- お役立ち記事
- Fundamentals of fatigue strength in metal materials and application to safe life design and damage tolerance design
Fundamentals of fatigue strength in metal materials and application to safe life design and damage tolerance design
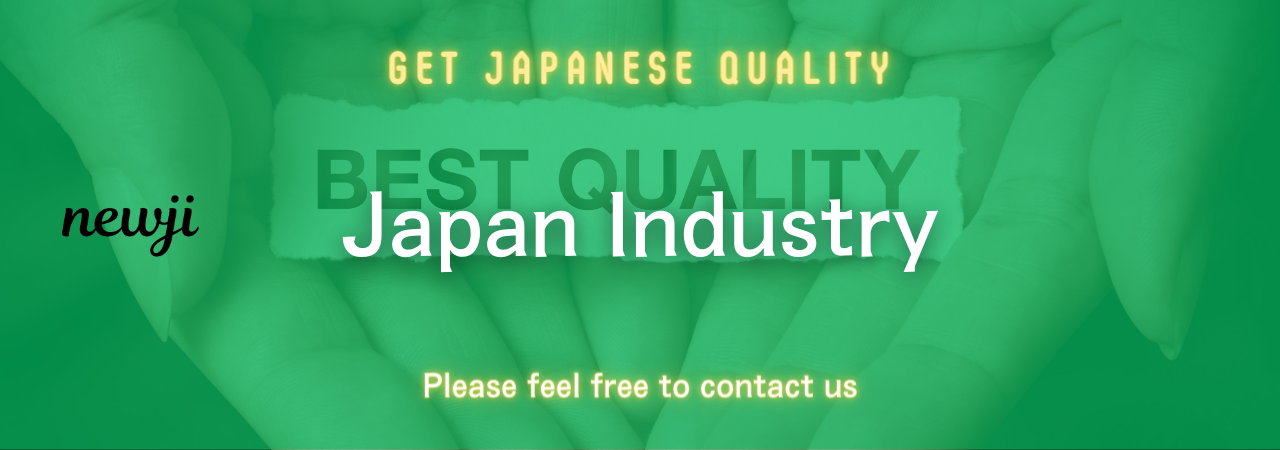
目次
Understanding Fatigue Strength in Metal Materials
When working with metal materials, one crucial concept to grasp is fatigue strength.
Fatigue strength refers to the ability of a material to withstand repeated cycles of stress without failing.
In the context of metals, fatigue occurs because of repetitive loading, which can eventually lead to cracks and fractures over time.
Imagine bending a paperclip back and forth until it breaks.
That’s a simplified version of what happens to metal under fatigue.
The repeated stress reduces its durability and ability to function, even though it may not show immediate signs of distress.
Understanding this concept is vital in designing components that can withstand the test of time under constant usage.
In metals, fatigue strength is characterized by the number of cycles a specimen can endure before failure occurs at a specific stress level.
This property is crucial in industries where metal components are subjected to millions of load cycles, such as in the aerospace, automotive, and construction sectors.
Safe Life Design Concept
The safe life design is a traditional engineering approach used to ensure that a component lasts for its entire intended service life without failure.
This method is widely used in critical applications where the unexpected failure of components could lead to catastrophic consequences.
The basic principle of safe life design involves conservatively estimating the fatigue life of a component.
Engineers calculate the maximum allowable stress that a component can endure over its lifespan and design it within those parameters.
While this approach is effective, it can lead to over-designed components, which may result in heavier structures and increased manufacturing costs.
Safe life design relies heavily on extensive testing and historical data to predict how long a component can last under specific conditions.
It is considered a preventive measure, ensuring that parts are replaced or maintained before they reach a critical point of potential failure.
Through stress analysis, material testing, and comparisons with established fatigue data, engineers can predict the safe life of a component with reasonable accuracy.
Advantages of Safe Life Design
One of the primary benefits of the safe life design approach is its inherent safety.
By designing components that are supposed to operate below their fatigue limits, the likelihood of unexpected failures is significantly reduced.
This is particularly important in applications where human safety is a priority, such as aircraft structures.
Additionally, the safe life methodology also simplifies maintenance schedules.
Knowing the expected life of a component allows operators to plan for replacements well in advance, reducing the risk of unexpected downtime.
Damage Tolerance Design Concept
Contrasting with the safe life design is the damage tolerance design approach.
This method accepts that some level of damage will occur and focuses on assessing and managing it rather than eliminating it entirely.
Damage tolerance design is an increasingly popular alternative due to its flexibility and efficiency in real-world applications.
The damage tolerance concept involves understanding how materials behave once a crack or imperfection is present.
It considers the potential growth of these imperfections and seeks to determine their critical size, beyond which failure is imminent.
By understanding this progression, engineers can design components that can remain functional even when small flaws are present, thus allowing for repairs and maintenance before catastrophic failures occur.
Advantages of Damage Tolerance Design
One of the most notable advantages of damage tolerance design is its cost-effectiveness.
By allowing for inspection and repair rather than complete replacement, it reduces material costs and decreases the need for overly conservative designs.
Furthermore, damage tolerance can enhance weight efficiency in structural elements.
Designs do not need to be as robust as those in safe life methodologies, allowing for lighter and potentially more fuel-efficient structures, especially important in the aerospace sector.
Applications and Implications in Engineering
Both safe life and damage tolerance designs are essential to the engineering of durable and reliable metal components.
They offer different strategies for dealing with fatigue, and the choice between them depends on specific application requirements such as safety, weight, cost, and maintenance feasibility.
Aerospace and automotive industries often lean toward damage tolerance design because of the high costs associated with replacing components.
These sectors benefit from the flexibility of being able to inspect and repair parts without compromising safety.
Conversely, industries such as nuclear power generation might prefer safe life design due to the extraordinarily high safety standards required.
No risk is acceptable, so every component must be designed to operate without failure for its entire lifespan, with any replacement factored into routine service schedules.
In essence, the application of these concepts allows for the design of products that meet the necessary performance criteria while also offering ways to manage costs and ensure safety.
Each approach provides unique tools and strategies for dealing with the inevitable material fatigue that occurs during a component’s life cycle.
Conclusion
Understanding both the fundamentals of fatigue strength and the design philosophies of safe life and damage tolerance is crucial for engineers working with metal materials.
Balancing these methodologies enables the development of products that can meet rigorous safety standards while also optimizing for cost and performance.
Through precise, application-specific engineering, designers can ensure that their metal components meet the demands of their respective industries, maintaining safety and reliability in a world reliant on durable metal materials.
資料ダウンロード
QCD調達購買管理クラウド「newji」は、調達購買部門で必要なQCD管理全てを備えた、現場特化型兼クラウド型の今世紀最高の購買管理システムとなります。
ユーザー登録
調達購買業務の効率化だけでなく、システムを導入することで、コスト削減や製品・資材のステータス可視化のほか、属人化していた購買情報の共有化による内部不正防止や統制にも役立ちます。
NEWJI DX
製造業に特化したデジタルトランスフォーメーション(DX)の実現を目指す請負開発型のコンサルティングサービスです。AI、iPaaS、および先端の技術を駆使して、製造プロセスの効率化、業務効率化、チームワーク強化、コスト削減、品質向上を実現します。このサービスは、製造業の課題を深く理解し、それに対する最適なデジタルソリューションを提供することで、企業が持続的な成長とイノベーションを達成できるようサポートします。
オンライン講座
製造業、主に購買・調達部門にお勤めの方々に向けた情報を配信しております。
新任の方やベテランの方、管理職を対象とした幅広いコンテンツをご用意しております。
お問い合わせ
コストダウンが利益に直結する術だと理解していても、なかなか前に進めることができない状況。そんな時は、newjiのコストダウン自動化機能で大きく利益貢献しよう!
(Β版非公開)