- お役立ち記事
- Fundamentals of in-vehicle networks and key points for CAN network design and troubleshooting
Fundamentals of in-vehicle networks and key points for CAN network design and troubleshooting
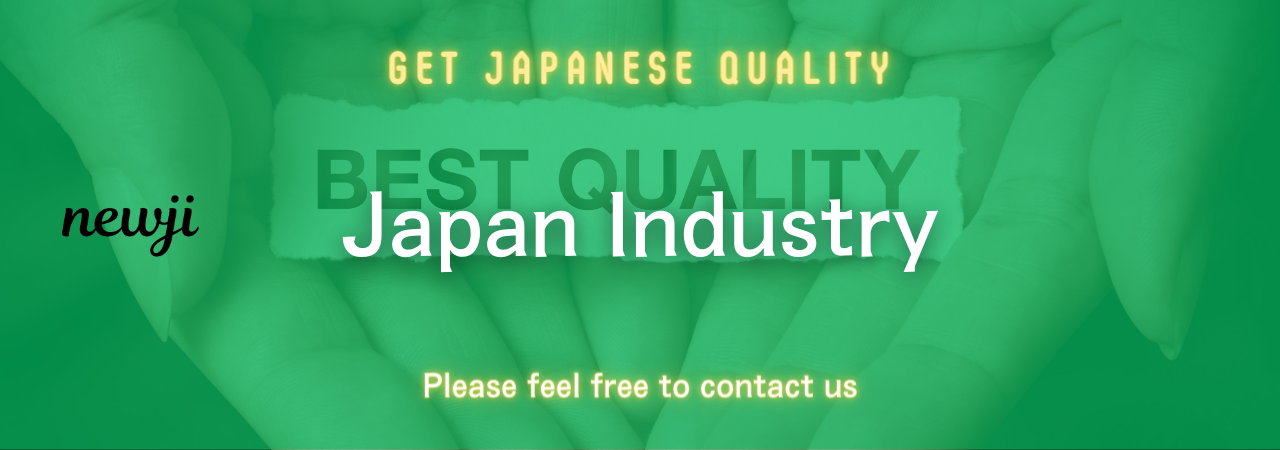
目次
Understanding In-Vehicle Networks
In-vehicle networks have become the backbone of modern automobiles, linking a variety of electronic systems and components to create a cohesive system for vehicle management and telematics.
Understanding the fundamentals of these networks is essential for engineers, designers, and technicians to ensure seamless vehicle operation and innovation in automotive technology.
At its core, an in-vehicle network is a communication setup that allows different electronic components within a vehicle to exchange data.
These networks serve to reduce wiring complexity, improve system efficiency, and enhance vehicle safety and performance.
Among the different types of in-vehicle networks, the Controller Area Network (CAN) has emerged as one of the most prevalent standards due to its reliability, robustness, and cost-effectiveness.
The Importance of CAN Networks
CAN networks are a type of serial communication protocol extensively used in the automotive industry to connect different electronic control units (ECUs).
These ECUs manage various functions, including engine control, transmission, braking systems, and more.
The ability of a CAN network to share data at high speeds and with high accuracy makes it ideal for real-time vehicle applications.
Moreover, CAN networks are designed with fault-tolerance capabilities, making them especially suitable for use in the demanding conditions experienced by automotive systems.
The standardized message format of CAN networks facilitates interoperability between different manufacturers’ components, supporting modular design and system integration.
Key Points for CAN Network Design
When designing a CAN network, several critical elements must be considered to ensure optimal performance and reliability.
Network Topology
The topology of a CAN network refers to its physical arrangement and layout.
Typically, CAN networks are designed in a bus topology, with all nodes connected to a single backbone.
This structure minimizes the amount of wiring needed and supports easy addition or removal of ECUs, making it flexible and scalable.
It’s important to ensure that the maximum recommended length for CAN cables is not exceeded to prevent signal degradation.
Data Rate and Bit Timing
Selecting an appropriate data rate is essential to balance transmission speed and network performance.
For typical automotive applications, CAN networks support different data rates, with 125 kbps and 500 kbps being the most common.
Each network’s bit timing must be properly configured to ensure accurate data transmission.
This involves adjusting parameters like time quanta and synchronization segments to accommodate physical layer delays.
Error Handling
Robust error handling mechanisms are a vital part of CAN network design.
These networks automatically detect and recover from errors such as bit errors, acknowledgment errors, and form errors.
Designing systems to handle these errors involves the implementation of error recovery and retransmission strategies to maintain data integrity.
Physical Layer Considerations
The physical layer of the CAN network is equally important for guaranteeing reliable communication.
Shielded twisted-pair cables are commonly used to reduce electromagnetic interference.
Terminating resistors must be placed correctly at both ends of the network to maintain the characteristic impedance and minimize signal reflections.
Troubleshooting CAN Networks
Even well-designed CAN networks can encounter issues during operation.
Awareness of common troubleshooting techniques is beneficial for quickly diagnosing and resolving these problems.
Monitoring and Diagnostics
Using tools like oscilloscopes and CAN bus analyzers can aid in monitoring network traffic and diagnosing issues.
These tools can display messages in real-time, helping identify errors such as disconnected nodes, malfunctioning ECUs, or incorrect termination.
Regular monitoring can also indicate early signs of network degradation.
Identifying Faults
One common technique for troubleshooting is systematically disconnecting and reconnecting nodes to determine the source of the fault.
This approach can help isolate faulty ECUs or issues with wiring.
Additionally, error counters built into most CAN controllers can provide useful information about the type of error detected.
Line Quality Testing
Ensuring that the physical quality of the CAN bus is sound is also vital.
This includes checking for cable wear and tear, proper connector seating, and contamination that might cause signal integrity issues.
A thorough analysis of line quality might involve inspecting the voltage levels and noise margins on the network.
Software Diagnostics
Software diagnostics involves using dedicated tools to analyze the software setup on each ECU.
This can help identify configuration errors, firmware glitches, or incompatibilities contributing to communication issues.
Regular software updates can also mitigate certain types of failures and improve network stability.
Conclusion
In-vehicle networks, particularly CAN networks, are critical elements in modern automobiles, allowing for efficient and reliable communication between various electronic components.
Understanding these networks requires a grasp of their design elements, like topology, data rates, error handling, and physical layer considerations.
Furthermore, effective troubleshooting techniques ensure that these networks function optimally.
As automotive technology continues to advance, the importance of skilled cultivation and maintenance of in-vehicle networks will remain a key aspect of vehicle innovation and safety.
Both engineers and technicians must develop a firm grasp of these concepts to remain at the forefront of automotive development.
資料ダウンロード
QCD調達購買管理クラウド「newji」は、調達購買部門で必要なQCD管理全てを備えた、現場特化型兼クラウド型の今世紀最高の購買管理システムとなります。
ユーザー登録
調達購買業務の効率化だけでなく、システムを導入することで、コスト削減や製品・資材のステータス可視化のほか、属人化していた購買情報の共有化による内部不正防止や統制にも役立ちます。
NEWJI DX
製造業に特化したデジタルトランスフォーメーション(DX)の実現を目指す請負開発型のコンサルティングサービスです。AI、iPaaS、および先端の技術を駆使して、製造プロセスの効率化、業務効率化、チームワーク強化、コスト削減、品質向上を実現します。このサービスは、製造業の課題を深く理解し、それに対する最適なデジタルソリューションを提供することで、企業が持続的な成長とイノベーションを達成できるようサポートします。
オンライン講座
製造業、主に購買・調達部門にお勤めの方々に向けた情報を配信しております。
新任の方やベテランの方、管理職を対象とした幅広いコンテンツをご用意しております。
お問い合わせ
コストダウンが利益に直結する術だと理解していても、なかなか前に進めることができない状況。そんな時は、newjiのコストダウン自動化機能で大きく利益貢献しよう!
(Β版非公開)