- お役立ち記事
- Fundamentals of sliding mode control and application to ensuring robustness and design
Fundamentals of sliding mode control and application to ensuring robustness and design
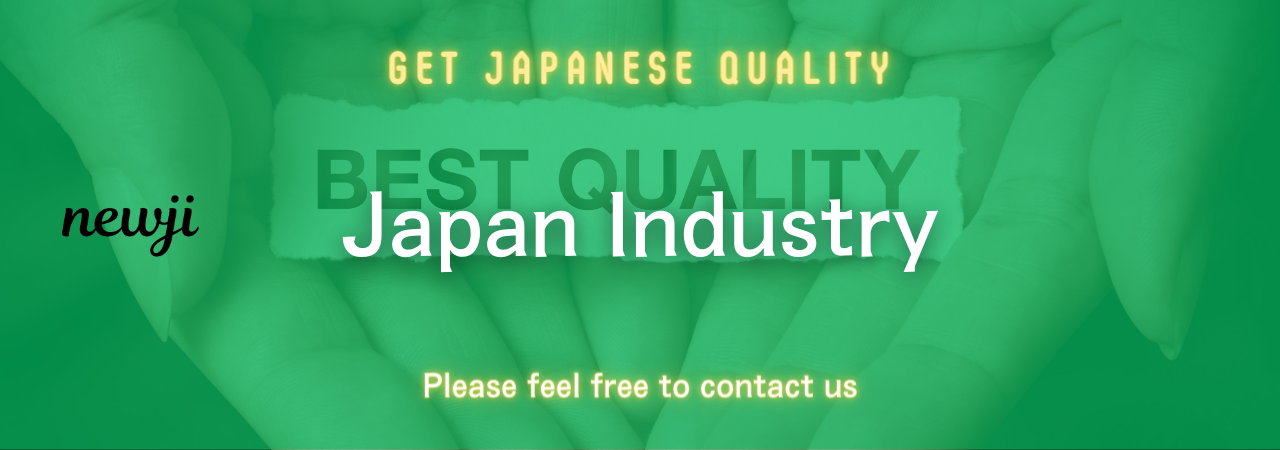
目次
Understanding Sliding Mode Control
Sliding mode control (SMC) is an advanced control technique used in engineering systems to ensure robustness and precision.
It is particularly important in applications where performance needs to be maintained despite variations or uncertainties in system parameters.
At its core, sliding mode control is about maintaining system stability and achieving desired behavior in a dynamic environment.
What is Sliding Mode Control?
Sliding mode control is a form of variable structure control system, which means the control strategy changes based on the state of the system.
The system switches between different control laws to keep the system on a “sliding surface.”
This sliding surface represents the desired state or behavior of the system.
Once the system reaches this sliding surface, it “slides” along it despite external disturbances or internal uncertainties.
This approach is highly effective in dealing with non-linear systems or systems with unknown parameters.
The robustness of SMC comes from its ability to reduce the system’s sensitivity to parameter variations, making it ideal for real-world applications where perfect models are rarely available.
How Sliding Mode Control Works
In sliding mode control, the main goal is to design a control law that maintains the system on the sliding surface.
This involves two key steps:
1. **Reaching Phase**: In this phase, the controller acts to bring the system state to the sliding surface from any initial condition.
2. **Sliding Phase**: Once the system state reaches the sliding surface, the controller ensures that the state ‘slides’ along the surface, maintaining the desired system behavior.
The sliding surface is typically defined in terms of the system states, and its design is crucial for ensuring the desired dynamics are achieved.
This is often done by choosing a suitable sliding variable, which is a function of the system state variables.
The design of the sliding surface and the control law needs to minimize the reaching phase while ensuring stable sliding motion.
Applications of Sliding Mode Control
Sliding mode control is applied across various fields, including robotics, automotive systems, aerospace, and electrical machines.
The following are some examples of its applications:
– **Robotics**: In robotic systems, SMC helps in precise position and force control, even when the robot interacts with unpredictable environments.
– **Automotive Systems**: Sliding mode control is used for vehicle stability control, ensuring that cars perform reliably under different driving conditions.
– **Aerospace**: In aircraft control systems, SMC aids in handling aerodynamic uncertainties and disturbances, enhancing stability and performance.
– **Electrical Drives**: It is used for controlling motor drives, ensuring efficiency and robustness against load variations.
Ensuring Robustness with Sliding Mode Control
One of the standout features of sliding mode control is its inherent robustness.
Robustness refers to the system’s ability to maintain performance under uncertain conditions.
Here, we discuss how SMC achieves this and the benefits it brings.
Handling Disturbances and Uncertainties
Sliding mode control is particularly effective in systems where disturbances and parameter variations are significant.
This robustness is achieved by the system’s motion along the sliding surface, where the control action compensates for any uncertainties.
This “chattering” effect in sliding mode control refers to the rapid switching action that occurs, which can sometimes lead to wear or mechanical stress.
However, control design techniques strive to minimize this effect while maintaining robustness.
Additionally, adaptive sliding mode control strategies can be implemented where the sliding surface adapts according to changes in system dynamics, further enhancing robustness.
Designing for Robustness
Designing a sliding mode controller involves setting up a control law that defines how the system should switch between different states to stay on the sliding surface.
The controller must be designed to handle the worst-case scenario of system disturbances.
This involves:
– **Defining Sliding Surface**: Choose a surface that reflects the desired behavior and dynamics of the system.
– **Control Law**: Develop a control law that ensures the system can reach and maintain the sliding phase despite disturbances.
– **Minimizing Chattering**: Implement strategies to reduce chattering, such as higher-order SMC or incorporating boundary layers.
The design process is iterative and involves extensive simulations and validation to ensure the controller meets the robustness requirements.
Design Techniques for Sliding Mode Control
Several techniques assist engineers and researchers in designing effective sliding mode controllers.
Understanding these can help in applying SMC effectively to varied systems.
Higher-order Sliding Modes
Higher-order sliding modes are an advancement that helps mitigate the chattering issue typical in traditional sliding mode controllers.
They achieve the same robustness but with smoother control signals.
This is particularly useful in systems where mechanical wear due to chattering is a concern.
Adaptive Sliding Mode Control
Adaptive sliding mode control involves real-time adjustment of the control parameters to respond to changing system dynamics or environmental conditions.
This approach improves robustness and performance by optimizing control in various operating conditions.
Integral Sliding Mode Control
Integral sliding mode control adds an integral action to the control law, improving precision and steady-state performance.
It’s effective in eliminating steady-state errors while maintaining the robustness of the original control design.
Conclusion
Sliding mode control is a powerful tool in the control engineer’s arsenal, offering robustness and precision in systems with uncertainties and non-linearities.
Understanding its fundamentals and applications can lead to better control strategies in various fields.
From robotics to aerospace, sliding mode control ensures systems remain stable and reliable even in unpredictable environments.
The continuous development of design techniques promises even more improvements in performance and application scope for future systems.
As engineers continue to explore and refine SMC methodologies, it will only become more significant in the design and control of complex, dynamic systems.
資料ダウンロード
QCD調達購買管理クラウド「newji」は、調達購買部門で必要なQCD管理全てを備えた、現場特化型兼クラウド型の今世紀最高の購買管理システムとなります。
ユーザー登録
調達購買業務の効率化だけでなく、システムを導入することで、コスト削減や製品・資材のステータス可視化のほか、属人化していた購買情報の共有化による内部不正防止や統制にも役立ちます。
NEWJI DX
製造業に特化したデジタルトランスフォーメーション(DX)の実現を目指す請負開発型のコンサルティングサービスです。AI、iPaaS、および先端の技術を駆使して、製造プロセスの効率化、業務効率化、チームワーク強化、コスト削減、品質向上を実現します。このサービスは、製造業の課題を深く理解し、それに対する最適なデジタルソリューションを提供することで、企業が持続的な成長とイノベーションを達成できるようサポートします。
オンライン講座
製造業、主に購買・調達部門にお勤めの方々に向けた情報を配信しております。
新任の方やベテランの方、管理職を対象とした幅広いコンテンツをご用意しております。
お問い合わせ
コストダウンが利益に直結する術だと理解していても、なかなか前に進めることができない状況。そんな時は、newjiのコストダウン自動化機能で大きく利益貢献しよう!
(Β版非公開)