- お役立ち記事
- Example of introducing a production line optimization algorithm useful for factory operations
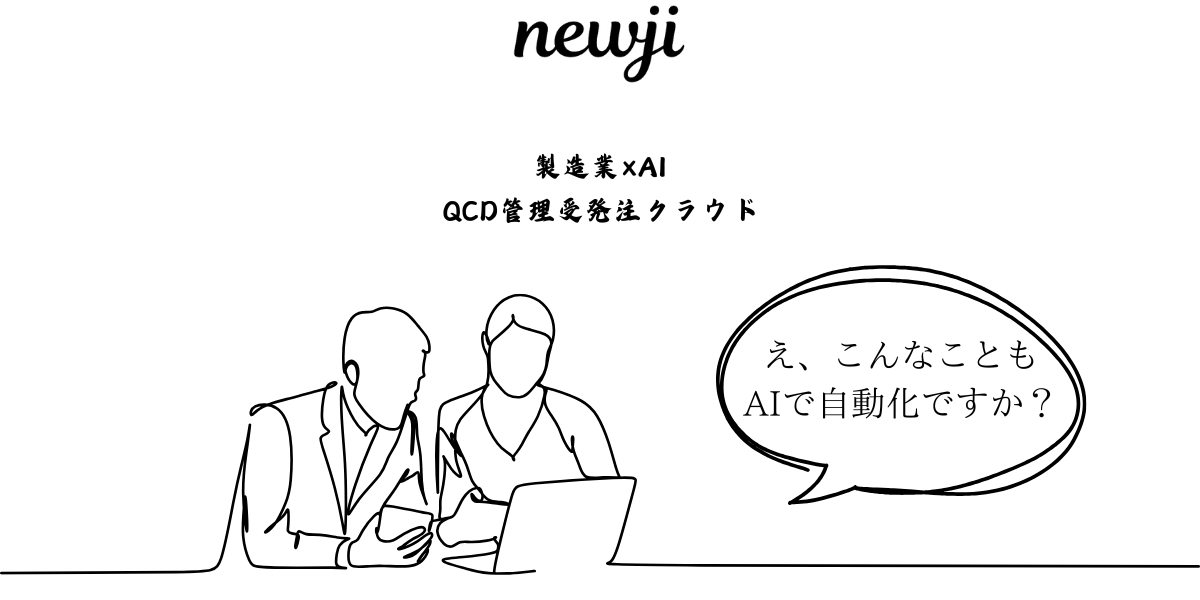
Example of introducing a production line optimization algorithm useful for factory operations
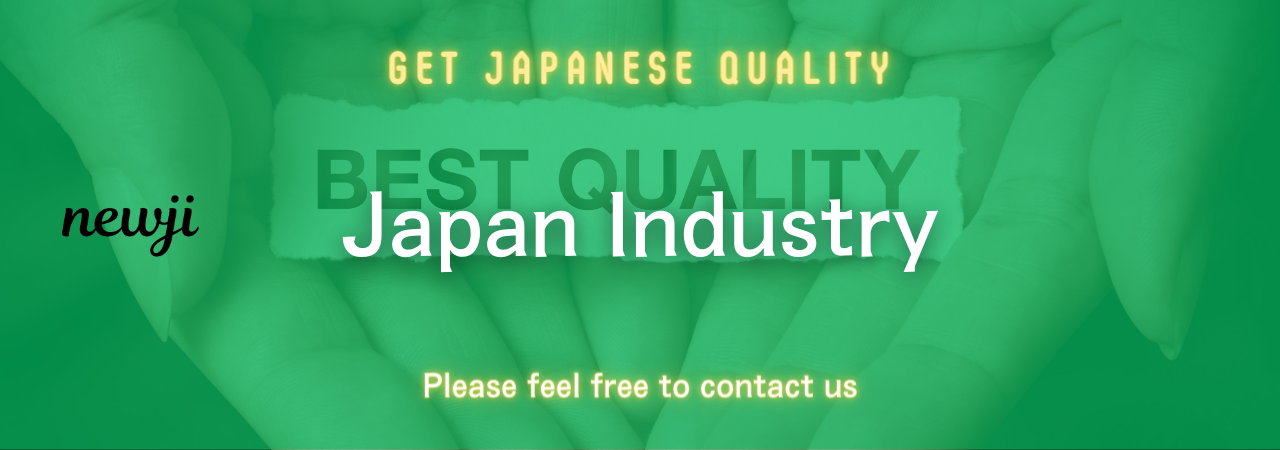
目次
Understanding Production Line Optimization
Production line optimization is a process that involves improving the efficiency and productivity of manufacturing operations.
It is crucial for factories to ensure that their production lines run smoothly, with minimal downtime and waste.
By doing so, factories can increase their output, reduce costs, and improve product quality.
Optimization algorithms play a vital role in achieving these goals by analyzing data and providing actionable insights.
The Importance of Production Line Optimization
In today’s competitive market, factories need to operate at peak efficiency to stay ahead.
Production line optimization can have a significant impact on a business’s bottom line.
When production processes are streamlined, resources are used more effectively, leading to cost savings.
Moreover, optimizing production lines helps in reducing downtime caused by equipment failure or inefficient scheduling.
Improved productivity is another significant benefit of production line optimization.
When a factory’s operations are optimized, it can produce more goods in a shorter period.
This capability is critical in meeting customer demand and competing in the market.
Another advantage is the enhancement of product quality.
Optimized production lines ensure that manufacturing processes are consistent, reducing the likelihood of defects.
High-quality products result in customer satisfaction and can lead to increased sales.
Introducing an Algorithm for Optimization
One of the most popular algorithms used in production line optimization is the Genetic Algorithm (GA).
This algorithm mimics the process of natural selection to create highly efficient solutions.
It begins by identifying the key variables that impact the production process and then iteratively tests different combinations to find the most efficient setup.
GAs are particularly effective because they can handle complex problems with many variables.
This capability makes them ideal for optimizing production lines where multiple factors, such as machine settings, labor schedules, and material flow, must be considered.
How the Algorithm Works
The Genetic Algorithm starts with an initial population of possible solutions.
These solutions are represented as “chromosomes,” which are essentially strings of data containing different variables.
Each chromosome is evaluated based on a “fitness function,” which measures how well it performs in optimizing production.
The best-performing chromosomes are selected and used to create a new generation of solutions through processes called “crossover” and “mutation.”
Crossover involves combining parts of two chromosomes to create a new solution, while mutation introduces small changes to a chromosome.
These processes ensure diversity among the solutions, allowing the algorithm to explore a wide range of possibilities.
The algorithm continues this cycle of selection, crossover, and mutation until it converges on the most optimal solution or reaches a set number of iterations.
Benefits of Using Genetic Algorithms
Genetic Algorithms offer several advantages in the realm of production line optimization.
Firstly, they are highly adaptable and can be tailored to specific production scenarios.
This flexibility ensures that the algorithm provides relevant solutions for various industries.
Secondly, GAs are capable of discovering solutions that may not be apparent through traditional problem-solving methods.
Their ability to explore multiple possibilities simultaneously often leads to innovative approaches to production line optimization.
Another benefit is the algorithm’s efficiency in finding optimal solutions within a reasonable timeframe.
While some optimization methods can be time-consuming, Genetic Algorithms typically provide faster results, enabling quicker implementation of solutions.
Practical Applications
Real-world examples demonstrate the effectiveness of Genetic Algorithms in optimizing production lines.
For instance, a car manufacturing plant implemented a GA to optimize its assembly line scheduling.
By doing so, the plant reduced its production cycle time and increased output by 15%.
Another example is a food processing company that used a Genetic Algorithm to optimize its packaging line.
The algorithm helped the company minimize packaging waste and improve the consistency of its product presentation, enhancing customer satisfaction.
These practical applications highlight the potential of algorithms like GA to transform production processes across various industries.
Implementing an Optimization Algorithm
To successfully implement a production line optimization algorithm, several steps must be taken.
First, it’s essential to gather comprehensive data on the current production processes.
This data provides the foundation for the algorithm to analyze and identify areas for improvement.
Next, defining the objectives and constraints of the optimization process is crucial.
Clearly understanding what the factory aims to achieve, whether it’s reducing waste, cutting costs, or increasing output, guides the algorithm’s development.
After defining goals, selecting the appropriate algorithm is the next step.
While Genetic Algorithms are popular, other algorithms such as simulated annealing or particle swarm optimization may be more suitable depending on the specific requirements and complexity of the production line.
Once the algorithm is chosen, it must be integrated into the factory’s existing systems.
This integration may involve some level of customization to ensure the algorithm interacts effectively with machinery and data management systems.
Finally, ongoing monitoring and adjustments are necessary.
As production variables change over time, the algorithm may need to be fine-tuned to maintain optimal performance.
Conclusion
Production line optimization is an invaluable strategy for improving factory operations.
By utilizing sophisticated algorithms like the Genetic Algorithm, factories can unlock new levels of efficiency and productivity.
These advancements lead to cost savings, improved product quality, and enhanced competitiveness in the market.
As technology continues to evolve, the use of optimization algorithms will become even more integral to successful manufacturing operations.
Factories that embrace these innovations are likely to remain at the forefront of their industries, delivering high-quality products while maximizing their operational potential.
資料ダウンロード
QCD調達購買管理クラウド「newji」は、調達購買部門で必要なQCD管理全てを備えた、現場特化型兼クラウド型の今世紀最高の購買管理システムとなります。
ユーザー登録
調達購買業務の効率化だけでなく、システムを導入することで、コスト削減や製品・資材のステータス可視化のほか、属人化していた購買情報の共有化による内部不正防止や統制にも役立ちます。
NEWJI DX
製造業に特化したデジタルトランスフォーメーション(DX)の実現を目指す請負開発型のコンサルティングサービスです。AI、iPaaS、および先端の技術を駆使して、製造プロセスの効率化、業務効率化、チームワーク強化、コスト削減、品質向上を実現します。このサービスは、製造業の課題を深く理解し、それに対する最適なデジタルソリューションを提供することで、企業が持続的な成長とイノベーションを達成できるようサポートします。
オンライン講座
製造業、主に購買・調達部門にお勤めの方々に向けた情報を配信しております。
新任の方やベテランの方、管理職を対象とした幅広いコンテンツをご用意しております。
お問い合わせ
コストダウンが利益に直結する術だと理解していても、なかなか前に進めることができない状況。そんな時は、newjiのコストダウン自動化機能で大きく利益貢献しよう!
(Β版非公開)