- お役立ち記事
- Application of machine fatigue life prediction technology and online abnormality prediction damage monitoring technology using AE sensing
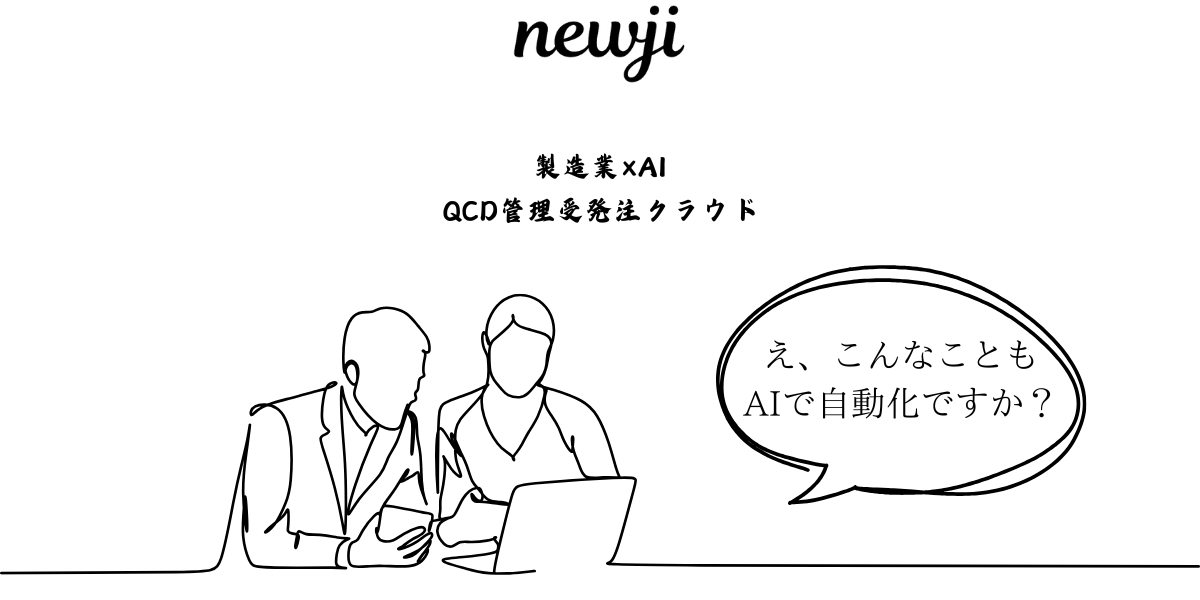
Application of machine fatigue life prediction technology and online abnormality prediction damage monitoring technology using AE sensing
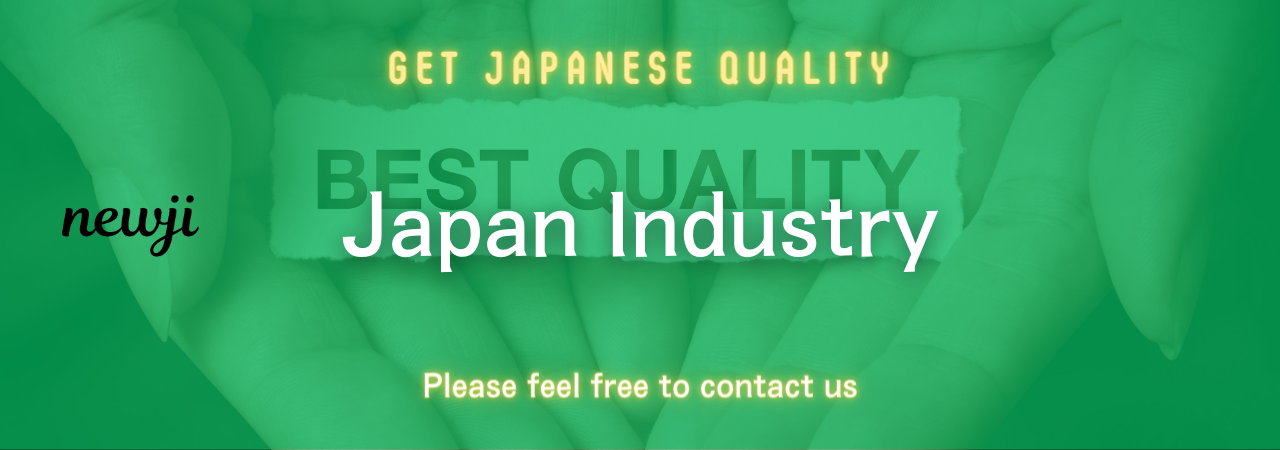
目次
Introduction to Machine Fatigue Life Prediction
Machine fatigue life prediction is a crucial aspect of modern engineering, especially in industries that rely on heavy machinery and complex systems.
Understanding when a machine component is likely to fail allows for proactive maintenance, preventing unexpected breakdowns and costly repairs.
By applying advanced technology, such as machine learning and artificial intelligence, engineers can predict the lifespan of machine parts with a high degree of accuracy.
AE Sensing: The Game Changer
Acoustic Emission (AE) sensing is a powerful technique used to monitor the integrity of structures and machinery.
It involves the detection of high-frequency waves released by a material when it undergoes deformation or stress.
These emissions can provide crucial information about the condition and health of a machine component.
By using AE sensing, engineers can detect early signs of fatigue in materials before visible cracks or damage occur.
This allows for timely interventions, reducing the risk of catastrophic failures.
The technology is especially valuable in industries like aerospace, automotive, and manufacturing, where safety and reliability are of utmost importance.
How Machine Fatigue Life Prediction Works
The process of predicting machine fatigue life involves several steps.
First, data is collected from the machine components using sensors, including AE sensors.
This data includes various parameters such as stress, vibration, and temperature, which are critical in assessing the condition of the machinery.
Next, the collected data is analyzed using sophisticated algorithms and models.
Machine learning techniques, such as neural networks and decision trees, play a significant role in this stage.
They help in identifying patterns and trends that indicate potential failures.
Once the analysis is complete, the system provides insights into the remaining useful life of the machine components.
This information is invaluable for maintenance planning and resource allocation, as it allows for maintenance activities to be scheduled at the most opportune times, minimizing downtime and maximizing productivity.
Online Abnormality Prediction and Damage Monitoring
In addition to predicting the fatigue life of machine parts, AE sensing can also be used for online abnormality prediction and damage monitoring.
This involves continuously monitoring the state of the machinery while it is in operation.
When abnormalities or damages are detected, the system can immediately alert operators, enabling swift action to prevent further damage.
This real-time monitoring capability is highly beneficial in industries where unscheduled downtime can lead to significant financial losses.
The integration of AE sensing with online monitoring systems helps create a comprehensive diagnostic framework.
It not only predicts potential failures but also ensures constant vigilance over the machinery’s health, providing a holistic approach to machine maintenance.
Benefits of Using AE Sensing for Machine Monitoring
There are numerous benefits of using AE sensing technology for machine fatigue life prediction and damage monitoring.
Improved Safety
By detecting damage early and preventing unexpected failures, AE sensing helps maintain a safe working environment.
This is crucial in industries where equipment failures can lead to hazardous situations.
Cost Efficiency
Routine maintenance can be costly and disruptive.
However, with machine fatigue life prediction, maintenance can be performed exactly when needed, optimizing resource use and reducing unnecessary expenses.
Enhanced Equipment Lifespan
By identifying and addressing issues early, AE sensing helps extend the lifespan of machinery.
This maximizes return on investment and reduces the frequency of expensive equipment replacements.
Reduced Downtime
Real-time monitoring facilitates rapid response to issues, minimizing the downtime associated with unexpected breakdowns.
This leads to higher overall productivity and efficiency.
Challenges in Implementing AE Sensing
Despite its advantages, implementing AE sensing technology comes with challenges.
Complex Data Analysis
Interpreting the data from AE sensors requires advanced data analysis skills and sophisticated algorithms.
Engineers need to develop models that accurately predict fatigue life and detect anomalies.
Initial Investment
The cost of installing AE sensing technology can be significant.
However, the long-term savings in maintenance costs and extended equipment life typically justify the initial investment.
Integration with Existing Systems
In some cases, integrating AE sensing with legacy machinery and systems can pose challenges.
Companies must ensure seamless integration to harness the full benefits of the technology.
The Future of Machine Fatigue Life Prediction
As technology continues to evolve, machine fatigue life prediction and AE sensing will likely become even more sophisticated.
The integration of the Internet of Things (IoT) with AE sensing opens up new possibilities for remote monitoring and predictive maintenance.
Furthermore, advancements in machine learning and artificial intelligence will enhance the accuracy and reliability of fatigue life predictions.
These technologies will become invaluable tools for industries looking to optimize their maintenance strategies and ensure equipment safety and longevity.
Conclusion
Machine fatigue life prediction and online abnormality prediction using AE sensing represent a significant advancement in industrial maintenance.
By adopting these technologies, companies can enhance safety, reduce costs, and improve operational efficiency.
While challenges exist, the benefits of implementing AE sensing far outweigh the drawbacks, positioning it as a vital component in the future of machinery maintenance.
資料ダウンロード
QCD調達購買管理クラウド「newji」は、調達購買部門で必要なQCD管理全てを備えた、現場特化型兼クラウド型の今世紀最高の購買管理システムとなります。
ユーザー登録
調達購買業務の効率化だけでなく、システムを導入することで、コスト削減や製品・資材のステータス可視化のほか、属人化していた購買情報の共有化による内部不正防止や統制にも役立ちます。
NEWJI DX
製造業に特化したデジタルトランスフォーメーション(DX)の実現を目指す請負開発型のコンサルティングサービスです。AI、iPaaS、および先端の技術を駆使して、製造プロセスの効率化、業務効率化、チームワーク強化、コスト削減、品質向上を実現します。このサービスは、製造業の課題を深く理解し、それに対する最適なデジタルソリューションを提供することで、企業が持続的な成長とイノベーションを達成できるようサポートします。
オンライン講座
製造業、主に購買・調達部門にお勤めの方々に向けた情報を配信しております。
新任の方やベテランの方、管理職を対象とした幅広いコンテンツをご用意しております。
お問い合わせ
コストダウンが利益に直結する術だと理解していても、なかなか前に進めることができない状況。そんな時は、newjiのコストダウン自動化機能で大きく利益貢献しよう!
(Β版非公開)