- お役立ち記事
- Product life and market failure rate estimation using “reliability data analysis method” to prevent market failures and its key points
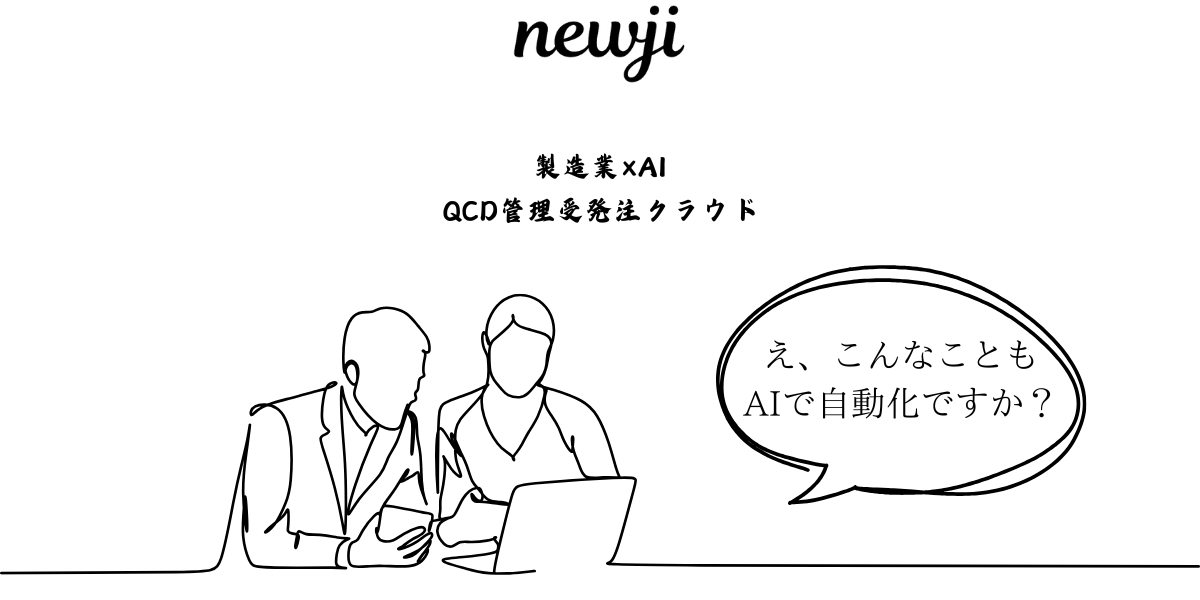
Product life and market failure rate estimation using “reliability data analysis method” to prevent market failures and its key points
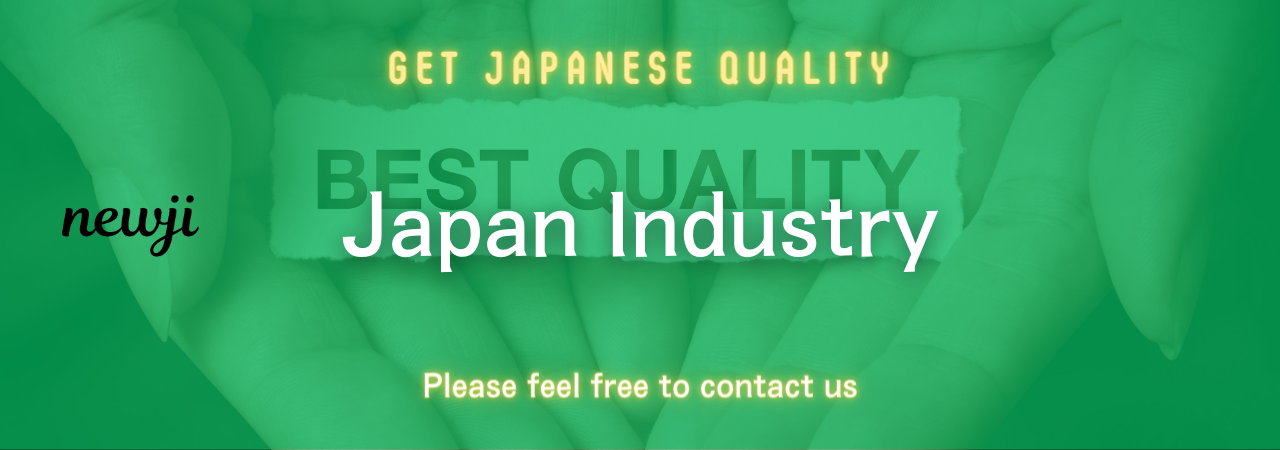
目次
Understanding Reliability Data Analysis
Reliability data analysis is a method used to estimate product life and to predict the market failure rate of a product.
This analysis relies on data and statistical tools to gauge how long a product will last before it fails.
It is crucial for manufacturers and businesses aiming to improve product quality, reduce warranty costs, and prevent market failures.
By understanding and implementing this method, companies can significantly enhance their product development processes and customer satisfaction.
Why Is Reliability Data Analysis Important?
Reliability data analysis plays a pivotal role in the manufacturing and retail industries.
It enables businesses to evaluate a product’s reliability over time, which in turn helps them to anticipate when a product might fail.
By using this data, companies can plan better for the production, improve their products, design better warranties, and ultimately provide better customer support.
Moreover, understanding when and why products fail allows businesses to implement strategies that reduce these failure rates.
This proactive approach to potential market failures contributes directly to a company’s positive reputation and long-term success.
Key Concepts in Reliability Data Analysis
To effectively utilize reliability data analysis, it’s important to understand a few key concepts.
These concepts form the foundation upon which reliability predictions and analyses are made.
1. Failure Rate
The failure rate is a measure of the frequency with which an engineered system or component fails.
Understanding this rate helps businesses know how often they can expect a product to require repair or replacement over a certain period.
2. Mean Time Between Failures (MTBF)
MTBF is the predicted elapsed time between inherent failures of a system during operation.
This calculation is crucial for estimating the time a product can be used reliably.
The higher the MTBF, the better the product’s reliability.
3. Mean Time To Failure (MTTF)
Similar to MTBF, MTTF is the average time until a product fails.
The difference is that MTTF is typically used for products that are not repairable after they fail.
Knowing the MTTF can inform decisions about product replacements and life-cycle planning.
4. Survival Analysis
Survival analysis refers to a set of statistical approaches used to determine the time it takes for an event of interest to occur, such as product failure.
This analysis provides insights into product longevity and expected lifespan.
Steps to Conduct Reliability Data Analysis
There are several steps involved in performing a reliability data analysis, which help in systematically deriving meaningful insights from data.
Data Collection
Data collection is the first step.
Gather data on product performance and failure rates.
This data can be in the form of field data, reliability tests, or accelerated life tests.
Data Preparation
Prepare the data for analysis.
This involves cleaning the data to remove any inconsistencies or anomalies, which could skew the analysis results.
Data Analysis
Use statistical tools and models to analyze the data.
Common methods include life data analysis and accelerated life testing, which allow you to estimate product life and failure rates accurately.
Model Selection
Select the appropriate predictive models that align with your data and analysis objectives.
These models help in understanding product reliability over time and under various conditions.
Result Interpretation
Interpret the results of the analysis to make informed decisions regarding product improvements, maintenance activities, and warranty policies.
Benefits of Reliability Data Analysis
Implementing reliability data analysis offers various benefits to both companies and consumers.
Enhanced Product Quality
With a clear understanding of failure rates and product life, companies can focus on improving the parts of their products most prone to failure, enhancing overall product quality.
Cost Reduction
By predicting failures, companies can plan maintenance and production schedules more effectively, reducing the costs associated with unscheduled repairs and downtime.
Customer Satisfaction
Reliable products that meet expectations lead to satisfied customers, more positive reviews, and higher rates of customer retention.
Informed Decision-Making
With accurate failure predictions, businesses can make informed decisions about product updates, recalls, or discontinuations based on solid data.
Challenges in Reliability Data Analysis
While beneficial, reliability data analysis also poses challenges that companies must address.
Data Collection Difficulties
Gathering reliable and sufficient data can be challenging.
It requires significant time and resources to ensure data accuracy and relevance.
Complexity of Analysis
The analysis involves complex statistical methods and models, which require specialized knowledge and expertise to correctly interpret and use.
Changing Variables
Product usage conditions and environments often change, making it difficult to generalize reliability predictions across all scenarios.
Conclusion
In conclusion, reliability data analysis is an indispensable tool for industries aiming to produce high-quality and durable products.
By understanding the underlying principles and implementing systematic analysis techniques, businesses can anticipate and mitigate product failures, reduce costs, and ultimately achieve greater customer satisfaction.
Investing in quality data collection and skilled analysts is essential to leverage the full potential of reliability data analysis for business growth and market success.
資料ダウンロード
QCD調達購買管理クラウド「newji」は、調達購買部門で必要なQCD管理全てを備えた、現場特化型兼クラウド型の今世紀最高の購買管理システムとなります。
ユーザー登録
調達購買業務の効率化だけでなく、システムを導入することで、コスト削減や製品・資材のステータス可視化のほか、属人化していた購買情報の共有化による内部不正防止や統制にも役立ちます。
NEWJI DX
製造業に特化したデジタルトランスフォーメーション(DX)の実現を目指す請負開発型のコンサルティングサービスです。AI、iPaaS、および先端の技術を駆使して、製造プロセスの効率化、業務効率化、チームワーク強化、コスト削減、品質向上を実現します。このサービスは、製造業の課題を深く理解し、それに対する最適なデジタルソリューションを提供することで、企業が持続的な成長とイノベーションを達成できるようサポートします。
オンライン講座
製造業、主に購買・調達部門にお勤めの方々に向けた情報を配信しております。
新任の方やベテランの方、管理職を対象とした幅広いコンテンツをご用意しております。
お問い合わせ
コストダウンが利益に直結する術だと理解していても、なかなか前に進めることができない状況。そんな時は、newjiのコストダウン自動化機能で大きく利益貢献しよう!
(Β版非公開)