- お役立ち記事
- How to introduce digital twin technology to accelerate process improvement in the manufacturing industry
How to introduce digital twin technology to accelerate process improvement in the manufacturing industry
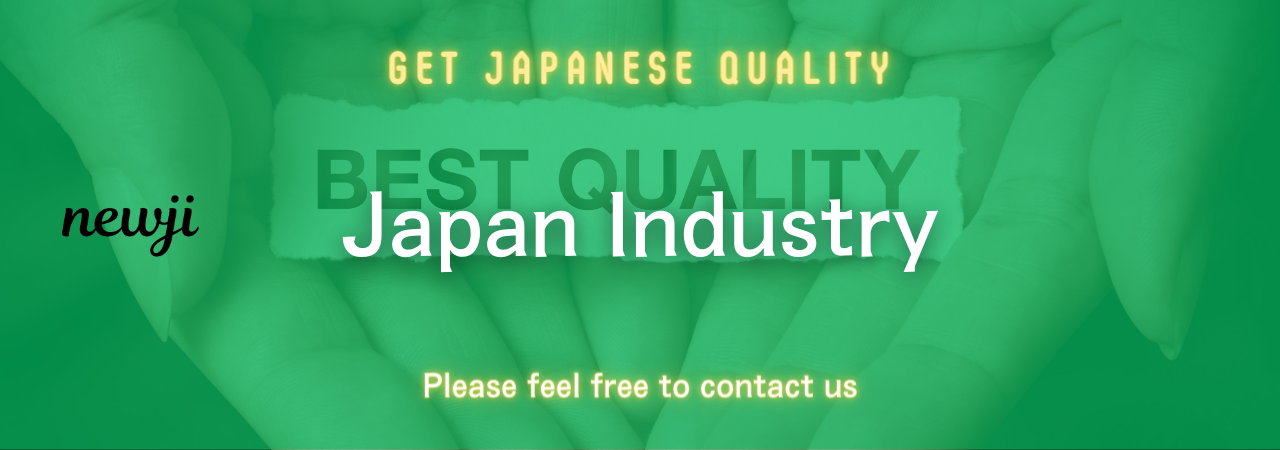
目次
Understanding Digital Twin Technology
Digital twin technology is transforming industries, and the manufacturing sector is at the forefront of this revolution.
A digital twin is a virtual model of a physical process, product, or service, effectively bridging the gap between the physical and digital worlds.
By using real-time data and simulation, digital twins can replicate the functioning of their physical counterparts to optimize operations and predict future outcomes.
These virtual counterparts enable manufacturers to enhance the efficiency of their production processes, reduce costs, and improve product quality.
By creating a dynamic digital representation, manufacturers can test scenarios, analyze performance, and foresee potential issues without disrupting actual operations.
The Benefits of Digital Twin Technology in Manufacturing
In the manufacturing industry, digital twins offer several advantages that contribute to process improvements and operational excellence.
Enhanced Product Design
With digital twin technology, manufacturers can simulate product designs and test them in a virtual environment.
This process helps identify design flaws and enables adjustments before the production phase.
It fosters innovation and creativity, as designers can experiment with various configurations without incurring physical testing costs.
Streamlined Production Processes
Digital twins allow manufacturers to scrutinize every step of their production processes.
They can identify bottlenecks, optimize resource allocation, and streamline workflows to increase efficiency.
This results in faster production times, lower operational costs, and increased output without compromising quality.
Predictive Maintenance
By continuously monitoring equipment and machinery through digital twins, manufacturers can predict malfunctions before they occur.
Predictive maintenance reduces downtime, extends equipment life, and minimizes unexpected repair costs.
It ensures that production lines remain operational, enhancing overall productivity.
Improved Decision-Making
Leveraging digital twin technology allows manufacturers to make data-driven decisions.
By analyzing real-time data, managers can assess the impact of changes and improvements before implementing them on the shop floor.
This data-centric approach results in better strategic planning and operational adjustments.
Steps to Implement Digital Twin Technology in Manufacturing
Bringing digital twin technology into the manufacturing ecosystem requires a strategic approach to ensure successful implementation.
1. Define Objectives and Scope
Start by defining the goals you aim to achieve with digital twin technology.
Whether it is improving product quality, reducing production costs, or increasing efficiency, having clear objectives will guide the entire process.
Identifying the specific areas where digital twins will be beneficial helps to focus efforts and resources where they are most needed.
2. Choose the Right Technology Partner
Selecting the right technology partner is critical for the successful adoption of digital twins.
Look for partners with expertise in digital twin solutions and experience in the manufacturing sector.
Evaluate their technology, support services, and previous project outcomes to ensure they align with your business objectives.
3. Gather and Integrate Data
To create an accurate digital twin, you need to gather data from various sources within your manufacturing environment.
This data can include sensor readings, machine outputs, and operational logs.
Integration with existing IT systems and industry 4.0 technologies is essential for seamless data flow and real-time updates.
4. Develop and Test the Digital Twin
Once you have the necessary data, develop the digital twin model using simulation software and analytical tools.
It is crucial to test the model extensively, verifying its accuracy and functionality.
Ensure the digital twin replicates the physical process accurately and can simulate potential scenarios and outcomes reliably.
5. Implement and Monitor the Solution
Upon successful testing, implement the digital twin solution within your manufacturing operations.
Monitor its performance closely, assessing its impact on production processes and outcomes.
Collect feedback from all stakeholders and make necessary adjustments to align the digital twin with changing business needs and goals.
Overcoming Challenges in Digital Twin Implementation
While the benefits of digital twin technology are immense, implementing it comes with challenges that manufacturers need to navigate.
Data Management and Privacy
Handling vast volumes of data poses challenges, especially related to data privacy and security.
Manufacturers should establish robust data management protocols and ensure compliance with data protection regulations to safeguard sensitive information.
Integration with Legacy Systems
Integrating digital twin technology with existing legacy systems can be complex.
Manufacturers may need to upgrade infrastructure and ensure compatibility with modern technologies to enable smooth data exchange and real-time updates.
Cost and Resource Allocation
The initial investment required for implementing digital twins may be high.
Manufacturers should plan their budgets effectively and allocate resources strategically to manage costs.
Exploring scalable solutions can help manage financial commitments more effectively.
Future Prospects of Digital Twin Technology in Manufacturing
As technology evolves, digital twin technology is set to become increasingly vital in the manufacturing industry.
Advancements in artificial intelligence and machine learning will further enhance the capabilities of digital twins, enabling predictive modeling and more accurate simulations.
Manufacturers adopting digital twin technology can expect improved competitiveness, better risk management, and enhanced sustainability practices.
Embracing digital twins not only accelerates process improvements but also prepares manufacturers for future challenges and opportunities in an ever-changing industrial landscape.
In conclusion, introducing digital twin technology can profoundly impact the manufacturing sector, driving innovations and efficiencies like never before.
By following strategic steps for implementation and addressing associated challenges, manufacturers can unlock the full potential of digital twins to revolutionize their operations and stay ahead in the competitive market.
資料ダウンロード
QCD調達購買管理クラウド「newji」は、調達購買部門で必要なQCD管理全てを備えた、現場特化型兼クラウド型の今世紀最高の購買管理システムとなります。
ユーザー登録
調達購買業務の効率化だけでなく、システムを導入することで、コスト削減や製品・資材のステータス可視化のほか、属人化していた購買情報の共有化による内部不正防止や統制にも役立ちます。
NEWJI DX
製造業に特化したデジタルトランスフォーメーション(DX)の実現を目指す請負開発型のコンサルティングサービスです。AI、iPaaS、および先端の技術を駆使して、製造プロセスの効率化、業務効率化、チームワーク強化、コスト削減、品質向上を実現します。このサービスは、製造業の課題を深く理解し、それに対する最適なデジタルソリューションを提供することで、企業が持続的な成長とイノベーションを達成できるようサポートします。
オンライン講座
製造業、主に購買・調達部門にお勤めの方々に向けた情報を配信しております。
新任の方やベテランの方、管理職を対象とした幅広いコンテンツをご用意しております。
お問い合わせ
コストダウンが利益に直結する術だと理解していても、なかなか前に進めることができない状況。そんな時は、newjiのコストダウン自動化機能で大きく利益貢献しよう!
(Β版非公開)