- お役立ち記事
- Fundamentals and design of sequence control, application of ladder programming, and practical points
月間77,185名の
製造業ご担当者様が閲覧しています*
*2025年2月28日現在のGoogle Analyticsのデータより
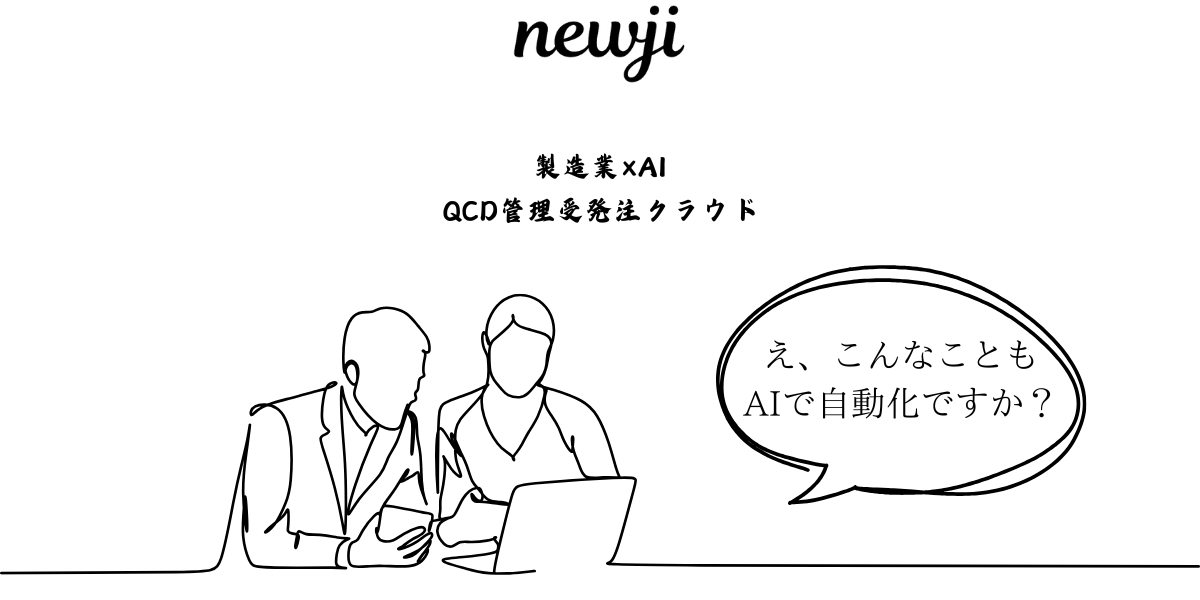
Fundamentals and design of sequence control, application of ladder programming, and practical points
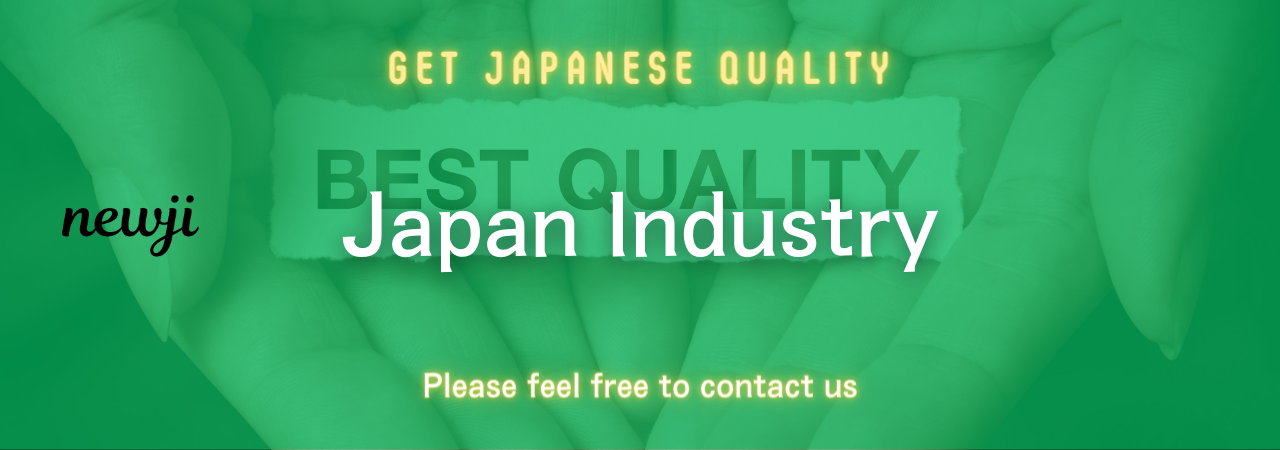
目次
Understanding Sequence Control
Sequence control is a method used in automation and control systems to ensure that processes are executed in a specific order.
This type of control is crucial in industries where precise operations are needed, such as in manufacturing lines, where each step must be completed before the next one begins.
Sequence control can be found in various applications, from traffic lights to complex industrial systems.
The fundamental concept of sequence control involves a series of operations dictated by a pre-defined sequence.
Each operation must be executed in the correct order to achieve the desired outcome.
This can involve tasks like starting a motor, opening a valve, or checking a sensor reading.
The system will move to the next step in the sequence only when the previous step has been successfully completed and any required conditions are met.
The Role of Ladder Programming
Ladder programming is one of the most commonly used languages in sequence control.
It is particularly popular in designing and implementing control systems for programmable logic controllers (PLCs).
The reason for its popularity lies in its simplicity and resemblance to electrical relay logic diagrams, making it easy for engineers and technicians with an electrical background to understand.
Ladder diagrams utilize visual symbols to represent control circuits.
These symbols appear as rungs on a ladder, where each rung consists of a series of switches and coils that correspond to inputs, outputs, and actions.
By visually mapping out the sequence of control, engineers can easily design and troubleshoot automated systems.
A typical ladder program might involve sequences that start by checking sensor inputs, processing these inputs through logical operations, and producing outputs like turning on or off motors or lights.
Each rung can be thought of as a set of instructions telling the system what to do under specific conditions.
Designing Sequence Control Systems
The design of a sequence control system requires meticulous planning and understanding of the processes involved.
The first step in designing such a system is to clearly define each step of the sequence and the conditions that must be met for progression.
This involves identifying all necessary inputs (such as sensors or user commands) and desired outputs (like actuators or motors).
Once the sequence is documented, it’s translated into a control program, often using ladder programming.
This involves creating a flow of logic that the control system will follow.
It’s essential to account for every possible scenario and include fail-safes and error-handling mechanisms to ensure smooth and safe operation.
Testing is a critical step in the development of sequence control systems.
Simulations can be run to verify that the sequence performs as expected under various conditions.
Final implementation should only occur after rigorous testing to avoid costly mistakes and downtime.
Application Areas of Sequence Control
Sequence control is applied in various industries due to its ability to manage complex processes efficiently.
In manufacturing, for instance, assembly lines use sequence control to ensure each part of a product is assembled correctly.
Automated guided vehicles (AGVs) in warehouses often rely on sequence control to navigate paths and complete tasks.
In the realm of home automation, sequence control ensures that lighting, security, and climate control systems operate in harmony based on user preferences and environmental conditions.
Moreover, in transportation systems, sequence control is pivotal in managing railway signals and switches, ensuring smooth train operations.
Practical Points to Consider
When designing and implementing sequence control systems, there are several practical aspects to keep in mind:
First, simplicity is key.
While it’s tempting to create overly complex sequences to handle every possible situation, keeping sequences simple makes them easier to implement and troubleshoot.
Second, flexibility should be built into the system.
Processes can change, and a rigid system may not adapt well, leading to inefficiencies or requiring costly redesigns.
Designing with modular logic blocks allows for easier updates and scalability.
Third, safety cannot be overemphasized.
In any control system, especially in industrial applications, safety precautions must be integrated to prevent hazardous situations.
Ensuring there’s a manual override or emergency stop functionality is vital.
Lastly, clear documentation is essential.
Properly documenting the program logic, including sequence steps, conditions, and changes, can save time during future maintenance or when onboarding new personnel.
The Future of Sequence Control
As technology advances, the field of sequence control continues to evolve.
The integration of more advanced control methodologies, including artificial intelligence and machine learning, is poised to make automated systems even smarter and more efficient.
These technologies could allow for predictive maintenance, where the control system anticipates and identifies maintenance needs before they result in failures.
Moreover, the trend of Industry 4.0 and the Internet of Things (IoT) paves the way for even more interconnected and responsive sequence control systems.
These advancements promise more adaptability and data-driven improvements, ultimately enhancing productivity and efficiency across various sectors.
In conclusion, understanding the fundamentals and design of sequence control, along with the application of ladder programming, equips engineers and technicians to implement systems that are efficient, reliable, and adaptable.
Keeping practical points in mind ensures these systems operate smoothly, providing value across numerous applications and industries.
資料ダウンロード
QCD管理受発注クラウド「newji」は、受発注部門で必要なQCD管理全てを備えた、現場特化型兼クラウド型の今世紀最高の受発注管理システムとなります。
ユーザー登録
受発注業務の効率化だけでなく、システムを導入することで、コスト削減や製品・資材のステータス可視化のほか、属人化していた受発注情報の共有化による内部不正防止や統制にも役立ちます。
NEWJI DX
製造業に特化したデジタルトランスフォーメーション(DX)の実現を目指す請負開発型のコンサルティングサービスです。AI、iPaaS、および先端の技術を駆使して、製造プロセスの効率化、業務効率化、チームワーク強化、コスト削減、品質向上を実現します。このサービスは、製造業の課題を深く理解し、それに対する最適なデジタルソリューションを提供することで、企業が持続的な成長とイノベーションを達成できるようサポートします。
製造業ニュース解説
製造業、主に購買・調達部門にお勤めの方々に向けた情報を配信しております。
新任の方やベテランの方、管理職を対象とした幅広いコンテンツをご用意しております。
お問い合わせ
コストダウンが利益に直結する術だと理解していても、なかなか前に進めることができない状況。そんな時は、newjiのコストダウン自動化機能で大きく利益貢献しよう!
(β版非公開)