- お役立ち記事
- Fundamentals of metal fatigue fracture and key points to prevent fatigue fracture
Fundamentals of metal fatigue fracture and key points to prevent fatigue fracture
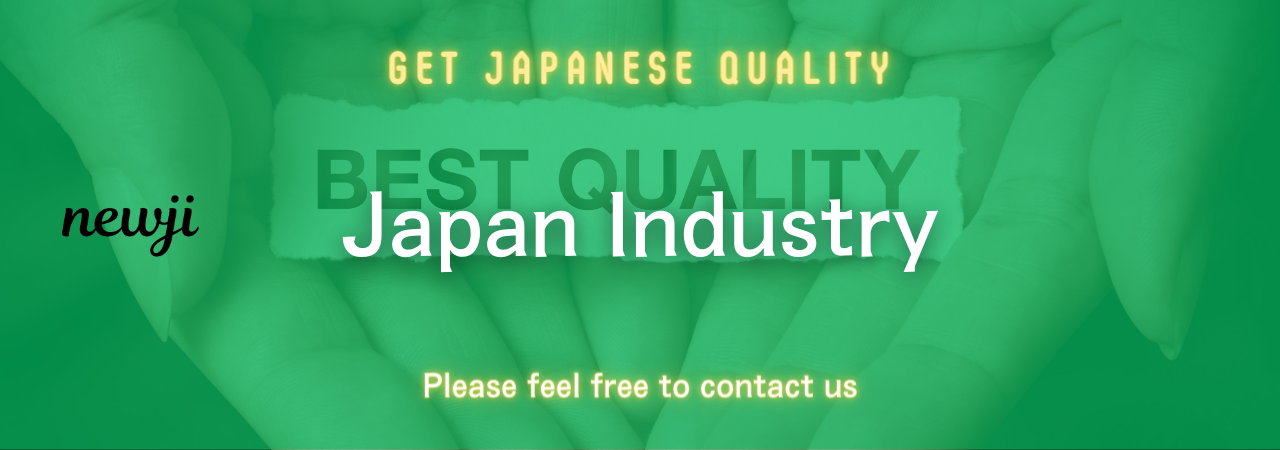
目次
Understanding Metal Fatigue Fracture
Metal fatigue refers to the progressive and localized structural damage that occurs when a material is subjected to cyclic loading.
Even if the stresses are below the ultimate tensile strength of the material, repeated loading leads to the initiation and propagation of cracks.
This ultimately results in a metal fatigue fracture, which can be sudden and catastrophic in nature.
The phenomenon of metal fatigue was first recognized in the 19th century when engineers observed unexpected failures in axle components.
Since then, it has become clear that understanding metal fatigue fracture is critical to ensuring the durability and safety of various structures and components.
Industries such as aerospace, automotive, and construction are particularly concerned with this phenomenon due to the potential consequences of a failure.
Causes of Metal Fatigue
Metal fatigue fracture is caused by cyclic stresses and strains experienced by a material over time.
These stresses can arise from various sources, including mechanical loads, thermal expansions, and vibrations.
The process of fatigue begins with crack initiation, often at stress concentrations such as notches, welds, or surface imperfections.
The cyclic nature of loading leads to the propagation of these cracks, often starting from microscopic levels.
Over repeated cycles, cracks can grow and reach a critical size, at which point the remaining uncracked section of the material can no longer support the load, leading to catastrophic failure.
Other factors contribute to metal fatigue, including:
1. **Material Type**: Different metals have varying levels of resistance to fatigue.
For example, aluminum alloys typically have lower fatigue resistance compared to steels.
2. **Surface Finish**: Rough surfaces or surface scratches can serve as stress concentrators, increasing the likelihood of crack initiation.
3. **Environmental Factors**: Corrosive environments can accelerate fatigue crack growth.
This phenomenon, known as corrosion fatigue, results from the interaction of mechanical stress and chemical reactions.
Phases of Metal Fatigue
Metal fatigue occurs in three distinct phases:
1. **Crack Initiation**: This is the initial stage where small cracks form.
These are often so small that they go undetected until they start to grow.
2. **Crack Propagation**: In this phase, the crack grows incrementally with each load cycle.
This is the longest phase in the fatigue life, where material toughness plays a crucial role.
3. **Fracture**: Once the crack reaches a critical length, the material can no longer sustain the load, leading to a sudden rupture.
This final phase happens very quickly.
Preventing Metal Fatigue Fracture
Preventing metal fatigue involves a comprehensive approach that includes material selection, design considerations, and regular maintenance.
The following are some key strategies to mitigate metal fatigue:
Material Selection
Choosing the right material is the first step in preventing metal fatigue.
Materials with high fatigue limits, such as certain steels and titanium alloys, are preferred for critical applications.
Additionally, materials with a fine grain structure can improve resistance to crack initiation and propagation.
Design Considerations
1. **Stress Concentration Reduction**: Design components with smooth surface finishes and avoid sharp corners or notches as these act as stress concentrators.
Fillets and radii can help distribute stress more evenly.
2. **Load Management**: Ensure that the design can accommodate the expected cyclic loads without exceeding material fatigue limits.
This might involve reinforcing critical components or using thicker materials.
3. **Fatigue Analysis**: Use computer-aided engineering software to simulate and analyze potential fatigue failure points in the design stage.
Regular Maintenance and Inspection
Routine inspections can identify early signs of fatigue, such as small surface cracks or deformation.
Nondestructive testing techniques like ultrasonic testing and dye penetrant inspection are effective in finding cracks that aren’t visible to the naked eye.
Regular maintenance can also involve surface treatments that improve fatigue resistance.
For example, shot peening introduces residual compressive stresses on the surface of a component, delaying crack initiation and growth.
Environmental Controls
Protecting materials from corrosive environments can significantly extend their fatigue life.
Applying coatings or using corrosion-resistant materials are common approaches.
Additionally, controlling temperature and humidity levels can help protect materials used in extreme environments.
Conclusion
Metal fatigue fracture is a critical phenomenon that can have serious implications if not properly managed.
Understanding its causes and phases is essential for designing and maintaining structures that are safe and durable.
By combining appropriate material selection, thoughtful design, regular maintenance, and environmental controls, the risk of fatigue-related failures can be significantly reduced.
Through continued research and innovation, engineers are developing even more effective methods to predict, manage, and prevent metal fatigue, ensuring the reliability of components across all industries.
資料ダウンロード
QCD調達購買管理クラウド「newji」は、調達購買部門で必要なQCD管理全てを備えた、現場特化型兼クラウド型の今世紀最高の購買管理システムとなります。
ユーザー登録
調達購買業務の効率化だけでなく、システムを導入することで、コスト削減や製品・資材のステータス可視化のほか、属人化していた購買情報の共有化による内部不正防止や統制にも役立ちます。
NEWJI DX
製造業に特化したデジタルトランスフォーメーション(DX)の実現を目指す請負開発型のコンサルティングサービスです。AI、iPaaS、および先端の技術を駆使して、製造プロセスの効率化、業務効率化、チームワーク強化、コスト削減、品質向上を実現します。このサービスは、製造業の課題を深く理解し、それに対する最適なデジタルソリューションを提供することで、企業が持続的な成長とイノベーションを達成できるようサポートします。
オンライン講座
製造業、主に購買・調達部門にお勤めの方々に向けた情報を配信しております。
新任の方やベテランの方、管理職を対象とした幅広いコンテンツをご用意しております。
お問い合わせ
コストダウンが利益に直結する術だと理解していても、なかなか前に進めることができない状況。そんな時は、newjiのコストダウン自動化機能で大きく利益貢献しよう!
(Β版非公開)