- お役立ち記事
- Unlocking the Secrets of Japanese Manufacturing: How the “Conveyor” Revolutionizes Efficiency
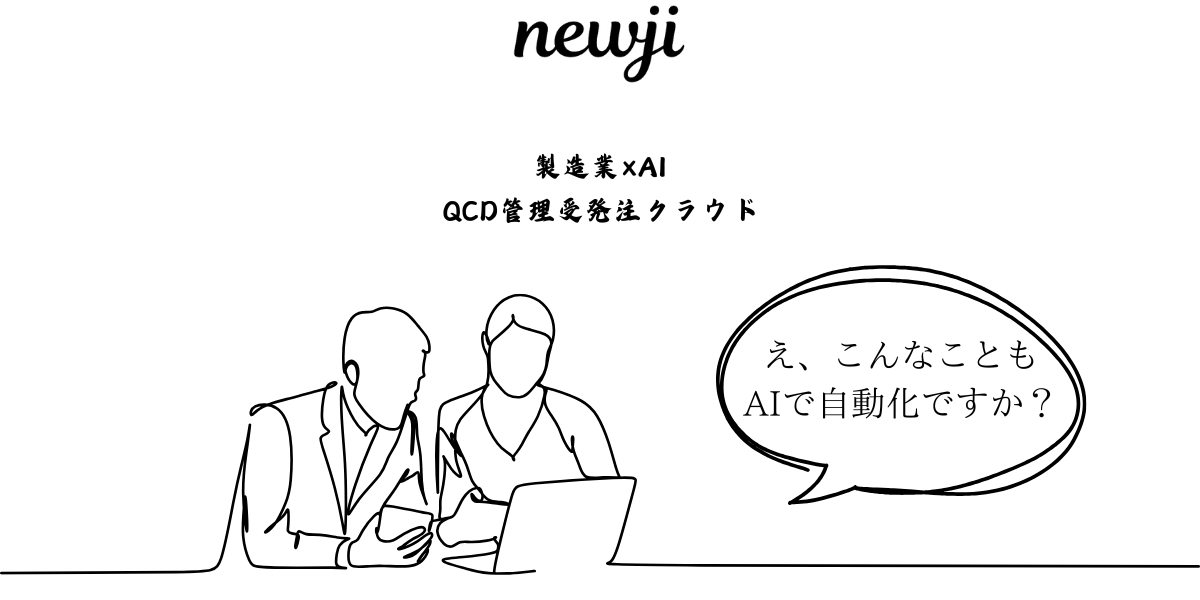
Unlocking the Secrets of Japanese Manufacturing: How the “Conveyor” Revolutionizes Efficiency
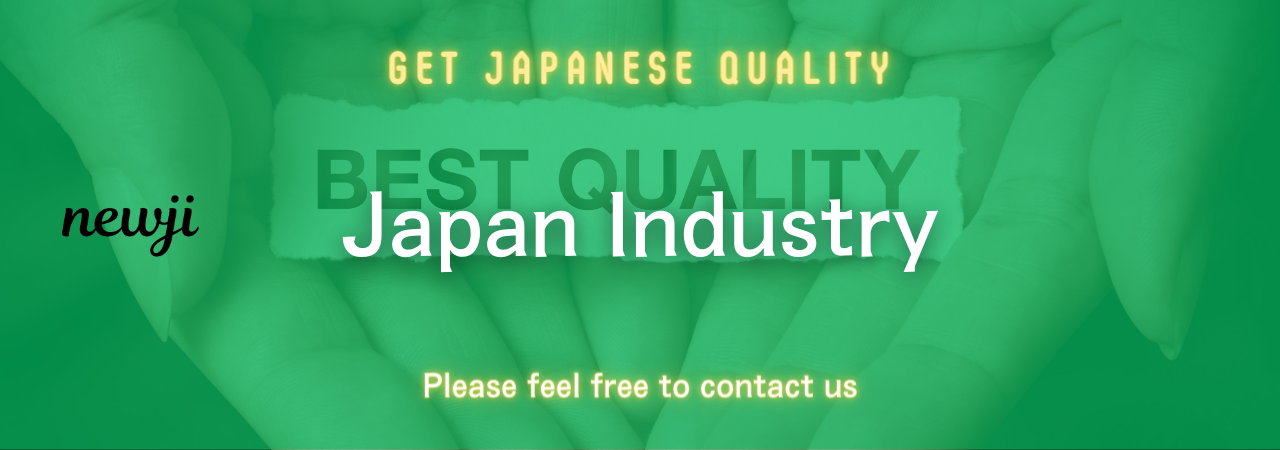
目次
Introduction to Japanese Manufacturing Excellence
Japanese manufacturing has long been celebrated for its remarkable efficiency, precision, and innovation. Central to this success is the seamless integration of advanced systems and methodologies that streamline production processes. One such pivotal element is the “Conveyor” system, a cornerstone in enhancing manufacturing efficiency. Understanding the intricacies of Japanese conveyor systems offers valuable insights into achieving superior operational performance and competitive advantage in the global market.
The Role of Conveyor Systems in Japanese Manufacturing
Conveyor systems in Japan are not merely tools for moving materials from one point to another. They embody a philosophy of continuous improvement and operational excellence. These systems are meticulously designed to align with the principles of lean manufacturing, minimizing waste and maximizing productivity.
Integration with Lean Manufacturing
Lean manufacturing focuses on eliminating non-value-added activities to enhance efficiency. Japanese conveyor systems are tailored to support this by ensuring smooth material flow, reducing bottlenecks, and facilitating real-time monitoring and adjustments. This seamless integration allows for a more responsive and adaptable production environment.
Automation and Precision
Automation is a hallmark of Japanese manufacturing. Conveyor systems are equipped with advanced sensors and control mechanisms that ensure precise movement and handling of materials. This automation reduces human error, enhances accuracy, and allows for a higher degree of customization in production processes.
Advantages of Implementing Conveyor Systems
Adopting conveyor systems in manufacturing operations offers numerous benefits that contribute to overall efficiency and productivity.
Enhanced Efficiency
Conveyor systems automate the material handling process, significantly reducing the time required to move items between different stages of production. This automation accelerates the overall production cycle, leading to increased output without compromising quality.
Improved Quality Control
With precise movement and handling, conveyor systems minimize the risk of damage to materials and products during transit. Additionally, the integration of quality checkpoints along the conveyor ensures that defects are detected and addressed promptly, maintaining high standards of product quality.
Cost Reduction
By streamlining the production process and reducing the need for manual labor, conveyor systems help lower operational costs. The reduction in labor costs, coupled with increased production efficiency, results in significant cost savings over time.
Flexibility and Scalability
Conveyor systems can be customized to meet the specific needs of different manufacturing processes. They offer flexibility in terms of design and layout, allowing for easy reconfiguration as production requirements evolve. This scalability ensures that the system can grow alongside the business, accommodating increased production demands without substantial additional investments.
Challenges and Disadvantages
While conveyor systems offer numerous advantages, their implementation is not without challenges. Understanding these potential drawbacks is essential for making informed decisions.
High Initial Investment
The installation of conveyor systems requires a substantial upfront investment. Costs associated with purchasing, installing, and integrating the system into existing operations can be significant, particularly for small to medium-sized enterprises.
Maintenance and Downtime
Conveyor systems, being mechanical and electrical systems, are susceptible to wear and tear. Regular maintenance is essential to ensure optimal performance and prevent unexpected downtime. Maintenance costs and the potential for production interruptions can pose challenges to consistent operations.
Lack of Flexibility in Some Systems
While many conveyor systems are designed to be flexible, some may lack the adaptability required for highly dynamic production environments. This rigidity can limit the ability to quickly adjust to changes in production demands or introduce new product lines.
Supplier Negotiation Techniques in the Japanese Market
Negotiating with Japanese suppliers requires a nuanced understanding of cultural norms and business practices. Effective negotiation strategies can lead to favorable terms and long-term partnerships.
Building Trust and Relationships
In Japan, building a strong, trust-based relationship is foundational to successful business dealings. Taking the time to establish rapport, understanding the supplier’s values, and demonstrating commitment to a long-term partnership are crucial steps in the negotiation process.
Respect for Hierarchical Structures
Japanese businesses often operate within hierarchical structures. Recognizing and respecting these hierarchies during negotiations can facilitate smoother interactions and demonstrate professionalism.
Emphasis on Quality and Precision
Japanese suppliers prioritize quality and precision. Highlighting mutual commitments to high standards and detailing how both parties can achieve these goals can strengthen negotiation positions.
Patience and Persistence
Negotiations in Japan may take longer compared to Western practices. Exhibiting patience and persistence, without appearing impatient or aggressive, aligns with Japanese business etiquette and can lead to more successful outcomes.
Understanding Market Conditions for Japanese Conveyor Systems
Navigating the market for Japanese conveyor systems involves understanding the current trends, demand dynamics, and competitive landscape.
Technological Advancements
Japan is at the forefront of technological innovation in manufacturing. Conveyor systems incorporate cutting-edge technologies such as IoT integration, AI-driven analytics, and advanced automation to enhance performance and adaptability.
Competitive Pricing and Value Proposition
While Japanese conveyor systems are known for their quality and reliability, they may be priced higher than alternatives from other regions. Evaluating the value proposition, considering long-term benefits and cost savings, is essential when assessing the competitiveness of these systems.
Global Supply Chain Considerations
Global supply chain challenges, such as fluctuations in demand, transportation delays, and geopolitical factors, can impact the availability and cost of Japanese conveyor systems. Staying informed about these dynamics helps in planning and mitigating potential disruptions.
Sustainability and Environmental Regulations
Increasing emphasis on sustainability and environmental responsibility influences the design and operation of conveyor systems. Japanese manufacturers are incorporating eco-friendly materials and energy-efficient technologies to comply with stringent environmental regulations and meet market demand for sustainable solutions.
Best Practices for Procuring and Implementing Conveyor Systems
Ensuring successful procurement and implementation of conveyor systems involves adhering to best practices that maximize efficiency and minimize risks.
Comprehensive Needs Assessment
Begin by conducting a thorough assessment of your production processes to identify specific requirements. Understanding the types of materials handled, production volume, space constraints, and desired automation levels guides the selection of the most suitable conveyor system.
Selecting the Right Supplier
Choose suppliers with a proven track record and expertise in conveyor systems. Evaluate their capabilities, quality standards, and after-sales support. Building a partnership with a reliable supplier ensures ongoing support and facilitates future upgrades or expansions.
Customization and Flexibility
Opt for conveyor systems that offer customization to accommodate unique production needs. Flexible systems that can be easily reconfigured or expanded provide long-term value and adaptability as your manufacturing requirements evolve.
Integration with Existing Systems
Ensure that the new conveyor system can seamlessly integrate with your current machinery and software. Compatibility minimizes disruptions during installation and allows for efficient data exchange and process synchronization.
Training and Support
Invest in comprehensive training for your staff to operate and maintain the conveyor system effectively. Access to technical support and maintenance services from the supplier enhances system reliability and longevity.
Continuous Monitoring and Improvement
Implement systems for continuous monitoring of conveyor performance. Utilizing data analytics and feedback loops allows for proactive maintenance, performance optimization, and ongoing improvements to sustain high efficiency levels.
Case Studies: Success Stories in Japanese Conveyor Implementation
Examining real-world examples of successful conveyor system implementations in Japanese manufacturing provides practical insights and inspiration.
Automotive Industry Automation
A leading Japanese automaker integrated advanced conveyor systems across its assembly lines, resulting in a 30% increase in production efficiency. The seamless material flow and real-time monitoring facilitated rapid identification and resolution of bottlenecks, enhancing overall operational performance.
Electronics Manufacturing Precision
A Japanese electronics manufacturer adopted highly precise conveyor systems to handle delicate components with minimal risk of damage. The enhanced handling precision led to a 20% reduction in product defects and significantly improved quality control outcomes.
Food Processing Efficiency
A food processing company in Japan implemented conveyor systems equipped with sanitation-friendly materials and automated cleaning processes. This integration ensured compliance with stringent hygiene standards while boosting production speed and consistency.
Future Trends in Conveyor Systems and Japanese Manufacturing
The landscape of conveyor systems and manufacturing is continually evolving, driven by technological advancements and changing market demands.
Integration of Artificial Intelligence
AI-driven conveyor systems are poised to revolutionize manufacturing by enabling predictive maintenance, optimizing material flow, and enhancing decision-making processes. The incorporation of machine learning algorithms allows conveyors to adapt dynamically to changing production conditions.
Internet of Things (IoT) Connectivity
IoT-enabled conveyor systems offer real-time data collection and analysis, providing valuable insights into operational performance. This connectivity facilitates proactive maintenance, energy management, and comprehensive tracking of materials throughout the production cycle.
Sustainability and Green Manufacturing
Sustainable practices are becoming increasingly important in manufacturing. Future conveyor systems are expected to focus on energy efficiency, reduced emissions, and the use of recyclable materials, aligning with global sustainability goals and regulatory requirements.
Modular and Flexible Designs
The demand for modular and easily reconfigurable conveyor systems is growing, driven by the need for adaptable manufacturing environments. These designs support rapid changes in production lines, enabling manufacturers to respond swiftly to market trends and consumer demands.
Conclusion: Harnessing the Power of Conveyor Systems for Manufacturing Excellence
The integration of conveyor systems in Japanese manufacturing exemplifies the pursuit of operational excellence and continuous improvement. By embracing advanced conveyor technologies and adhering to best practices in procurement and implementation, manufacturers can unlock significant efficiencies, enhance product quality, and maintain a competitive edge in the global market. Understanding the nuances of Japanese manufacturing philosophies and leveraging the strengths of conveyor systems paves the way for sustainable growth and long-term success.
資料ダウンロード
QCD調達購買管理クラウド「newji」は、調達購買部門で必要なQCD管理全てを備えた、現場特化型兼クラウド型の今世紀最高の購買管理システムとなります。
ユーザー登録
調達購買業務の効率化だけでなく、システムを導入することで、コスト削減や製品・資材のステータス可視化のほか、属人化していた購買情報の共有化による内部不正防止や統制にも役立ちます。
NEWJI DX
製造業に特化したデジタルトランスフォーメーション(DX)の実現を目指す請負開発型のコンサルティングサービスです。AI、iPaaS、および先端の技術を駆使して、製造プロセスの効率化、業務効率化、チームワーク強化、コスト削減、品質向上を実現します。このサービスは、製造業の課題を深く理解し、それに対する最適なデジタルソリューションを提供することで、企業が持続的な成長とイノベーションを達成できるようサポートします。
オンライン講座
製造業、主に購買・調達部門にお勤めの方々に向けた情報を配信しております。
新任の方やベテランの方、管理職を対象とした幅広いコンテンツをご用意しております。
お問い合わせ
コストダウンが利益に直結する術だと理解していても、なかなか前に進めることができない状況。そんな時は、newjiのコストダウン自動化機能で大きく利益貢献しよう!
(Β版非公開)