- お役立ち記事
- Procurement requirements when introducing AI robots for production lines
Procurement requirements when introducing AI robots for production lines
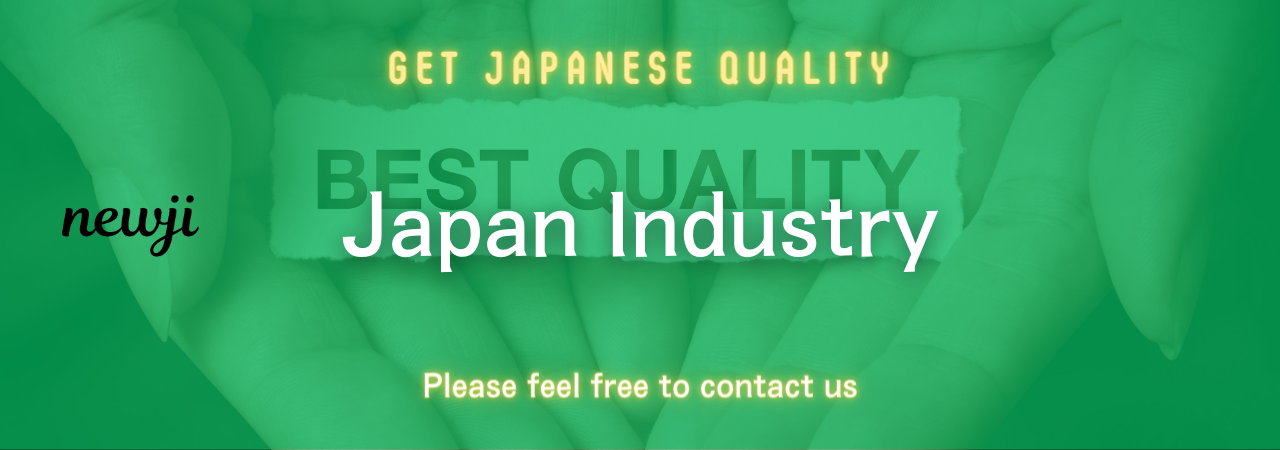
目次
Understanding Procurement Requirements for AI Robots
Introducing AI robots to production lines can revolutionize the way industries operate, bringing about increased efficiency, cost savings, and improved product quality.
However, integrating AI technology into production requires careful planning and understanding of procurement requirements.
In this guide, we’ll explore the key considerations and steps involved in the procurement process for AI robots.
Identifying Your Production Line Needs
Before commencing the procurement process, it’s crucial to perform a detailed assessment of your production line needs.
Identify the tasks that could benefit from automation and pinpoint areas where AI robots can enhance productivity.
Evaluate the current workflow and determine the desired outcomes, such as reduced cycle times or improved product precision.
Understanding these needs will help guide the decision-making process and ensure the right AI technology is selected.
Setting a Budget and Assessing Costs
Budgeting is an essential component of procurement.
Determine how much you are willing to invest in AI robots and associated technologies. Consider not only the initial purchase cost but also ongoing expenses, such as maintenance, training, and potential upgrades.
It’s wise to assess the potential return on investment by calculating cost savings from increased productivity and reduced labor costs. With a clear budget in place, you can prioritize solutions that offer the best value for your investment.
Researching AI Robot Suppliers
Selecting a reputable AI robot supplier is crucial for a successful procurement process.
Research various suppliers to compare their offerings, reputation, and expertise in the industry. Look for suppliers with a proven track record of delivering reliable and innovative AI solutions.
It’s a good idea to reach out to other businesses that have successfully integrated AI robots into their production lines. Their insights and experiences can guide you toward making informed choices.
Evaluating Robot Capabilities and Specifications
Once you’ve identified potential suppliers, evaluate the capabilities and specifications of the AI robots they offer.
Consider factors such as speed, precision, adaptability, and scalability. It’s essential to ensure the robots can efficiently perform the tasks required by your production line.
Understand the software and AI algorithms that power the robots, as well as their ability to integrate with existing systems and future technologies.
Compliance and Safety Regulations
Compliance with safety and industry regulations is a critical aspect of procuring AI robots.
Familiarize yourself with relevant standards and ensure that the robots you’re considering meet all safety and compliance requirements. This includes verification of safety certifications, testing protocols, and adherence to ethical guidelines in AI deployment.
Robust compliance ensures not only the safety of human workers but also the sustainability of production operations.
Training and Support Services
The successful introduction of AI robots requires comprehensive training and ongoing support services.
Evaluate the training programs offered by suppliers and determine the level of support they provide post-implementation. Training should cover operations, maintenance, and troubleshooting to maximize robot performance and minimize downtime.
Continuous support services ensure that any issues arising are swiftly addressed, maintaining seamless production operations.
Scalability and Future Technology Considerations
When procuring AI robots, it’s vital to consider scalability and future technological advancements.
Choose robots that can grow with your business and adapt to emerging trends. This flexibility ensures that your initial investment is protected and can accommodate possible expansions or changes in production line needs.
It’s advantageous to engage suppliers with a forward-thinking approach to technology, ensuring ongoing innovation in their offerings.
Finalizing Contracts and Agreements
Once all factors have been carefully considered and evaluated, the procurement process culminates in finalizing contracts and agreements with your chosen supplier.
Ensure all terms, conditions, and responsibilities are clearly outlined.
Key contract elements include deliverables, timelines, pricing, service agreements, and warranties. Transparency in agreements protects both parties and sets the stage for a productive long-term collaboration.
Implementing AI Robots on the Production Line
With contracts in place, begin the process of integrating AI robots into your production line.
Develop a structured implementation plan that includes timelines, resource allocation, and coordination with stakeholders.
It’s essential to conduct pilot tests to confirm that the robots function correctly and meet the anticipated objectives.
Adjustments and optimizations based on initial results help in refining the integration process.
Monitoring and Optimizing Performance
Post-implementation, closely monitor the performance of AI robots and their impact on production line efficiency.
Analyze key metrics to ensure desired outcomes are achieved, and be prepared to make necessary adjustments. Gather feedback from workers and managers to identify areas for improvement.
Regular maintenance and software updates are crucial for optimizing performance and ensuring long-term operational success.
Conclusion
Procuring AI robots for production lines is an investment that can significantly enhance productivity and efficiency.
By understanding and addressing procurement requirements, businesses can make informed decisions that lead to successful integration and optimal performance.
With careful planning, research, and execution, AI robots can become a transformative force in modern industrial operations.
資料ダウンロード
QCD調達購買管理クラウド「newji」は、調達購買部門で必要なQCD管理全てを備えた、現場特化型兼クラウド型の今世紀最高の購買管理システムとなります。
ユーザー登録
調達購買業務の効率化だけでなく、システムを導入することで、コスト削減や製品・資材のステータス可視化のほか、属人化していた購買情報の共有化による内部不正防止や統制にも役立ちます。
NEWJI DX
製造業に特化したデジタルトランスフォーメーション(DX)の実現を目指す請負開発型のコンサルティングサービスです。AI、iPaaS、および先端の技術を駆使して、製造プロセスの効率化、業務効率化、チームワーク強化、コスト削減、品質向上を実現します。このサービスは、製造業の課題を深く理解し、それに対する最適なデジタルソリューションを提供することで、企業が持続的な成長とイノベーションを達成できるようサポートします。
オンライン講座
製造業、主に購買・調達部門にお勤めの方々に向けた情報を配信しております。
新任の方やベテランの方、管理職を対象とした幅広いコンテンツをご用意しております。
お問い合わせ
コストダウンが利益に直結する術だと理解していても、なかなか前に進めることができない状況。そんな時は、newjiのコストダウン自動化機能で大きく利益貢献しよう!
(Β版非公開)