- お役立ち記事
- Basics of seal (gasket/packing) technology, optimal selection, and effective use for leak prevention measures
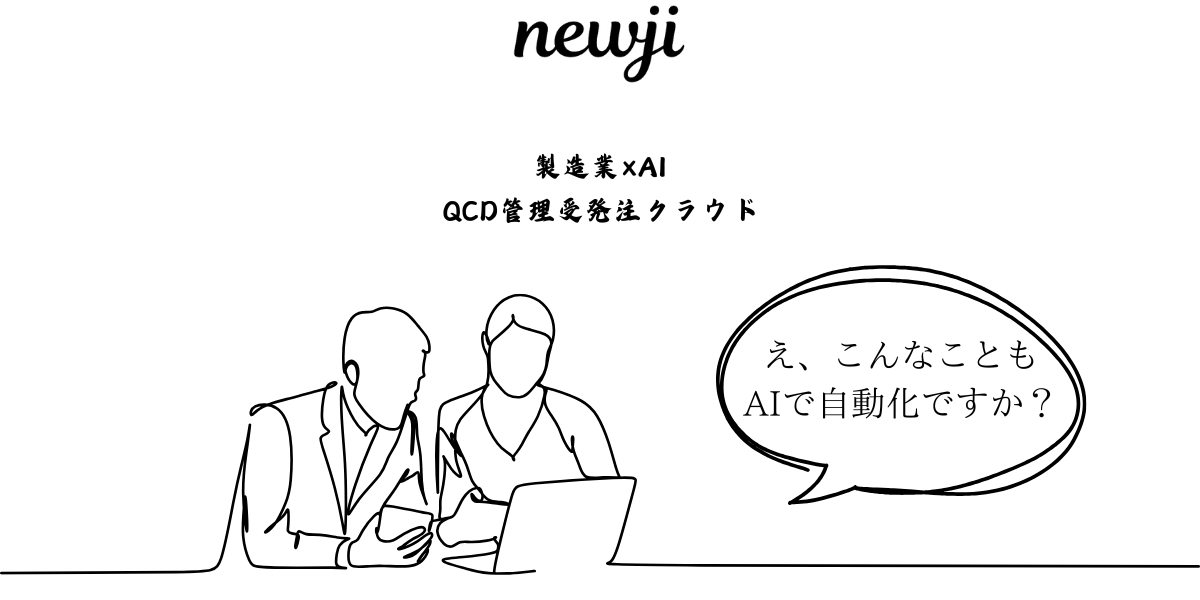
Basics of seal (gasket/packing) technology, optimal selection, and effective use for leak prevention measures
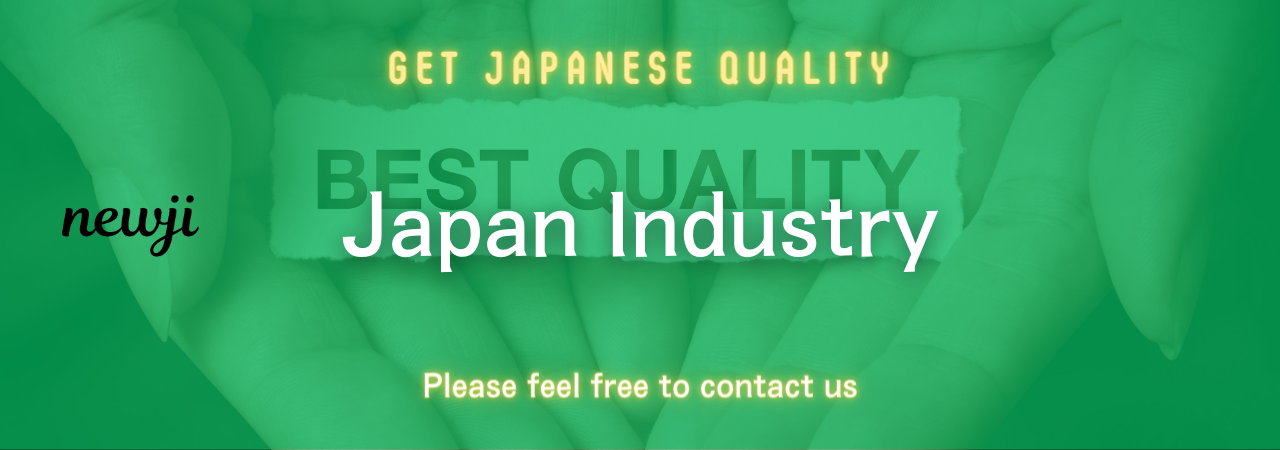
目次
Understanding Seal Technology
When discussing seal technology, it’s essential to first understand what seals and gaskets are.
Seals, also known as gaskets or packings, are crucial components designed to prevent leaks in a variety of applications.
Typically made from flexible materials, they form a tight barrier between two surfaces, effectively sealing any potential gaps.
This is particularly important in industries where fluid or gas leakage can have significant safety and operational repercussions.
Seals come in many different shapes and sizes, each tailored for specific functions and materials.
From rubber O-rings to metallic gaskets, the variety ensures compatibility with a wide range of industrial applications.
O-rings, for example, are small, circular seals commonly used in hydraulic and pneumatic systems.
They are prized for their simplicity and effectiveness in preventing leaks at minimal cost.
Choosing the Right Seal
Selecting the right seal is crucial to the effectiveness of the sealing process.
This decision is influenced by several factors, including the operational environment, material compatibility, and the type of fluid or gas being sealed.
Operational Environment
The environment in which a seal operates is a significant consideration.
Factors like temperature, pressure, and the presence of chemicals can impact a seal’s performance.
For instance, seals used in high-temperature environments require materials resistant to heat degradation.
In contrast, those used in areas with chemical exposure might require chemically resistant materials to prevent deterioration.
When selecting a seal, it’s important to ensure it can withstand the specific environmental challenges it will face.
This will help maintain its integrity and effectiveness over time, minimizing the risk of leakage.
Material Compatibility
Material compatibility is another critical factor in seal selection.
The seal material must be compatible with the surfaces it contacts and the fluid or gas it seals.
Incompatible materials can result in premature seal failure due to chemical reactions or physical stress.
Rubber seals, for example, may work well with water but could be inappropriate for sealing petroleum products due to potential swelling.
In such cases, a more suitable material like Viton might be chosen for its resistance to oil and fuels.
Type of Fluid or Gas
The specific fluid or gas being sealed also influences seal selection.
Different materials react differently to different substances, influencing their performance and longevity.
For example, a seal designed for use with gases may not perform well with liquids due to differences in physical properties.
Understanding the nature of the fluid or gas, whether it is corrosive, flammable, or inert, guides the choice of a suitable seal.
Correct identification ensures the seal can effectively contain the substance without compromising safety or reliability.
Effective Use of Seals
Once the appropriate seal is selected, proper installation and maintenance are vital to ensuring leak prevention.
Even the best-sealed materials can fail if installed incorrectly or if maintenance is neglected.
Installation Best Practices
Proper installation is key to the effective functioning of seals.
This typically involves ensuring the sealing surface is clean, smooth, and free of debris.
Any irregularities can prevent a tight seal, leading to potential leaks.
It’s also important to follow specific installation procedures for each type of seal.
For instance, O-rings should be lubricated before installation to reduce friction and ensure a tight fit.
On the other hand, gaskets may require specific torque settings to prevent over-compression or under-compression.
By adhering to these best practices, you can extend the life of the seal and improve its performance.
Regular Maintenance
Maintenance plays a crucial role in the longevity and reliability of seals.
Regular inspections can help identify potential issues before they lead to leaks.
Checking for signs of wear, such as cracks, deformation, or hardening, can prevent unnecessary damage.
Routine maintenance also involves replacing seals at regular intervals, even if they do not show visible signs of wear.
This precautionary measure ensures that the sealing system remains in top condition and continues to operate effectively.
Benefits of Using Seals
The use of seals in industrial applications offers multiple benefits, including enhanced safety, operational efficiency, and reduced environmental impact.
Enhanced Safety
Seals play a crucial role in enhancing safety by preventing leaks of hazardous materials.
In industries such as chemical manufacturing or oil and gas, even a small leak can pose significant health and safety risks.
By effectively containing these substances, seals help mitigate potential hazards.
Operational Efficiency
Leaks, even minor ones, can lead to wastage and operational inefficiencies.
By ensuring that fluids and gases remain contained within systems, seals contribute to smoother operations and reduced resource wastage.
This efficiency translates into cost savings and enhanced productivity for businesses.
Reduced Environmental Impact
Seals help minimize the environmental impact by preventing leaks of pollutants into the environment.
In sectors where environmentally harmful substances are handled, effective sealing minimizes the risk of contamination, supporting sustainability efforts.
Conclusion
Seal technology, encompassing gaskets and packings, is a critical component in preventing leaks across various industries.
Selecting the right seal, based on factors like the operational environment, material compatibility, and fluid type, ensures optimal performance.
Coupled with proper installation and regular maintenance, seals not only enhance safety and operational efficiency but also help reduce environmental impacts.
Understanding the basics of seal technology and its applications can play a pivotal role in achieving leak-free and efficient industrial processes.
資料ダウンロード
QCD調達購買管理クラウド「newji」は、調達購買部門で必要なQCD管理全てを備えた、現場特化型兼クラウド型の今世紀最高の購買管理システムとなります。
ユーザー登録
調達購買業務の効率化だけでなく、システムを導入することで、コスト削減や製品・資材のステータス可視化のほか、属人化していた購買情報の共有化による内部不正防止や統制にも役立ちます。
NEWJI DX
製造業に特化したデジタルトランスフォーメーション(DX)の実現を目指す請負開発型のコンサルティングサービスです。AI、iPaaS、および先端の技術を駆使して、製造プロセスの効率化、業務効率化、チームワーク強化、コスト削減、品質向上を実現します。このサービスは、製造業の課題を深く理解し、それに対する最適なデジタルソリューションを提供することで、企業が持続的な成長とイノベーションを達成できるようサポートします。
オンライン講座
製造業、主に購買・調達部門にお勤めの方々に向けた情報を配信しております。
新任の方やベテランの方、管理職を対象とした幅広いコンテンツをご用意しております。
お問い合わせ
コストダウンが利益に直結する術だと理解していても、なかなか前に進めることができない状況。そんな時は、newjiのコストダウン自動化機能で大きく利益貢献しよう!
(Β版非公開)