- お役立ち記事
- Fundamentals of metal additive manufacturing technology and key points for introduction and application
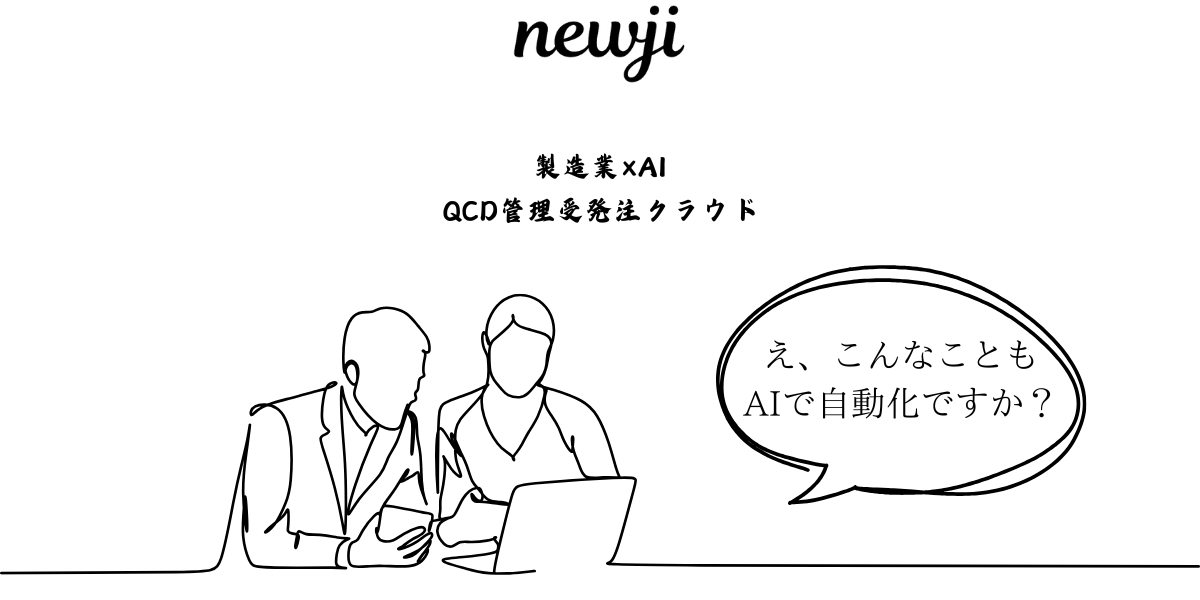
Fundamentals of metal additive manufacturing technology and key points for introduction and application
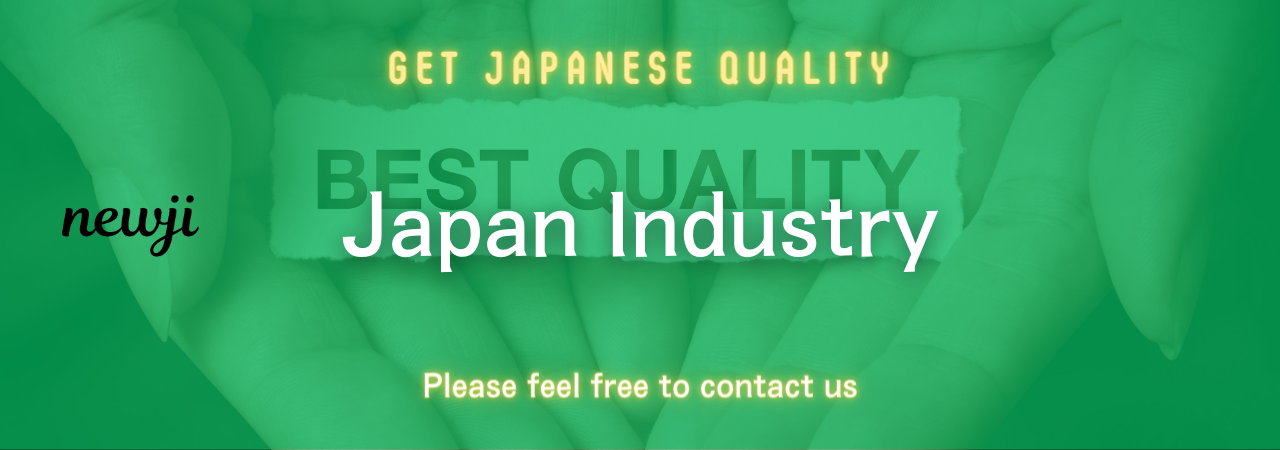
目次
Understanding Metal Additive Manufacturing
Metal additive manufacturing, often referred to as 3D printing for metals, is an innovative technology that enables the creation of complex, lightweight, and strong parts.
Unlike traditional manufacturing processes, which often involve subtracting material from a solid block, additive manufacturing builds objects layer by layer from digital models.
The process begins with a computer-aided design (CAD) file, which is sliced into thin layers.
These layers guide the printer to deposit metal powder or wire, fusing it together using a heat source like a laser or electron beam.
Metal additive manufacturing is transforming industries by offering unmatched design flexibility, rapid prototyping, and efficient production.
Industries such as aerospace, automotive, healthcare, and consumer goods are increasingly adopting this technology to innovate and meet specific needs.
Types of Metal Additive Manufacturing Technologies
There are several metal additive manufacturing technologies, each with its unique process and applications.
Powder Bed Fusion
Powder Bed Fusion (PBF) is one of the most widely used techniques in metal additive manufacturing.
This method involves spreading a fine layer of metal powder on a build platform.
A heat source, typically a laser, selectively fuses the powder based on the digital model.
The platform then lowers, and a new powder layer is spread on top, repeating the process until the part is complete.
Variations of PBF include Selective Laser Melting (SLM) and Direct Metal Laser Sintering (DMLS).
Directed Energy Deposition
Directed Energy Deposition (DED) uses focused thermal energy to fuse materials as they are being deposited.
This method is particularly beneficial for repairing existing parts or adding features to pre-formed components.
DED can use either powder or wire feedstock, and it is often employed in aerospace and military applications.
Binder Jetting
Binder Jetting differs from other methods by using a liquid binding agent to adhere metal powder particles.
Once the part is built, it is removed from the printer, and the unbonded powder is recycled.
The printed part is then subjected to a post-processing step to remove the binder and to sinter the metal, achieving its final strength and density.
Advantages of Metal Additive Manufacturing
Metal additive manufacturing offers numerous advantages over traditional manufacturing techniques.
Design Flexibility
One of the most significant benefits is the ability to create complex geometries that would be impossible or prohibitively expensive to produce using conventional methods.
This allows designers to optimize parts for performance, weight, and material efficiency.
Rapid Prototyping
Additive manufacturing significantly reduces the time required to move from concept to prototype.
This rapid turnaround is invaluable in industries where time-to-market is critical, facilitating quicker innovation and design iteration.
Material Efficiency
Traditional manufacturing processes often result in material waste.
In contrast, metal additive manufacturing uses only the material necessary to build the object, reducing waste and associated costs.
Additionally, these processes often leverage lightweight materials, contributing to fuel efficiency in industries like aerospace.
Challenges and Considerations
While metal additive manufacturing has many benefits, it is not without its challenges.
Surface Finish and Mechanical Properties
The as-printed surface finish of metal additively manufactured parts can be rougher than parts made through conventional means.
Post-processing steps, such as machining, polishing, or heat treatment, may be required to achieve the desired finish and mechanical properties.
Equipment and Material Costs
The initial investment in metal additive manufacturing equipment can be substantial.
Additionally, metal powders and wires used as feedstock are often more expensive than bulk materials used in traditional manufacturing.
However, these costs can be offset by the reduction in material waste and increased design efficiency.
Skill and Knowledge Requirements
Successful implementation of metal additive manufacturing requires skilled personnel familiar with the technology, materials, and design software.
Training and upskilling existing staff are crucial to maximize the potential benefits.
Key Points for Introduction and Application
When considering the introduction of metal additive manufacturing in your business, several key factors should be kept in mind.
Assessing Business Needs
Understand what aspects of your current manufacturing process will benefit most from the flexibility and efficiency of additive manufacturing.
Identify specific applications where complex, lightweight designs or on-demand production could offer competitive advantages.
Invest in the Right Technology
Choose the appropriate additive manufacturing technology that aligns with your production needs.
Consider factors such as material compatibility, build size, precision, and production speed when selecting equipment.
Integration with Existing Processes
Plan how metal additive manufacturing will integrate with your current production workflow.
Identify any necessary changes in supply chain management, quality control, and post-processing operations.
Partnerships and Collaborations
Consider collaborating with technology providers, research institutions, or other businesses that have experience in metal additive manufacturing.
These partnerships can provide access to expertise, resources, and new markets.
Conclusion
Metal additive manufacturing stands at the forefront of a manufacturing revolution, offering unprecedented possibilities for innovation and efficiency.
By understanding the fundamentals, applications, and challenges, businesses can strategically adopt this technology to meet ever-evolving market demands.
With proper planning and investment, metal additive manufacturing can unlock new opportunities and drive competitive advantage.
資料ダウンロード
QCD調達購買管理クラウド「newji」は、調達購買部門で必要なQCD管理全てを備えた、現場特化型兼クラウド型の今世紀最高の購買管理システムとなります。
ユーザー登録
調達購買業務の効率化だけでなく、システムを導入することで、コスト削減や製品・資材のステータス可視化のほか、属人化していた購買情報の共有化による内部不正防止や統制にも役立ちます。
NEWJI DX
製造業に特化したデジタルトランスフォーメーション(DX)の実現を目指す請負開発型のコンサルティングサービスです。AI、iPaaS、および先端の技術を駆使して、製造プロセスの効率化、業務効率化、チームワーク強化、コスト削減、品質向上を実現します。このサービスは、製造業の課題を深く理解し、それに対する最適なデジタルソリューションを提供することで、企業が持続的な成長とイノベーションを達成できるようサポートします。
オンライン講座
製造業、主に購買・調達部門にお勤めの方々に向けた情報を配信しております。
新任の方やベテランの方、管理職を対象とした幅広いコンテンツをご用意しております。
お問い合わせ
コストダウンが利益に直結する術だと理解していても、なかなか前に進めることができない状況。そんな時は、newjiのコストダウン自動化機能で大きく利益貢献しよう!
(Β版非公開)