- お役立ち記事
- Computational fluid analysis and fluid-structure interaction analysis using finite volume method
Computational fluid analysis and fluid-structure interaction analysis using finite volume method
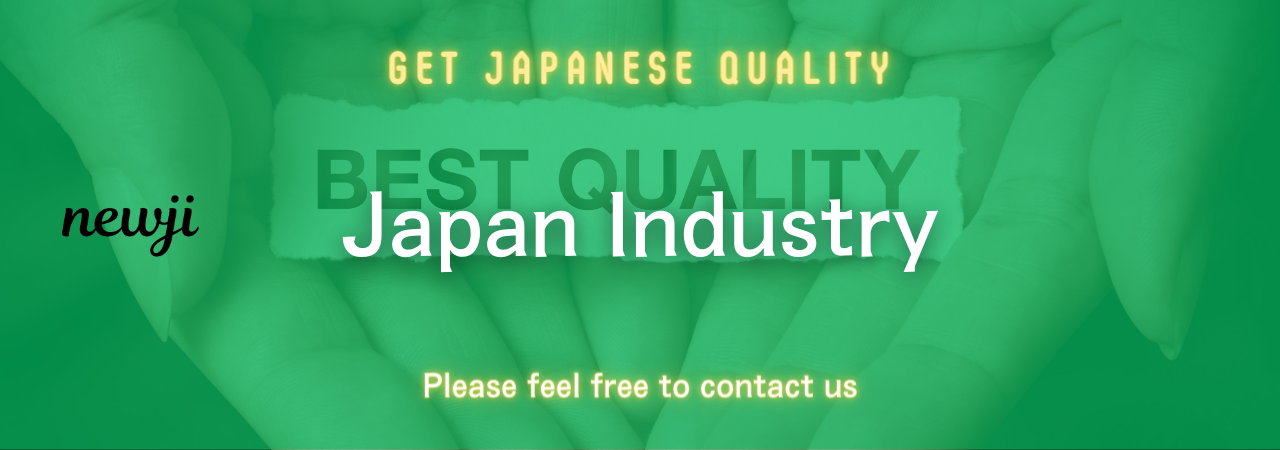
目次
Understanding Computational Fluid Analysis
Computational fluid analysis is a critical tool in engineering that helps us understand how fluids behave in various environments.
By simulating fluid flow using computer software, engineers and researchers can predict how gases or liquids will react under different conditions.
This type of analysis is fundamental in industries such as aerospace, automotive, and energy, where fluid dynamics play a crucial role.
The finite volume method is a widely used approach in computational fluid dynamics (CFD).
It involves dividing a physical domain into a finite number of small volumes.
The equations governing fluid flow are then solved over these small volumes, allowing for detailed modeling of complex fluid behavior.
The Role of Fluid-Structure Interaction Analysis
Fluid-structure interaction (FSI) analysis extends the capabilities of computational fluid analysis by considering how fluids interact with solid structures.
This interaction can have significant effects on the performance and safety of engineering systems.
For example, in the design of an aircraft wing, engineers must consider how the air currents flowing around the wing will affect its structural integrity.
FSI analysis combines the principles of fluid dynamics and structural mechanics.
By integrating these disciplines, engineers can predict how a structure will respond to fluid forces over time.
This type of analysis is essential for optimizing designs and ensuring that structures can withstand the stresses they encounter during operation.
The Benefits of Using the Finite Volume Method
The finite volume method offers several advantages for computational fluid and FSI analyses.
Firstly, it is highly adaptable to irregular geometries, making it suitable for complex shapes that are often encountered in real-world applications.
This flexibility enables engineers to model detailed and accurate representations of the systems they are studying.
Additionally, the finite volume method is conservation-oriented.
This means it inherently respects the conservation laws of mass, momentum, and energy, which are fundamental principles in fluid dynamics.
The method’s conservation properties ensure that the analyses are physically realistic and reliable.
Applications in Various Industries
Computational fluid and FSI analyses using the finite volume method have a wide range of applications across multiple industries.
In the automotive industry, these analyses help improve vehicle aerodynamics, enhancing fuel efficiency and stability.
Engineers can simulate airflow around vehicles to identify areas of high drag and design solutions to minimize it.
In aerospace, CFD and FSI analyses are crucial for designing safe and efficient aircraft.
They help ensure that planes can handle the aerodynamic forces encountered during flight.
These analyses also contribute to the development of more energy-efficient engines by optimizing air intake and exhaust flow.
The energy sector also benefits from these analyses, particularly in the design of wind turbines and hydraulic machinery.
By understanding how fluids move and interact with structures, companies can create more efficient and durable energy solutions.
Challenges in Computational Fluid and FSI Analyses
Despite their numerous advantages, computational fluid and FSI analyses come with their own set of challenges.
One of the primary challenges is that these simulations can be computationally intensive.
The complexity of the models requires significant computational resources, which can be costly and time-consuming.
Another challenge is ensuring the accuracy of the models.
CFD and FSI analyses rely on complex mathematical equations and assumptions, which need to be meticulously validated against experimental data.
This process can be elaborate and requires expertise to ensure that the models provide reliable results.
Future Developments in the Field
The field of computational fluid dynamics and fluid-structure interaction is constantly evolving.
Advancements in computational power and algorithms continue to enhance the accuracy and efficiency of these analyses.
Machine learning and artificial intelligence are emerging as powerful tools to refine simulations and reduce computational costs.
Moreover, researchers are exploring the potential of quantum computing to solve fluid dynamics problems.
Quantum computers have the potential to carry out simulations at speeds unattainable by classical computers, opening new horizons for the industry.
Conclusion
In conclusion, computational fluid and FSI analyses using the finite volume method are invaluable tools for engineers and researchers.
These analyses enable the detailed study of complex fluid behaviors and their interactions with structures, leading to better designs and optimized systems across various industries.
While challenges remain, ongoing developments continue to enhance the capabilities and applications of these methods, promising a bright future for this field.
資料ダウンロード
QCD調達購買管理クラウド「newji」は、調達購買部門で必要なQCD管理全てを備えた、現場特化型兼クラウド型の今世紀最高の購買管理システムとなります。
ユーザー登録
調達購買業務の効率化だけでなく、システムを導入することで、コスト削減や製品・資材のステータス可視化のほか、属人化していた購買情報の共有化による内部不正防止や統制にも役立ちます。
NEWJI DX
製造業に特化したデジタルトランスフォーメーション(DX)の実現を目指す請負開発型のコンサルティングサービスです。AI、iPaaS、および先端の技術を駆使して、製造プロセスの効率化、業務効率化、チームワーク強化、コスト削減、品質向上を実現します。このサービスは、製造業の課題を深く理解し、それに対する最適なデジタルソリューションを提供することで、企業が持続的な成長とイノベーションを達成できるようサポートします。
オンライン講座
製造業、主に購買・調達部門にお勤めの方々に向けた情報を配信しております。
新任の方やベテランの方、管理職を対象とした幅広いコンテンツをご用意しております。
お問い合わせ
コストダウンが利益に直結する術だと理解していても、なかなか前に進めることができない状況。そんな時は、newjiのコストダウン自動化機能で大きく利益貢献しよう!
(Β版非公開)