- お役立ち記事
- Inside Japan’s Pioneering Semiconductor Manufacturing: Innovations and Technology Behind the Equipment Revolution
Inside Japan’s Pioneering Semiconductor Manufacturing: Innovations and Technology Behind the Equipment Revolution
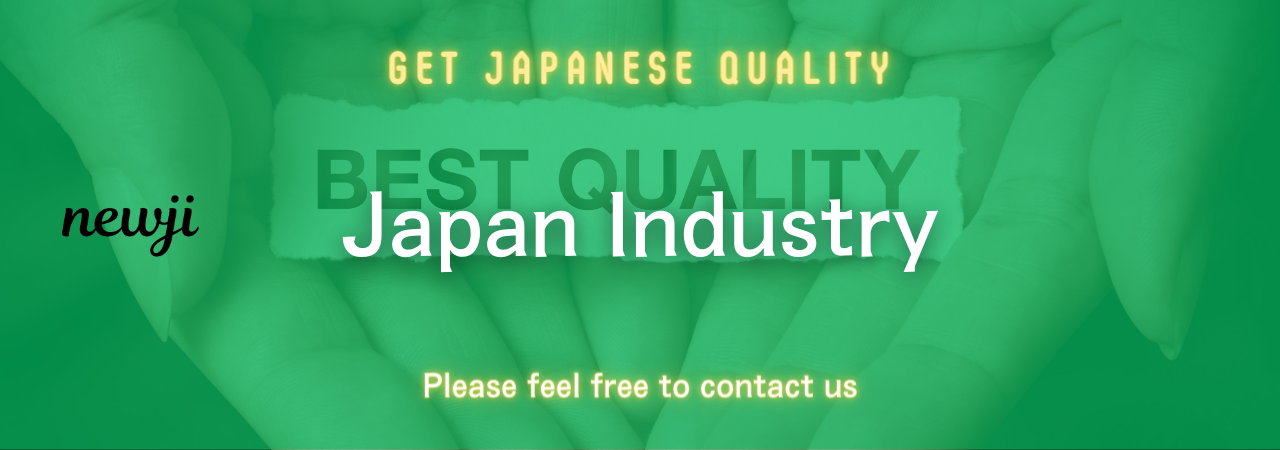
目次
Introduction to Japan’s Semiconductor Manufacturing Prowess
Japan has long been recognized as a global leader in technology and manufacturing. In the semiconductor industry, this reputation is particularly well-earned. Japanese companies have consistently pushed the boundaries of innovation, producing cutting-edge equipment that powers the global electronics market. This article delves into the heart of Japan’s semiconductor manufacturing, exploring the innovations and technologies driving the equipment revolution. It also offers practical insights from the perspective of procurement and purchasing, highlighting advantages and disadvantages, supplier negotiation techniques, market conditions, and best practices.
Historical Context of Japan’s Semiconductor Industry
Japan’s entry into the semiconductor market dates back to the 1960s, a period marked by rapid technological advancement and economic growth. Early investments in research and development laid the foundation for Japan’s dominance in memory chips and manufacturing equipment. Companies like Toshiba, NEC, and Hitachi became household names, synonymous with quality and reliability.
During the 1980s, Japan solidified its leadership by introducing innovative manufacturing processes and equipment. However, the industry faced challenges in the 1990s with increased competition from South Korea, Taiwan, and later, China. Despite these hurdles, Japanese semiconductor manufacturers adapted by focusing on high-precision equipment and automation, maintaining their critical role in the global supply chain.
Innovations Driving the Equipment Revolution
Japan’s semiconductor equipment revolution is characterized by several key innovations:
1. Precision Engineering
Japanese manufacturers are renowned for their precision engineering capabilities. High-precision machinery ensures the production of semiconductor components with minimal defects and exceptional performance. This level of accuracy is crucial for the fabrication of integrated circuits, where even the slightest deviation can impact functionality.
2. Automation and Robotics
Automation is at the core of Japan’s semiconductor manufacturing prowess. Advanced robotics and automated systems enhance production efficiency, reduce labor costs, and minimize human error. These technologies enable the mass production of semiconductors without compromising quality.
3. Advanced Material Science
The development of new materials has been instrumental in advancing semiconductor technology. Japanese companies invest heavily in research to discover materials that offer better electrical properties, higher thermal stability, and greater durability. Innovations in material science contribute to the creation of more powerful and efficient semiconductors.
4. Photolithography Techniques
Photolithography is a critical process in semiconductor manufacturing. Japanese firms have pioneered advanced photolithography techniques, enabling the production of smaller and more complex chip designs. These techniques increase the density of transistors on a chip, enhancing performance while reducing power consumption.
5. Environmental Sustainability
Sustainability is increasingly important in semiconductor manufacturing. Japanese companies prioritize environmentally friendly practices, such as reducing energy consumption, minimizing waste, and recycling materials. Sustainable manufacturing not only benefits the environment but also aligns with global regulatory standards and consumer expectations.
Procurement and Purchasing Insights
From a procurement and purchasing perspective, partnering with Japanese semiconductor equipment suppliers offers numerous advantages but also presents certain challenges. Understanding these dynamics is crucial for optimizing supply chains and maintaining competitive advantage.
Advantages of Procuring from Japanese Suppliers
1. Superior Quality and Reliability
Japanese manufacturers are synonymous with high quality and reliability. Their commitment to precision engineering and rigorous quality control ensures that the equipment procured meets the highest standards. This reliability translates into fewer breakdowns, reduced maintenance costs, and consistent production output.
2. Technological Leadership
Japanese companies lead in semiconductor equipment innovation. Procuring from these suppliers provides access to the latest technologies and advancements, enabling manufacturers to stay ahead in the competitive market. This technological edge is essential for producing cutting-edge semiconductors that meet evolving industry demands.
3. Comprehensive Support and Service
Japanese suppliers offer extensive support, including training, technical assistance, and maintenance services. This comprehensive support ensures that clients can maximize the performance and lifespan of their equipment. Additionally, Japanese companies often provide swift response times and effective problem-solving capabilities.
4. Strong Supplier Relationships
Japanese business culture emphasizes long-term relationships and mutual trust. Building strong supplier relationships can lead to better terms, priority access to new technologies, and collaborative opportunities for innovation. These relationships are invaluable in maintaining a resilient and responsive supply chain.
Disadvantages and Challenges
1. High Initial Costs
Japanese semiconductor equipment tends to be more expensive compared to alternatives from other regions. The superior quality and advanced technology come at a premium, which can be a significant consideration for companies with limited budgets.
2. Language and Cultural Barriers
Language differences and cultural nuances can pose challenges in communication and negotiation. Understanding and navigating these barriers require cultural sensitivity and, often, the assistance of experienced intermediaries or bilingual staff.
3. Longer Lead Times
Due to the high demand and precision manufacturing processes, lead times for Japanese equipment can be longer. This can impact production schedules and require careful planning to ensure timely procurement and deployment.
4. Dependence on Supplier Stability
Reliance on a few key Japanese suppliers can create vulnerabilities in the supply chain. Any disruption, such as natural disasters or economic shifts in Japan, can have cascading effects on global semiconductor production.
Supplier Negotiation Techniques
Effective negotiation with Japanese semiconductor equipment suppliers requires a nuanced approach that respects cultural norms and leverages the strengths of both parties. Here are key techniques for successful negotiations:
1. Building Trust and Relationships
Japanese business culture prioritizes trust and long-term relationships. Investing time in building rapport and demonstrating commitment can lead to more favorable negotiation outcomes. Regular visits, open communication, and mutual respect are essential components of this approach.
2. Understanding Cultural Etiquette
Knowledge of Japanese business etiquette can enhance negotiations. This includes formal greetings, the exchange of business cards with both hands, maintaining eye contact without being confrontational, and showing appreciation for the supplier’s time and expertise.
3. Emphasizing Mutual Benefits
Highlighting how the partnership benefits both parties fosters a collaborative atmosphere. Instead of a zero-sum mindset, focus on shared goals such as quality improvement, innovation, and market expansion. This approach aligns interests and promotes cooperation.
4. Patience and Persistence
Negotiations with Japanese suppliers may take longer due to the thorough decision-making processes and consensus-driven culture. Patience and persistence are crucial, allowing time for detailed discussions and careful consideration of proposals.
5. Leveraging Technical Expertise
Demonstrating a deep understanding of semiconductor manufacturing and the specific technical needs of your organization can enhance credibility. Engaging in technical dialogues and showcasing informed questions can build respect and facilitate more productive negotiations.
6. Clear and Detailed Agreements
Ensure that all agreements are clearly documented, specifying terms, conditions, responsibilities, and expectations. Detailed contracts help prevent misunderstandings and provide a solid foundation for the partnership.
Market Conditions and Trends
Understanding the current market conditions and trends in the semiconductor industry is vital for making informed procurement decisions.
1. Global Demand for Semiconductors
The global demand for semiconductors continues to grow, driven by advancements in artificial intelligence, Internet of Things (IoT) devices, automotive electronics, and 5G technology. This surge in demand puts pressure on the supply chain, highlighting the importance of reliable and innovative equipment suppliers.
2. Supply Chain Resilience
Recent disruptions, such as the COVID-19 pandemic and geopolitical tensions, have underscored the need for resilient supply chains. Diversifying suppliers and strengthening partnerships with reliable Japanese manufacturers can enhance supply chain stability.
3. Technological Advancements
Emerging technologies, including extreme ultraviolet (EUV) lithography, advanced packaging, and heterogeneous integration, are shaping the future of semiconductor manufacturing. Japanese equipment suppliers are at the forefront of these advancements, offering state-of-the-art solutions to meet evolving production requirements.
4. Sustainability and Environmental Regulations
Increasing focus on sustainability and stringent environmental regulations are driving the semiconductor industry towards greener manufacturing practices. Japanese suppliers’ commitment to environmental sustainability aligns with these trends, making them attractive partners for eco-conscious manufacturers.
Best Practices in Procurement and Purchasing
Adopting best practices in procurement and purchasing can optimize the benefits of partnering with Japanese semiconductor equipment suppliers.
1. Comprehensive Supplier Evaluation
Conduct thorough evaluations of potential suppliers, assessing factors such as technological capabilities, financial stability, reputation, and alignment with your company’s values and objectives. Utilize site visits, reference checks, and performance assessments to make informed decisions.
2. Strategic Sourcing
Develop a strategic sourcing plan that identifies key suppliers, outlines procurement strategies, and aligns with long-term business goals. Strategic sourcing helps in securing the best value, ensuring quality, and fostering strong supplier relationships.
3. Risk Management
Implement robust risk management practices to identify, assess, and mitigate potential risks in the supply chain. This includes diversifying suppliers, establishing contingency plans, and regularly reviewing supplier performance and market conditions.
4. Collaborative Innovation
Engage in collaborative innovation with suppliers. Sharing insights, co-developing technologies, and participating in joint research initiatives can lead to breakthroughs that benefit both parties. This collaborative approach fosters a mutually beneficial partnership focused on continuous improvement.
5. Performance Metrics and Continuous Improvement
Establish clear performance metrics to monitor supplier performance, including quality, delivery times, and responsiveness. Regularly review these metrics and work with suppliers to identify areas for improvement, ensuring sustained excellence and adaptability to changing market demands.
6. Leveraging Technology and Data Analytics
Utilize technology and data analytics to enhance procurement processes. Tools such as supply chain management systems, predictive analytics, and artificial intelligence can provide valuable insights, streamline operations, and support data-driven decision-making.
Conclusion
Japan’s pioneering role in semiconductor manufacturing is underpinned by relentless innovation, precision engineering, and a commitment to quality and sustainability. For procurement and purchasing professionals, partnering with Japanese suppliers offers access to cutting-edge technologies, reliable equipment, and comprehensive support. However, navigating the associated challenges requires strategic approaches, cultural understanding, and robust risk management.
By embracing best practices, fostering strong supplier relationships, and staying informed about market trends, companies can fully leverage the advantages of Japan’s semiconductor manufacturing prowess. As the global demand for semiconductors continues to rise, Japanese equipment suppliers will remain critical partners in driving technological advancement and maintaining competitive advantage in the rapidly evolving electronics landscape.
資料ダウンロード
QCD調達購買管理クラウド「newji」は、調達購買部門で必要なQCD管理全てを備えた、現場特化型兼クラウド型の今世紀最高の購買管理システムとなります。
ユーザー登録
調達購買業務の効率化だけでなく、システムを導入することで、コスト削減や製品・資材のステータス可視化のほか、属人化していた購買情報の共有化による内部不正防止や統制にも役立ちます。
NEWJI DX
製造業に特化したデジタルトランスフォーメーション(DX)の実現を目指す請負開発型のコンサルティングサービスです。AI、iPaaS、および先端の技術を駆使して、製造プロセスの効率化、業務効率化、チームワーク強化、コスト削減、品質向上を実現します。このサービスは、製造業の課題を深く理解し、それに対する最適なデジタルソリューションを提供することで、企業が持続的な成長とイノベーションを達成できるようサポートします。
オンライン講座
製造業、主に購買・調達部門にお勤めの方々に向けた情報を配信しております。
新任の方やベテランの方、管理職を対象とした幅広いコンテンツをご用意しております。
お問い合わせ
コストダウンが利益に直結する術だと理解していても、なかなか前に進めることができない状況。そんな時は、newjiのコストダウン自動化機能で大きく利益貢献しよう!
(Β版非公開)