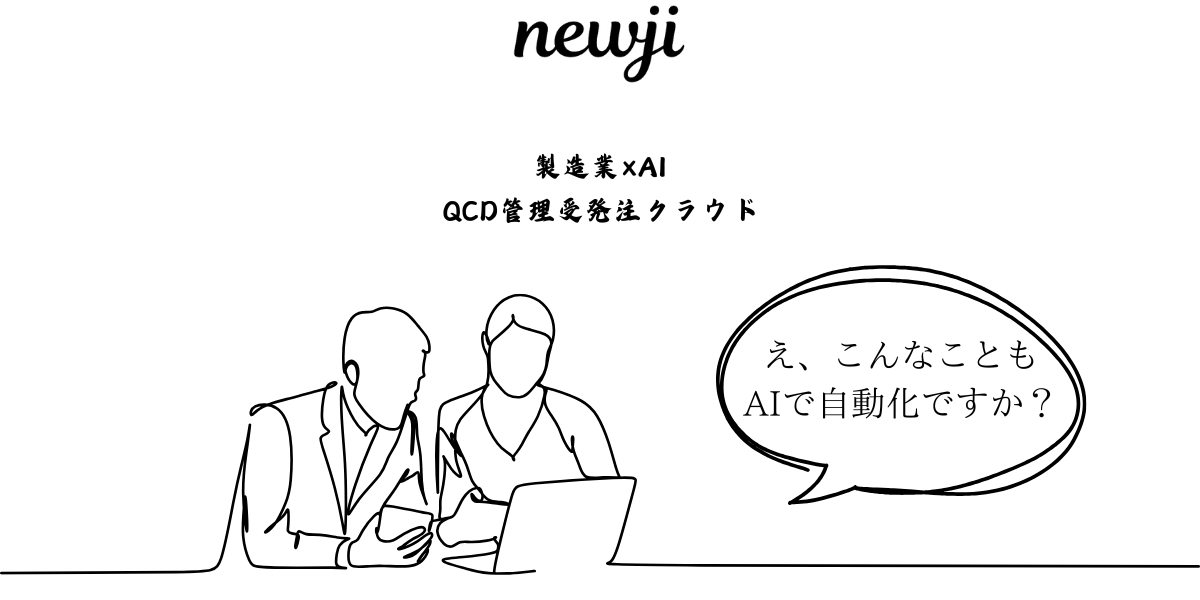
Distortion, residual stress, crack generation mechanism and countermeasures by heat treatment simulation
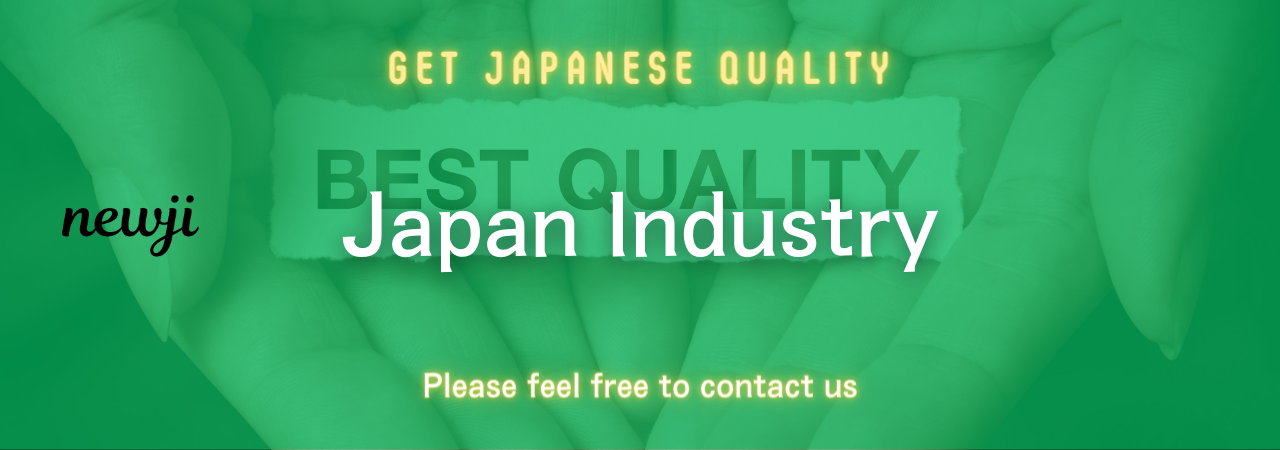
目次
Introduction to Heat Treatment Simulation
Heat treatment is a vital process in material science and engineering, which involves heating and cooling materials to alter their physical and mechanical properties without changing their shapes.
The main objective of this process is to improve material performance, including strength, toughness, ductility, and resistance to wear and corrosion.
However, during heat treatment, issues such as distortion, residual stress, and crack generation can occur, leading to compromised material integrity.
Simulation techniques are key to understanding and mitigating these challenges.
Heat treatment simulation uses computational models to predict the outcome of heat treatment processes, allowing engineers to optimize procedures and prevent potential problems.
This article will explore the mechanisms behind distortion, residual stress, and crack formation during heat treatment and unravel how simulation can serve as an essential tool in counteracting these issues.
Understanding Distortion in Heat Treatment
Distortion in heat-treated materials results from uneven temperature distribution within the material, leading to inconsistent expansion and contraction.
As different parts of a material may experience varying temperatures, they will expand or contract at different rates, causing deformation.
This can lead to components deviating from their intended shapes, negatively affecting their fit and functionality in their subsequent applications.
Distortion can lead not only to increased production costs but also to a compromised quality of final products.
Understanding the causes and controlling distortion is essential for manufacturers striving for precision and reliability.
Predicting Distortion Through Simulation
Heat treatment simulation models allow engineers to anticipate how different materials respond to thermal cycles.
These models consider material properties, component geometry, and heating techniques to predict potential distortions.
By utilizing finite element analysis (FEA) and other simulation tools, engineers can estimate the amount and direction of distortion that might occur.
Identifying these factors enables manufacturers to adjust the heat treatment process parameters, such as temperature gradients and cooling rates, to minimize distortion.
Residual Stress in Heat-Treated Materials
Residual stress refers to the stress retained within a material after the original cause of the stress has been removed.
Heat treatment can introduce residual stresses due to differential contractions and expansions during the heating and cooling phases.
While some level of residual stress is inevitable, excessive levels can lead to unwanted deformations, cracking, or even premature failure of the component.
Residual stress can manifest as tensile or compressive stress.
Tensile stress, in particular, is more concerning as it can reduce the overall strength of the material and make it more susceptible to cracking.
Addressing Residual Stress with Simulation
Simulation technology can model the distribution of residual stresses, helping engineers to understand where and why these stresses develop.
By simulating the heat treatment process, it is possible to identify critical stress points and modify process parameters accordingly.
Adjustments may include altering heating and cooling rates or redesigning the component geometry to reduce stress concentration areas.
Simulation can also help assess the overall stress profile of the material, ensuring that stress levels remain within acceptable limits for its intended application.
Mechanism of Crack Generation
Crack formation during heat treatment is a critical concern, as it can lead to catastrophic failure of components.
Cracks are primarily caused by thermal stresses resulting from uneven heating and cooling.
When the stresses exceed the tensile strength of the material, cracks may initiate and propagate.
Chemical changes, such as phase transformations and material inhomogeneities, can also increase the likelihood of crack formation by altering stress distributions and making certain areas more susceptible to fracture.
Mitigating Cracks with Simulation Techniques
Heat treatment simulation provides insights into the thermal and structural dynamics occurring within the material.
By utilizing simulation, engineers can predict the probability and location of crack initiation.
This information allows manufacturers to design heat treatment schedules that minimize rapid temperature changes and avoid stress build-up.
Further, simulation can aid in evaluating microstructural changes and ensuring uniform material properties, thus reducing the likelihood of crack development.
Practical Countermeasures Using Simulation
Implementing practical countermeasures during heat treatment can significantly reduce the likelihood of distortion, residual stress, and crack formation.
Heat treatment simulation offers a proactive approach to designing these countermeasures.
One effective measure is to use controlled heating and cooling rates.
By employing simulation, one can determine the optimal rates that minimize thermal gradients, thereby reducing the incidence of distortion.
Simulation also allows for the customization of heat treatment cycles for specific materials, accommodating their unique behavioral characteristics and preventing the formation of residual stress.
Furthermore, simulation enhances the understanding of phase transformations and microstructural changes, enabling precise control over material properties and minimizing the risk of crack formation.
Conclusion
Heat treatment simulation plays a crucial role in predicting and mitigating challenges arising from distortion, residual stress, and crack generation.
By applying advanced computational models, engineers can gain valuable insights into how materials respond to thermal cycles and adjust procedures to optimize outcomes.
As the demand for high-performance materials continues to grow, the ability to simulate and control heat treatment processes becomes increasingly important.
Implementing simulation-driven strategies ensures that materials meet stringent quality standards, aiding manufacturers in producing reliable and durable components.
The evolution of heat treatment simulation tools represents a significant advancement in materials engineering, driving both efficiency and innovation in the industry.
資料ダウンロード
QCD調達購買管理クラウド「newji」は、調達購買部門で必要なQCD管理全てを備えた、現場特化型兼クラウド型の今世紀最高の購買管理システムとなります。
ユーザー登録
調達購買業務の効率化だけでなく、システムを導入することで、コスト削減や製品・資材のステータス可視化のほか、属人化していた購買情報の共有化による内部不正防止や統制にも役立ちます。
NEWJI DX
製造業に特化したデジタルトランスフォーメーション(DX)の実現を目指す請負開発型のコンサルティングサービスです。AI、iPaaS、および先端の技術を駆使して、製造プロセスの効率化、業務効率化、チームワーク強化、コスト削減、品質向上を実現します。このサービスは、製造業の課題を深く理解し、それに対する最適なデジタルソリューションを提供することで、企業が持続的な成長とイノベーションを達成できるようサポートします。
オンライン講座
製造業、主に購買・調達部門にお勤めの方々に向けた情報を配信しております。
新任の方やベテランの方、管理職を対象とした幅広いコンテンツをご用意しております。
お問い合わせ
コストダウンが利益に直結する術だと理解していても、なかなか前に進めることができない状況。そんな時は、newjiのコストダウン自動化機能で大きく利益貢献しよう!
(Β版非公開)