- お役立ち記事
- Precision and Innovation: The Art of Unit and Device Assembly in Japanese Manufacturing
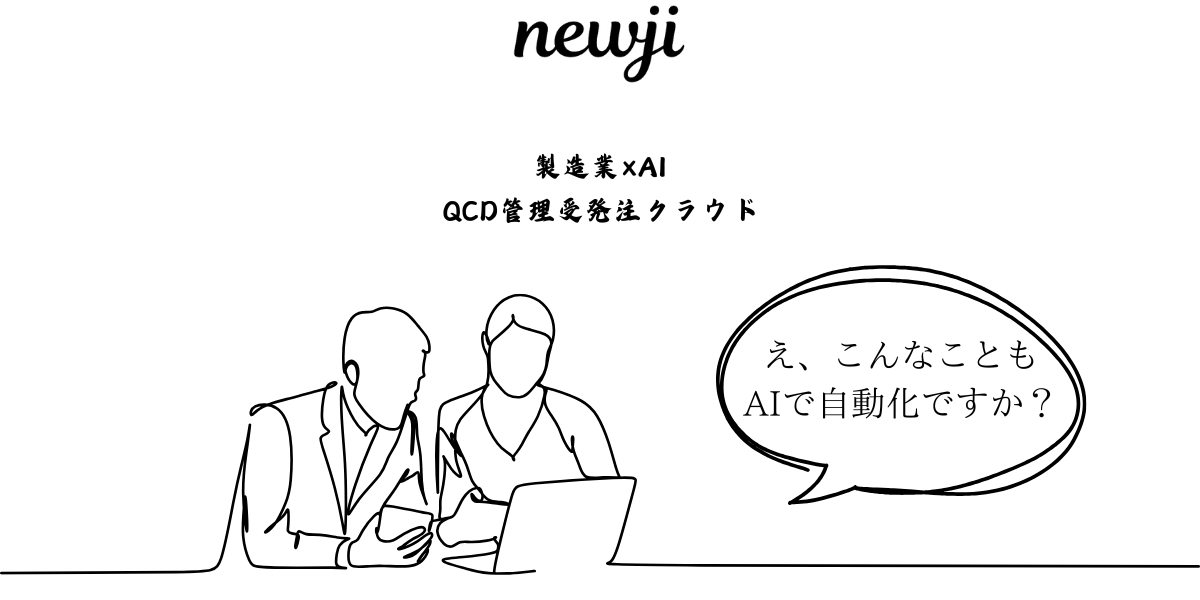
Precision and Innovation: The Art of Unit and Device Assembly in Japanese Manufacturing
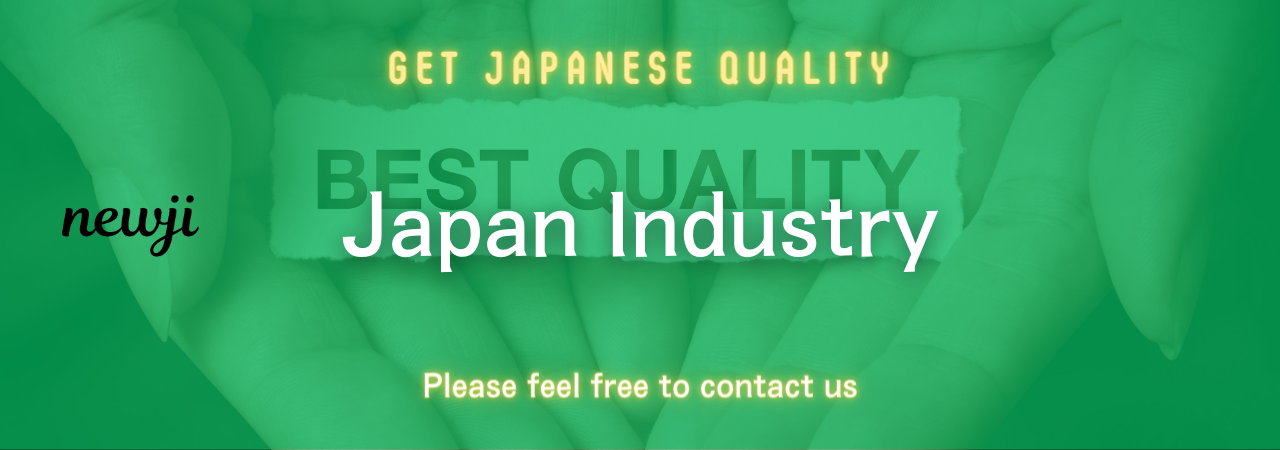
目次
Understanding Japanese Manufacturing Excellence
Japanese manufacturing has long been synonymous with precision, quality, and innovation. This reputation has been built over decades through a combination of cultural values, advanced technologies, and meticulous processes. Understanding the factors that contribute to Japanese manufacturing excellence is essential for procurement and purchasing professionals aiming to leverage the strengths of Japanese suppliers.
Historical Context
The post-World War II era was a pivotal period for Japanese manufacturing. Faced with the challenge of rebuilding the economy, Japanese companies adopted practices that emphasized efficiency and quality. Influential management philosophies, such as Total Quality Management (TQM) and Just-in-Time (JIT) production, were developed during this time. These practices not only boosted productivity but also laid the foundation for Japan’s competitive edge in global markets.
Core Principles: Kaizen, Just-in-Time, and More
Central to Japanese manufacturing are principles like Kaizen, which focuses on continuous improvement. This philosophy encourages employees at all levels to suggest and implement small, incremental changes that enhance processes and reduce waste. Another key principle is Just-in-Time (JIT) production, which aims to reduce inventory costs by synchronizing production schedules with demand. Additionally, Total Quality Control (TQC) ensures that every aspect of production meets stringent quality standards, minimizing defects and increasing customer satisfaction.
Procurement in Japanese Manufacturing
Procurement strategies in Japanese manufacturing are intricately linked to the country’s emphasis on quality and efficiency. Effective procurement ensures that only the best materials and components are sourced, contributing to the overall excellence of the final product.
Selecting the Right Suppliers
Choosing the right suppliers is critical in Japanese manufacturing. Companies often engage in long-term partnerships with suppliers who demonstrate reliability, quality, and a commitment to improvement. The selection process typically involves rigorous evaluations, including site visits, quality audits, and assessments of the supplier’s production capabilities. By meticulously selecting suppliers, Japanese manufacturers ensure that their supply chain is robust and capable of meeting their high standards.
Supplier Relationship Management
Supplier relationship management (SRM) in Japan goes beyond transactional interactions. Japanese companies foster close, collaborative relationships with their suppliers, often involving joint development projects and shared growth objectives. Regular communication, mutual trust, and a focus on mutual benefits are hallmarks of SRM practices in Japanese manufacturing. This collaborative approach leads to better alignment between suppliers and manufacturers, resulting in higher quality products and more efficient processes.
Advantages of Japanese Unit and Device Assembly
Japanese unit and device assembly processes offer numerous advantages that set them apart from competitors. These advantages stem from a combination of advanced techniques, cultural dedication to craftsmanship, and innovative technologies.
High Precision and Quality
Precision is a cornerstone of Japanese manufacturing. Assembly processes are meticulously designed to ensure that every component fits perfectly, reducing the likelihood of errors and defects. This high level of precision not only enhances the functionality and durability of the final product but also contributes to better performance and reliability. Quality control measures are integrated into every stage of the assembly process, ensuring that standards are consistently met.
Innovative Practices
Innovation is deeply ingrained in Japanese manufacturing. Companies continuously invest in research and development to improve assembly techniques and incorporate cutting-edge technologies. Automation and robotics are extensively used to enhance precision and efficiency. Additionally, Japanese manufacturers often employ advanced materials and processes that contribute to the overall innovation of unit and device assembly, allowing them to stay ahead of industry trends and meet evolving market demands.
Challenges and Disadvantages
Despite the numerous advantages, there are challenges and disadvantages associated with Japanese unit and device assembly that procurement and purchasing professionals must consider.
Language and Cultural Barriers
Language and cultural differences can pose significant challenges in international procurement. Miscommunications may lead to misunderstandings regarding specifications, timelines, and quality expectations. Moreover, cultural differences in business practices, such as decision-making processes and negotiation styles, can complicate collaboration. Overcoming these barriers often requires patience, cultural sensitivity, and sometimes the assistance of intermediaries or bilingual staff.
High Cost Structures
Japanese manufacturing is renowned for its quality, but this often comes at a higher cost. The emphasis on precision, quality control, and continuous improvement results in higher production costs compared to some other regions. While the long-term benefits of superior quality and reliability can offset these costs, initial procurement budgets may need to be higher to secure the best suppliers and technologies.
Supplier Negotiation Techniques
Effective negotiation with Japanese suppliers requires an understanding of their business culture and practices. Building strong relationships and approaching negotiations with respect and mutual benefit in mind are essential for successful outcomes.
Building Trust and Long-Term Relationships
Trust is fundamental in Japanese business culture. Suppliers are more inclined to offer favorable terms and collaborate on improvements when they trust their buyers. Building trust involves consistent communication, honoring commitments, and demonstrating reliability over time. Focusing on long-term relationships rather than short-term gains fosters a cooperative atmosphere where both parties are invested in each other’s success.
Negotiation Strategies
Negotiation with Japanese suppliers often involves a collaborative approach rather than a confrontational one. Understanding their priorities, such as quality and reliability, and aligning one’s proposals to support these interests can lead to more productive negotiations. It is also important to be patient, as decision-making processes may take longer due to consensus-building within the supplier’s organization. Presenting data-driven arguments and being flexible with terms can help in reaching mutually beneficial agreements.
Market Conditions and Trends
Staying abreast of market conditions and trends is vital for effective procurement from Japanese suppliers. The landscape is continually evolving, influenced by technological advancements, economic shifts, and global supply chain dynamics.
Technological Advancements
The rapid pace of technological innovation in Japan affects procurement strategies significantly. Advancements in automation, robotics, and materials science can lead to new opportunities for collaboration but also require procurement professionals to stay informed about the latest developments. Embracing these technologies can enhance efficiency and product quality, but it also necessitates ongoing investment in learning and adapting to new systems.
Global Supply Chain Dynamics
Global supply chains are subject to various external factors, including geopolitical tensions, trade policies, and disruptions such as natural disasters or pandemics. Japanese manufacturers, like others, must navigate these challenges to maintain a stable supply chain. Procurement professionals must develop strategies to mitigate risks, such as diversifying suppliers, maintaining safety stock, and establishing contingency plans to ensure uninterrupted supply.
Best Practices in International Procurement from Japan
Adopting best practices in international procurement can help maximize the benefits of sourcing from Japanese manufacturers while minimizing potential challenges.
Leveraging Technology and Automation
Utilizing advanced procurement technologies can streamline the sourcing process, enhance communication, and improve data management. Tools such as e-procurement platforms, supply chain management software, and collaborative project management systems facilitate better coordination with Japanese suppliers. Automation can reduce manual errors, speed up transactions, and provide real-time visibility into the procurement process, leading to more informed decision-making.
Continuous Improvement and Feedback Loops
Implementing continuous improvement practices is essential for maintaining and enhancing procurement efficiency. Establishing feedback loops with suppliers allows for the identification and resolution of issues promptly. Regular performance reviews, joint improvement initiatives, and open communication channels foster an environment where both parties can collaboratively enhance processes and outcomes. This iterative approach aligns with the Japanese philosophy of Kaizen and helps sustain high standards over time.
Case Studies
Examining real-world examples of successful procurement and purchasing from Japanese manufacturers can provide valuable insights and practical lessons.
One notable case is that of a global automotive company that partnered with several Japanese suppliers to enhance its production quality and efficiency. By adopting JIT principles and collaborating closely with suppliers on quality control, the company was able to reduce defects and streamline its inventory management. This partnership not only improved the company’s product offerings but also strengthened its competitive position in the market.
Another example involves a consumer electronics firm that leveraged advanced robotics technology from a Japanese supplier to automate its assembly line. This collaboration resulted in significant improvements in production speed and precision, enabling the company to meet growing demand while maintaining high quality standards. The success of this partnership was attributed to the open communication, shared innovation goals, and mutual trust between the two companies.
Conclusion
Procurement and purchasing from Japanese manufacturers offer a multitude of benefits, including high precision, superior quality, and innovative practices. However, navigating the complexities of international procurement requires a deep understanding of cultural nuances, effective negotiation strategies, and the ability to manage challenges such as language barriers and higher cost structures. By adopting best practices, leveraging technology, and fostering strong supplier relationships, companies can successfully harness the strengths of Japanese manufacturing to enhance their own operations and achieve long-term success in the global market.
資料ダウンロード
QCD調達購買管理クラウド「newji」は、調達購買部門で必要なQCD管理全てを備えた、現場特化型兼クラウド型の今世紀最高の購買管理システムとなります。
ユーザー登録
調達購買業務の効率化だけでなく、システムを導入することで、コスト削減や製品・資材のステータス可視化のほか、属人化していた購買情報の共有化による内部不正防止や統制にも役立ちます。
NEWJI DX
製造業に特化したデジタルトランスフォーメーション(DX)の実現を目指す請負開発型のコンサルティングサービスです。AI、iPaaS、および先端の技術を駆使して、製造プロセスの効率化、業務効率化、チームワーク強化、コスト削減、品質向上を実現します。このサービスは、製造業の課題を深く理解し、それに対する最適なデジタルソリューションを提供することで、企業が持続的な成長とイノベーションを達成できるようサポートします。
オンライン講座
製造業、主に購買・調達部門にお勤めの方々に向けた情報を配信しております。
新任の方やベテランの方、管理職を対象とした幅広いコンテンツをご用意しております。
お問い合わせ
コストダウンが利益に直結する術だと理解していても、なかなか前に進めることができない状況。そんな時は、newjiのコストダウン自動化機能で大きく利益貢献しよう!
(Β版非公開)