- お役立ち記事
- Fundamentals of injection molding, causes of molding defects, and preventive measures
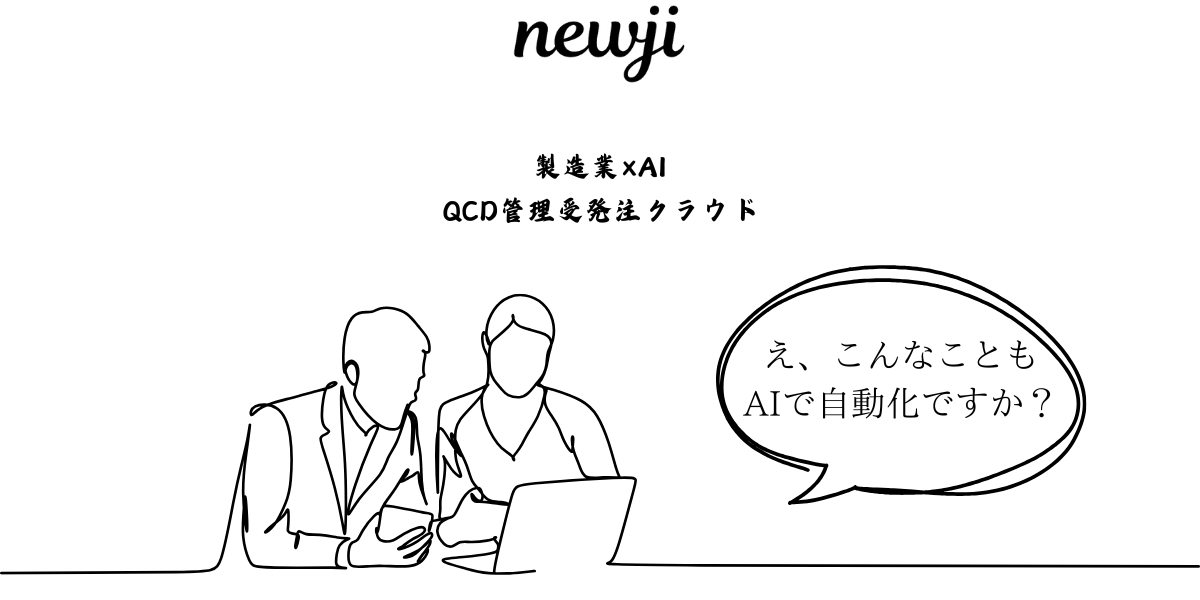
Fundamentals of injection molding, causes of molding defects, and preventive measures
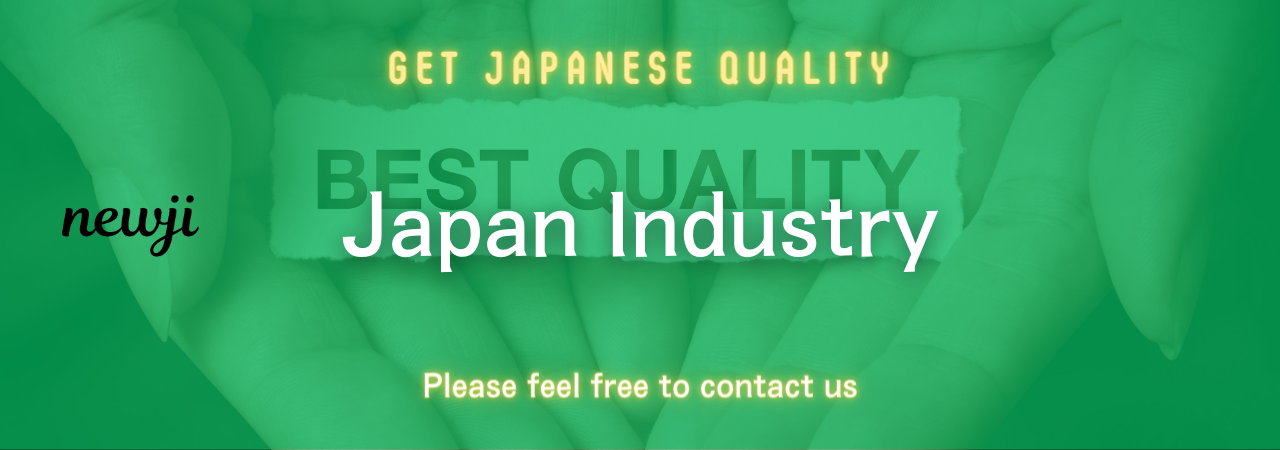
目次
Understanding Injection Molding
Injection molding is a popular manufacturing process used to produce a wide variety of products, from everyday household items to complex parts for automotive and aerospace industries.
This method involves injecting molten material into a mold, which is then cooled and solidified to produce the final object.
The materials commonly used for injection molding include plastics, metals, elastomers, and thermosetting polymers.
One of the main advantages of injection molding is its ability to produce large quantities of identical parts with high precision and at a rapid pace.
This makes it an efficient and cost-effective solution for mass production.
Additionally, the process offers flexibility in material and color choices, allowing for the creation of complex shapes and designs.
Key Components of Injection Molding
To better understand injection molding, it is essential to familiarize oneself with its key components and their functions.
The Mold
The mold is a hollow metal block into which molten material is injected.
It is made of steel or aluminum and consists of two main parts: the cavity and the core.
These parts give the mold its shape and define the final product’s structure.
The Injection Unit
The injection unit is responsible for melting the material and injecting it into the mold.
It includes a hopper for feeding raw material, a reciprocating screw or plunger for melting material, and a nozzle for injecting it into the mold.
The Clamping Unit
The clamping unit holds the mold together during the injection process.
It applies necessary force to keep the mold closed, preventing any leakage of material.
Once the part is cooled and solidified, the clamping unit opens the mold to eject the final product.
Common Causes of Molding Defects
Despite its advantages, injection molding can sometimes result in defects that affect the quality and consistency of the final products.
Identifying the causes of these defects is crucial to developing effective corrective measures.
Material-Related Issues
The quality and properties of the raw material used can significantly impact the molding outcome.
Improper drying of materials, contamination, or incorrect material selection can lead to defects such as voids, bubbles, and weak parts.
Processing Errors
Injection molding involves several stages, including melting, injection, cooling, and ejection.
Issues arising during any of these stages can cause defects.
For example, incorrect temperature settings can lead to incomplete filling or surface blemishes.
Mold Design Flaws
The mold itself can be a source of defects if not designed or maintained properly.
Factors like poor venting, inadequate cooling channels, or sharp corners can result in problems like warping, sink marks, and flash.
Effective Measures to Prevent Defects
While molding defects can be challenging, implementing preventive measures can significantly reduce their occurrence and improve product quality.
Selecting the Right Material
Choosing the appropriate material for your injection molding needs is critical.
Ensure that the material is suitable for the intended application and that it meets the required mechanical and thermal properties.
Proper material handling and storage should also be maintained to prevent contamination.
Optimizing Mold Design
A well-designed mold is fundamental to the success of the injection molding process.
Ensure that the mold design includes proper venting, adequate cooling channels, and smooth transitions to avoid sharp corners.
Regular inspections and maintenance of the mold will also help in prolonging its life and ensuring consistent production quality.
Fine-Tuning the Processing Parameters
Precise control of processing parameters like temperature, injection speed, and pressure is crucial to achieving defect-free products.
Establishing optimal settings for these parameters through trials and simulations can help in minimizing defects.
Using automated systems for monitoring can also enhance consistency and reduce human error.
Regular Machine Maintenance
Regular maintenance of the injection molding machinery ensures proper functioning and reduces the likelihood of defects caused by equipment malfunctions.
This includes cleaning the machine, checking for wear and tear on parts, and calibrating the system as needed.
Conclusion
Injection molding is a highly versatile and efficient manufacturing process used across numerous industries to produce high-quality parts.
However, like any manufacturing process, it is not without its challenges, particularly in preventing defects.
By understanding the fundamentals of injection molding, recognizing the common causes of defects, and implementing preventive measures, manufacturers can optimize their processes and ensure the production of reliable and consistent products.
Continual learning, innovation, and adaptation will further enhance the capabilities and efficiencies of injection molding in the future.
資料ダウンロード
QCD調達購買管理クラウド「newji」は、調達購買部門で必要なQCD管理全てを備えた、現場特化型兼クラウド型の今世紀最高の購買管理システムとなります。
ユーザー登録
調達購買業務の効率化だけでなく、システムを導入することで、コスト削減や製品・資材のステータス可視化のほか、属人化していた購買情報の共有化による内部不正防止や統制にも役立ちます。
NEWJI DX
製造業に特化したデジタルトランスフォーメーション(DX)の実現を目指す請負開発型のコンサルティングサービスです。AI、iPaaS、および先端の技術を駆使して、製造プロセスの効率化、業務効率化、チームワーク強化、コスト削減、品質向上を実現します。このサービスは、製造業の課題を深く理解し、それに対する最適なデジタルソリューションを提供することで、企業が持続的な成長とイノベーションを達成できるようサポートします。
オンライン講座
製造業、主に購買・調達部門にお勤めの方々に向けた情報を配信しております。
新任の方やベテランの方、管理職を対象とした幅広いコンテンツをご用意しております。
お問い合わせ
コストダウンが利益に直結する術だと理解していても、なかなか前に進めることができない状況。そんな時は、newjiのコストダウン自動化機能で大きく利益貢献しよう!
(Β版非公開)