- お役立ち記事
- Physical cleaning technology in the manufacturing process of semiconductor devices and how to utilize AI in the manufacturing process
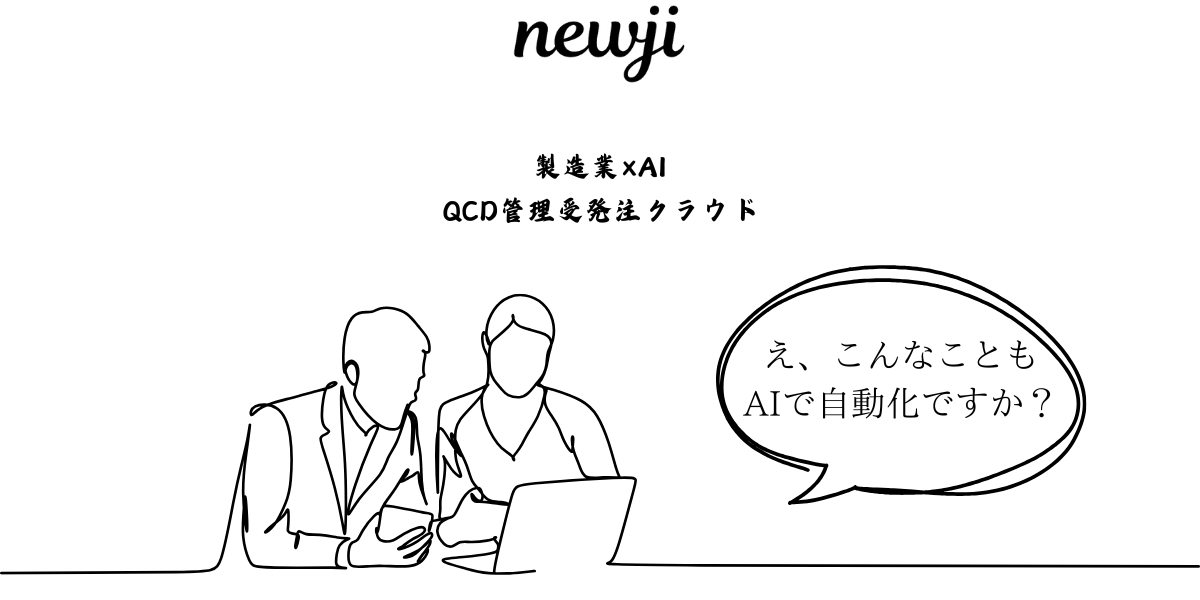
Physical cleaning technology in the manufacturing process of semiconductor devices and how to utilize AI in the manufacturing process
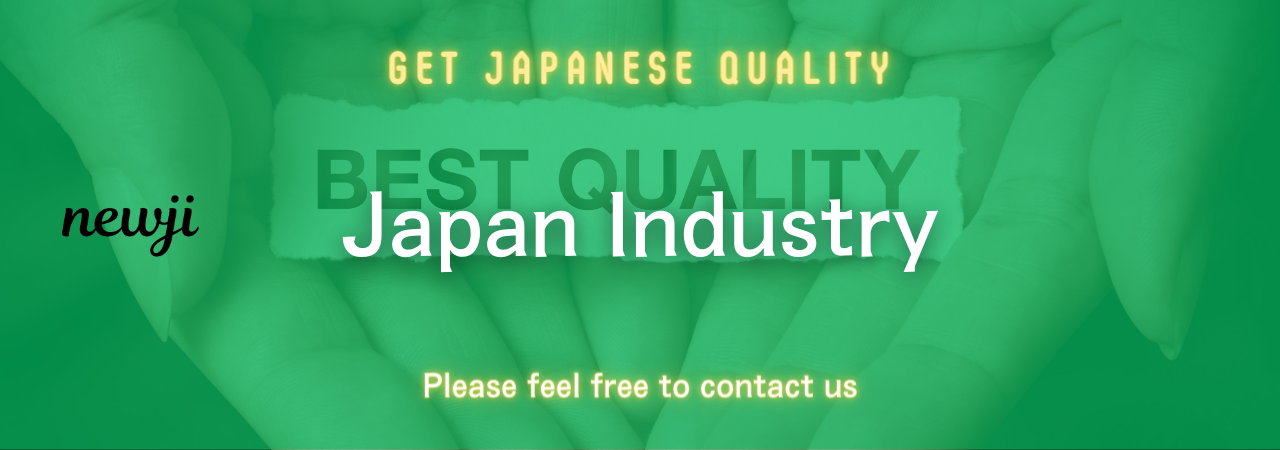
目次
Introduction to Semiconductor Manufacturing
Semiconductor devices are at the heart of every piece of modern technology.
They power everything from smartphones to cars, playing a crucial role in the devices we use daily.
The manufacturing process of semiconductors is incredibly complex and requires a high level of precision.
One critical aspect of this process is the physical cleaning technology used to ensure that each semiconductor is free of contaminants.
This ensures their optimal functionality and longevity.
Moreover, with the advancement of Artificial Intelligence (AI), manufacturers are exploring new ways to optimize these processes.
The Importance of Cleaning in Semiconductor Manufacturing
The fabrication of semiconductor devices involves numerous steps and various chemicals, which can introduce contaminants.
These contaminants, such as particles, metals, and organic residues, can lead to defects in the chips being produced.
Even the smallest particle can cause a significant problem, hence the need for thorough cleaning techniques throughout the manufacturing process.
Cleaning is crucial not only before the initial stages of production but throughout the entire manufacturing process.
For instance, during wafer fabrication, cleaning steps are strategically placed to remove particles and residues before critical process steps like oxidation, etching, or doping.
A failure to adequately clean can result in substantial wastage and increased costs.
Understanding Physical Cleaning Techniques
Physical cleaning methods are largely employed to ensure the removal of particles without affecting the semiconductor’s surface physically or chemically.
Some widely used techniques include mechanical scrubbing, ultrasonic cleaning, and mega-sonic cleaning.
Mechanical Scrubbing
Mechanical scrubbing involves physically removing particles from the wafer surface using soft brushes.
It’s often used in combination with chemical cleaning solutions to enhance its effectiveness.
However, care must be taken to avoid introducing new contaminants or causing damage to sensitive wafer surfaces.
Ultrasonic Cleaning
Ultrasonic cleaning utilizes high-frequency sound waves in liquid to remove particles.
This method sends ultrasonic vibrations through a cleaning solution to dislodge contaminants.
Ultrasonic cleaning is effective for removing submicron particles but can sometimes lead to cavitation, potentially damaging the wafer surface.
Mega-Sonic Cleaning
Mega-sonic cleaning is similar to ultrasonic cleaning but operates at a higher frequency.
This method reduces cavitation effects, making it a safer option for delicate wafer surfaces.
Mega-sonic cleaning is widely used due to its ability to remove particles without causing surface damage effectively.
Challenges in Physical Cleaning
Physical cleaning methods come with their own set of challenges.
As semiconductor devices become smaller, the precision required in cleaning them also increases.
Conventional cleaning methods face limitations in reaching the minute surfaces and complex architectures of modern semiconductors.
Another challenge is avoiding recontamination, where particles are redeposited on the wafer surface after cleaning.
This can occur from inadequate rinsing or drying processes, necessitating the integration of highly precise, automated cleaning systems.
Leveraging AI in Semiconductor Manufacturing
With the advent of AI, there is significant potential to optimize the semiconductor manufacturing process, including the cleaning phases.
AI algorithms can process vast amounts of data to predict and enhance cleaning regimens and equipment performance accurately.
Predictive Maintenance
AI can be used to monitor cleaning equipment and predict failures before they occur.
By analyzing equipment data, AI algorithms can forecast when maintenance should be performed, preventing downtime and enhancing productivity in the manufacturing environment.
Process Optimization
AI can provide insights into process optimization by analyzing historical cleaning data.
It can identify patterns and correlations that might not be apparent to human operators.
This allows for fine-tuning the cleaning process to maximize efficiency and minimize defects.
Real-time Monitoring and Control
AI systems can offer real-time monitoring and control of the cleaning process.
By continuously analyzing data from sensors and imaging systems, AI can detect anomalies and adjust processes on the fly, ensuring optimal cleaning outcomes.
Future Prospects of AI in Semiconductor Manufacturing
The integration of AI in semiconductor production holds immense promise for the future.
Manufacturers are continuously exploring ways to implement AI not only for cleaning processes but throughout the entire semiconductor fabrication lifecycle.
The use of AI-driven robotics and machine learning algorithms can lead to the development of fully autonomous production lines.
Such advancements could drastically reduce production costs, improve yield rates, and increase the scalability of semiconductor manufacturing.
Moreover, with the rise of 5G technology and the Internet of Things (IoT), the demand for semiconductors is anticipated to grow exponentially.
Implementing AI-driven solutions could be crucial in meeting this demand efficiently and sustainably.
Conclusion
Physical cleaning processes are integral to the manufacture of semiconductor devices.
Employing techniques such as mechanical scrubbing, ultrasonic, and mega-sonic cleaning ensures the removal of harmful contaminants.
However, the integration of AI into these cleaning processes and broader semiconductor manufacturing holds the key to future improvements.
By leveraging AI for predictive maintenance, process optimization, and real-time monitoring, manufacturers can achieve higher yields and maintain the quality of semiconductor devices.
As technology advances, the synergy between physical cleaning methods and AI will likely revolutionize semiconductor manufacturing, setting new benchmarks for efficiency and precision.
資料ダウンロード
QCD調達購買管理クラウド「newji」は、調達購買部門で必要なQCD管理全てを備えた、現場特化型兼クラウド型の今世紀最高の購買管理システムとなります。
ユーザー登録
調達購買業務の効率化だけでなく、システムを導入することで、コスト削減や製品・資材のステータス可視化のほか、属人化していた購買情報の共有化による内部不正防止や統制にも役立ちます。
NEWJI DX
製造業に特化したデジタルトランスフォーメーション(DX)の実現を目指す請負開発型のコンサルティングサービスです。AI、iPaaS、および先端の技術を駆使して、製造プロセスの効率化、業務効率化、チームワーク強化、コスト削減、品質向上を実現します。このサービスは、製造業の課題を深く理解し、それに対する最適なデジタルソリューションを提供することで、企業が持続的な成長とイノベーションを達成できるようサポートします。
オンライン講座
製造業、主に購買・調達部門にお勤めの方々に向けた情報を配信しております。
新任の方やベテランの方、管理職を対象とした幅広いコンテンツをご用意しております。
お問い合わせ
コストダウンが利益に直結する術だと理解していても、なかなか前に進めることができない状況。そんな時は、newjiのコストダウン自動化機能で大きく利益貢献しよう!
(Β版非公開)