- お役立ち記事
- Fundamentals of reliability testing technology and application to life prediction and reliability evaluation of electronic components and mounted boards
Fundamentals of reliability testing technology and application to life prediction and reliability evaluation of electronic components and mounted boards
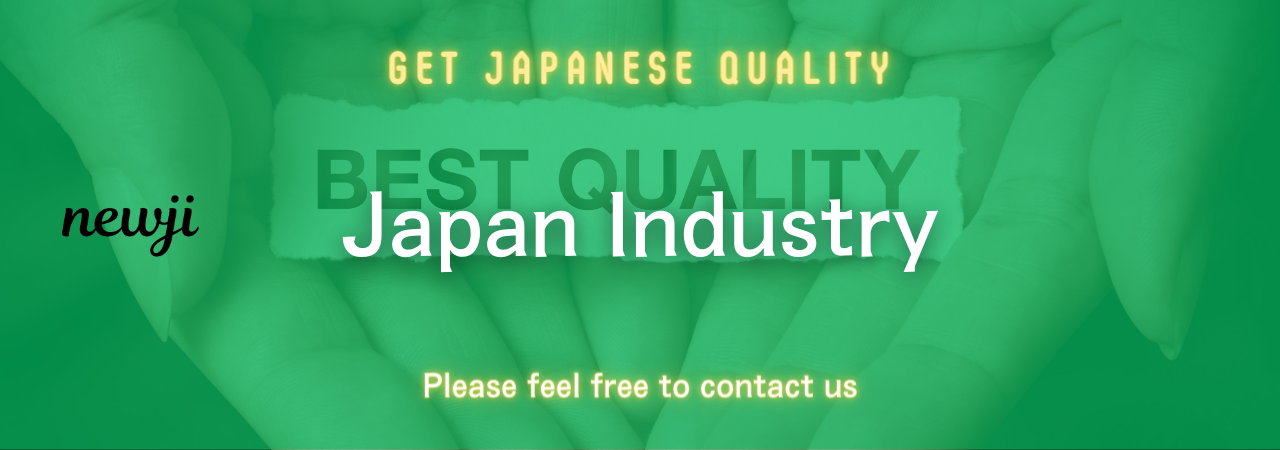
目次
Understanding Reliability Testing
Reliability testing is essential in determining the durability and longevity of electronic components and mounted boards.
It provides insights into how a product will perform under various conditions over time.
This process involves rigorous testing methods that simulate different environmental and operational scenarios.
Reliability testing helps manufacturers ensure that their products are reliable, safe, and meet the required standards before reaching consumers.
Importance of Reliability Testing
Reliability testing is crucial because it identifies potential failures and weaknesses in electronic components and boards.
It ensures that products meet the necessary quality standards and perform as expected throughout their life cycle.
By predicting how long a product will last and its failure modes, manufacturers can improve product designs, reduce costs, and enhance customer satisfaction.
Types of Reliability Testing
There are several types of reliability testing methods used to evaluate electronic components and mounted boards.
Environmental Testing
Environmental testing simulates the conditions that a product might face in its actual use environment.
This includes exposure to extreme temperatures, humidity, vibration, shock, and other environmental factors.
The goal is to identify how these conditions impact the performance and durability of the product.
Life Testing
Life testing involves subjecting a product to stress over an extended period to assess its long-term performance and durability.
This testing helps manufacturers determine the average lifespan of a product and identify potential failure points.
Accelerated Life Testing (ALT)
Accelerated life testing speeds up the aging process of a product by applying higher stress levels than it would experience in normal use.
This method is useful for predicting a product’s life expectancy in a shorter time frame.
By simulating increased stress, manufacturers can identify potential reliability issues early in the product development process.
Stress Testing
Stress testing involves subjecting a product to varying levels of stress to evaluate its performance and reliability.
This method helps identify the product’s limit and how it behaves under extreme conditions.
Stress testing is critical for understanding a product’s robustness and failure thresholds.
Application to Life Prediction
Life prediction is an integral part of reliability testing that helps estimate the expected lifespan of electronic components and mounted boards.
Statistical Models
Statistical models, such as Weibull analysis, are used to predict a product’s reliability and lifespan.
These models analyze failure data to estimate the time until the next failure occurs.
By understanding the failure distribution, manufacturers can make informed decisions on warranty periods and maintenance schedules.
Data Collection
Data collection is vital in life prediction and involves gathering information from testing results and field data.
By analyzing this data, manufacturers can identify trends and patterns that influence product reliability.
This information is used to improve product designs and make data-driven decisions.
Failure Mechanisms
Understanding failure mechanisms is crucial for accurate life prediction.
By identifying the causes of failure, manufacturers can implement design changes to improve product reliability.
Common failure mechanisms in electronic components include thermal cycling, mechanical wear, and corrosion.
Reliability Evaluation of Electronic Components
Reliability evaluation assesses the performance and durability of electronic components in various scenarios.
Component Testing
Component testing evaluates the performance of individual components to ensure they meet the required standards.
This testing includes examining electrical, mechanical, and thermal characteristics.
By evaluating each component, manufacturers can identify potential weak points and improve overall product reliability.
Board-Level Testing
Board-level testing evaluates the reliability of mounted electronic boards.
This process involves assessing how the components function together under simulated operational conditions.
Board-level testing helps identify issues with the integration of components and potential solder joint failures.
Challenges in Reliability Testing
Reliability testing presents several challenges that manufacturers need to address.
Complexity of Modern Electronics
Modern electronic components and boards are increasingly complex, making reliability testing more challenging.
The rise of advanced technologies and miniaturization has led to more intricate designs, requiring sophisticated testing methods.
Time and Cost Constraints
Reliability testing can be time-consuming and costly, especially for accelerated life tests and advanced statistical modeling.
Manufacturers must balance the need for thorough testing with budget and time constraints to ensure efficient product development.
Future Trends in Reliability Testing
As technology advances, reliability testing practices continue to evolve.
Automated Testing
Automated testing solutions are becoming more prevalent, helping to streamline the testing process.
These systems can perform complex tests more efficiently, reducing time and labor costs.
Machine Learning and AI
Machine learning and artificial intelligence are increasingly being used to enhance reliability testing.
These technologies can analyze large data sets to predict failure patterns and improve testing accuracy.
In conclusion, reliability testing is a fundamental aspect of developing high-quality electronic components and mounted boards.
By understanding and applying these testing methodologies, manufacturers can predict product life, improve reliability, and ensure customer satisfaction.
資料ダウンロード
QCD調達購買管理クラウド「newji」は、調達購買部門で必要なQCD管理全てを備えた、現場特化型兼クラウド型の今世紀最高の購買管理システムとなります。
ユーザー登録
調達購買業務の効率化だけでなく、システムを導入することで、コスト削減や製品・資材のステータス可視化のほか、属人化していた購買情報の共有化による内部不正防止や統制にも役立ちます。
NEWJI DX
製造業に特化したデジタルトランスフォーメーション(DX)の実現を目指す請負開発型のコンサルティングサービスです。AI、iPaaS、および先端の技術を駆使して、製造プロセスの効率化、業務効率化、チームワーク強化、コスト削減、品質向上を実現します。このサービスは、製造業の課題を深く理解し、それに対する最適なデジタルソリューションを提供することで、企業が持続的な成長とイノベーションを達成できるようサポートします。
オンライン講座
製造業、主に購買・調達部門にお勤めの方々に向けた情報を配信しております。
新任の方やベテランの方、管理職を対象とした幅広いコンテンツをご用意しております。
お問い合わせ
コストダウンが利益に直結する術だと理解していても、なかなか前に進めることができない状況。そんな時は、newjiのコストダウン自動化機能で大きく利益貢献しよう!
(Β版非公開)