- お役立ち記事
- Key points and change point management of process control methods based on Toyota style quality control
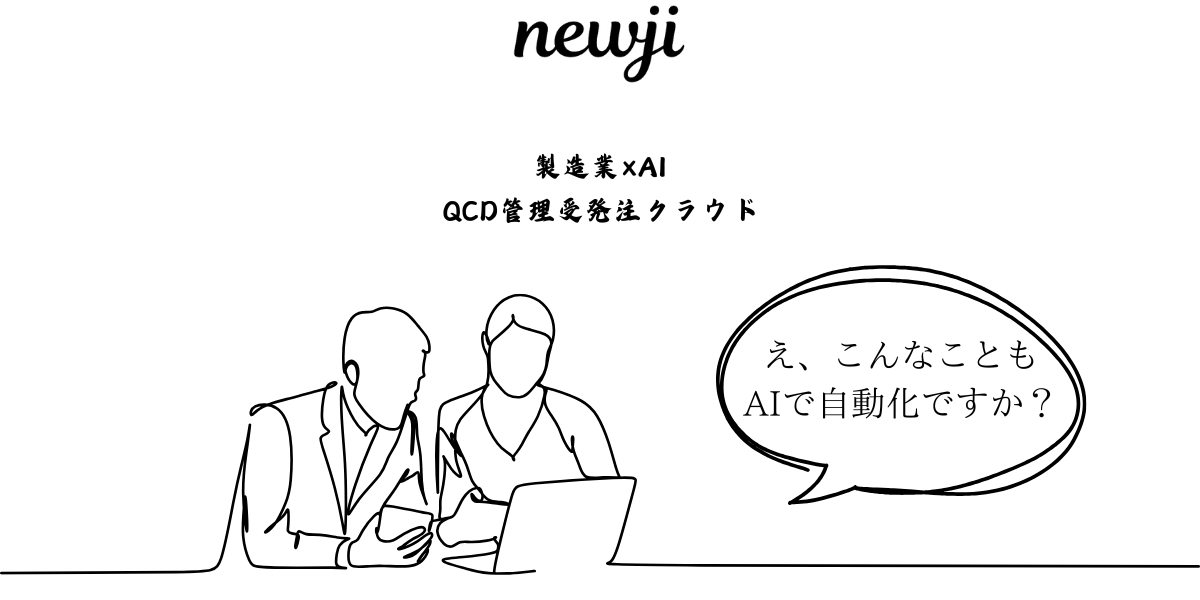
Key points and change point management of process control methods based on Toyota style quality control
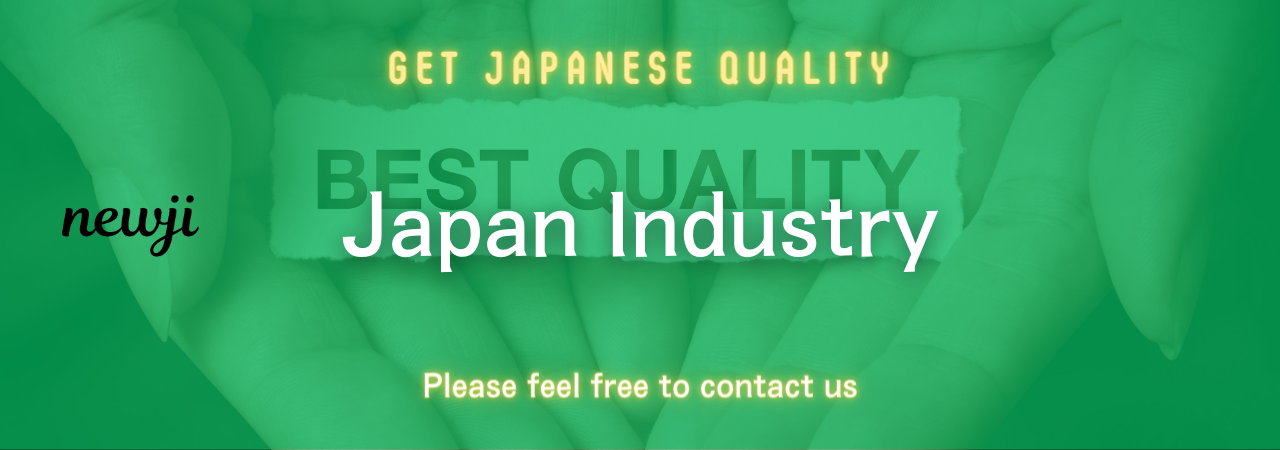
目次
Understanding Toyota’s Quality Control Philosophy
The Toyota Production System (TPS) is globally renowned for its efficiency and effectiveness in manufacturing and quality control.
At the core of Toyota’s success is a robust framework of process control methods, which emphasize continuous improvement and operational excellence.
Understanding these methods is essential for businesses seeking to enhance their own production processes and quality standards.
Quality control within the Toyota framework focuses on preventing defects by controlling and improving processes.
This approach has been pivotal in ensuring the consistent delivery of high-quality products, and it’s grounded in a few key principles: respect for people, Kaizen (continuous improvement), and the elimination of waste, commonly referred to as “lean manufacturing.”
Key Points of Toyota’s Process Control Methods
Toyota’s process control is characterized by several distinctive practices.
These methods are designed to maximize productivity and minimize errors, thereby ensuring a high standard of quality across all stages of production.
1. Standardized Work
At Toyota, the foundation of quality control is standardized work.
This involves developing a precise, repeatable process that defines the most efficient way to perform a task.
Standardized work ensures that employees follow the best practices consistently, reducing variability and errors.
In practical terms, this means documenting each step in the production process, including the tools and materials required, task sequences, and target times.
This documentation becomes the baseline for measuring improvements and identifying deviations.
2. Jidoka (Automation with a Human Touch)
Jidoka, a term that encapsulates Toyota’s approach to automation, is about empowering machines and workers to detect and flag abnormalities.
When a problem is identified, the process is immediately halted to prevent the continuation of defective output.
This principle ensures that issues are addressed at the source, preventing defects from propagating through the production line.
By incorporating human oversight and autonomous machines, Toyota harmonizes technology with human intelligence to maintain stringent quality controls.
3. Kaizen (Continuous Improvement)
Kaizen is the practice of continuous improvement, central to Toyota’s quality control strategy.
It involves all employees actively seeking ways to improve processes, products, and services.
Kaizen encourages incremental changes that may seem small individually but cumulatively lead to significant improvements in efficiency and quality.
This practice fosters a culture where improvement is everyone’s responsibility and innovation is a daily goal.
4. Just-In-Time (JIT) Manufacturing
Just-In-Time is a production strategy that aligns raw-material orders with production schedules.
Toyota uses JIT to reduce waste by receiving goods only as needed in the production process, minimizing inventory costs.
This approach relies heavily on precise process control and a well-synchronized supply chain.
By producing just what is needed, when it is needed, JIT not only streamlines operations but also enhances product quality by reducing potential for obsolescence and defects.
5. Visual Management Tools
Visual management is an integral component of Toyota’s process control.
Tools such as Kanban boards, shadow boards, and visual controls keep all team members informed and focused on the objectives.
These tools help facilitate communication, highlight abnormalities, and ensure that everyone is aligned on performance targets and any action items required for improvement.
By making processes visible, problems become apparent and can be addressed swiftly.
Change Point Management in Toyota’s Process Control
Managing change points effectively is crucial in Toyota’s process control methods.
Change points refer to any transition that alters a process, such as changes in materials, personnel, equipment, or operating conditions.
These transitions pose potential risks for quality degradation if not managed properly.
1. Change Point Process Control
Toyota employs a meticulous change point process control system.
This system involves identifying potential change points and implementing control measures to ensure that these changes do not affect product quality adversely.
A critical aspect of this management is thorough documentation before and after any change.
This includes understanding the impact of the change on the process, retraining employees if necessary, and recalibrating equipment.
2. Preemptive Risk Assessment
Before implementing any changes, Toyota’s quality control team conducts risk assessments.
This involves evaluating potential risks associated with the change and devising strategies to mitigate them.
Risk assessment ensures that all foreseeable problems are identified and addressed proactively, reducing the likelihood of quality issues arising post-change.
3. Continuous Monitoring and Feedback
Post-change, the processes undergo continuous monitoring to ensure the changes yield positive outcomes.
Any deviations or abnormalities are quickly analyzed, with feedback loops in place to refine the process further.
By maintaining an ongoing feedback system, Toyota can quickly adapt to new challenges and harness opportunities for improvement, even after a change has been implemented.
The Benefits of Toyota’s Quality Control Methods
Adopting Toyota-style quality control methods offers numerous benefits for organizations aiming to improve their production processes and product quality.
1. Enhanced Product Quality
Through rigorous standardized work, vigilant monitoring, and continuous improvement practices, companies can achieve significantly higher product quality.
2. Reduced Waste and Costs
Lean manufacturing principles minimize waste and optimize resource use, directly reducing production costs and increasing operational efficiency.
3. Increased Employee Engagement
When employees are empowered to partake in improvement initiatives, their engagement and job satisfaction increase, fostering a culture of collaboration and innovation.
4. Better Adaptability to Change
With a strong change point management system, organizations are better equipped to implement changes smoothly, maintaining quality standards throughout transitions.
In summary, Toyota’s approach to quality control, with its emphasis on process efficiency, standardized operations, and continuous improvement, serves as a robust model for any business seeking to enhance its manufacturing processes.
By understanding and applying these principles, companies can achieve superior quality outcomes, operational excellence, and sustained competitive advantage.
資料ダウンロード
QCD調達購買管理クラウド「newji」は、調達購買部門で必要なQCD管理全てを備えた、現場特化型兼クラウド型の今世紀最高の購買管理システムとなります。
ユーザー登録
調達購買業務の効率化だけでなく、システムを導入することで、コスト削減や製品・資材のステータス可視化のほか、属人化していた購買情報の共有化による内部不正防止や統制にも役立ちます。
NEWJI DX
製造業に特化したデジタルトランスフォーメーション(DX)の実現を目指す請負開発型のコンサルティングサービスです。AI、iPaaS、および先端の技術を駆使して、製造プロセスの効率化、業務効率化、チームワーク強化、コスト削減、品質向上を実現します。このサービスは、製造業の課題を深く理解し、それに対する最適なデジタルソリューションを提供することで、企業が持続的な成長とイノベーションを達成できるようサポートします。
オンライン講座
製造業、主に購買・調達部門にお勤めの方々に向けた情報を配信しております。
新任の方やベテランの方、管理職を対象とした幅広いコンテンツをご用意しております。
お問い合わせ
コストダウンが利益に直結する術だと理解していても、なかなか前に進めることができない状況。そんな時は、newjiのコストダウン自動化機能で大きく利益貢献しよう!
(Β版非公開)