- お役立ち記事
- Fundamentals of metal fracture surface analysis and application to stress estimation, fracture mechanism, and fracture cause estimation
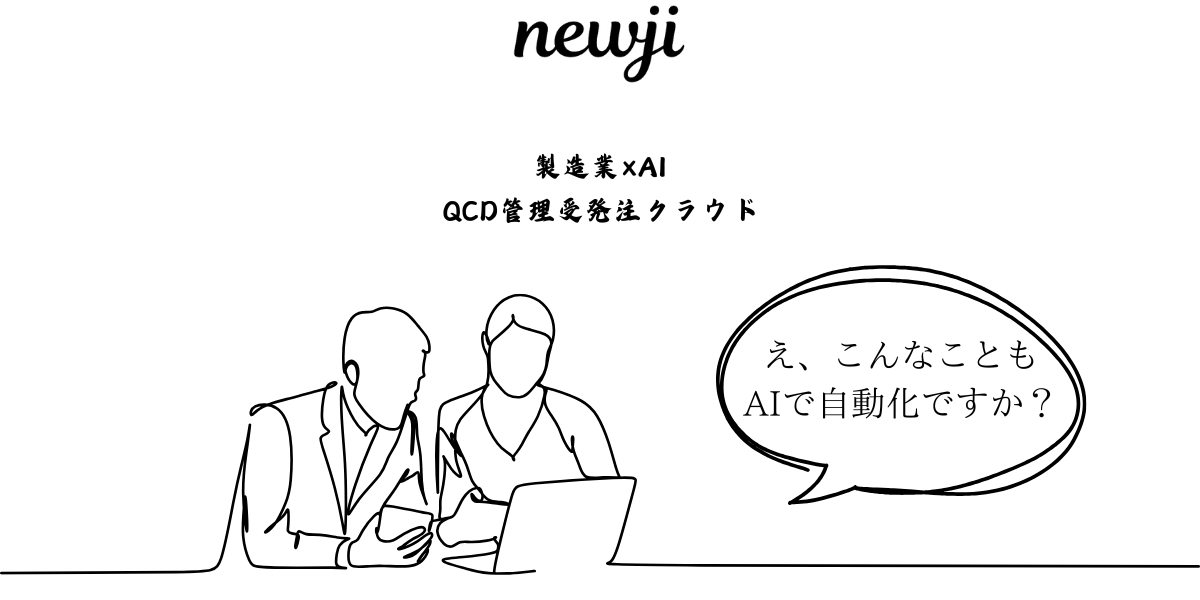
Fundamentals of metal fracture surface analysis and application to stress estimation, fracture mechanism, and fracture cause estimation
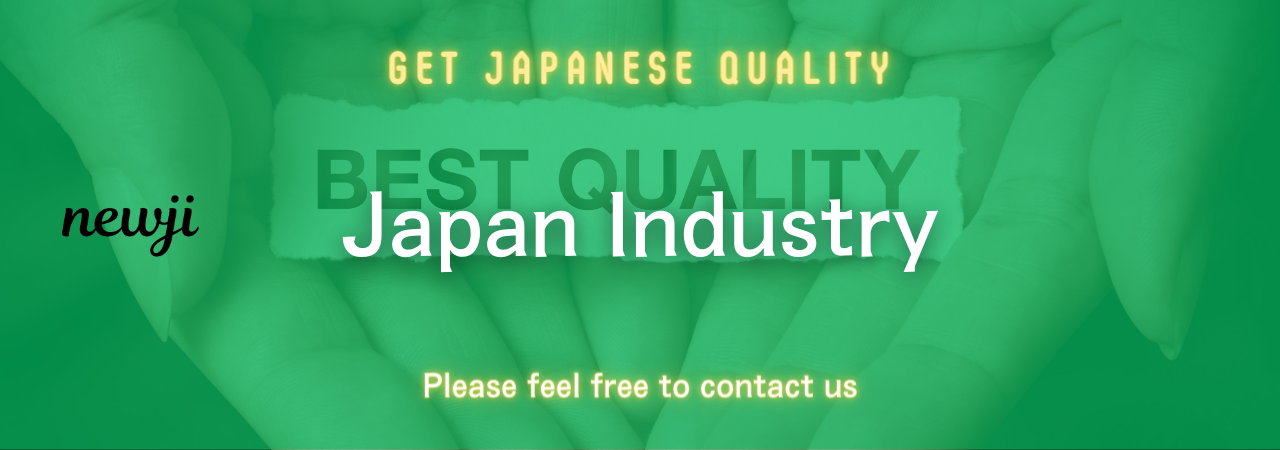
目次
Understanding Metal Fracture Surface Analysis
Metal fracture surface analysis is a crucial aspect of materials science and engineering.
It involves examining the surfaces of broken metals to uncover valuable information about the nature of the fracture.
This process provides insights into the stresses that caused the fracture, the mechanism behind the break, and the potential reasons why the fracture occurred in the first place.
What is Metal Fracture Surface Analysis?
Metal fracture surface analysis is essentially an investigative technique used by engineers and scientists to determine the causes of material failure.
When a metal object breaks, the analysis of its fracture surface can tell a lot about the stresses it underwent and the conditions leading to its failure.
By closely examining the characteristics of the fracture surface, experts can identify whether a metal failed due to tension, compression, shear, or a combination of these stresses.
The Importance of Stress Estimation
Estimating the stress that led to a metal’s failure is vital for improving the safety and performance of structures.
Stress estimation helps engineers know whether a component was subjected to normal operating conditions or excessive stress.
If fractures are due to unexpected stress levels, it may indicate design shortcomings or improper use of materials.
Fracture Mechanism Analysis
Fracture mechanism analysis focuses on understanding how and why the fracture occurred.
The mechanism can be ductile, brittle, fatigue, or a combination, each having distinct indications on the fracture surface.
– **Ductile Fracture**: Characterized by a significant plastic deformation before failure, ductile fractures show dimpled surfaces.
– **Brittle Fracture**: Leads to little or no plastic deformation, with a shiny, granular appearance indicating rapid crack propagation.
– **Fatigue Fracture**: Occurs under repeated stress cycles, showing beach marks or striations that suggest progressive failure.
Fracture Cause Estimation
Determining the cause of fracture goes beyond identifying the stresses; it includes assessing other factors such as material defects, design flaws, or corrosion.
By pinpointing the cause, industries can prevent future failures by adopting more robust designs, selecting better materials, or implementing improved maintenance procedures.
Methods of Analyzing Metal Fracture Surfaces
To perform a metal fracture surface analysis, experts employ various microscopic and macroscopic methods.
Visual Examination
The first step often involves a simple visual examination with the naked eye or a magnifying glass.
This method helps quickly assess obvious features like deformation or pre-existing macro-flaws.
Optical Microscopy
Optical microscopy offers a closer look at fracture surfaces, revealing finer details such as the fracture pattern and initiation points.
This analysis helps in distinguishing between ductile and brittle fractures and can identify striation patterns indicative of fatigue failure.
Scanning Electron Microscopy (SEM)
SEM is a powerful tool for high-resolution examination of fracture surfaces.
It provides detailed images and topographical data, crucial for analyzing micro-features and understanding the fracture path.
SEM is invaluable for identifying microvoids, river patterns, and secondary cracks.
Energy Dispersive X-ray Spectroscopy (EDX)
Coupled with SEM, EDX allows for elemental analysis of the fracture surface.
This technique can detect compositional variations or impurities that might have contributed to the fracture, offering insight into material inconsistencies or contamination.
X-ray Diffraction (XRD)
XRD is utilized to identify the crystalline structure and phases present at the fracture site.
Changes in the diffraction patterns can indicate phase transformations occurring during fracture, particularly in heat-treated alloys.
Applications of Fracture Surface Analysis
Metal fracture surface analysis is applied across various industries to enhance safety, reliability, and performance.
Aerospace Industry
In aerospace, fracture analysis contributes to understanding the root causes of component failures.
By analyzing fractures from crashed aircraft, forensic engineers can improve material selection and design parameters for future models.
Automotive Sector
The automotive industry relies on fracture surface analysis to prevent failure in engine components, chassis, and structural parts.
Failure analysis not only aids in improving the materials used but also in refining manufacturing processes.
Construction and Infrastructure
Bridges and buildings require robust materials to ensure long service life.
Fracture analysis helps in understanding failure modes of structural metals, leading to more resilient constructions and mitigation of risks.
Preventing Metal Failures
To minimize the occurrence of metal failures, industries must adopt preventive measures based on fracture surface analysis findings.
Material Selection
Choosing the right material for the job is fundamental.
Metals should be selected based on their mechanical properties, resistance to environmental conditions, and tolerance to operational stresses.
Design Improvements
Using insights from fracture analysis, engineers can redesign components to better distribute loads and reduce stress concentrations, enhancing durability.
Regular Maintenance
Routine inspections and maintenance can detect early signs of wear or damage, preventing catastrophic failures.
Using non-destructive testing methods helps in monitoring component integrity over time.
Conclusion
Metal fracture surface analysis is a powerful tool that aids in understanding the nature, mechanism, and cause of metal failures.
Through detailed examination and analysis, industries can make informed decisions that lead to safer and more reliable products.
By applying findings from fracture studies, engineers can improve designs, select appropriate materials, and implement effective maintenance strategies, ultimately prolonging the lifespan of metal components and preventing future failures.
資料ダウンロード
QCD調達購買管理クラウド「newji」は、調達購買部門で必要なQCD管理全てを備えた、現場特化型兼クラウド型の今世紀最高の購買管理システムとなります。
ユーザー登録
調達購買業務の効率化だけでなく、システムを導入することで、コスト削減や製品・資材のステータス可視化のほか、属人化していた購買情報の共有化による内部不正防止や統制にも役立ちます。
NEWJI DX
製造業に特化したデジタルトランスフォーメーション(DX)の実現を目指す請負開発型のコンサルティングサービスです。AI、iPaaS、および先端の技術を駆使して、製造プロセスの効率化、業務効率化、チームワーク強化、コスト削減、品質向上を実現します。このサービスは、製造業の課題を深く理解し、それに対する最適なデジタルソリューションを提供することで、企業が持続的な成長とイノベーションを達成できるようサポートします。
オンライン講座
製造業、主に購買・調達部門にお勤めの方々に向けた情報を配信しております。
新任の方やベテランの方、管理職を対象とした幅広いコンテンツをご用意しております。
お問い合わせ
コストダウンが利益に直結する術だと理解していても、なかなか前に進めることができない状況。そんな時は、newjiのコストダウン自動化機能で大きく利益貢献しよう!
(Β版非公開)