- お役立ち記事
- Main types and causes of injection molding troubles
Main types and causes of injection molding troubles
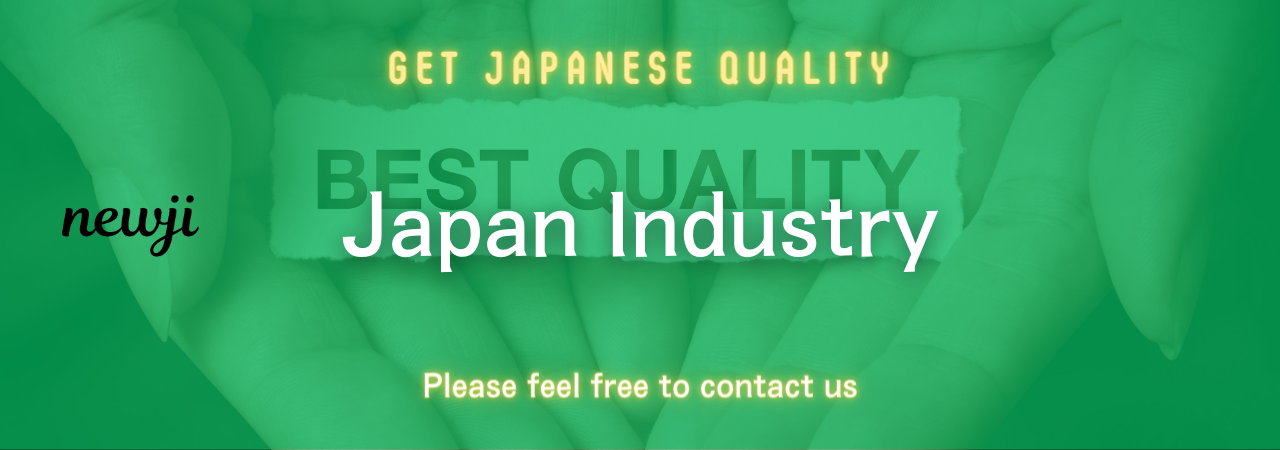
目次
Understanding Injection Molding
Injection molding is a manufacturing process used to create a wide variety of plastic products.
This technique involves injecting molten materials into a mold to form a specific shape.
It is widely used in industries such as automotive, consumer goods, and medical equipment due to its efficiency and ability to produce high-quality parts in large volumes.
However, like any manufacturing process, injection molding is not without its issues.
Understanding the types of troubles that can occur and their causes can help manufacturers mitigate risks and improve product quality.
Common Injection Molding Issues
Despite its many advantages, injection molding can encounter several types of issues.
Here are some of the most common problems that manufacturers face and their potential causes.
1. Warping
Warping refers to the distortion or bending of a molded part, leading to deviations from the intended design.
This problem occurs when there is uneven shrinkage during the cooling phase.
Causes of Warping
– Uneven Cooling: When different parts of the mold cool at different rates, it can lead to uneven shrinkage.
– Incorrect Mold Temperature: If the mold is either too hot or too cold, it can cause improper cooling.
– Improper Material Choices: Using materials with high shrinkage rates without compensating can lead to warping.
2. Sink Marks
Sink marks appear as depressions on the surface of a molded part.
They are generally circular and occur when the inner part of the material cools and shrinks slowly.
Causes of Sink Marks
– Thick Sections: Excessive material thickness can cause the outer layer to harden while the inner layers remain molten.
– Insufficient Cooling Time: Not allowing enough time for proper cooling can lead to shrinkage.
– Low Injection Pressure: If the pressure applied is insufficient, it leads to inadequate packing of materials.
3. Short Shots
A short shot is when the mold cavity is not completely filled with the material, resulting in an incomplete product.
This defect can lead to weak parts and is undesirable in finished products.
Causes of Short Shots
– Low Material Temperature: If the material is not heated adequately, it will not flow properly into the mold.
– Mold Flow Resistance: Complex molds with high resistance levels can hinder complete filling.
– Injection Speed: Slow injection speed prevents the material from filling the mold in time.
4. Flash
Flash occurs when excess material escapes and solidifies outside the desired shape.
This defect can cause aesthetic issues and require extra post-processing.
Causes of Flash
– High Injection Pressure: Excess pressure can force material out of the mold cavity.
– Wear and Tear on Mold: Gaps in the mold due to wear or damage allow excess material to escape.
– Incorrect Clamp Force: Insufficient clamping may permit leakage of the molten material.
5. Jetting
Jetting is a defect where a part of the molded product has a twisted or ropey appearance.
It is caused when the material flows rapidly in a narrow stream rather than spreading evenly.
Causes of Jetting
– High Injection Speed: Rapid injection causes the material to shoot directly and form uneven layers.
– Poor Gate Design: Improper gate location or size can lead to turbulent flow.
– Low Material Temperature: Inadequate heating results in a less fluid material that doesn’t flow smoothly.
Preventing Injection Molding Problems
To prevent these troubles, manufacturers should adopt best practices throughout the injection molding process.
Consistent Mold Design
A well-designed mold is crucial for preventing many common issues.
Ensuring uniform wall thickness and optimizing flow paths can reduce defects like warping and sink marks.
Proper Material Selection
Select materials based on the product’s design requirements and characteristics.
Different materials have different properties in terms of cooling and shrinkage.
Optimized Process Parameters
Monitor and adjust injection speed, temperature, pressure, and cooling time.
Fine-tuning these parameters helps in achieving desired outcomes and minimizing defects.
Regular Maintenance
Perform routine checks on molds to address wear and tear promptly.
This ensures that the mold maintains its precision and performs consistently.
Enhanced Operator Training
Training operators on the latest techniques and technologies can also prevent many issues.
A skilled operator can identify potential problems early and make necessary adjustments.
Conclusion
While injection molding is an efficient and versatile manufacturing method, it is not without challenges.
By understanding the common types of troubles and their causes, manufacturers can take proactive steps to minimize defects and improve product quality.
Implementing proper practices and maintaining attention to detail can lead to more successful injection molding operations and superior finished products.
資料ダウンロード
QCD調達購買管理クラウド「newji」は、調達購買部門で必要なQCD管理全てを備えた、現場特化型兼クラウド型の今世紀最高の購買管理システムとなります。
ユーザー登録
調達購買業務の効率化だけでなく、システムを導入することで、コスト削減や製品・資材のステータス可視化のほか、属人化していた購買情報の共有化による内部不正防止や統制にも役立ちます。
NEWJI DX
製造業に特化したデジタルトランスフォーメーション(DX)の実現を目指す請負開発型のコンサルティングサービスです。AI、iPaaS、および先端の技術を駆使して、製造プロセスの効率化、業務効率化、チームワーク強化、コスト削減、品質向上を実現します。このサービスは、製造業の課題を深く理解し、それに対する最適なデジタルソリューションを提供することで、企業が持続的な成長とイノベーションを達成できるようサポートします。
オンライン講座
製造業、主に購買・調達部門にお勤めの方々に向けた情報を配信しております。
新任の方やベテランの方、管理職を対象とした幅広いコンテンツをご用意しております。
お問い合わせ
コストダウンが利益に直結する術だと理解していても、なかなか前に進めることができない状況。そんな時は、newjiのコストダウン自動化機能で大きく利益貢献しよう!
(Β版非公開)