- お役立ち記事
- Basics and points of use of “vibration mode analysis” necessary for noise and vibration countermeasures
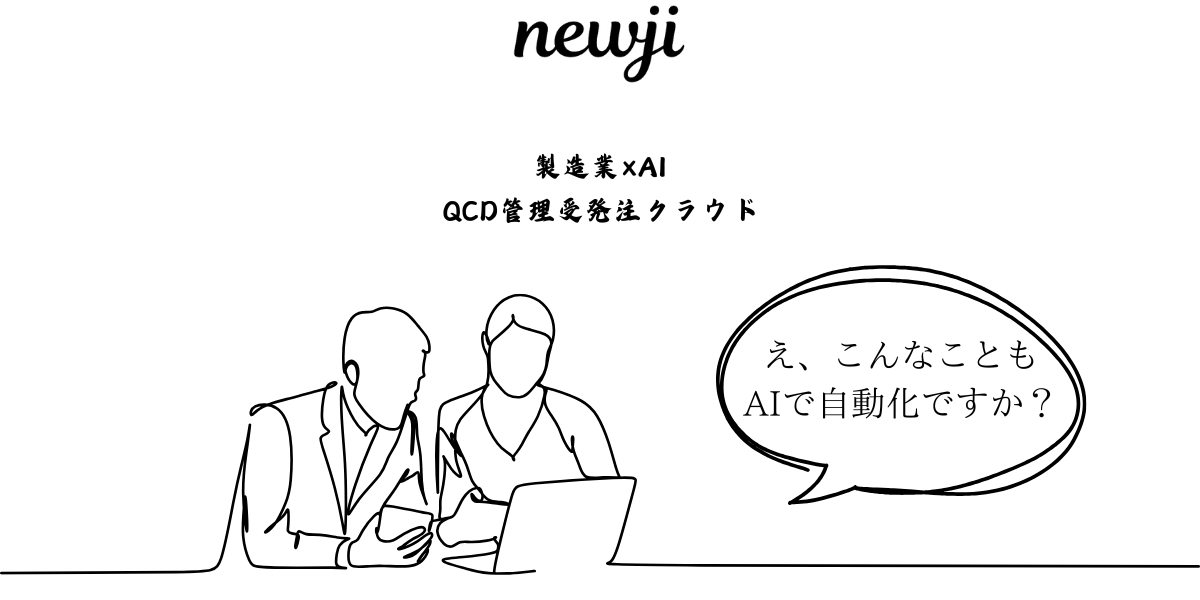
Basics and points of use of “vibration mode analysis” necessary for noise and vibration countermeasures
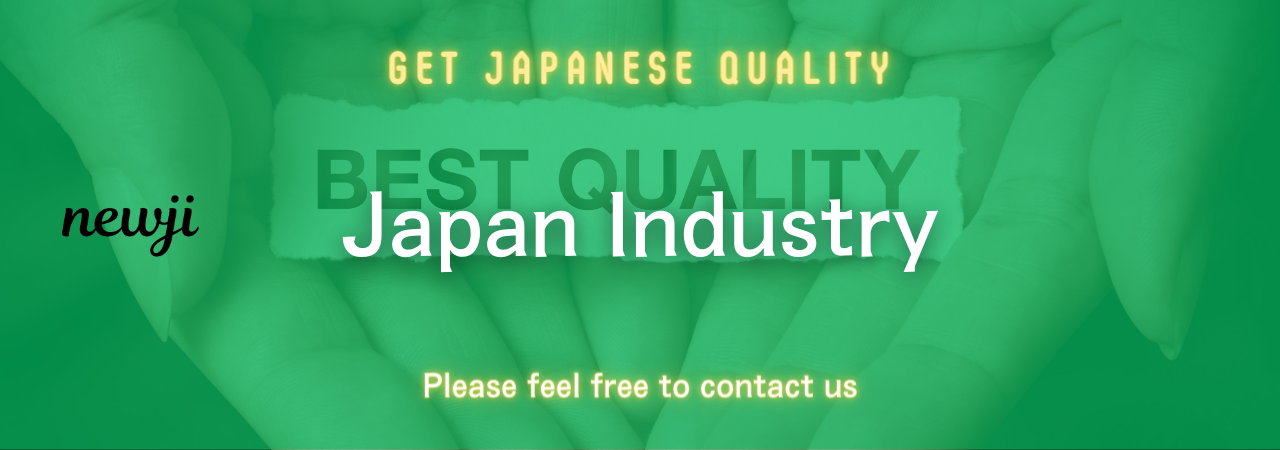
目次
Understanding Vibration Mode Analysis
Vibration mode analysis is a key technique used in engineering to study the vibrations in structures and mechanical systems.
By examining these vibrations, engineers can predict the behavior of a system under various conditions and identify potential issues related to noise and vibrations.
Understanding this process is crucial for designing quieter, more efficient, and more comfortable machines and structures.
What is Vibration Mode Analysis?
Vibration mode analysis, also known as modal analysis, is a method used to determine the natural frequencies, mode shapes, and damping characteristics of a structure.
Natural frequencies are specific frequencies at which a system tends to oscillate with larger amplitude when excited by an external force.
These frequencies are important because when a system is subjected to vibrations at its natural frequency, resonance occurs, potentially leading to increased vibrations and even structural failure.
Mode shapes describe the pattern of vibration that a structure undergoes at a particular natural frequency.
Each mode shape represents a specific way in which the structure deforms and vibrates.
Damping characteristics refer to the dissipative properties of the structure, which affect how quickly vibrations decrease in amplitude over time.
Importance of Vibration Mode Analysis
Vibration mode analysis is essential in designing and optimizing mechanical systems and structures for several reasons:
1. **Noise Reduction**:
By identifying and addressing specific mode shapes that contribute to noise, engineers can implement changes to reduce unwanted sounds.
This is especially significant in industries like automotive, aerospace, and consumer electronics, where noise reduction is a key design consideration.
2. **Vibration Control**:
Controlling vibrations is crucial for the longevity and safety of structures and machines.
Understanding the mode shapes and natural frequencies helps in designing solutions to mitigate excessive vibrations, enhancing system reliability and performance.
3. **Structural Health Monitoring**:
Vibration mode analysis can be used to monitor the health of structures by observing changes in their vibrational characteristics over time.
This approach helps in early detection of faults or damages, allowing for timely maintenance and preventing catastrophic failures.
4. **Design Optimization**:
Engineers use vibration mode analysis to optimize the design of components by minimizing vibrations, increasing fatigue life, and ensuring that structures meet their intended performance without overdesign.
Steps in Vibration Mode Analysis
Performing a vibration mode analysis involves several critical steps:
1. System Modeling
The first step in vibration mode analysis involves creating a mathematical model of the structure or system under study.
This model represents the physical parameters such as mass, stiffness, and damping, which affect the vibrational behavior.
2. Frequency Analysis
Once the model is set, engineers conduct a frequency analysis to determine the natural frequencies of the system.
This can be done using analytical methods for simple structures or through numerical techniques like finite element analysis (FEA) for complex systems.
3. Identifying Mode Shapes
After determining the natural frequencies, the next step is to identify the mode shapes associated with each frequency.
Mode shapes are often visualized using computer software to help engineers understand how different parts of the structure will vibrate.
4. Damping Analysis
In this step, engineers analyze the damping characteristics of the system to quantify how vibrations are reduced over time.
Damping is crucial because it helps prevent resonance from causing excessive vibrations and possible damage to the structure.
Tools and Techniques
There are several tools and techniques used in vibration mode analysis:
– **Analytical Methods**: These methods use mathematical equations to describe the vibrational behavior of simple systems.
They are often used for preliminary analysis and understanding basic concepts.
– **Experimental Modal Analysis (EMA)**: This technique involves physically testing a structure and measuring its response to vibrations.
Using sensors and actuators, engineers can capture data that is then analyzed to identify the natural frequencies and mode shapes.
– **Finite Element Analysis (FEA)**: For complex systems, FEA is a powerful numerical tool used to simulate the vibrational behavior.
It involves breaking down the structure into smaller elements and applying numerical methods to solve for the vibrational characteristics.
Applications in Noise and Vibration Mitigation
Vibration mode analysis plays a vital role in noise and vibration mitigation across various fields:
Automotive Industry
In the automotive industry, vibration mode analysis is used to design quieter and smoother-operating vehicles.
By analyzing the vibrational behavior of components like engines, suspensions, and body panels, engineers can make adjustments to reduce road noise and enhance ride comfort.
Aerospace Engineering
Aircraft are subjected to a wide range of vibrational frequencies during flight.
Vibration mode analysis helps in designing aircraft structures that can withstand these vibrations, ensuring passenger comfort and structural integrity.
Consumer Electronics
In consumer electronics, such as smartphones and laptops, vibration mode analysis is used to minimize unwanted vibrations that may affect device performance.
This is especially important in devices with moving parts, like hard drives or cooling fans.
Conclusion
Vibration mode analysis is a critical tool in the engineering toolkit for addressing noise and vibration challenges.
By understanding the natural frequencies, mode shapes, and damping characteristics of a system, engineers can design solutions that enhance performance, reduce noise, and improve the safety and reliability of structures and mechanical systems.
Through continued advancements in analytical and numerical methods, vibration mode analysis will remain at the forefront of innovation across various industries.
資料ダウンロード
QCD調達購買管理クラウド「newji」は、調達購買部門で必要なQCD管理全てを備えた、現場特化型兼クラウド型の今世紀最高の購買管理システムとなります。
ユーザー登録
調達購買業務の効率化だけでなく、システムを導入することで、コスト削減や製品・資材のステータス可視化のほか、属人化していた購買情報の共有化による内部不正防止や統制にも役立ちます。
NEWJI DX
製造業に特化したデジタルトランスフォーメーション(DX)の実現を目指す請負開発型のコンサルティングサービスです。AI、iPaaS、および先端の技術を駆使して、製造プロセスの効率化、業務効率化、チームワーク強化、コスト削減、品質向上を実現します。このサービスは、製造業の課題を深く理解し、それに対する最適なデジタルソリューションを提供することで、企業が持続的な成長とイノベーションを達成できるようサポートします。
オンライン講座
製造業、主に購買・調達部門にお勤めの方々に向けた情報を配信しております。
新任の方やベテランの方、管理職を対象とした幅広いコンテンツをご用意しております。
お問い合わせ
コストダウンが利益に直結する術だと理解していても、なかなか前に進めることができない状況。そんな時は、newjiのコストダウン自動化機能で大きく利益貢献しよう!
(Β版非公開)