- お役立ち記事
- Basics of parts processing methods for designers, points to incorporate into design, and know-how
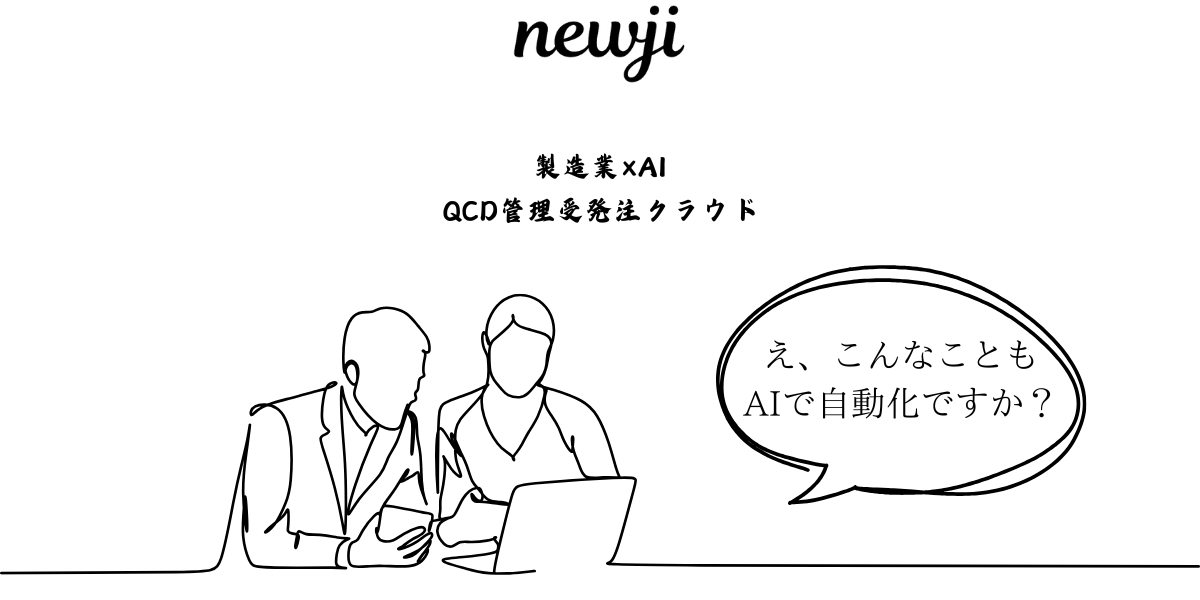
Basics of parts processing methods for designers, points to incorporate into design, and know-how
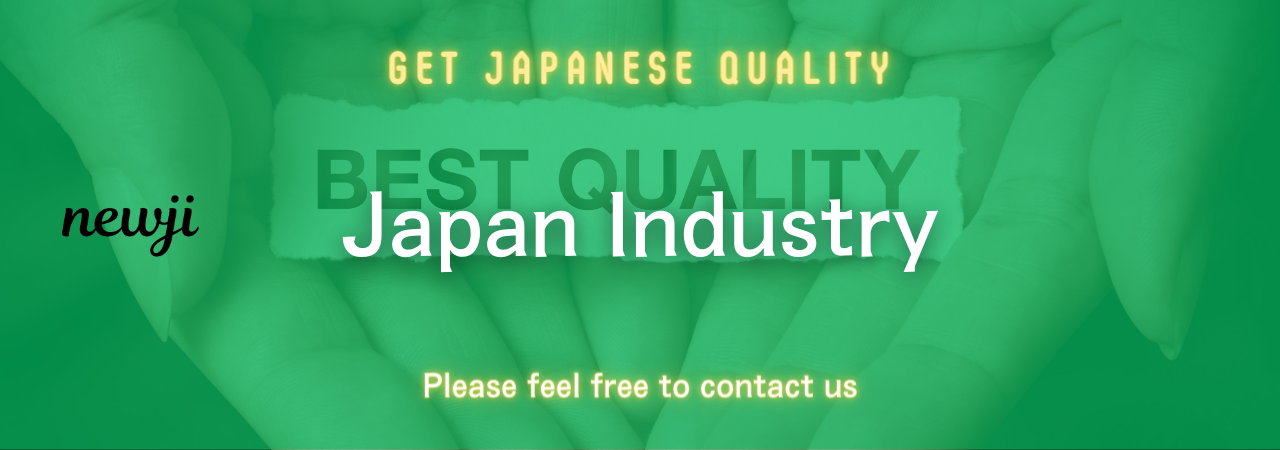
目次
Understanding Parts Processing Methods
Parts processing is a critical aspect of product design and manufacturing.
It is the process of transforming raw materials into final components through various techniques and technologies.
For designers, understanding these methods is essential to create efficient and manufacturable products.
Familiarity with parts processing can guide designers in choosing appropriate materials and designs that meet both aesthetic and functional requirements.
Casting
Casting is a versatile manufacturing process that involves pouring liquid material into a mold, which then solidifies into the desired shape.
This method is widely used for producing complex shapes that would be difficult to achieve with other techniques.
Designers should consider casting for parts that require intricate geometries or need to be produced in large volumes.
Common materials used in casting include metals, plastics, and ceramics.
When incorporating casting into design, it’s vital to think about the mold release, draft angles, and any potential shrinkage of the material as it cools.
These factors affect the final dimensions and quality of the part.
Milling
Milling is a subtractive manufacturing process where a rotating cutting tool removes material from a workpiece to form a desired shape.
It is suitable for creating parts with precise tolerances and smooth finishes.
Materials commonly used in milling include metals, plastics, and wood.
Designers must take into account the cutting paths, tool access, and the stability of the material during milling.
Complex designs might need specialized tools or multiple setups, impacting the overall production time and cost.
3D Printing
3D printing, also known as additive manufacturing, builds parts layer by layer from digital files.
This method provides great flexibility in design and is perfect for prototyping and bespoke pieces.
3D printing can handle a variety of materials like plastics, metals, and composites.
For 3D printing, designers should optimize designs for strength, minimize the need for supports, and consider the layer thickness for the desired surface finish.
Using this approach, designers can quickly iterate and refine their concepts before moving to mass production.
Injection Molding
Injection molding is a popular choice for mass-producing plastic parts.
It involves injecting molten material into a mold where it cools and solidifies.
This process is efficient for high-volume production and achieves tight tolerances and consistent quality.
When designing parts for injection molding, considerations include the choice of plastic, mold design, wall thickness uniformity, and potential warping.
Well-planned designs reduce cycle times and increase the overall efficiency of production.
Points to Incorporate into Design
When designing parts, it is crucial to integrate knowledge of processing methods into the design phase.
Here are some key points to consider:
Material Selection
The choice of material influences the manufacturing process, product durability, cost, and performance.
Designers should evaluate materials based on their physical properties, environmental impact, and compatibility with the chosen processing method.
Design for Manufacturability
A design should be practical for manufacturing.
This involves considering the ease of production, cost-effectiveness, and quality control.
Designers should simplify shapes, avoid unnecessary complexities, and ensure clear tolerance allocations.
Tolerances and Fits
Designers must define the tolerances for each dimension to ensure parts fit and function as intended.
Understanding the capabilities of the chosen processing method helps set realistic tolerances that facilitate smooth assembly and operation.
Know-How for Effective Design
For effective design, blending creativity with technical knowledge is key.
Here are some strategies to enhance design proficiency:
Stay Updated with Technology
Manufacturing technologies are constantly evolving.
Designers should keep abreast of the latest developments in materials, processing techniques, and tools to offer cutting-edge solutions.
Collaboration with Engineers
Designers should work closely with engineers during the design and development phases.
This collaboration ensures that the concept is feasible, meets technical standards, and optimizes the use of resources.
Prototype and Test
Prototyping allows designers to test and validate their designs before full-scale production.
It identifies potential issues and provides an opportunity for refinement, leading to better final products.
Continuous Learning
Ongoing education through courses, workshops, and professional development keeps designers at the forefront of innovation.
Learning from both successes and challenges enhances skills and broadens design capabilities.
By understanding parts processing methods, incorporating key considerations into designs, and applying effective strategies, designers can create innovative and manufacturable products that meet industry standards and consumer expectations.
資料ダウンロード
QCD調達購買管理クラウド「newji」は、調達購買部門で必要なQCD管理全てを備えた、現場特化型兼クラウド型の今世紀最高の購買管理システムとなります。
ユーザー登録
調達購買業務の効率化だけでなく、システムを導入することで、コスト削減や製品・資材のステータス可視化のほか、属人化していた購買情報の共有化による内部不正防止や統制にも役立ちます。
NEWJI DX
製造業に特化したデジタルトランスフォーメーション(DX)の実現を目指す請負開発型のコンサルティングサービスです。AI、iPaaS、および先端の技術を駆使して、製造プロセスの効率化、業務効率化、チームワーク強化、コスト削減、品質向上を実現します。このサービスは、製造業の課題を深く理解し、それに対する最適なデジタルソリューションを提供することで、企業が持続的な成長とイノベーションを達成できるようサポートします。
オンライン講座
製造業、主に購買・調達部門にお勤めの方々に向けた情報を配信しております。
新任の方やベテランの方、管理職を対象とした幅広いコンテンツをご用意しております。
お問い合わせ
コストダウンが利益に直結する術だと理解していても、なかなか前に進めることができない状況。そんな時は、newjiのコストダウン自動化機能で大きく利益貢献しよう!
(Β版非公開)