- お役立ち記事
- Fundamentals of gears, strength design, and noise reduction technology
Fundamentals of gears, strength design, and noise reduction technology
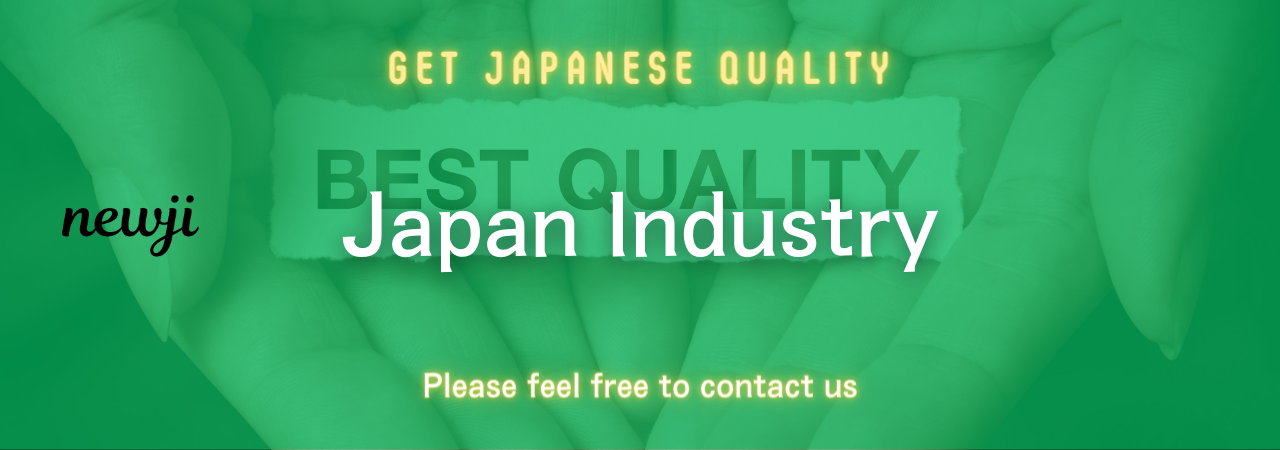
目次
Understanding Gears
Gears are an essential component in many machines and mechanisms, helping to transfer motion and power efficiently.
They come in various shapes and sizes, each designed to perform specific tasks.
The basic function of gears is to transmit torque and speed between moving parts.
This is achieved by meshing their teeth together and rotating, which then drives one gear’s rotation through another.
Common types of gears include spur gears, helical gears, bevel gears, and worm gears.
Each type offers unique advantages and is chosen based on the application.
For example, spur gears are used for simple tasks and are known for their straightforward design.
Helical gears, with their angled teeth, offer smoother and quieter operation, making them ideal for complex machinery.
Understanding the fundamentals of gear design is crucial to selecting the right gear for any purpose.
Strength Design of Gears
When designing gears for strength, engineers must consider several critical factors to ensure durability and reliability.
The strength of a gear is primarily influenced by materials, tooth design, and load conditions.
Selecting the appropriate material for gear construction is crucial because it directly impacts the gear’s performance and lifespan.
Common materials used for gears include steel, brass, aluminum, and plastic, each offering different levels of strength and wear resistance.
Tooth design is another vital component in gear strength.
The shape and size of the gear teeth determine how well they mesh with each other, impacting efficiency and wear.
Properly designed teeth can significantly enhance the gear’s ability to handle high loads and decrease the likelihood of failure.
Load conditions refer to the forces applied to the gears during operation.
Designers need to account for variable loads, as any unforeseen stress can lead to gear failure.
This involves calculating the expected forces and setting safety margins to prevent overloading.
A comprehensive understanding of load conditions allows engineers to create gears that maintain their integrity under varying stresses.
Techniques for Noise Reduction in Gears
Gears can often be a source of noise in machinery, which can be a significant concern, especially in settings where quiet operation is crucial.
Reducing gear noise involves several strategies aimed at minimizing vibration and improving the smoothness of gear operation.
One technique for noise reduction is optimizing the gear meshing.
This involves ensuring that the gear teeth engage and disengage smoothly, which minimizes the noise generated from vibration.
Helical gears are often preferred for their quieter operation compared to spur gears because their angled teeth allow for gradual engagement.
Material selection also plays a role in noise reduction.
Using materials with good damping properties can help absorb vibrations, reducing the noise produced during operation.
Additionally, incorporating proper lubrication between gears can lessen friction and noise.
Another effective method is to refine the manufacturing process of gears.
Precision machining ensures that gears have smooth surfaces and accurate dimensions, reducing the potential for vibrations that cause noise.
Regular maintenance and inspection are also essential, as worn or damaged gears can significantly increase noise levels.
Balancing Gear Design Objectives
Designing gears involves finding a balance between strength, functionality, and noise reduction.
Achieving this balance requires careful consideration of each design component to ensure the gears perform efficiently and last long.
For instance, strengthening gears might involve using robust materials and thorough tooth design, which could conflict with noise reduction goals that might favor smoother but softer materials.
Engineers often use computer-aided design (CAD) software to model gears and simulate their operation under various conditions.
This tool helps predict the performance of gear designs and allows for adjustments before manufacturing.
By balancing these design objectives, engineers can optimize gears for specific applications, resulting in machines that operate efficiently without compromising performance.
Advancements in Gear Technology
Recent advancements in gear technology have made it possible to engineer gears with even greater efficiency and reduced noise.
Innovations in materials science and engineering practices continue to improve gear performance across various applications.
One major advancement is the use of advanced composite materials, which offer high strength-to-weight ratios and excellent wear resistance.
These materials can provide the necessary strength for gears while also contributing to quieter operation through better vibration damping.
Furthermore, the use of 3D printing technology allows for rapid prototyping and testing of gear designs, which speeds up the development process and makes it easier to iterate and refine gear features.
This technology enables the production of complex gear shapes that wouldn’t be possible with traditional manufacturing methods.
Digital twin technology, another cutting-edge tool, lets engineers create a virtual replica of the gear system.
This allows for real-time monitoring and proactive maintenance, reducing the likelihood of unexpected gear failures and optimizing noise levels.
Conclusion
Understanding the fundamentals of gears, including their strength design and noise reduction techniques, is crucial for engineers and manufacturers.
By focusing on the materials, tooth design, load conditions, and noise reduction techniques, engineers can ensure the reliable and efficient operation of gear systems.
Balancing these elements is key to producing gears that meet specific applications’ demands, foster innovation, and leverage advancements in technology.
As gear technology evolves, leveraging these insights will become integral to engineering success and the continued advancement of machinery.
資料ダウンロード
QCD調達購買管理クラウド「newji」は、調達購買部門で必要なQCD管理全てを備えた、現場特化型兼クラウド型の今世紀最高の購買管理システムとなります。
ユーザー登録
調達購買業務の効率化だけでなく、システムを導入することで、コスト削減や製品・資材のステータス可視化のほか、属人化していた購買情報の共有化による内部不正防止や統制にも役立ちます。
NEWJI DX
製造業に特化したデジタルトランスフォーメーション(DX)の実現を目指す請負開発型のコンサルティングサービスです。AI、iPaaS、および先端の技術を駆使して、製造プロセスの効率化、業務効率化、チームワーク強化、コスト削減、品質向上を実現します。このサービスは、製造業の課題を深く理解し、それに対する最適なデジタルソリューションを提供することで、企業が持続的な成長とイノベーションを達成できるようサポートします。
オンライン講座
製造業、主に購買・調達部門にお勤めの方々に向けた情報を配信しております。
新任の方やベテランの方、管理職を対象とした幅広いコンテンツをご用意しております。
お問い合わせ
コストダウンが利益に直結する術だと理解していても、なかなか前に進めることができない状況。そんな時は、newjiのコストダウン自動化機能で大きく利益貢献しよう!
(Β版非公開)