- お役立ち記事
- Fundamentals of sensorless vector control of permanent magnet synchronous motors and application to magnetic pole position estimation method
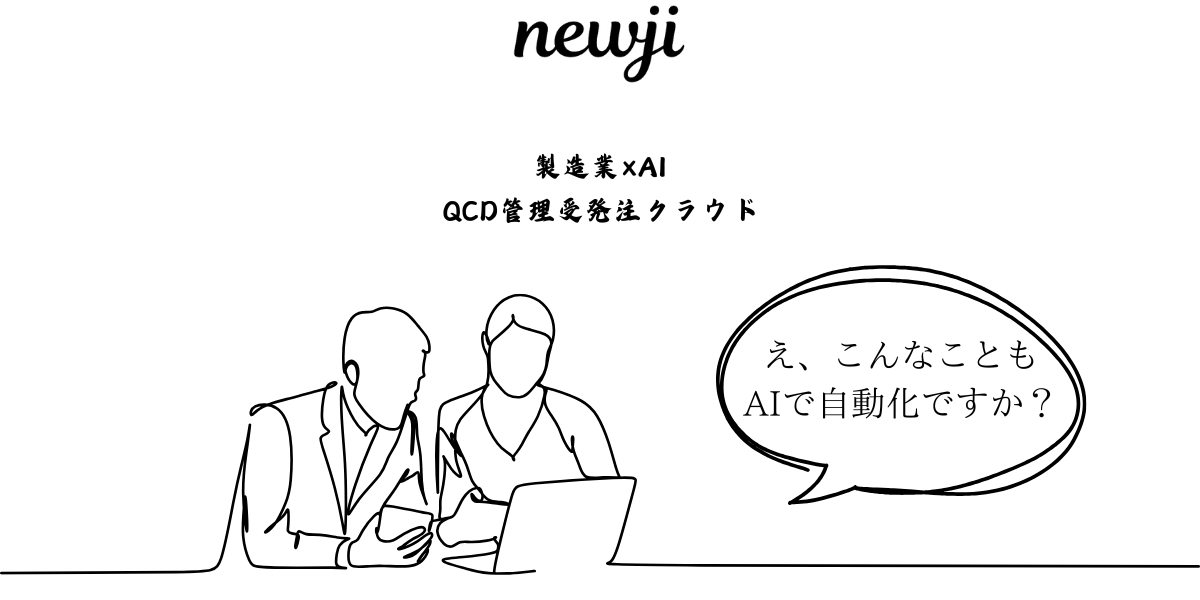
Fundamentals of sensorless vector control of permanent magnet synchronous motors and application to magnetic pole position estimation method
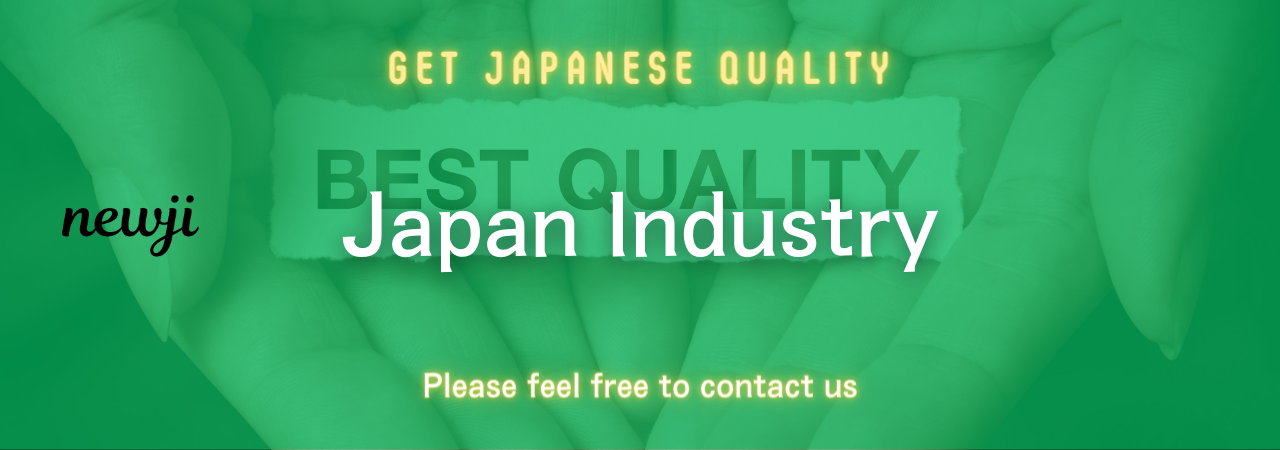
目次
Understanding Sensorless Vector Control of Permanent Magnet Synchronous Motors
Permanent Magnet Synchronous Motors (PMSMs) are a popular choice in various applications due to their high efficiency, compact size, and reliability.
The use of PMSMs spans from industrial machines to electric vehicles.
One crucial aspect of controlling these motors is the application of vector control techniques, particularly sensorless vector control.
Understanding the basics of this control method opens doors to optimizing motor performance and reducing costs.
Sensorless vector control eliminates the need for mechanical sensors, which are used traditionally to detect the rotor position.
This approach relies on estimating the rotor position and speed using mathematical models and algorithms.
The absence of physical sensors in PMSMs leads to several advantages, such as reduced system cost, increased robustness, and enhanced reliability.
The Fundamentals of Sensorless Control
The primary objective of sensorless vector control is to accurately estimate the rotor flux position and torque without employing physical sensors.
The process involves creating mathematical models that describe the behavior of the PMSM.
These models use real-time data from the motor, such as voltages and currents, to provide an estimation of the rotor position.
Two main techniques are employed in sensorless control:
1. Signal Injection Method.
2. Back Electromotive Force (EMF) Method.
Signal Injection Method
The signal injection method introduces a high-frequency voltage signal into the motor and observes the current response.
The asymmetry in the motor inductance and the impact of the signal enables the estimation of the rotor position.
This method is particularly effective at low speeds where the back EMF is not significant enough for estimation.
Back EMF Method
The back EMF method estimates rotor position by analyzing the motor’s back EMF, which is the voltage generated opposing the supply voltage as the rotor moves.
By differentiating the back EMF model, the rotor position and speed can be estimated.
This method works effectively at medium to high speeds.
Advantages of Sensorless Vector Control
Deploying sensorless vector control in PMSMs comes with several benefits:
1. Cost Efficiency: Eliminating mechanical sensors reduces the overall cost and complexity of the motor system.
2. Increased Reliability: Mechanical sensors are susceptible to wear and tear; removing them enhances the system’s reliability and lifespan.
3. Simplified Maintenance: Without sensors, there are fewer mechanical components to maintain, making the system simpler to service.
4. Enhanced Performance: Accurate rotor position estimation leads to optimized performance in terms of torque control and energy efficiency.
Challenges in Sensorless Vector Control
While the sensorless approach offers multiple advantages, it also poses challenges:
1. Reduced Low-Speed Performance: At very low speeds, estimating the rotor position becomes challenging due to inadequate back EMF.
2. Complexity of Algorithms: Implementing precise mathematical models requires sophisticated algorithms that may increase computational demands.
3. Sensitivity to Parameters: The accuracy of the sensorless control heavily relies on the accuracy of motor parameters, which might vary due to temperature and load changes.
Application of Magnetic Pole Position Estimation
Magnetic pole position estimation is crucial for achieving effective sensorless vector control.
Accurate estimation ensures that the motor operates efficiently and maintains desired performance levels.
Several algorithms can be used to estimate the magnetic pole position:
Extended Kalman Filter (EKF)
EKF is a popular algorithm utilized for estimating both parameters and states in a system.
For PMSMs, it applies to estimating the rotor position and speed.
The EKF updates its estimates in real-time, accommodating the system’s nonlinearities, making it suitable for dynamic environments.
Sliding Mode Observer (SMO)
The SMO technique involves creating a mathematical observer to estimate unmeasurable states such as rotor position and speed.
The observer ‘slides’ across the system states, adapting to disturbances and inaccuracies in the model, thus providing accurate estimates.
Model Reference Adaptive System (MRAS)
MRAS compares the output of a process model with that of a reference model to determine the rotor position.
The adaptability of MRAS systems allows for adjustments in the model to account for anomalies, ensuring efficiency in position estimation.
The Future of Sensorless Vector Control
As technology advances, the sensorless vector control of PMSMs will continue to evolve.
Research continues to optimize algorithms, reduce computational requirements, and improve low-speed performance.
The continual improvement in this domain will expand the application scope of PMSMs, supporting innovation in electric transportation, robotics, and renewable energy sectors.
Conclusion
Understanding the fundamentals of sensorless vector control in permanent magnet synchronous motors is essential for optimizing motor performance while minimizing costs.
Despite the challenges, the technology offers significant advantages and continues to evolve.
Application of advanced algorithms for pole position estimation further enhances the capability of sensorless control, promising a reliable future for PMSM technologies.
資料ダウンロード
QCD調達購買管理クラウド「newji」は、調達購買部門で必要なQCD管理全てを備えた、現場特化型兼クラウド型の今世紀最高の購買管理システムとなります。
ユーザー登録
調達購買業務の効率化だけでなく、システムを導入することで、コスト削減や製品・資材のステータス可視化のほか、属人化していた購買情報の共有化による内部不正防止や統制にも役立ちます。
NEWJI DX
製造業に特化したデジタルトランスフォーメーション(DX)の実現を目指す請負開発型のコンサルティングサービスです。AI、iPaaS、および先端の技術を駆使して、製造プロセスの効率化、業務効率化、チームワーク強化、コスト削減、品質向上を実現します。このサービスは、製造業の課題を深く理解し、それに対する最適なデジタルソリューションを提供することで、企業が持続的な成長とイノベーションを達成できるようサポートします。
オンライン講座
製造業、主に購買・調達部門にお勤めの方々に向けた情報を配信しております。
新任の方やベテランの方、管理職を対象とした幅広いコンテンツをご用意しております。
お問い合わせ
コストダウンが利益に直結する術だと理解していても、なかなか前に進めることができない状況。そんな時は、newjiのコストダウン自動化機能で大きく利益貢献しよう!
(Β版非公開)