- お役立ち記事
- Practical points for effective FMEA procedures and prevention of quality problems
Practical points for effective FMEA procedures and prevention of quality problems
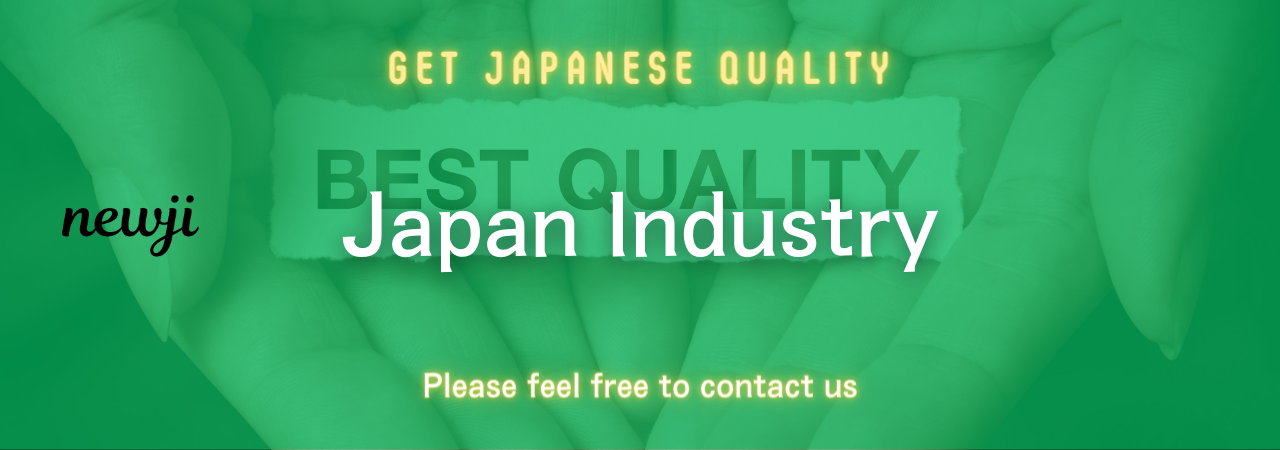
目次
Understanding FMEA: A Quick Overview
Failure Mode and Effects Analysis, commonly known as FMEA, is a systematic approach used to identify potential failure modes within a system, product, or process, and assess the risks associated with those failures.
It’s an essential tool in quality management and process improvement that allows businesses to prevent defects before they occur.
This practice is especially crucial in sectors where failures could lead to serious consequences, such as automotive, aerospace, and healthcare industries.
FMEA involves examining every component, subsystem, and process step, identifying where potential failures could occur, and predicting their impact on the product or process.
By analyzing this data, companies can prioritize which risks need immediate attention and develop strategies to mitigate or eliminate those potential problems.
Key Steps in the FMEA Process
1. Identify Failure Modes
The first step in the FMEA process is identifying all possible failure modes.
A failure mode represents any error or defect in a process, design, or item of equipment.
Brainstorming sessions with cross-functional teams can be instrumental in discovering various ways components or processes might fail.
2. Analyze Effects and Causes
Next, assess the effects of each identified failure mode.
Understanding the impact helps in determining the severity of the consequences should the failure occur.
Teams also need to analyze the root causes of these failures.
Tools like the “5 Whys” or cause-and-effect diagrams can be useful during this phase.
3. Assign Severity, Occurrence, and Detection Ratings
Each failure mode is further evaluated by assigning ratings for severity, occurrence, and detection.
Severity assesses the seriousness of the impact, occurrence estimates the probability of the failure happening, and detection evaluates how easily the failure can be detected before it reaches the customer.
These ratings are typically scaled from 1 to 10, with higher numbers indicating greater risk.
4. Calculate Risk Priority Number (RPN)
To prioritize risks, calculate the Risk Priority Number (RPN) by multiplying the severity, occurrence, and detection ratings.
The RPN helps in ranking the failure modes, with higher numbers indicating more critical issues that require immediate attention and preventive measures.
5. Develop Action Plans
Once the failure modes are prioritized, develop actionable plans to mitigate the impacts or reduce the likelihood of those failures.
This might include design changes, process improvements, or adding new controls and inspections.
Action plans should clearly define the tasks, responsible personnel, and timelines.
6. Implement and Monitor Improvements
After developing and executing the action plans, the next step is to implement these changes and closely monitor their effectiveness.
Regular reviews are necessary to ensure improvements are sustained and further adjustments are made as necessary.
It’s crucial to document these changes to maintain a comprehensive record of process improvements.
How FMEA Prevents Quality Problems
FMEA is an effective tool for preventing quality problems for several reasons:
– **Proactive Risk Management:** By identifying potential failures early, FMEA allows companies to take proactive steps to mitigate risks, preventing defects from reaching the customer.
– **Improvement Conversation:** The FMEA process fosters communication among different teams and departments, encouraging collaboration to improve process designs and implementations.
– **Resource Allocation:** By prioritizing issues based on their RPN, organizations can efficiently allocate resources to address the most critical problems first, leading to more effective problem-solving.
– **Continuous Improvement:** With a systematic review process, FMEA encourages continuous process analysis and improvement, adapting to new changes and reducing the chance of future failures.
Challenges and Best Practices in FMEA Implementation
While FMEA is a robust tool, companies often face challenges in its implementation.
Here are some best practices to ensure effective FMEA procedures:
1. Involve Cross-Functional Teams
To capture a holistic view of potential failure modes, involve members from different departments and disciplines.
This cross-functional approach brings diverse perspectives and insights into the analysis process.
2. Maintain Updated Documentation
Regularly update FMEA documentation to reflect any changes in design, process, or operational environments.
An outdated FMEA document can lead to misinformed decisions and overlooked risks.
3. Prioritize Based on Data
Use data-driven insights to prioritize failure modes, ensuring that subjective opinions do not skew risk assessments.
Base decisions on objective information and reliable statistical data as much as possible.
4. Training and Awareness
Provide adequate training for all team members involved in the FMEA process.
Awareness of terminology, procedures, and goals is crucial for effective implementation.
5. Reassess Regularly
Schedule regular FMEA reviews at periodic intervals or when significant changes to the process or design occur.
This ensures that new risks are identified and managed promptly.
Conclusion
FMEA is a vital component in the quality management toolkit, offering a structured way to identify, assess, and mitigate risks.
By following a systematic approach and adhering to best practices, organizations can dramatically reduce quality issues and improve customer satisfaction.
Implementing an effective FMEA procedure is not just about preventing failures but is also about fostering innovation and continuous improvement, ensuring sustainable success in the competitive market.
資料ダウンロード
QCD調達購買管理クラウド「newji」は、調達購買部門で必要なQCD管理全てを備えた、現場特化型兼クラウド型の今世紀最高の購買管理システムとなります。
ユーザー登録
調達購買業務の効率化だけでなく、システムを導入することで、コスト削減や製品・資材のステータス可視化のほか、属人化していた購買情報の共有化による内部不正防止や統制にも役立ちます。
NEWJI DX
製造業に特化したデジタルトランスフォーメーション(DX)の実現を目指す請負開発型のコンサルティングサービスです。AI、iPaaS、および先端の技術を駆使して、製造プロセスの効率化、業務効率化、チームワーク強化、コスト削減、品質向上を実現します。このサービスは、製造業の課題を深く理解し、それに対する最適なデジタルソリューションを提供することで、企業が持続的な成長とイノベーションを達成できるようサポートします。
オンライン講座
製造業、主に購買・調達部門にお勤めの方々に向けた情報を配信しております。
新任の方やベテランの方、管理職を対象とした幅広いコンテンツをご用意しております。
お問い合わせ
コストダウンが利益に直結する術だと理解していても、なかなか前に進めることができない状況。そんな時は、newjiのコストダウン自動化機能で大きく利益貢献しよう!
(Β版非公開)