- お役立ち記事
- Unlocking the Art of Japanese Manufacturing: The Molding Process Explained
Unlocking the Art of Japanese Manufacturing: The Molding Process Explained
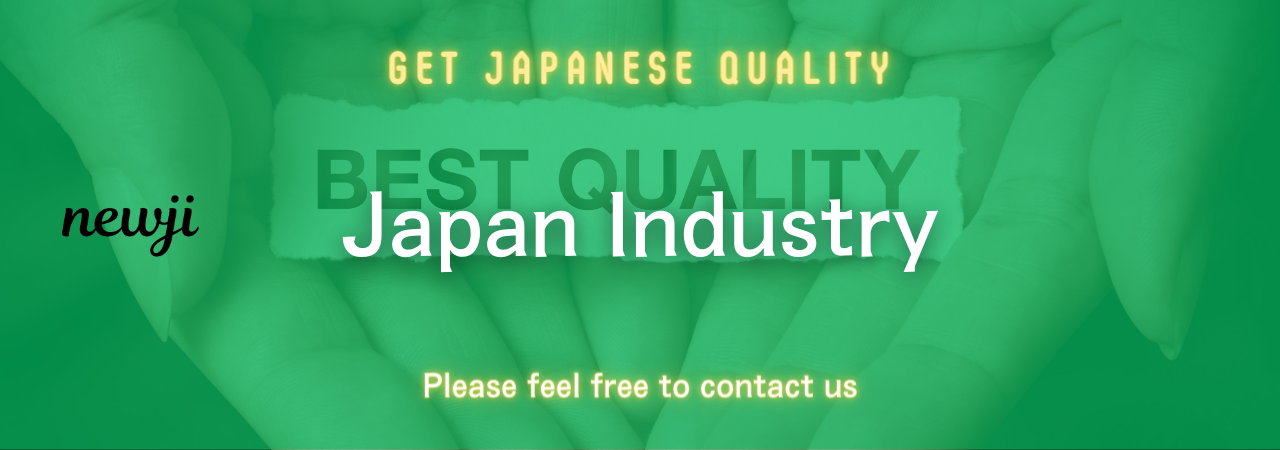
目次
Introduction to Japanese Manufacturing Excellence
Japanese manufacturing is renowned worldwide for its precision, quality, and efficiency. Central to this reputation is the molding process, a fundamental technique used in various industries, from automotive to electronics. Understanding the intricacies of the molding process in Japanese manufacturing can provide valuable insights into their success. This article delves into the art of Japanese molding, exploring practical aspects from procurement and purchasing perspectives, the advantages and disadvantages, supplier negotiation techniques, market conditions, and best practices.
The Molding Process in Japanese Manufacturing
Types of Molding Techniques
Japanese manufacturers employ a variety of molding techniques to meet diverse production needs. The most common types include injection molding, blow molding, compression molding, and rotational molding. Each technique has its specific applications and benefits, allowing manufacturers to choose the most suitable method for their products.
Precision and Quality Control
Precision is a cornerstone of Japanese manufacturing. In the molding process, this is achieved through meticulous control of every stage, from material selection to final product inspection. Advanced machinery and sophisticated quality control systems ensure that each molded part meets stringent quality standards. This emphasis on precision minimizes defects and enhances the overall reliability of the products.
Procurement and Purchasing in Japanese Molding
Supplier Selection and Evaluation
Selecting the right suppliers is crucial in the molding process. Japanese companies prioritize suppliers who demonstrate high quality, reliability, and the ability to innovate. The evaluation process often includes rigorous assessments of the supplier’s manufacturing capabilities, quality control systems, and financial stability. Building long-term relationships with trusted suppliers ensures a consistent supply of high-quality materials.
Strategic Sourcing
Strategic sourcing involves identifying and connecting with suppliers who can provide the best value in terms of cost, quality, and delivery times. Japanese manufacturers often engage in strategic sourcing to secure materials at competitive prices without compromising on quality. This approach involves negotiating favorable terms and fostering collaborative relationships with suppliers.
Inventory Management
Effective inventory management is essential to maintain seamless production processes. Japanese companies utilize just-in-time (JIT) inventory systems to minimize waste and reduce holding costs. By coordinating closely with suppliers, they ensure that materials arrive precisely when needed, enhancing the efficiency of the molding process.
Advantages of Japanese Molding Techniques
High Quality and Precision
Japanese molding techniques are synonymous with high quality and precision. The meticulous attention to detail in every stage of the process ensures that the final products meet the highest standards. This focus on quality not only satisfies customer expectations but also enhances the brand reputation.
Efficiency and Productivity
Efficiency is a key advantage of Japanese molding. Advanced automation and streamlined workflows reduce production times and increase output. This high level of productivity allows companies to meet tight deadlines and respond swiftly to market demands.
Innovation and Technology
Japanese manufacturers are at the forefront of technological innovation in molding. Continuous investment in research and development leads to the adoption of cutting-edge machinery and techniques. This commitment to innovation drives improvements in product design, manufacturing processes, and overall production efficiency.
Disadvantages and Challenges
High Initial Investment
While Japanese molding techniques offer numerous benefits, they often require significant initial investment in advanced machinery and technology. This can be a barrier for smaller companies or those with limited capital.
Complexity of Processes
The high level of precision and quality control in Japanese molding processes can make them complex and difficult to manage. This complexity requires skilled labor and comprehensive training programs, adding to the overall costs.
Supply Chain Dependencies
Relying on a network of specialized suppliers can make Japanese manufacturers vulnerable to supply chain disruptions. Any delays or issues with suppliers can have significant impacts on production schedules and overall efficiency.
Supplier Negotiation Techniques
Building Long-term Relationships
Japanese companies emphasize building long-term, trust-based relationships with their suppliers. This approach fosters collaboration and mutual support, leading to more favorable negotiation outcomes. Strong relationships can also result in better terms, such as discounts, priority service, and exclusive agreements.
Transparent Communication
Clear and transparent communication is vital during negotiations. Japanese firms ensure that all parties understand the terms and expectations, reducing the risk of misunderstandings and conflicts. This transparency helps in negotiating fair and balanced agreements.
Win-win Strategies
Japanese negotiation techniques focus on creating win-win scenarios where both parties benefit. By understanding the supplier’s needs and constraints, companies can propose solutions that provide value to both sides, ensuring sustainable and profitable partnerships.
Market Conditions and Trends
Global Supply Chain Dynamics
Global supply chain dynamics significantly impact Japanese manufacturing. Factors such as geopolitical tensions, trade policies, and global economic conditions influence the availability and cost of materials. Japanese companies must remain agile and adaptable to navigate these challenges effectively.
Sustainability and Environmental Considerations
There is an increasing emphasis on sustainability in the molding process. Japanese manufacturers are adopting eco-friendly materials and processes to reduce their environmental footprint. This trend not only meets regulatory requirements but also aligns with consumer demand for sustainable products.
Technological Advancements
Rapid technological advancements continue to shape the molding landscape. Innovations such as 3D printing, smart manufacturing, and the Internet of Things (IoT) are being integrated into the production processes. Staying abreast of these technologies is essential for maintaining competitiveness.
Best Practices in Japanese Molding
Continuous Improvement (Kaizen)
Continuous improvement, or Kaizen, is a fundamental principle in Japanese manufacturing. Companies regularly assess and refine their processes to enhance efficiency, reduce waste, and improve quality. This ongoing commitment to improvement ensures that manufacturing practices remain optimal and competitive.
Lean Manufacturing
Lean manufacturing principles are extensively applied in Japanese molding processes. By eliminating non-value-added activities, optimizing workflows, and fostering a culture of efficiency, companies achieve higher productivity and lower costs. Lean practices also enhance flexibility and responsiveness to market changes.
Employee Training and Development
Investing in employee training and development is crucial for maintaining high standards in the molding process. Japanese companies prioritize the skill development of their workforce, ensuring that employees are proficient in the latest techniques and technologies. A well-trained workforce contributes to consistent quality and innovation.
Advanced Quality Control Systems
Implementing advanced quality control systems is essential for maintaining the high standards associated with Japanese manufacturing. These systems include automated inspection tools, real-time monitoring, and comprehensive quality assurance protocols. Rigorous quality control ensures that defects are minimized and products meet or exceed customer expectations.
Case Studies: Success Stories in Japanese Molding
Automotive Industry
Japanese automotive manufacturers, such as Toyota and Honda, utilize advanced molding techniques to produce high-quality components. Their commitment to precision and efficiency has resulted in reliable and long-lasting vehicles that are highly regarded worldwide. Continuous collaboration with suppliers ensures that parts meet stringent performance standards.
Electronics Sector
In the electronics sector, companies like Sony and Panasonic leverage innovative molding processes to create intricate and durable components. The integration of automation and smart technologies enhances their ability to produce complex parts with exceptional accuracy, meeting the demanding specifications of modern electronic devices.
Consumer Goods
Japanese manufacturers of consumer goods, such as Unilever and Panasonic, apply best practices in molding to produce a wide range of products, from household appliances to personal care items. Their focus on quality and efficiency ensures that products are both reliable and competitively priced.
Future Directions in Japanese Molding
Embracing Industry 4.0
Japanese manufacturers are increasingly adopting Industry 4.0 technologies, including automation, data analytics, and artificial intelligence, to enhance their molding processes. These technologies enable greater flexibility, real-time monitoring, and predictive maintenance, driving further improvements in efficiency and quality.
Sustainable Manufacturing Practices
The future of Japanese molding lies in sustainable manufacturing practices. Companies are investing in eco-friendly materials, energy-efficient machinery, and waste reduction strategies to minimize their environmental impact. This commitment to sustainability not only meets regulatory standards but also aligns with global trends towards greener production.
Global Expansion and Collaboration
Japanese manufacturers are expanding their global presence and collaborating with international partners to enhance their molding capabilities. By leveraging global expertise and resources, they can innovate more effectively and respond to diverse market needs, maintaining their competitive edge in the global marketplace.
Conclusion
Japanese manufacturing continues to set the benchmark for quality, efficiency, and innovation in the molding industry. By focusing on precision, strategic procurement, and continuous improvement, Japanese companies have mastered the art of molding, delivering products that meet the highest standards. While challenges such as high initial investments and supply chain dependencies exist, the benefits of Japanese molding techniques—ranging from superior quality to operational efficiency—are undeniable. As the industry evolves with technological advancements and sustainability practices, Japanese manufacturers remain well-positioned to lead the way, offering valuable lessons and strategies for success in the global market.
資料ダウンロード
QCD調達購買管理クラウド「newji」は、調達購買部門で必要なQCD管理全てを備えた、現場特化型兼クラウド型の今世紀最高の購買管理システムとなります。
ユーザー登録
調達購買業務の効率化だけでなく、システムを導入することで、コスト削減や製品・資材のステータス可視化のほか、属人化していた購買情報の共有化による内部不正防止や統制にも役立ちます。
NEWJI DX
製造業に特化したデジタルトランスフォーメーション(DX)の実現を目指す請負開発型のコンサルティングサービスです。AI、iPaaS、および先端の技術を駆使して、製造プロセスの効率化、業務効率化、チームワーク強化、コスト削減、品質向上を実現します。このサービスは、製造業の課題を深く理解し、それに対する最適なデジタルソリューションを提供することで、企業が持続的な成長とイノベーションを達成できるようサポートします。
オンライン講座
製造業、主に購買・調達部門にお勤めの方々に向けた情報を配信しております。
新任の方やベテランの方、管理職を対象とした幅広いコンテンツをご用意しております。
お問い合わせ
コストダウンが利益に直結する術だと理解していても、なかなか前に進めることができない状況。そんな時は、newjiのコストダウン自動化機能で大きく利益貢献しよう!
(Β版非公開)