- お役立ち記事
- Fundamentals of dry etching technology and application to high-precision microfabrication using atomic layer etching (ALE) technology
Fundamentals of dry etching technology and application to high-precision microfabrication using atomic layer etching (ALE) technology
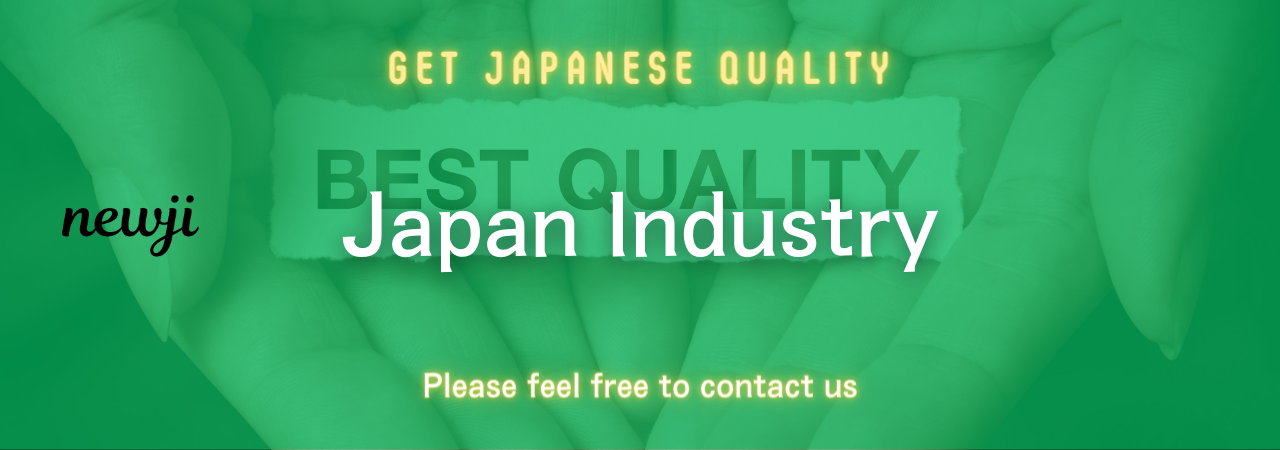
目次
Understanding Dry Etching Technology
Dry etching technology is a vital process in the field of microfabrication, where it is used to create intricate structures on semiconductor wafers.
Unlike wet etching, which involves the use of liquid chemicals to remove material from wafers, dry etching employs gases to etch materials in a controlled environment.
This process ensures precision and accuracy, which is crucial in the production of smaller and more complex electronic components.
The importance of dry etching lies in its ability to deliver fine, anisotropic etches, meaning it etches materials directionally.
This is essential for creating high-aspect-ratio structures.
In the world of microfabrication, where every nanometer can count, the directional control offered by dry etching is invaluable.
The Role of Plasmas in Dry Etching
One of the central aspects of dry etching is the use of plasmas.
Plasmas are ionized gases that contain a mixture of ions, electrons, and neutral particles.
These charged particles provide the energy needed to remove material from the surface of wafers.
The process begins by introducing a process gas, such as oxygen or chlorine, into a chamber containing the wafer.
An external energy source, like radio frequency (RF) power, is used to ionize the gas, creating plasma.
The energetic ions in the plasma then collide with the wafer surface, breaking the bonds and removing material through physical or chemical means.
Controlling the plasma parameters is essential to achieving precise etching results.
This includes managing the ion energy, ion density, and plasma composition, which all affect the etch rate and uniformity.
Applications of Dry Etching in Microfabrication
The semiconductor industry relies heavily on dry etching technology to fabricate integrated circuits (ICs), sensors, and various other components that form the backbone of modern electronics.
Dry etching comes into play primarily during the photolithography process to define intricate patterns on wafers.
Photolithography involves using light to transfer a geometric pattern from a photomask onto a light-sensitive chemical photoresist coated on the wafer’s surface.
Once the pattern is developed, dry etching is used to remove the exposed material, allowing manufacturers to create precise layers of circuits and components.
This is especially crucial as devices become increasingly miniaturized, requiring extremely tight tolerances to function correctly.
Challenges in Dry Etching Technology
Despite its advantages, dry etching technology presents several challenges.
One significant concern is the potential for plasma-induced damage, where the high-energy ions can harm the underlying materials, affecting device performance.
Careful process optimization and equipment design are needed to minimize this damage.
Another challenge is achieving selectivity, which is the ability to etch one material while preserving others.
Selectivity is important in microfabrication because multiple layers of different materials are often etched simultaneously.
Achieving high selectivity ensures that the desired structures are formed without unwanted erosion of other layers.
Atomic Layer Etching (ALE) Technology
To overcome some of the limitations of traditional dry etching processes, Atomic Layer Etching (ALE) technology has emerged as a highly precise solution.
ALE is a novel approach that allows atomic-level control over the etching process, delivering even greater precision and repeatability.
ALE operates on the principle of removing individual atomic layers one at a time.
This is achieved through a cyclic process involving two or more steps, typically alternating between the adsorption of reactive chemicals and the removal of these adsorbed layers with controlled energy input.
The cyclic nature of ALE ensures that each etching cycle is self-limiting, contributing to its high accuracy.
Advantages of ALE in Microfabrication
The advantages of ALE in microfabrication are manifold.
Firstly, it offers unrivaled precision and uniformity, which translates to superior control over nanoscale features.
This is particularly beneficial for manufacturing devices with thin film layers, where thickness uniformity is crucial.
Secondly, ALE boasts excellent selectivity compared to traditional dry etching methods.
Its ability to precisely etch specific layers enhances the material’s integrity and reduces the risk of damaging underlying structures.
Moreover, the slow and controlled nature of ALE allows manufacturers to adapt the process easily for different materials and devices.
This flexibility is critical in a rapidly advancing field where materials and designs are constantly evolving.
The Future of Microfabrication with ALE
As the demand for smaller and more complex electronic devices continues to grow, the need for precision and reliability in microfabrication processes becomes more apparent.
ALE represents a significant advancement that promises to push the boundaries of what’s possible in device manufacturing.
Looking ahead, the integration of ALE with other emerging technologies could drive further innovations.
This includes combining ALE with advanced lithography techniques to create even smaller features or incorporating it into novel materials and superconductors for next-generation electronics.
In conclusion, while dry etching technology has already established itself as a cornerstone in microfabrication, ALE offers a glimpse into the future of high-precision manufacturing.
By refining processes at the atomic level, ALE stands to play an instrumental role in shaping the future of electronics, making it a critical area of focus for researchers and industry professionals alike.
資料ダウンロード
QCD調達購買管理クラウド「newji」は、調達購買部門で必要なQCD管理全てを備えた、現場特化型兼クラウド型の今世紀最高の購買管理システムとなります。
ユーザー登録
調達購買業務の効率化だけでなく、システムを導入することで、コスト削減や製品・資材のステータス可視化のほか、属人化していた購買情報の共有化による内部不正防止や統制にも役立ちます。
NEWJI DX
製造業に特化したデジタルトランスフォーメーション(DX)の実現を目指す請負開発型のコンサルティングサービスです。AI、iPaaS、および先端の技術を駆使して、製造プロセスの効率化、業務効率化、チームワーク強化、コスト削減、品質向上を実現します。このサービスは、製造業の課題を深く理解し、それに対する最適なデジタルソリューションを提供することで、企業が持続的な成長とイノベーションを達成できるようサポートします。
オンライン講座
製造業、主に購買・調達部門にお勤めの方々に向けた情報を配信しております。
新任の方やベテランの方、管理職を対象とした幅広いコンテンツをご用意しております。
お問い合わせ
コストダウンが利益に直結する術だと理解していても、なかなか前に進めることができない状況。そんな時は、newjiのコストダウン自動化機能で大きく利益貢献しよう!
(Β版非公開)