- お役立ち記事
- Fundamentals of laser welding and laser processing technology and applications to joining dissimilar metals and materials
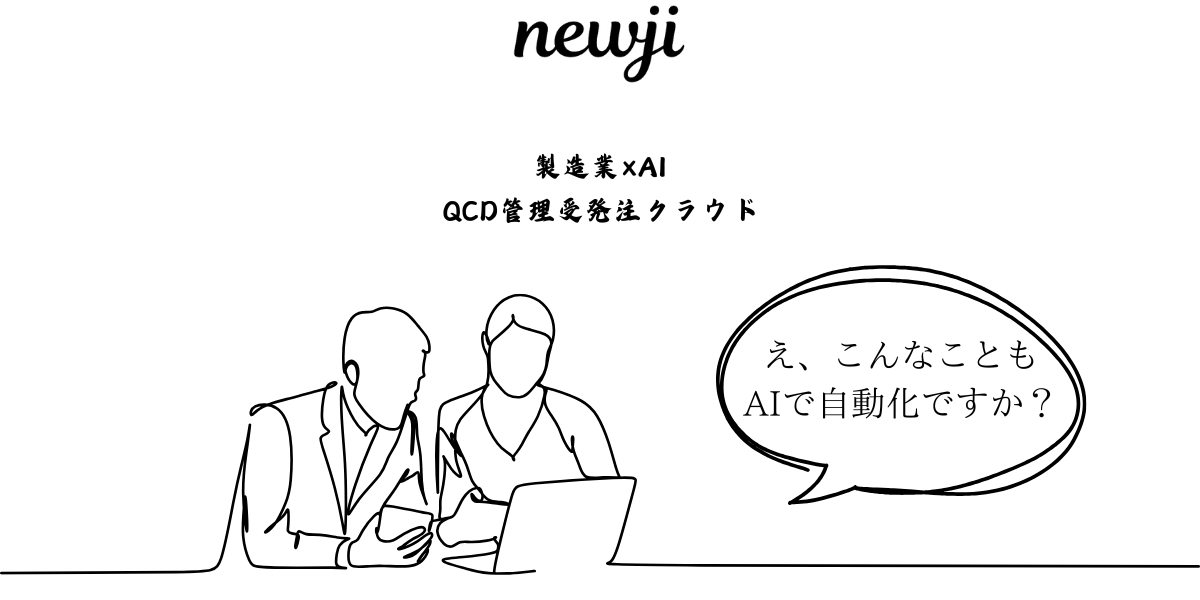
Fundamentals of laser welding and laser processing technology and applications to joining dissimilar metals and materials
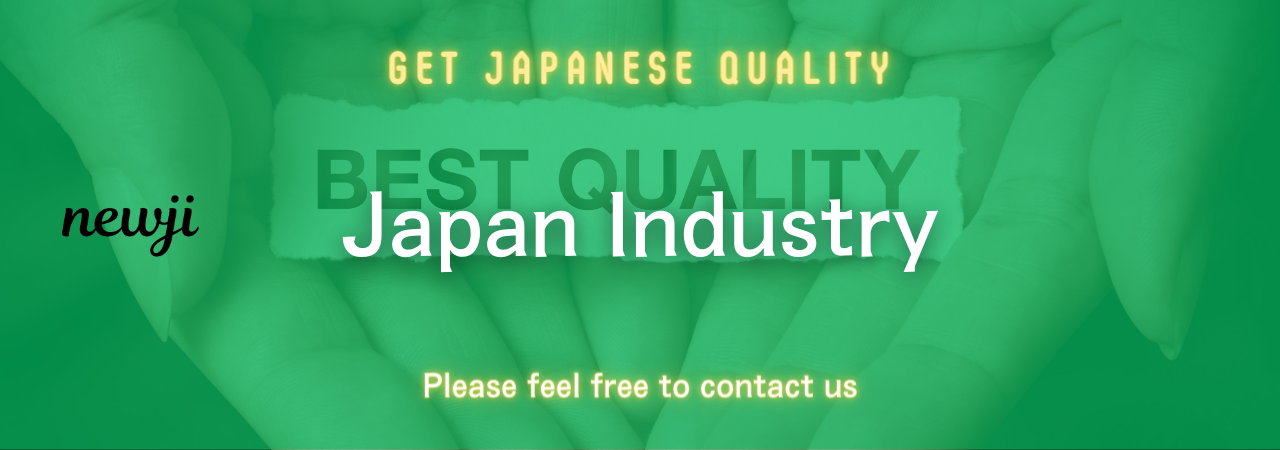
目次
Introduction to Laser Welding and Processing Technology
Laser welding and processing technology is transforming the landscape of manufacturing and production industries.
This advanced technique utilizes a concentrated beam of light to join materials, making it a powerful tool for precision and efficiency.
Over the years, laser technology has expanded its reach into numerous sectors, offering innovative solutions to complex manufacturing challenges.
Understanding the Basics of Laser Welding
At its core, laser welding involves using a concentrated beam of light to melt and join two pieces of material.
The laser produces a high-energy light beam that is focused onto a small spot.
This precision allows for deep penetration with minimal heat distortion, making it ideal for applications where accuracy is paramount.
Laser welding is highly versatile and can be adapted to various materials, including metals, plastics, and composites.
The process is well-suited for both thin and thick materials, providing strong welds with minimal distortion.
Additionally, laser welding is often employed in high-speed operations, enhancing productivity and reducing costs.
Types of Lasers Used in Welding
There are several types of lasers used in welding, with the most common being CO2 lasers, fiber lasers, and Nd:YAG lasers.
**CO2 Lasers:**
CO2 lasers are widely used in laser welding due to their ability to deliver high power output.
They are particularly effective for welding non-metallic materials and metals with high thermal conductivity.
**Fiber Lasers:**
Fiber lasers are known for their versatility and efficiency.
They offer high beam quality and are ideal for welding a wide range of materials.
Due to their compact design, fiber lasers are often used in automated welding systems, allowing for precise control and flexibility.
**Nd:YAG Lasers:**
Nd:YAG lasers are used for their ability to deliver high peak power in pulsed mode.
They are suitable for spot welding and are commonly used in industries where detailed precision is required, such as electronics and medical device manufacturing.
Applications of Laser Welding in Manufacturing
Laser welding technology has revolutionized the manufacturing industry, offering significant advantages across various sectors.
Automotive Industry
In the automotive industry, laser welding is extensively used for producing components like car body assemblies, engine parts, and transmission systems.
The precision and speed of laser welding make it an ideal process for mass production, reducing costs while improving product quality.
The technique is also employed in the fabrication of lightweight structures, contributing to improved fuel efficiency and performance.
Electronics Industry
The electronics industry benefits greatly from laser welding’s precision capabilities.
It is used to join delicate electronic components with minimal thermal distortion, ensuring the integrity and performance of the final product.
Laser welding is also essential in the production of micro-electronic devices where detailed accuracy is crucial.
Aerospace Industry
In the aerospace sector, laser welding is employed for its ability to create lightweight, high-strength joints.
Components in aircraft, such as turbine blades and structural assemblies, are often manufactured using laser welding techniques.
This ensures reliability and safety, which are paramount in aerospace applications.
Medical Device Manufacturing
Laser welding plays a critical role in the manufacturing of medical devices due to its clean and precise technique.
It is used to create strong seals on medical equipment, including surgical instruments and implantable devices.
The process ensures that devices meet the stringent safety and hygiene standards required in the healthcare industry.
Joining Dissimilar Metals and Materials
One of the key advantages of laser welding is its ability to join dissimilar metals and materials.
Traditional welding methods often struggle with this, as different materials have varying thermal conductivity and expansion rates.
Laser welding overcomes these challenges by providing precise control over heat input.
Challenges and Solutions
Joining dissimilar metals can present challenges, such as the formation of brittle intermetallic compounds.
By controlling the energy input and optimizing the weld pool shaping, laser welding minimizes these risks.
Advanced techniques, such as beam oscillation and tailored pulse profiles, are employed to improve joint quality and minimize defects.
Applications in Industry
The ability to join dissimilar materials opens up new possibilities in industries like automotive, electronics, and aerospace.
For example, laser welding allows for the combination of lightweight materials with high-strength alloys, resulting in components that are both durable and efficient.
This capability is crucial for producing innovative products that meet modern design and performance demands.
The Future of Laser Welding and Processing Technology
As technology continues to advance, the future of laser welding and processing technology looks promising.
Ongoing research and development are set to unlock even more applications and opportunities for innovation.
Advancements in Automation
Automation is playing a significant role in enhancing laser welding processes.
Robotic systems equipped with lasers are improving production efficiency and reducing human error.
These advancements enable consistent, high-quality welds, which are especially valuable in mass production environments.
New Material Combinations
Research into new material combinations is expanding the potential applications for laser welding.
As industries seek to develop stronger and lighter products, laser technology will be at the forefront of enabling these breakthroughs.
Environmental Impact
Laser welding offers an environmentally friendly alternative compared to traditional methods.
It reduces energy consumption and waste, making it an essential component in sustainable manufacturing practices.
Conclusion
Laser welding and processing technology is a cornerstone of modern manufacturing.
Its ability to join a wide range of materials with precision and efficiency makes it indispensable across various industries.
As innovation continues to drive this technology forward, its applications will only expand, offering exciting possibilities for the future.
資料ダウンロード
QCD調達購買管理クラウド「newji」は、調達購買部門で必要なQCD管理全てを備えた、現場特化型兼クラウド型の今世紀最高の購買管理システムとなります。
ユーザー登録
調達購買業務の効率化だけでなく、システムを導入することで、コスト削減や製品・資材のステータス可視化のほか、属人化していた購買情報の共有化による内部不正防止や統制にも役立ちます。
NEWJI DX
製造業に特化したデジタルトランスフォーメーション(DX)の実現を目指す請負開発型のコンサルティングサービスです。AI、iPaaS、および先端の技術を駆使して、製造プロセスの効率化、業務効率化、チームワーク強化、コスト削減、品質向上を実現します。このサービスは、製造業の課題を深く理解し、それに対する最適なデジタルソリューションを提供することで、企業が持続的な成長とイノベーションを達成できるようサポートします。
オンライン講座
製造業、主に購買・調達部門にお勤めの方々に向けた情報を配信しております。
新任の方やベテランの方、管理職を対象とした幅広いコンテンツをご用意しております。
お問い合わせ
コストダウンが利益に直結する術だと理解していても、なかなか前に進めることができない状況。そんな時は、newjiのコストダウン自動化機能で大きく利益貢献しよう!
(Β版非公開)