- お役立ち記事
- Unlocking Innovation: The Pioneering Role of Connector OEMs in Japanese Manufacturing Excellence
Unlocking Innovation: The Pioneering Role of Connector OEMs in Japanese Manufacturing Excellence
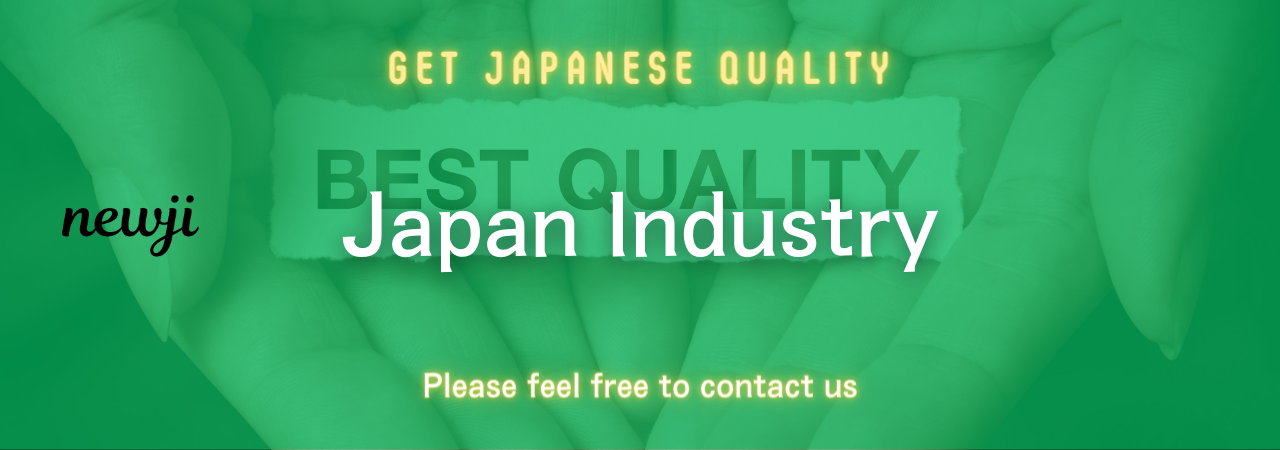
目次
Introduction to Connector OEMs in Japanese Manufacturing
Japanese manufacturing has long been synonymous with quality, precision, and innovation.
At the heart of this excellence lies the pivotal role played by Connector Original Equipment Manufacturers (OEMs).
These specialized manufacturers are instrumental in driving advancements across various industries, from automotive to electronics.
Understanding the dynamics of Connector OEMs provides valuable insights into the broader landscape of Japanese manufacturing prowess.
Understanding Connector OEMs
Connector OEMs are companies that design, manufacture, and supply connectors used in a wide array of products.
These connectors facilitate the transmission of electrical signals and power between different components, ensuring the seamless operation of devices and systems.
In Japan, Connector OEMs are renowned for their meticulous attention to detail, high-quality standards, and innovative solutions.
They collaborate closely with their clients to develop customized connectors tailored to specific requirements, thereby enhancing product performance and reliability.
Key Functions of Connector OEMs
– **Design and Engineering:** Developing connectors that meet precise specifications and industry standards.
– **Manufacturing:** Utilizing advanced technologies and materials to produce durable and reliable connectors.
– **Quality Control:** Implementing rigorous testing procedures to ensure each connector meets stringent quality benchmarks.
– **Supply Chain Management:** Coordinating the timely delivery of connectors to manufacturers, ensuring uninterrupted production processes.
The Role of Connector OEMs in Innovation
Connector OEMs are not merely suppliers; they are partners in innovation.
Their expertise enables the development of cutting-edge products by providing connectors that support the latest technological advancements.
For instance, in the automotive industry, OEM connectors are crucial for the integration of advanced driver-assistance systems (ADAS) and electric vehicle (EV) components.
By collaborating with Connector OEMs, manufacturers can stay ahead of technological trends and incorporate state-of-the-art features into their products.
Driving Technological Advancements
Connector OEMs contribute to innovation by:
– **Research and Development:** Investing in R&D to create connectors that accommodate emerging technologies and evolving industry demands.
– **Customization:** Offering bespoke solutions that address specific challenges faced by manufacturers, such as high-speed data transmission or extreme environmental conditions.
– **Material Innovation:** Exploring new materials that enhance connector performance, durability, and compatibility with diverse applications.
Advantages of Partnering with Japanese Connector OEMs
Collaborating with Japanese Connector OEMs offers numerous benefits that can significantly enhance manufacturing processes and product quality.
Unparalleled Quality and Reliability
Japanese OEMs are celebrated for their commitment to quality.
Stringent quality control measures ensure that each connector is reliable and performs consistently under various conditions.
This reliability is crucial for manufacturers aiming to deliver high-performance and long-lasting products to their customers.
Advanced Manufacturing Techniques
Japanese Connector OEMs leverage state-of-the-art manufacturing technologies, including precision machining, automated assembly, and rigorous testing protocols.
These advanced techniques enable the production of connectors with high precision and minimal defects, contributing to overall manufacturing excellence.
Customization and Flexibility
Connector OEMs in Japan offer a high degree of customization, allowing manufacturers to tailor connectors to their specific needs.
Whether it’s unique sizing, specialized materials, or intricate designs, these OEMs can accommodate diverse requirements, enhancing product functionality and performance.
Strong Supplier Relationships
Japanese OEMs prioritize building long-term partnerships with their clients.
This collaborative approach fosters mutual trust, enhances communication, and ensures that manufacturers receive the support they need to succeed in competitive markets.
Challenges and Considerations
While partnering with Japanese Connector OEMs offers significant advantages, there are also challenges to consider.
High Initial Investment
The advanced technologies and high-quality standards employed by Japanese OEMs often come with higher costs.
Manufacturers must weigh the benefits of superior quality and reliability against the increased initial investment.
Communication and Cultural Differences
Effective collaboration requires clear communication and understanding of cultural nuances.
Differences in business practices and communication styles can pose challenges, necessitating proactive efforts to bridge gaps and ensure smooth interactions.
Lead Times and Production Schedules
Japanese OEMs may have longer lead times due to their rigorous quality control and customization processes.
Manufacturers need to plan their production schedules accordingly to avoid delays and ensure timely delivery of their products.
Supplier Negotiation Techniques
Successful partnerships with Connector OEMs hinge on effective negotiation strategies.
Thorough Preparation
Before entering negotiations, conduct comprehensive research on the OEM’s capabilities, market position, and pricing structures.
Understanding their strengths and constraints enables more informed and strategic discussions.
Clear Communication of Requirements
Articulate your specific needs and expectations clearly and precisely.
Providing detailed specifications and use cases helps the OEM understand your requirements and develop appropriate solutions.
Building Relationships
Invest time in building strong personal relationships with key contacts within the OEM.
Trust and mutual respect are foundational to successful long-term partnerships and can facilitate more favorable negotiation outcomes.
Flexibility and Compromise
Approach negotiations with a willingness to be flexible and find mutually beneficial solutions.
Compromise on non-critical aspects can help reach agreements that satisfy both parties and strengthen the partnership.
Market Conditions and Trends
Staying abreast of market conditions and emerging trends is essential for optimizing procurement strategies.
Technological Advancements
The rapid pace of technological innovation drives demand for more sophisticated connectors.
Manufacturers must adapt to these changes by collaborating with OEMs that can provide connectors compatible with the latest technologies.
Global Supply Chain Dynamics
Global events, such as geopolitical tensions and pandemics, can disrupt supply chains.
Developing robust relationships with Japanese OEMs and diversifying supplier bases can mitigate risks and ensure supply chain resilience.
Sustainability and Environmental Concerns
There is increasing emphasis on sustainability in manufacturing.
Connector OEMs that prioritize eco-friendly materials and sustainable manufacturing practices are becoming more desirable partners.
Best Practices for Successful Collaboration
Implementing best practices can enhance the effectiveness of partnerships with Connector OEMs.
Establish Clear Objectives
Define your goals and expectations upfront to ensure alignment with the OEM’s capabilities and strategies.
Clear objectives provide a roadmap for collaboration and facilitate smoother project execution.
Regular Communication
Maintain consistent and open lines of communication with your OEM partners.
Regular updates, meetings, and feedback sessions help address issues promptly and keep projects on track.
Continuous Improvement
Adopt a mindset of continuous improvement to enhance product quality and operational efficiency.
Collaborate with OEMs to identify areas for improvement and implement innovative solutions that drive mutual growth.
Performance Monitoring
Implement robust metrics and monitoring systems to assess the performance of your OEM partners.
Regular performance reviews help ensure that quality standards are met and identify opportunities for enhancement.
Case Studies: Success Stories of Japanese Connector OEMs
Examining real-world examples highlights the impact of Japanese Connector OEMs on manufacturing success.
Automotive Industry
A leading automotive manufacturer partnered with a Japanese Connector OEM to develop high-performance connectors for electric vehicles.
The collaboration resulted in connectors that improved power efficiency and reliability, contributing to the vehicle’s overall performance and market competitiveness.
Consumer Electronics
A global electronics company worked with a Japanese Connector OEM to design customized connectors for its latest smartphone.
The resulting connectors supported faster data transfer speeds and enhanced durability, setting the product apart in a crowded market.
Industrial Automation
An industrial automation firm partnered with a Japanese Connector OEM to develop connectors for advanced robotics systems.
The customized connectors enabled seamless integration of components, enhancing the precision and efficiency of the robotic systems.
Future Outlook for Connector OEMs in Japan
The future of Connector OEMs in Japan looks promising, driven by continuous innovation and evolving market demands.
Embracing Industry 4.0
Connector OEMs are poised to play a crucial role in the Industry 4.0 revolution by providing connectors that support smart manufacturing technologies, including the Internet of Things (IoT), artificial intelligence (AI), and automation.
Expanding into Emerging Markets
Japanese Connector OEMs are exploring opportunities in emerging markets, diversifying their customer base and expanding their global footprint to drive sustained growth.
Focus on Sustainability
With increasing emphasis on environmental sustainability, Connector OEMs are investing in eco-friendly materials and sustainable manufacturing practices to meet the growing demand for green products.
Conclusion
Connector OEMs are indispensable to the fabric of Japanese manufacturing excellence.
Their commitment to quality, innovation, and collaboration enables manufacturers to produce high-performance, reliable products that meet global standards.
While challenges exist, the advantages of partnering with Japanese Connector OEMs—such as unparalleled quality, advanced manufacturing techniques, and strong supplier relationships—outweigh the drawbacks.
By employing effective negotiation techniques, staying attuned to market conditions, and adhering to best practices, manufacturers can unlock significant value from these partnerships.
As the manufacturing landscape continues to evolve, Connector OEMs in Japan will remain at the forefront of driving innovation and maintaining the country’s reputation for manufacturing excellence.
資料ダウンロード
QCD調達購買管理クラウド「newji」は、調達購買部門で必要なQCD管理全てを備えた、現場特化型兼クラウド型の今世紀最高の購買管理システムとなります。
ユーザー登録
調達購買業務の効率化だけでなく、システムを導入することで、コスト削減や製品・資材のステータス可視化のほか、属人化していた購買情報の共有化による内部不正防止や統制にも役立ちます。
NEWJI DX
製造業に特化したデジタルトランスフォーメーション(DX)の実現を目指す請負開発型のコンサルティングサービスです。AI、iPaaS、および先端の技術を駆使して、製造プロセスの効率化、業務効率化、チームワーク強化、コスト削減、品質向上を実現します。このサービスは、製造業の課題を深く理解し、それに対する最適なデジタルソリューションを提供することで、企業が持続的な成長とイノベーションを達成できるようサポートします。
オンライン講座
製造業、主に購買・調達部門にお勤めの方々に向けた情報を配信しております。
新任の方やベテランの方、管理職を対象とした幅広いコンテンツをご用意しております。
お問い合わせ
コストダウンが利益に直結する術だと理解していても、なかなか前に進めることができない状況。そんな時は、newjiのコストダウン自動化機能で大きく利益貢献しよう!
(Β版非公開)