- お役立ち記事
- Fundamentals of stress and strain for mechanical designers and applications to strength design
Fundamentals of stress and strain for mechanical designers and applications to strength design
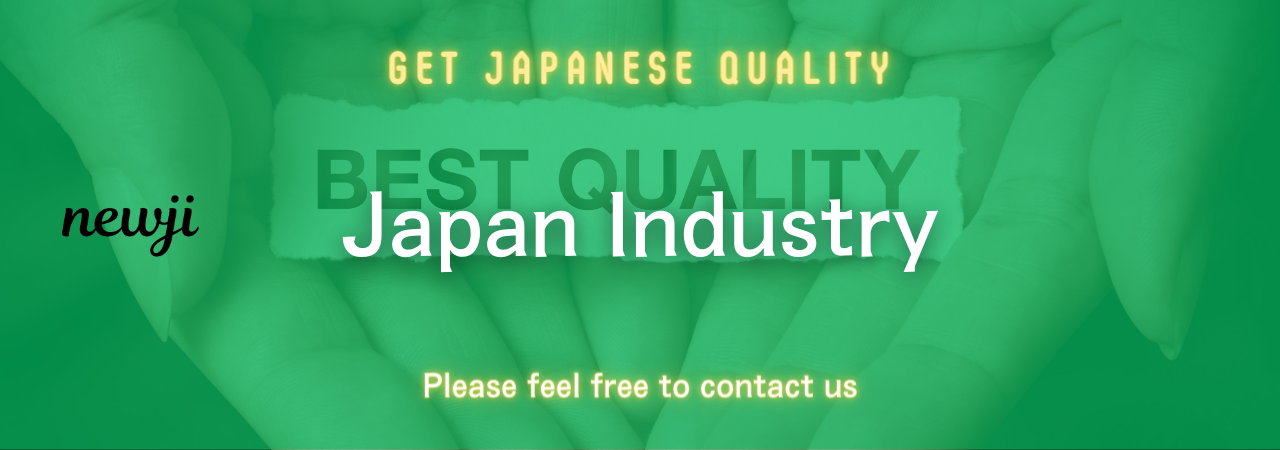
目次
Understanding Stress and Strain
Stress and strain are fundamental concepts in mechanical engineering and design that provide insights into how materials behave under various forces.
When a load is applied to an object, it experiences internal forces that lead to deformation.
This deformation is what we refer to as strain, while the internal forces experienced by the material are described as stress.
Mechanical designers must have a solid grasp of these concepts to ensure structures and components are safe and reliable.
What is Stress?
Stress is defined as the force applied per unit area within materials.
It arises when external loads act upon a material, causing internal resistance to the load.
The formula to calculate stress is given by:
\[ \sigma = \frac{F}{A} \]
where:
– \( \sigma \) is stress,
– \( F \) is the force applied,
– \( A \) is the cross-sectional area.
Stress is typically measured in units of Pascals (Pa) or pounds per square inch (psi).
There are different types of stress depending on how the force is applied:
1. **Tensile Stress**: Occurs when a material is subjected to a pulling or stretching force.
2. **Compressive Stress**: Occurs when a material is subjected to a pushing or squashing force.
3. **Shear Stress**: Occurs when forces are applied parallel to the surface, causing layers to slide over one another.
Understanding these types of stress is crucial for mechanical designers when selecting materials and designing components that will withstand the intended loads.
Understanding Strain
Strain, on the other hand, refers to the deformation or change in shape that a material experiences due to stress.
It is a dimensionless quantity, defined as the ratio of the change in dimension to the original dimension:
\[ \epsilon = \frac{\Delta L}{L_0} \]
where:
– \( \epsilon \) is strain,
– \( \Delta L \) is the change in length,
– \( L_0 \) is the original length.
Like stress, strain can be categorized based on the type of force causing the deformation:
1. **Tensile Strain**: Occurs when a material elongates under tensile stress.
2. **Compressive Strain**: Occurs when a material shortens due to compressive stress.
3. **Shear Strain**: Occurs when a material experiences angular deformation due to shear stress.
Grasping the relationship between stress and strain helps mechanical designers predict how materials will respond to different forces in real-world applications.
The Stress-Strain Relationship
The stress-strain curve is a fundamental tool used by mechanical designers to understand material behavior under load.
This curve is plotted by applying varying levels of stress to a material and measuring the resulting strain.
Elastic Region
In the initial stage of the stress-strain curve, materials typically exhibit elastic behavior.
During this phase, materials return to their original shape once the applied stress is removed.
The stress-strain relationship in this region is linear, and the slope of this linear portion is known as the modulus of elasticity, or Young’s modulus.
Young’s modulus is a critical factor in material selection and design, representing the material’s stiffness.
Materials with a high Young’s modulus are relatively stiff and resist deformation.
Plastic Region
As stress increases beyond the elastic limit, materials enter the plastic region.
In this region, permanent deformation occurs, and materials do not return to their original shape after unloading.
Designers must be aware of this transition to prevent structural failure in applications where only reversible deformation is acceptable.
Ultimate Tensile Strength and Fracture
The highest point on the stress-strain curve represents the ultimate tensile strength (UTS) of the material.
Beyond this point, the material can undergo necking and eventually fracture.
Understanding UTS is vital for designers to ensure that components have adequate strength to withstand maximum expected loads without failure.
Applications to Strength Design
Applying stress and strain principles is crucial in the design and analysis of various mechanical components.
Material Selection
Choosing the right material is a fundamental aspect of mechanical design.
By understanding the stress-strain behavior, designers can select materials with appropriate properties such as strength, ductility, and toughness.
Different applications require specific material characteristics, such as lightweight materials for aerospace or high-strength alloys for construction.
Safety Factor
In engineering practice, a safety factor is often applied to account for uncertainties in material properties, loading conditions, and environmental factors.
It ensures that even under unforeseen circumstances, the designed component remains safe and functional.
Calculating an appropriate safety factor involves considering the maximum load the component might experience and its material strength.
Fatigue and Cyclic Loading
Many components, such as bridges, vehicles, and machinery, experience repeated loading and unloading cycles over time.
This can lead to fatigue, resulting in failure at stress levels below the ultimate tensile strength.
Designers must analyze stress distribution and material endurance limits to mitigate fatigue and enhance component life.
Finite Element Analysis (FEA)
Finite Element Analysis is a powerful computational tool used by mechanical designers to simulate and analyze stress and strain in complex geometries and loading conditions.
FEA helps understand stress concentrations, distribution, and potential failure points, allowing for optimization and design refinement.
Conclusion
The fundamentals of stress and strain are essential for mechanical designers to ensure their designs are both effective and safe.
By understanding these concepts, selecting appropriate materials, and applying adequate design principles, engineers can create structures and components that perform reliably under various conditions.
Stress and strain analysis forms the backbone of engineering design, guiding decisions that impact the longevity and safety of everything from consumer products to critical infrastructure.
資料ダウンロード
QCD調達購買管理クラウド「newji」は、調達購買部門で必要なQCD管理全てを備えた、現場特化型兼クラウド型の今世紀最高の購買管理システムとなります。
ユーザー登録
調達購買業務の効率化だけでなく、システムを導入することで、コスト削減や製品・資材のステータス可視化のほか、属人化していた購買情報の共有化による内部不正防止や統制にも役立ちます。
NEWJI DX
製造業に特化したデジタルトランスフォーメーション(DX)の実現を目指す請負開発型のコンサルティングサービスです。AI、iPaaS、および先端の技術を駆使して、製造プロセスの効率化、業務効率化、チームワーク強化、コスト削減、品質向上を実現します。このサービスは、製造業の課題を深く理解し、それに対する最適なデジタルソリューションを提供することで、企業が持続的な成長とイノベーションを達成できるようサポートします。
オンライン講座
製造業、主に購買・調達部門にお勤めの方々に向けた情報を配信しております。
新任の方やベテランの方、管理職を対象とした幅広いコンテンツをご用意しております。
お問い合わせ
コストダウンが利益に直結する術だと理解していても、なかなか前に進めることができない状況。そんな時は、newjiのコストダウン自動化機能で大きく利益貢献しよう!
(Β版非公開)