- お役立ち記事
- Fundamentals of friction, wear, and lubrication, and applications to wear improvement technology and damage prevention design
月間77,185名の
製造業ご担当者様が閲覧しています*
*2025年2月28日現在のGoogle Analyticsのデータより
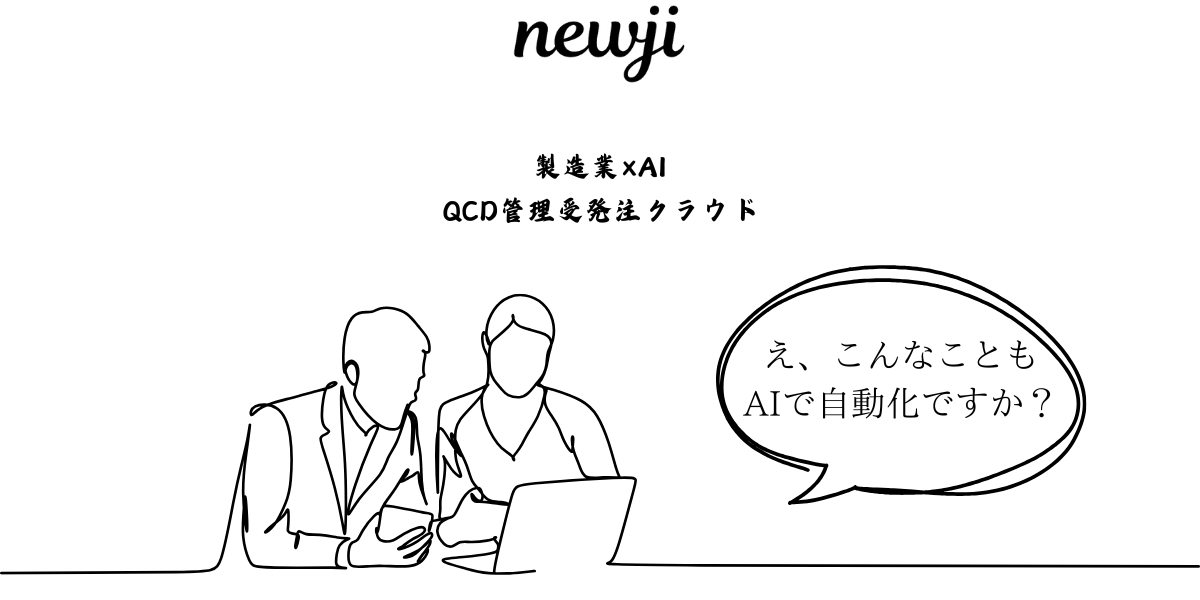
Fundamentals of friction, wear, and lubrication, and applications to wear improvement technology and damage prevention design
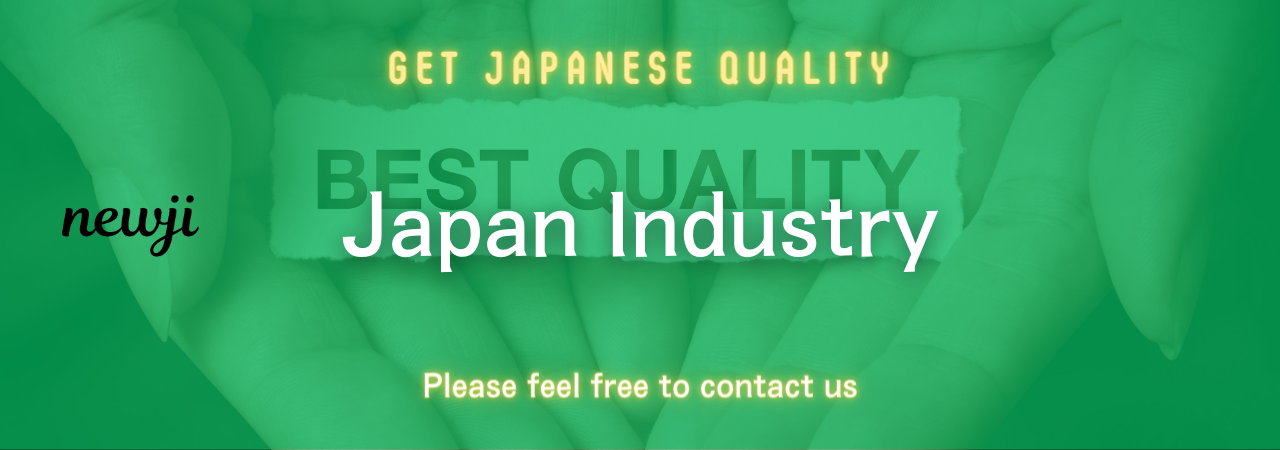
Understanding the principles of friction, wear, and lubrication is essential for engineers and designers working with moving parts.
These fundamentals play a crucial role in enhancing the performance, durability, and efficiency of mechanical systems.
By mastering these concepts, one can develop effective strategies for wear improvement and damage prevention.
目次
Understanding Friction
Friction is the resistance to motion that occurs when two surfaces slide against each other.
This force can be beneficial, such as providing traction for vehicle tires, or detrimental, leading to energy loss and wear of components.
Friction is generally classified into two types: static and kinetic.
Static friction is the force that needs to be overcome to initiate movement between stationary objects.
Once the movement starts, kinetic friction comes into play, which is usually less than static friction.
These forces are primarily determined by the nature of materials in contact, surface roughness, and the normal force pressing the surfaces together.
The Role of Friction in Mechanical Systems
In mechanical systems, friction is a double-edged sword.
While it is necessary for actions like gripping and braking, excessive friction can cause overheating, increased fuel consumption, and premature component failure.
Managing friction is thus vital to ensure the reliability and longevity of machinery.
Coefficient of Friction
The coefficient of friction is a dimensionless number that represents the ratio of frictional resistance to the normal force.
It is different for static and kinetic friction and varies with material pairs.
For improved industrial applications, understanding and controlling the coefficient of friction is crucial.
Examining Wear
Wear refers to the gradual removal of material from surfaces due to mechanical action.
It can significantly impact the performance and life span of components.
Understanding different types of wear can help in designing more robust systems.
Types of Wear
There are several types of wear, including adhesive wear, abrasive wear, surface fatigue, and corrosive wear.
1. **Adhesive Wear:** Occurs when materials transfer from one surface to another due to microscopic welding at contact points.
2. **Abrasive Wear:** Happens when hard particles or rough surfaces slide across a softer surface, scrapping material away.
3. **Surface Fatigue:** Results from repeated loading and unloading, causing surface cracks and material removal.
4. **Corrosive Wear:** Involves chemical or electrochemical reactions that degrade material surfaces.
Preventing Wear
Effective wear prevention strategies depend on understanding the specific wear mechanisms involved.
Among the common tactics are choosing appropriate materials, designing for reduced contact stress, and applying protective coatings or treatments.
Basics of Lubrication
Lubrication is the application of a substance (typically a fluid) to reduce friction and wear between two surfaces in relative motion.
Lubricants form a film that separates surfaces, minimizing direct contact and dissipating heat generated by friction.
Types of Lubricants
Lubricants can be classified into several categories, including oils, greases, solid lubricants, and gases.
1. **Oils:** Liquid lubricants, often blended with additives to enhance their properties.
2. **Greases:** Semi-solid lubricants that stick well to surfaces and provide long-lasting protection.
3. **Solid Lubricants:** Used in extreme conditions, such as graphite or molybdenum disulfide.
4. **Gaseous Lubricants:** Like air or other gases used in specialized applications.
Choosing the Right Lubricant
Selecting the appropriate lubricant involves considering factors such as operating conditions, temperature, load, and environmental impact.
Proper lubricant selection is crucial for optimizing performance and extending the life of machinery.
Applications to Wear Improvement Technology
The integration of advanced techniques and materials has led to significant improvements in wear resistance and component durability.
Material Selection
Choosing wear-resistant materials, such as ceramics, hard metals, or composites, can reduce wear and extend the life of components.
These materials are ideal for use in high-wear environments due to their superior hardness and chemical stability.
Surface Treatments
Surface treatments like ion implantation, carburizing, nitriding, and the application of coatings, such as tungsten carbide or diamond-like carbon (DLC), can significantly enhance wear resistance.
These treatments modify surface properties, improving hardness and reducing friction.
Damage Prevention Design
Proactive design strategies can prevent damage and improve the longevity of moving components.
Design Optimization
Effective design involves minimizing stress concentrations and ensuring balanced loads across components.
Finite Element Analysis (FEA) can be used to simulate stress distribution and optimize designs before manufacturing.
Regular Maintenance
Routine maintenance, including inspections and timely replacement of worn parts, is essential for preventing catastrophic failures.
Maintaining optimal lubrication and promptly addressing signs of wear can extend system longevity and efficiency.
Conclusion
Friction, wear, and lubrication are fundamental concepts essential to the design and operation of mechanical systems.
Understanding these forces and applying appropriate technologies can lead to significant improvements in performance and robustness.
By selecting the right materials, employing surface treatments, and optimizing designs, engineers can effectively reduce wear and prevent damage, leading to more reliable and efficient machines.
資料ダウンロード
QCD管理受発注クラウド「newji」は、受発注部門で必要なQCD管理全てを備えた、現場特化型兼クラウド型の今世紀最高の受発注管理システムとなります。
ユーザー登録
受発注業務の効率化だけでなく、システムを導入することで、コスト削減や製品・資材のステータス可視化のほか、属人化していた受発注情報の共有化による内部不正防止や統制にも役立ちます。
NEWJI DX
製造業に特化したデジタルトランスフォーメーション(DX)の実現を目指す請負開発型のコンサルティングサービスです。AI、iPaaS、および先端の技術を駆使して、製造プロセスの効率化、業務効率化、チームワーク強化、コスト削減、品質向上を実現します。このサービスは、製造業の課題を深く理解し、それに対する最適なデジタルソリューションを提供することで、企業が持続的な成長とイノベーションを達成できるようサポートします。
製造業ニュース解説
製造業、主に購買・調達部門にお勤めの方々に向けた情報を配信しております。
新任の方やベテランの方、管理職を対象とした幅広いコンテンツをご用意しております。
お問い合わせ
コストダウンが利益に直結する術だと理解していても、なかなか前に進めることができない状況。そんな時は、newjiのコストダウン自動化機能で大きく利益貢献しよう!
(β版非公開)