- お役立ち記事
- Basics of cutting technology and points for improving machining accuracy and cutting performance
Basics of cutting technology and points for improving machining accuracy and cutting performance
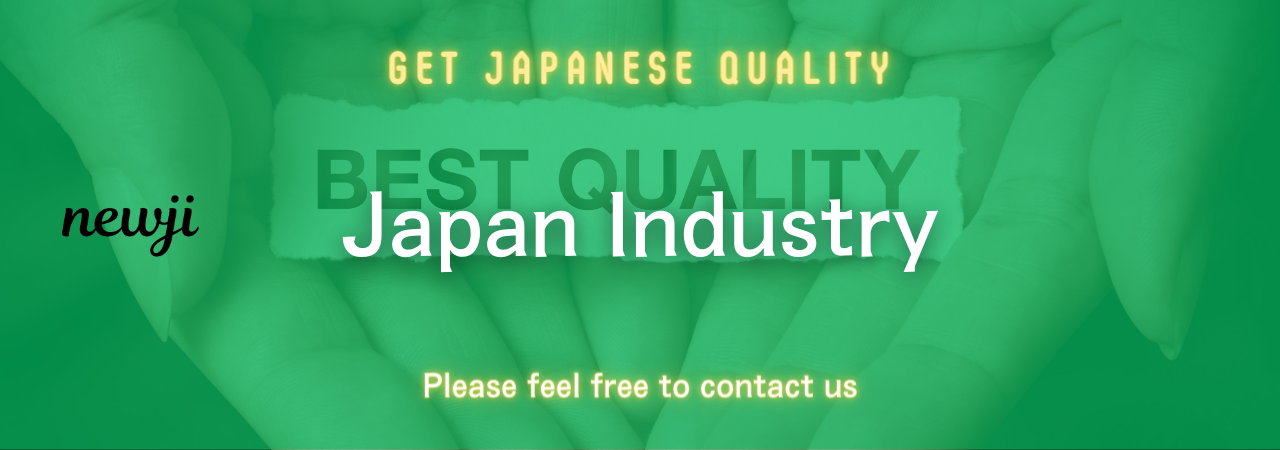
目次
Understanding Cutting Technology
Cutting technology is a crucial aspect of manufacturing and metalworking, impacting both the quality and efficiency of production processes.
It involves the removal of material from a workpiece using tools to shape or finish the product.
Cutting processes can range from simple hand tools to complex computer-controlled machinery.
The primary goal of cutting technology is to achieve precise dimensions, smooth finishes, and efficient production times.
There are several cutting techniques used in various industries, including turning, milling, drilling, sawing, and grinding.
Each method has its own set of tools and processes designed for specific materials and desired outcomes.
Methods of Cutting
The choice of cutting method depends on the material, desired shape, and required precision.
Here are some of the common cutting methods:
Turning
Turning involves rotating the workpiece while a cutting tool is moved linearly.
This process is primarily used to create cylindrical shapes and is commonly performed on a lathe.
Turning can achieve tight tolerances and smooth surface finishes.
Milling
Milling uses rotary cutters to remove material from a workpiece.
The milling machine can move the cutter in various directions to carve out complex shapes.
Milling is versatile and can produce flat surfaces, grooves, and contours.
Drilling
Drilling is the process of cutting or enlarging a hole in a workpiece using a rotating drill bit.
It’s a fundamental technique used in construction, metalworking, and woodworking.
Different types of drill bits are used depending on the material and desired hole size.
Sawing
Sawing is a method of cutting material using a saw blade.
It is often used for cutting metal, wood, and composite materials.
The type of saw depends on the material being cut, with options such as band saws, hacksaws, and circular saws.
Grinding
Grinding uses an abrasive wheel to remove material.
It’s typically used for finishing surfaces and achieving precise dimensions.
Grinding can produce high-quality finishes and tight tolerances.
Factors Affecting Machining Accuracy
Achieving high machining accuracy is essential for producing parts that meet specifications and function properly.
Several factors can influence machining accuracy:
Tool Selection
The selection of cutting tools plays a significant role in determining machining accuracy.
Choosing the right tool material, geometry, and coating can enhance cutting performance and extend tool life.
Different tools are suited for various materials and operations.
Cutting Parameters
Cutting parameters such as speed, feed, and depth of cut affect the quality of the final product.
Properly adjusting these parameters can minimize tool wear, improve surface finish, and increase dimensional accuracy.
Machine Condition
The condition of the machine tool is crucial for maintaining accuracy.
Worn or poorly maintained machines can lead to vibrations, deflections, and deviations from desired measurements.
Regular maintenance and calibration are essential to ensure optimal machine performance.
Workpiece Material
The properties of the workpiece material, such as hardness and elasticity, can impact machining accuracy.
Different materials respond differently to cutting forces, affecting the required tool type and machining strategy.
Enhancing Cutting Performance
Improving cutting performance involves optimizing various elements of the machining process to improve efficiency and quality.
Tool Wear Management
Tool wear is inevitable, but managing it effectively can improve performance.
Regularly monitoring tool condition and using wear-resistant coatings can extend tool life and reduce downtime.
Use of Coolants
Proper coolant application can reduce heat generation, enhance tool life, and improve surface finish.
Coolants also help in flushing away chips, preventing them from affecting the cutting process.
Precision Tool Holding
Using precision tool holders ensures that the tool is held securely, reducing vibrations and run-out.
This helps in maintaining accuracy and surface integrity.
Adopting Advanced Technologies
Incorporating modern technologies, such as CNC (Computer Numerical Control) machines and CAD/CAM software, can significantly enhance cutting performance.
These technologies enable high precision, repeatability, and complex geometry machining.
Conclusion
Cutting technology is fundamental to manufacturing, impacting efficiency, accuracy, and product quality.
By understanding the principles of different cutting methods and the factors affecting machining accuracy, manufacturers can optimize their processes and achieve superior results.
Continual advancements in cutting tools, technology, and methodologies drive the evolution of cutting performance, allowing for more complex and precise manufacturing capabilities.
資料ダウンロード
QCD調達購買管理クラウド「newji」は、調達購買部門で必要なQCD管理全てを備えた、現場特化型兼クラウド型の今世紀最高の購買管理システムとなります。
ユーザー登録
調達購買業務の効率化だけでなく、システムを導入することで、コスト削減や製品・資材のステータス可視化のほか、属人化していた購買情報の共有化による内部不正防止や統制にも役立ちます。
NEWJI DX
製造業に特化したデジタルトランスフォーメーション(DX)の実現を目指す請負開発型のコンサルティングサービスです。AI、iPaaS、および先端の技術を駆使して、製造プロセスの効率化、業務効率化、チームワーク強化、コスト削減、品質向上を実現します。このサービスは、製造業の課題を深く理解し、それに対する最適なデジタルソリューションを提供することで、企業が持続的な成長とイノベーションを達成できるようサポートします。
オンライン講座
製造業、主に購買・調達部門にお勤めの方々に向けた情報を配信しております。
新任の方やベテランの方、管理職を対象とした幅広いコンテンツをご用意しております。
お問い合わせ
コストダウンが利益に直結する術だと理解していても、なかなか前に進めることができない状況。そんな時は、newjiのコストダウン自動化機能で大きく利益貢献しよう!
(Β版非公開)